Aluminum CNC Machining — A Beginner’s guide
Aluminum CNC machining is one of the most prevalent manufacturing techniques due to its ability to produce complex yet lightweight parts quickly and cost-effectively.
Introduction to Aluminum CNC Machining
Very few substances can match the incredible versatility of aluminum. Aluminum is highly machinable and relatively inexpensive, making it perfect for CNC machining. Manufacturers can machine it three or even four times faster than other common machining materials such as steel and titanium.
Its flexibility and impressive strength-to-weight ratio make it ideal for use as the exterior skin panels of all forms of transportation, from automobiles and trains to aircraft and boats.
Greater emphasis on fuel efficiency and “lightweighting” has seen aluminum replace the heavier metals traditionally used to make components and internal structures. Its high corrosion resistance also avoids the need for heavy and expensive anti-corrosion coatings often required by other materials.
Additionally, aluminum is non-toxic, malleable and 100% recyclable. This is why the metal is so widely used for food and drink containers, trays, lids, sachets, pouches and wrappers.
Thanks to its sleek, silver surface finish, it is also well-suited for electronic devices like smartphones, laptops, tablets, and flatscreen TVs. It can even be found in construction projects both as a design feature and to provide structural support.
Put all these characteristics together and you have a material that is lighter than steel, stronger and more reliable than plastic, inexpensive, readily available and infinitely adaptable.
This guide will help you to understand:
• Where does aluminum come from?
• What is CNC machining?
• What types of aluminum are used in CNC machining?
• Steel versus aluminum CNC machining?
• What are the most common aluminum CNC machining processes?
Where does aluminum come from?
Aluminum is the most abundant metal element in the Earth’s crust. The metal industry smelts more than 40 million tons each year, and manufacturers use it in numerous applications.
Like most metals, aluminum is present in rocks throughout the Earth’s crust as an ore. Mining companies extract almost all aluminum metal from bauxite ore, which typically contains 30% to 60% aluminum oxide (or alumina). The rest is a mixture of silica, various iron oxides and titanium dioxide.
A two-step process transforms alumina into aluminum metal:
1. Extracting alumina from bauxite
Nearly all of the world’s alumina supply is produced using the Bayer Process. Austrian chemist, Carl Josef Bayer, developed this technique in the late 19th century.
It involves crushing bauxite into a fine powder, mixing it with water and heating the mixture with caustic soda. The caustic soda dissolves the alumina, allowing it to pass through filters.
Producers add aluminum hydroxide crystals to the alumina solution and then heat and dry the mixture to produce alumina.
2. Smelting alumina to produce aluminum metal
To smelt aluminum, refineries dissolve alumina in a fluorinated bath and use an electrical current to break it down into metallic aluminum and oxygen through a process called electrolysis. They then collect the aluminum and take it to a furnace, where they will combine it with recycled aluminum material and heat it until molten.
It is then poured into molds or mechanically extruded in various forms. The most common are sheets, billets, rods, tubes, plates, bars and wires. These are then cut into different shapes and sizes and shipped to another company or manufacturer that will machine them into countless products.
