CNC machining
Discover what is the manufacturing process CNC Machining and its usages in the industry.
Discover 3DEXPERIENCE SOLIDWORKS for Makers
What is the history of CNC machining?
Due to advances in technology, it is common to find Computer Numerically Controlled machines, or CNC machines, in all industries. CNC machines are automated milling devices that manufacture industrial components without direct human assistance. They use coded instructions sent to a computer, allowing factories to make parts accurately and quickly. The CNC machine has developed significantly in size and complexity since its beginnings in the 1950s by adapting to digital technologies.
The Beginnings of the CNC Machine
Before the advent of CNC machines, the ability of operators to fabricate parts was limited, resulting in poor adjustments or losses, and worker productivity remained low. There was an urgent need to operate machines automatically, which resulted in Swiss or precision machines.
In the 1940s, the first numerically controlled (CNC) machines appeared. The Parsons Corporation in Traverse City, Michigan, developed a system to design templates for helicopter blades. This machine is considered the first true CNC machine, as it manufactured goods by inserting punched cards into a device. The device then read and shaped the parts based on pre-programmed information.
CNC milling machine: a collaboration between MIT researchers and Parsons
During World War II, researchers at MIT (Massachusetts Institute of Technology) began working to create a CNC machine to assist the Air Force.
In 1949, Parsons teamed up with the MIT Servomechanics Laboratory to design rotor blades for the aerospace industry. They then developed the NC milling machine. This experiment received instructions via data on a perforated paper strip.
On May 5, 1952, the first working model of a continuous-path CNC milling machine was presented, for which Parsons applied for a patent.
APT Language Development
The Air Force continued to sponsor further research. Then the laboratory's computer application group, led by Douglas T. Ross, developed the Automatically Programmed Tool Language (APT), a special programming language that is easy to use.
The invention of APT was a significant turning point in the evolution of NC in terms of costs. It definitively settled the question of whether or not NC could be made economically viable. The APT language became the American standard for NC machine tool programming in 1974 and the international one in 1978.
Digital technology at the service of the CNC machine
In the 1960s and 1970s, the CNC machine took shape, thanks to digital technology that made the automation of production processes much more efficient.
In 1957, the first CAM (Computer Aided Manufacturing) software, an NC programming tool called PRONTO, was created thanks to the contribution of Dr. Patrick Hanratty. He established a direct link between CNC and CAM.
In 1960, Direct Numerical Control (DNC) eliminated paper web punching programs and allowed programmers to send files directly from the computer to the machine tool controller.
CNC machine tools developed in the 1970s with the advent of more powerful PCs and the democratization of the less expensive minicomputers. The latter made CAD (Computer-Aided Design) accessible to more users. In the 1980s, powerful workstations and Unix PCs contributed to the growth of CNC machine tools, as did the increasing power of CAD systems themselves.
