Composite manufacturing
Upload your design, get your composite manufacturing quote, choose your manufacturer and receive your parts!
SECURE PAYMENTS
Via payment card or purchase order
PROTECTED IP
Your data is confidential and secure with us. Use your own Non Disclosure Agreement
INSTANT QUOTE
For 3D Printing and CNC Machining, get quote in few seconds.
Composite manufacturing with 3DEXPERIENCE Make
From plywood to aircraft wings, composites can be found throughout modern society and are increasingly being used in place of traditional materials like wood and metal.
For millennia, humans have been combining different materials to create something that is more durable, flexible and capable than their constituent parts.
Composite manufacturing dates back to ancient brick-making when straw was added to wet clay or mud to accelerate the drying time and provide a stronger finished brick. Metal reinforcement bars in concrete structures perform much the same function. Concrete, the second most used material in the world after water, is itself a composite of loose stones and cement.
The primary reason for making composites is enhanced strength, as in the examples above, but it’s not the only one. For instance, a composite material may be less expensive, lighter, water and heat-resistant, more rigid, electrically conductive or a combination.
Modern composites have been designed to fulfill a specific need and are routinely used in industries such as aerospace, automotive, defence, marine, medical devices and sports equipment.
Common examples include engineered wood, carbon fiber, fiberglass, fibre-reinforced plastics and advanced ceramics. The list of composites is constantly growing as researchers experiment with different material combinations and develop new varieties, processes and applications.
On 3DEXPERIENCE Make, we offer composite manufacturing options across multiple processes such as 3D printing, CNC machining service, Laser cutting service and Injection molding service. 3DEXPERIENCE Make is an On-Demand Manufacturing platform, which connects designers or engineers with industrial service providers. Our service providers are mostly based in North America (United States and Canada) and in Europe (United Kingdom, France, Netherlands, Germany etc...).
Thanks to our powerful algorithm, you can get quotes in seconds for your composite project from dozens of manufacturing providers.
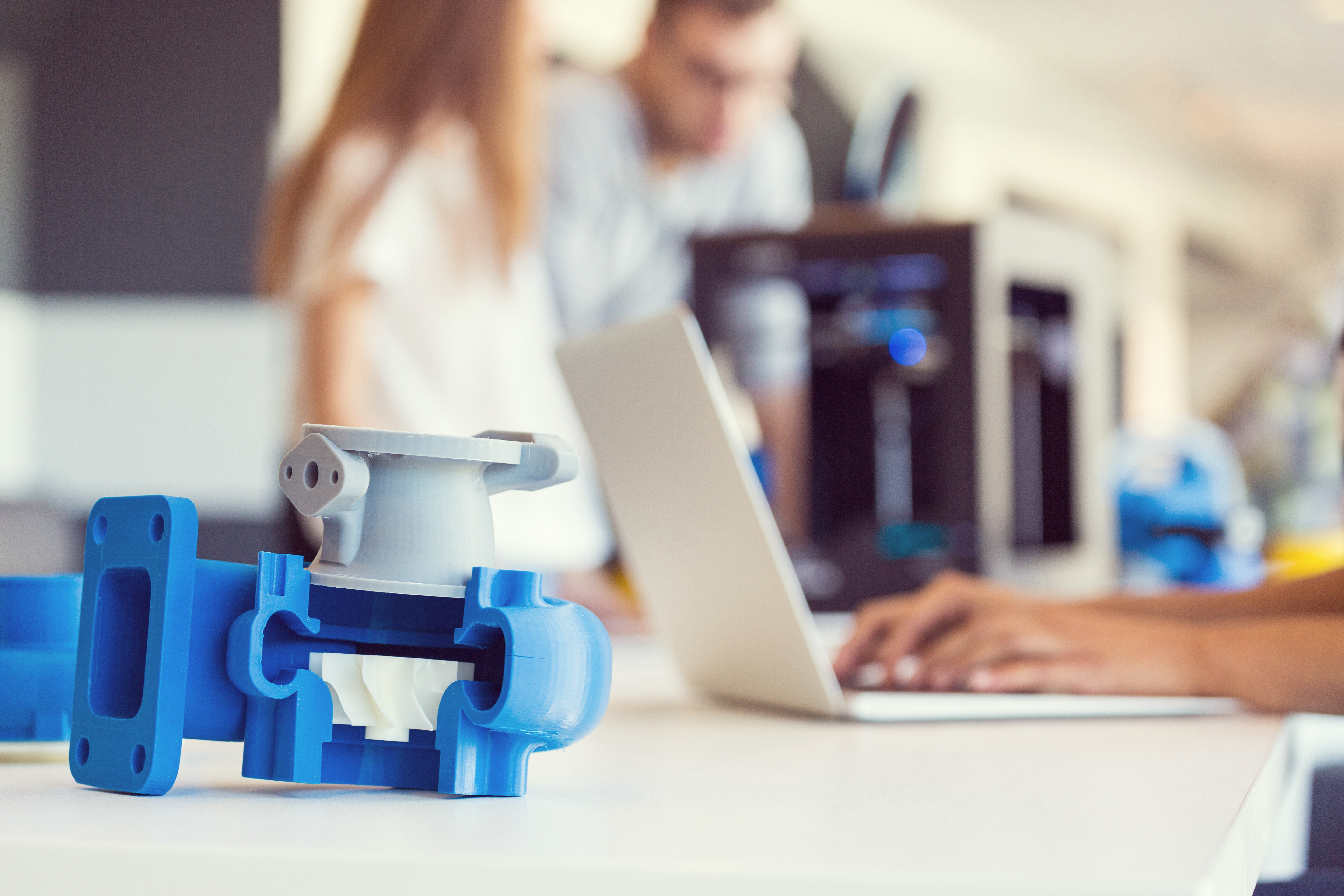
Our network of composite manufacturing providers
United States
Canada
United Kingdom
France
Germany
Netherlands
and many more...
Online manufacturing service: how does it work?
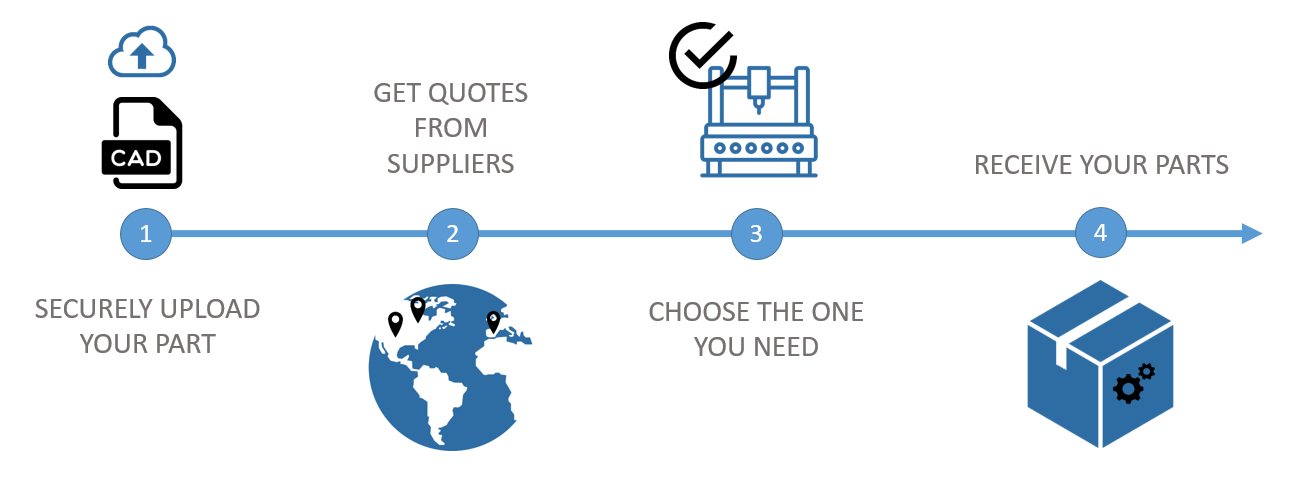
- Securely upload your part
- Get quotes from suppliers
- Choose the one you need
- Receive your parts
Composite materials available with our service providers
Composite materials for 3D printing processes
- Plastic Glass fiber
- Plastic Kevlar
- ABS Carbon fiber
- Gypsum
- PA Glass
- PA Aluminium
- PA Carbon fiber
- Plastic Carbon fiber
- PLA Wood
- PLA Copper
- Plastic Fibers
- Plastic Glass
Composite materials for CNC machining processes
- PC Glass
- PA Glass
Composite materials for Cutting, Molding & Forming processes
- PA Glass
What are the composite manufacturing processes available at 3DEXPERIENCE Make?