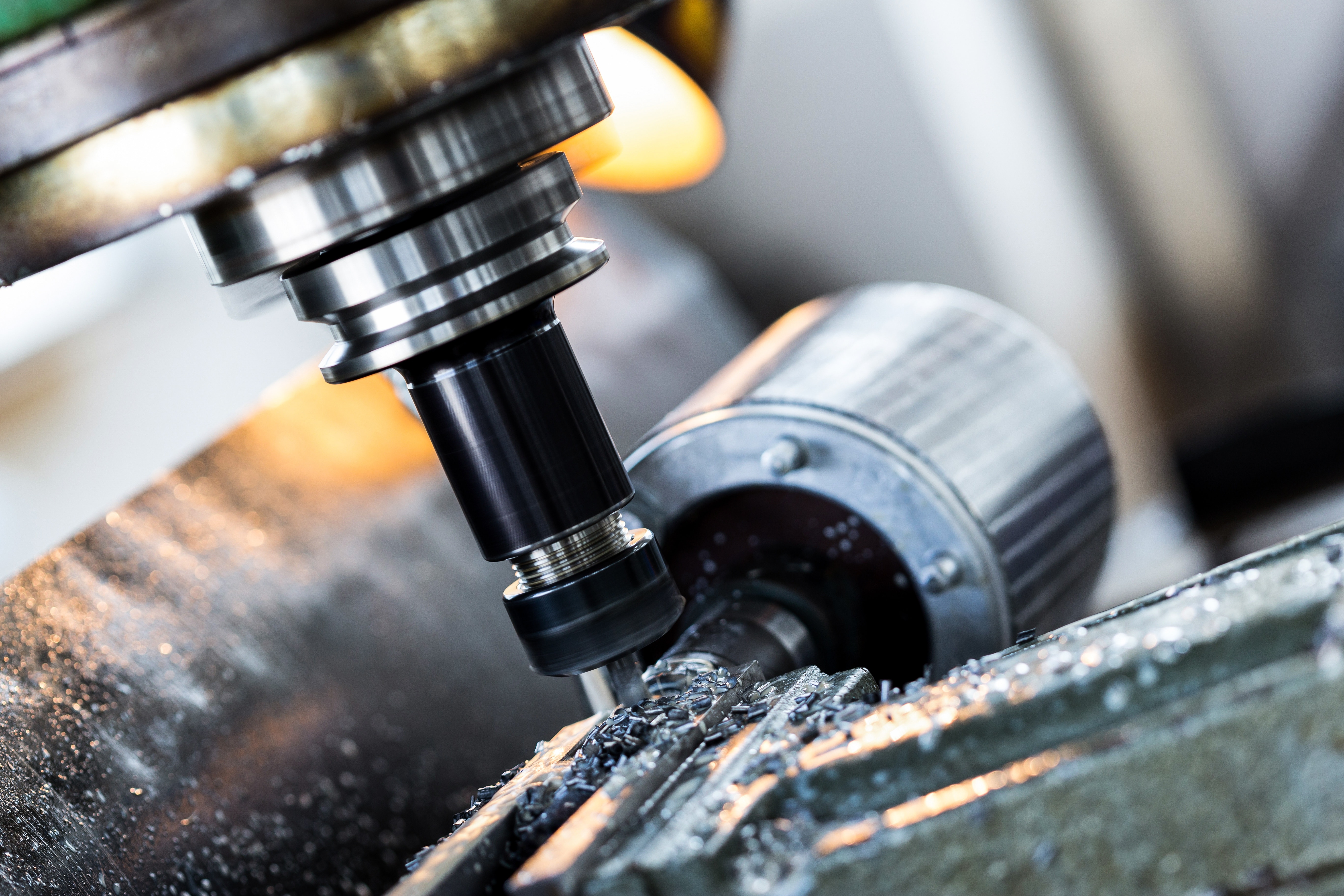
What is CNC machining?
A CNC machine combines traditional manufacturing techniques with a computer numerical control (CNC) system. This enables it to cut and shape stock material into objects impossible or too time-consuming and costly to achieve manually.
Being computer-controlled provides an extremely high level of precision. This translates into greater accuracy, consistency, productivity, control and design freedom with less waste.
The first numerically controlled machines were developed in the late 1940s by adding motors to the equipment already in use. The advent of computers in the 1960s led to the development of modern CNC machines.
The most frequently used CNC machines are milling and drilling machines, lathes, and plasma, laser and water cutters.
These machines all perform what is known as “subtractive” manufacturing methods. This means that material is removed (subtracted) from a workpiece during the process.