The evolution of CAD/CAM made multitasking on CNCs possible, ameliorating productivity on several levels. In 1976, 3D CAD/CAM systems were introduced.
Today, many individuals can buy—and even design—their own homemade CNC machines. In the future, CNC machining will be improved as robotic and automated processes develop in almost all areas.
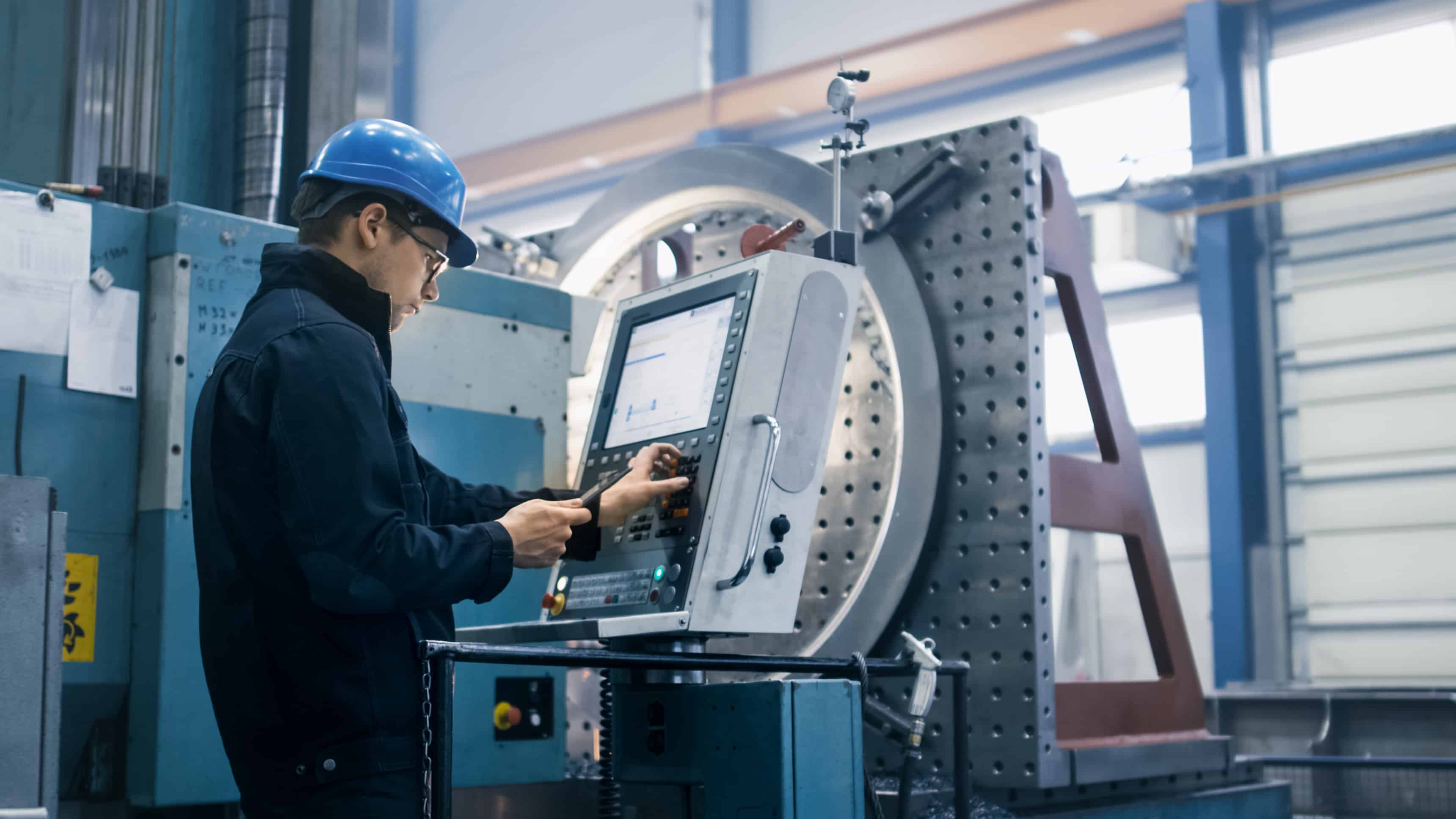
What is CNC machining?
CNC machining is a "subtractive" manufacturing process that typically uses computerized controls and machine tools to remove layers of material from a blank (or workpiece) and produce a custom part. This method is often presented instead of additive manufacturing processes, such as 3D printing, or formative manufacturing processes, such as liquid injection molding. The automated nature of CNC machining makes it possible to create simple, high-precision parts with high accuracy; and to fabricate unique, medium-scale production series cost-effectively.
What are the main steps of CNC machining?
While the CNC machining process offers a variety of operations and capabilities, the fundamental principles of the method remain largely the same. The main steps of CNC machining are as follows:
I. CAD model designing
The CNC machining process begins with creating a 2D vector or 3D Computer-Aided Design (CAD) of a solid part. This can be done either in-house or by a CAD/CAM (Computer-Aided Manufacturing) design service company. CAD software allows designers and manufacturers to make a model or render their parts. They can design their products according to customized technical specifications, such as dimensions and geometries.
Once the CAD design is complete, the designer exports it to a CNC-compatible file format, such as STEP or IGES.
II. CAD file conversion
The formatted CAD design file passes through software, usually a CAM, to extract the part's geometry and generate the digital programming code. It will give commands to the CNC machine and manipulate the tooling to produce the custom-designed part.
Numerically controlled machines use several languages, but the best known of the CNC is the general or geometric code, called G-code. This controls when, where, and how the machine tools move. For example, when to start or stop, how fast to get to a particular point, which paths to take, etc.
Once the CNC program is generated, the operator loads it onto the CNC machine.
III. Machine configuration
Before the operator executes the CNC program, he must prepare the CNC tool. These steps include:
- fixing the part directly in the machine, on its spindles, or in its clamps;
- attaching the necessary tooling, such as drills and cutters, to the appropriate machine components.
The operator can run the CNC program once the machine is fully set up.
IV. Machining operation execution
The CNC program acts as instructions for the CNC machine: it submits the machine controls that dictate the actions and movements of the tooling to the integrated machine computer, which operates and manipulates the tooling. Launching the program prompts the CNC tool to begin the CNC machining process, and the program guides the machine through the operation as it performs the necessary steps to manufacture a custom part or product.