3D Printing - Additive manufacturing
FDM, SLS, MJF, BJ, SLA...
Cutting
Laser cutting, Water cutting, Blade
(Milling, turning & spark machining)
CNC Machining - Substractive
Milling, turning & spark machining
Forming
Sheet Metal, Extrusion, Forming, Stamping
Features to help you
Check & repair or Geometry check is a feature that helps you to understand Geometry issue of your part and could repair it live and online.
Check & Repair
Check & repair or Geometry check is a feature that helps you to detect geometry issue on your part and repair it online and live.
Manufacturability Check
This feature is available only for 3D Printing service. It helps you check the manufacturability of your part, depending on the materials and the process.
Instant quote engine
Receive in seconds several quotes thanks to our instant quote engine.
What is a composite?
Composites are made by bonding two or more materials with complementary strengths and weaknesses together. They typically include a binding substance called a ‘matrix’ and a ‘reinforcement’ material that, once combined, provides superior properties to each individual component.
Though many are human-made, there are numerous natural composites, such as wood, which combines cellulose fibers in a matrix of lignin.
Most composites are created from the mixing of wet materials which harden or set over time. A process that can take anything from hours to weeks.
The matrix and reinforcement can be easily seen in the final composite. This characteristic is what separates composites from chemical compounds, solutions and mixtures.
Combining different materials and volumes together changes the enhanced synergy between them, enabling scientists to precisely optimise a composite to solve a particular problem.
Despite their generally high cost, fiber-reinforced composite materials are increasingly being relied upon for high-performance applications due to their high strength-to-weight ratio. They can better withstand the stringent requirements and loading pressures faced by aerospace structures, boat and scull hulls, bicycle frames and racing car monocoques.
The Boeing 787 Dreamliner and the Airbus A350 both have airframes, fuselages, wings, rudders largely comprised of composites.
Composites also continue to replace wood and metal in a wide variety of sporting goods, including tennis racquets, baseball bats, golf clubs, hockey sticks, rowing paddles, fishing rods, and all manner of boards and supports.
The manufacturing processes used to create glass and carbon fibers are crucial to understanding modern composite manufacturing.
Carbon fiber is made from organic polymers of between 5 to 10 microns in width (approximately 0.005mm to 0.1mm). The exact ingredients for the fibers usually depend on the manufacturer and the brand, but most contain organic polymers.
1. The raw materials are spun and stretched into long fibrous strings of molecules held together by carbon atoms.
2. These strands are washed and stabilized with chemicals.
3. The fibers are heated to around 300 degrees which force the carbon molecules to bond tightly together. This process, called carbonization, concentrates and purifies the carbon and provides a high strength-to-volume ratio.
4. The surface of the fibers is treated to oxidize them and improve bonding properties.
5. The carbon fibers are then wound onto bobbins and loaded into spinning machines to twist the fibres into yarns of different thicknesses and woven into fabric. Sheets or strips of this fabric are typically impregnated with resin and allowed to cure. Or, the loose fibers are pressed together with a plastic polymer via heat, pressure or a vacuum to form a composite material.
Fiberglass is made from silica sand with other ingredients such as limestone and soda ash to reduce the melting temperature and control other properties.
- The raw materials are melted in a temperature-controlled furnace.
- The resulting molten mixture travels down a channel to a machine that forms them into small marbles.
- These marbles are inspected to check for impurities before being melted again.
- The molten glass is then passed across metal spinnerets that are covered in tiny orifices.
- Centrifugal force pushes the molten glass out of the orifices as fine filaments. These filaments can be kept as they are or woven into a long continuous strand.