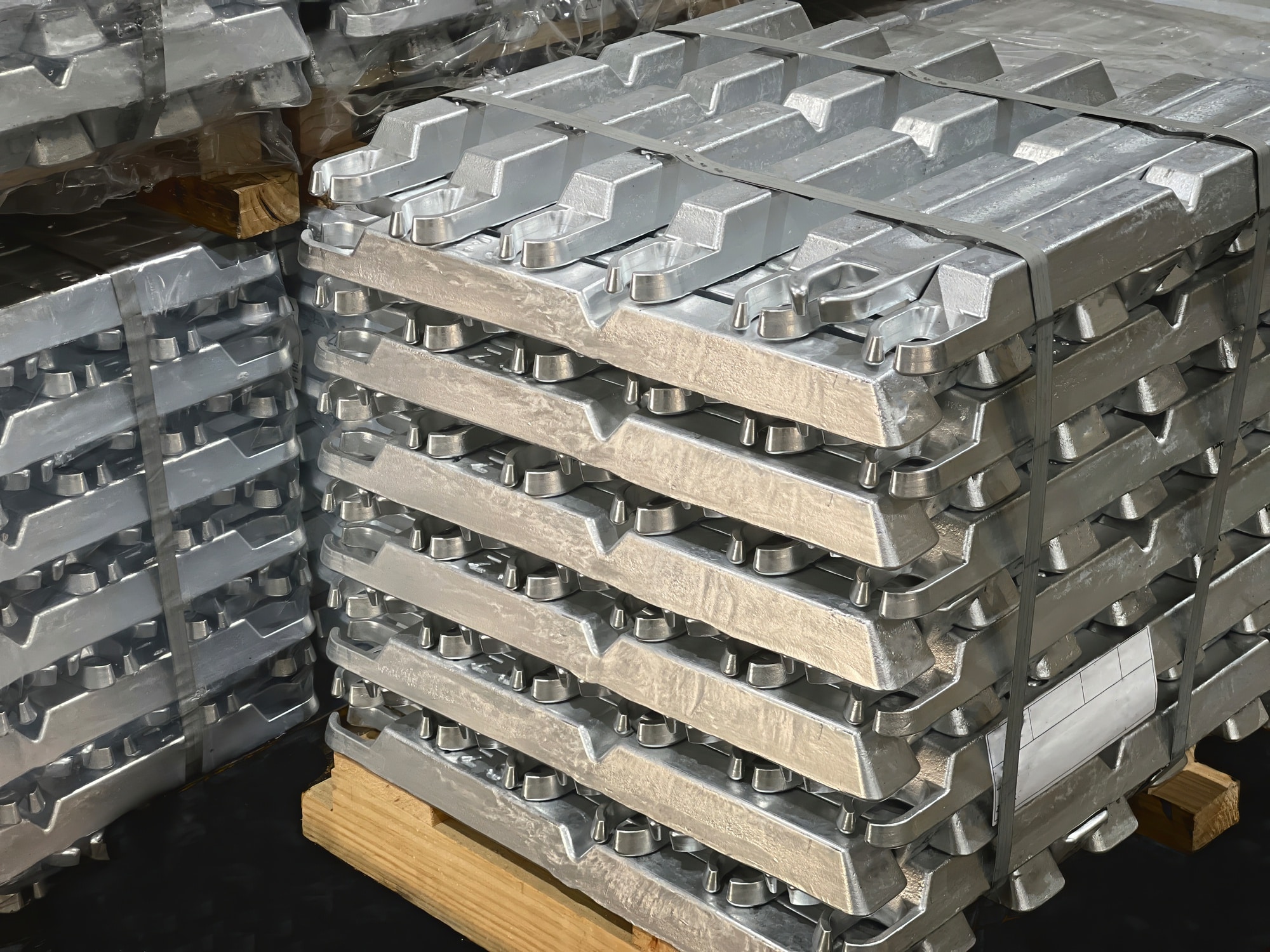
What types of aluminum are used in CNC machining?
In its pure form, aluminum is malleable, resistant to most forms of corrosion, non-magnetic and an excellent conductor of heat and electricity. However, it is too weak for most commercial applications.
Greater strength is achieved by combining molten aluminum with other elements such as copper, lithium, magnesium, manganese, silicon and zinc to form an alloy. These alloys also further enhance aluminum’s other natural properties.
The most common alloys used in aluminum CNC machining fall into three groups:
Cast aluminum alloys—Cast means shaped while molten or liquid. Producers form this type of alloy by pouring molten aluminum into a mold and cooled. Cast aluminum alloys are affordable, versatile, lightweight, durable and perform well under high temperatures.
The automotive industry is the largest user of cast alloys, accounting for around two-thirds of the aluminum used in cars. Parts made from cast alloys include engine parts, housings, steering columns and increasingly, structural supports. Other common uses include cookware, machinery components and handheld tools.
Cast alloys are less expensive to produce due to their low melting point and can produce a broader range of shapes thanks to the flexibility of molds. But they tend to have lower tensile strengths than wrought alloys, aren’t as easy to machine and are more hard-wearing on cutting tools.