A variety of techniques are used in composite manufacturing and the method employed will reflect the intended application. Other deciding factors include the cost of materials and equipment and the number of items to be produced.
The properties of the finished item will be determined by the properties of the component materials and by how the matrix and reinforcement are combined.
Common composite manufacturing processes include:
- Hand layup molding – The reinforcement material is laid into a mold and the matrix substance is applied by brush, roller or spray gun. The mold can be left open or enclosed and is left to cure. This manual process is relatively inexpensive and is widely used for low-volume, bespoke production.
- Resin transfer molding (RTM) – Sheets of reinforcement material are placed into a mold which is then closed in a heated press. The liquid matrix is premixed with a hardening catalyst and injected under pressure into the mold via small channels and left to cure. A vacuum is sometimes used to improve the flow of the matrix (vacuum-assisted resin transfer molding). This process is well-suited for medium-volume production and requires specialist equipment.
- Reaction injection molding – A resin and a hardening catalyst are sprayed into a mold in two jets. It can also be applied by programmable robots spraying the mixture directly onto sheets of preformed reinforcement materials laid out in a mold. Automated systems help make this process more efficient and accurate.
- Resin film infusion (RFI) – A film of gel-like resin film is layered with sheets of preformed reinforcement material. Heat and pressure are applied, and the resin liquefies and bonds the composite together.
- Injection molding – A premixed blend of chopped glass fiber and resin known as bulk molding compound (BMC) is forced into a heated mold. It liquefies and fills the mold, then it is cooled and once cured, the part is ejected. This process can be used for high-volume production.
- Compression molding – Resin sheets and chopped fibers are clamped together under pressure. When thoroughly combined, they are heated again and metal die is applied under pressure. The fiberglass composite takes the shape of the die, hardens and is ejected. Several parts can be made from each sheet and with the right equipment, the entire process can be automated, making it ideal for high-volume manufacturing.
- Pultrusion – A continuous mat of reinforcing fiber is pulled through a heated resin bath and guided through a heated die that applies the required shape. The composite is then cooled, cured and the long sheet is cut up into single parts.
- Extrusion – Long fiber preparations of glass or carbon fiber can be premixed with specialized thermoplastic and forced through a die under pressure. This forms a continuous shape that can be cured and cut into lengths. Extrusion is more commonly used to manufacture plastic but has recently been developed for use with composite materials.
- Strength-to-weight – Composites typically have a significantly higher strength-to-weight ratio than traditional materials such as wood, metal and plastic.
- Design flexibility – Composites can be formed into comples shapes and geometries just as easily as simple forms, often in one-piece, and can be finished in a variety of different ways.
- Manufacturability – Composites come in a variety of sizes and thicknesses and are generally easy to work with. They can be formed close to the final shape of the object so require minimal forming or finishing compared to a material like metal.
- Versatility – There are many different composite materials, each with their own properties and characteristics. What’s more, relatively minor changes in the raw materials used or in the manufacturing process can change how the composite behaves and its potential applications.
- Insulators – Many composites don't conduct heat or cold which makes them ideal for fire and blast protection and sub-zero applications.
- Durability– Most composites are resistant to water, chemicals and other forms of corrosion which makes them ideal for use in outdoor or harsh environments.
- Isotropic – Composites don’t have grain so won’t split, unlike wood.
- Cost – The raw materials, the manufacturing process and the tools needed to use composites can be expensive.
- Brittleness – Composites can be more brittle than other materials and therefore more easily damaged.
- Repairability – Repairing composites is possible, but it it may compromise structural integrity, be time-consuming and expensive, and require specialist equipment.
- Recyclability – Composites are generally problematic to recycle due to their structure and how thoroughly the matrix and reinforcement are blended together.
- Inspection – The strength of composite materials makes identifying any structural damage more difficult as defects and weaknesses may lie below the surface or appear the same as other areas.
Discover our other materials for manufacturing
Metal
Aluminium, Nickel, Stainless, Steel, Titanium, etc...
Plastic
ABS, POM(Acetal/Deltin), PEEK, PTFE, HDPE, PEI, PC, PP, etc...
Wax
Wax support, UV Curvable, etc...
Sand
Get multiple quotes for your parts in seconds