Aluminum Lithium (Al-Li) alloys—Lithium is the least dense elemental metal, making this type of alloy significantly lighter than pure aluminum or other materials. Due to this characteristic, the aerospace industry primarily uses Al-Li alloys for lower wing skins, inner wing structures, fuselages and fan blades. You can also find them in racing cars and space rockets.
The weight advantages offered by Al-Li alloys are offset by their lower machinability and reduced fracture toughness (the ability of a material containing a crack to resist further cracking). They are produced in relatively small volumes which also means they are more expensive.
Wrought aluminum alloys—Wrought means shaped while in a solid state. This type of alloy is produced by forming molten aluminum into billets or large slabs and then using tools to roll, forge, stamp or extrude these blocks into shape.
Wrought alloys are the most widely used material in aluminum CNC machining. This is because of their superior mechanical properties and structural integrity compared to cast alloys. They are easier to machine, have better surface finishes and are less hard wearing on the edges of cutting tools.
Steel Versus Aluminum CNC Machining
Aluminum and steel are the most widely used metals in CNC machining. Choosing which is the right one for a particular application comes down to five factors:
1. COST — Mild steels and carbon steels are generally cheaper than aluminum alloy equivalents. Whereas stainless steel tends to be more expensive. However, the price of metal varies depending on global demand and the cost of raw materials, energy and shipping.
When looking at cost, it’s also important to consider a material’s durability. A decision that might save money in the short term could cost more in the long term.
2. CORROSION RESISTANCE — Aluminum and stainless steel are both highly resistant to rust and corrosion. However, stainless steel is a more costly option. Manufacturers or end-users will need to paint, treat or coat every other type of steel to protect it, especially if they intend to expose the finished part to the elements. These coatings mean additional weight and cost, and they also need to be regularly reapplied at further expense.
3. WEIGHT — Aluminum is two to three times lighter than steel. Almost every company is looking to achieve the same or better product performance while incorporating lighter materials. This “lightweighting” trend has seen manufacturers substituting many parts previously machined from steel for aluminum.
4. STRENGTH — Steel may be heavier than aluminum but this makes it a much more durable material. Steel is incredibly strong and is unlikely to warp, bend or otherwise deform under force, heat or weight. Additionally, the surface of aluminum is more prone to scratches and dents compared to steel.
5. MACHINABILITY — Being less dense than steel means aluminum can be machined three or even four times faster. Aluminum also cools more quickly than steel; this reduces how long it takes to machine a part (cycle time) and the amount of coolant required.
Compared to steel, aluminum requires much less cutting force. This reduces the wear on cutting tools, helping to keep them sharper for longer. It is also possible to CNC aluminum on smaller and, therefore, potentially less expensive machines.
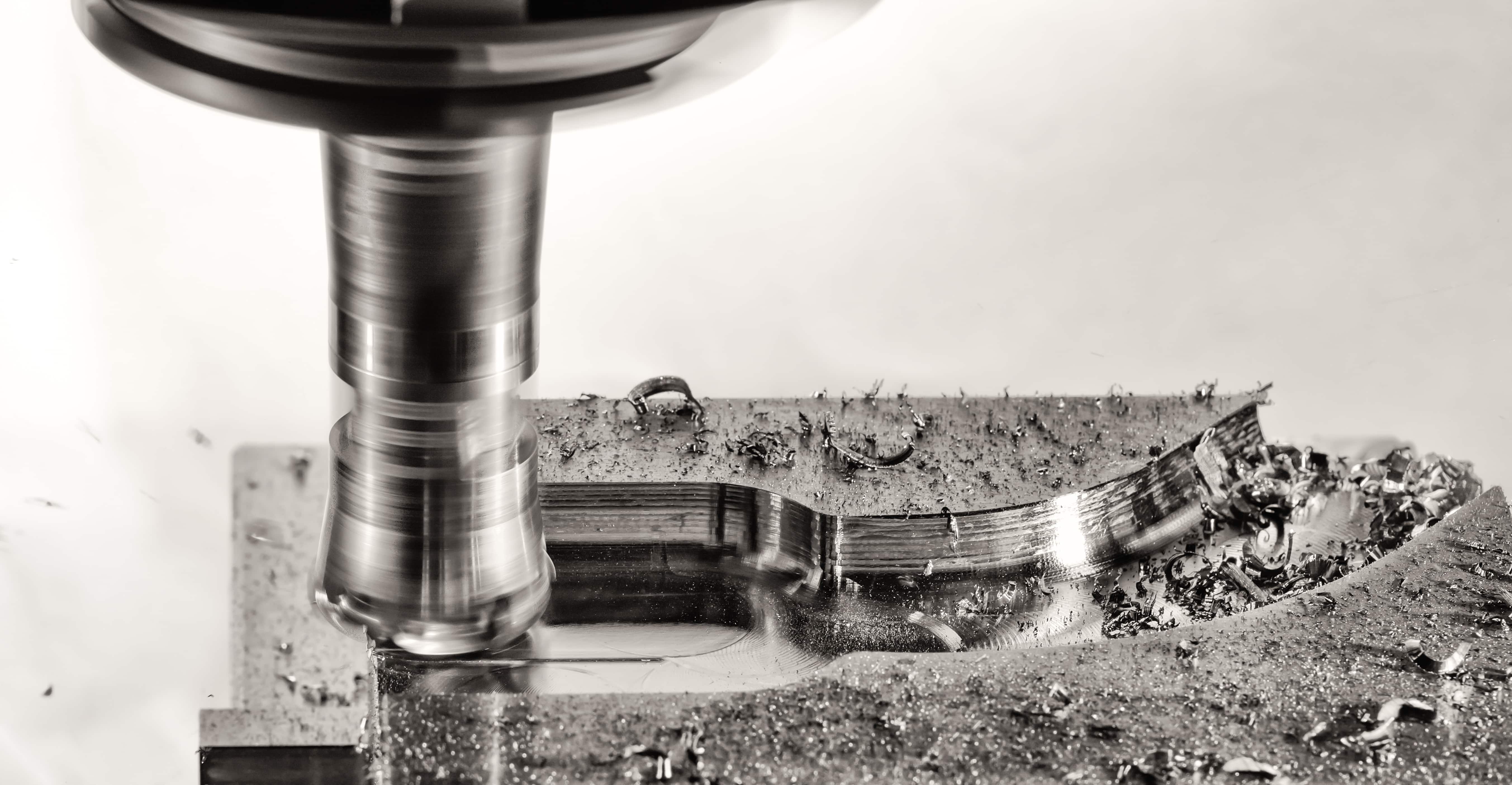
What are the most common aluminum CNC machining processes?
CNC milling machines are the most common and versatile way of machining aluminum parts. The machine uses rotating cutting tools to efficiently and precisely carve material from a stationary block of material.
Traditional milling machines transformed into “machining centers” in the 1960s thanks to the arrival of computer numerical control (CNC) systems, automatic tool changers and tool carousels. These machines are available in 2- to 12-axis configurations, although 3 to 5-axis are the most widely used.
CNC metal lathes, or CNC metal turning centers, firmly hold and rotate a workpiece while a toolhead holds a cutting tool or drill against it. These machines allow for very precise removal of material and manufacturers use them in a broad range of industries.
Typical lathe operations include drilling, shaping, slot-making, tapping, threading and tapering. CNC metal lathes are swiftly replacing older, more manual production models due to their ease of setting up, operation, repeatability and accuracy.
CNC plasma cutters heat compressed air to a very high temperature to create a “plasma arc” capable of melting metal up to six inches thick. Sheet material is held flat against a cutting table and a computer controls the path of the torch head. The compressed air blows away the hot molten metal, thereby cutting through the material. Plasma cutters are fast, precise, relatively easy to use and affordable, and manufacturers use them in many industries.
CNC laser machines either melt, burn or vaporize material away to create a cut edge. Similar to a plasma cutter, sheet material is held flat against a cutting table and a computer controls the path of the high-power laser beam.
Laser cutters use less energy than plasma cutters and are more precise, particularly when cutting thin sheets. However, only the most powerful and expensive laser cutters are capable of cutting through thick or dense materials.
CNC water cutters use extremely high-pressure jets of water forced through a narrow nozzle to cut through material. Water on its own is enough to cut through soft materials like wood or rubber. To cut through hard materials such as metal or stone, operators usually mix an abrasive substance with water.
Water cutters don’t heat material like plasma and laser cutters. This means that the presence of high temperatures won’t burn, warp or change its structure. It also helps to reduce waste and allows shapes cut from a sheet to be placed (or nested) closer together.
Learn more about sub-processes
Get multiple quotes for your parts in seconds