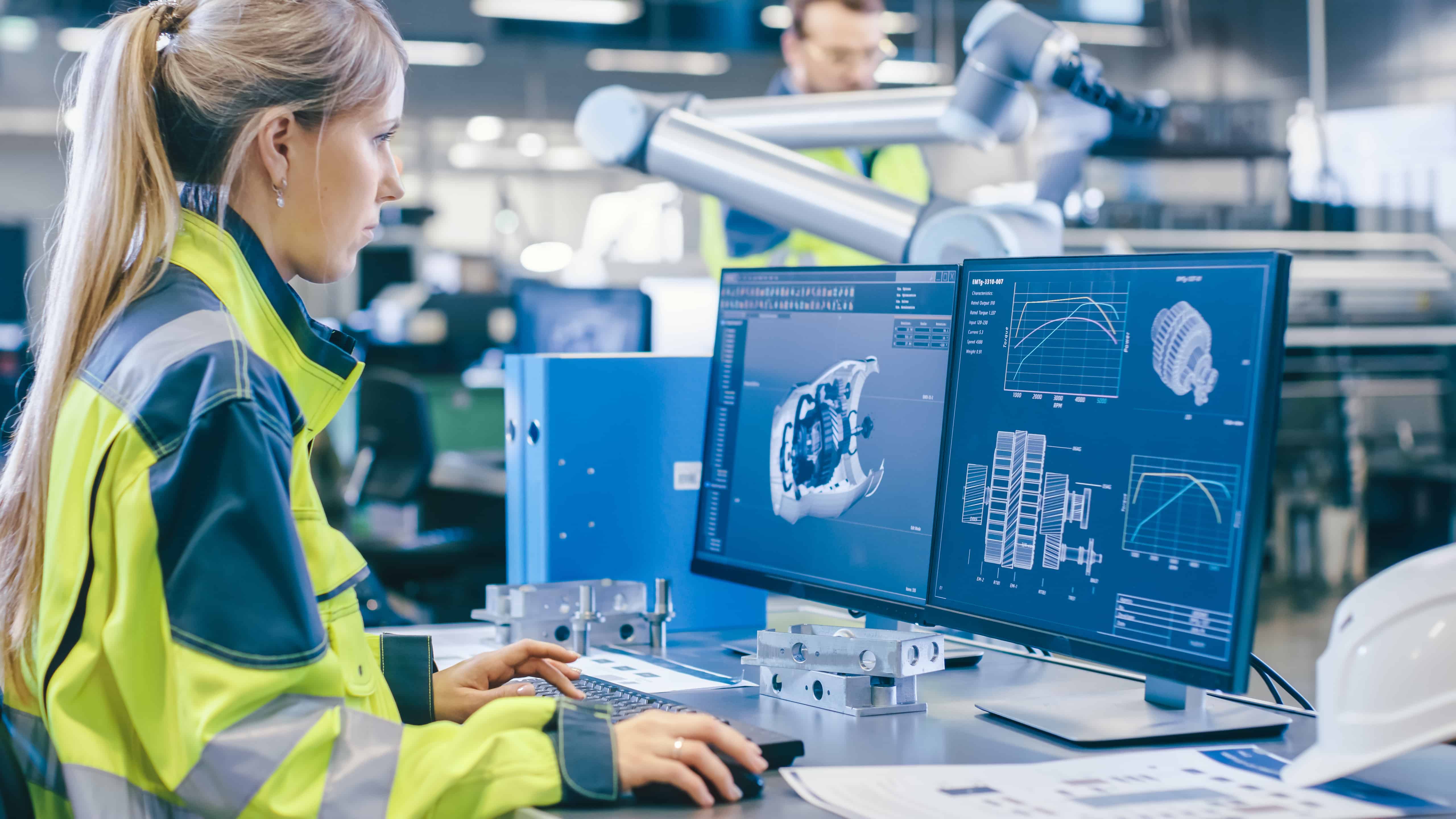
What are the different CNC machining processes?
CNC machining is a manufacturing process suitable for various industries, including automotive, aerospace, and construction. It can develop a wide range of products, such as car chassis, surgical equipment, and aircraft engines. The process encompasses several methods, including mechanical, chemical, electrical, and thermal, to remove the necessary material from the part to shape a custom part or product. The following are examples of the most common CNC machining operations:
I. CNC Drilling
In the case of CNC drilling, the CNC machine usually advances the rotary drill bit perpendicular to the plane of the workpiece surface. This technique produces vertically aligned holes. Their diameter is equal to the diameter of the drill bit used for drilling. The operational capabilities of the drilling process include counterboring, milling, reaming, and tapping.
II. CNC Milling
During CNC milling, the CNC machine feeds the workpiece to the cutting tool in the same direction as the rotation of the tool. This is not the case with manual milling. Here, the machine feeds the workpiece in the opposite direction to the rotation of the cutting tool. The operational capabilities of the milling process include :
- face milling: cutting flat, shallow surfaces and flat-bottomed cavities in the workpiece;
- Peripheral milling: cutting deep cavities in the workpiece, such as slots and threads.
III. CNC Turning
In CNC turning, the CNC machine feeds the cutting tool in a linear motion along the surface of the rotating workpiece. This removes material around the circumference until the desired diameter is reached. This technique makes it possible to shape cylindrical parts with external and internal features such as slots, cones, and threads. The operational capabilities of the turning process include boring, facing, grooving, and threading.
IV. Electrical Discharge Machining (EDM)
Electroerosion machining (EDM) is a process that consists of molding parts of a particular shape with electric sparks. In this case, current discharges occur between two electrodes, allowing sections of a given part to be removed.
When the space between the electrodes becomes smaller, the electric field becomes stronger than the dielectric. This causes a current to flow between the two electrodes. As a result, each one ejects parts of a workpiece.
In a process called "rinsing," a liquid dielectric appears when the current between the two electrodes has stopped. This then carries away debris from each finished part.
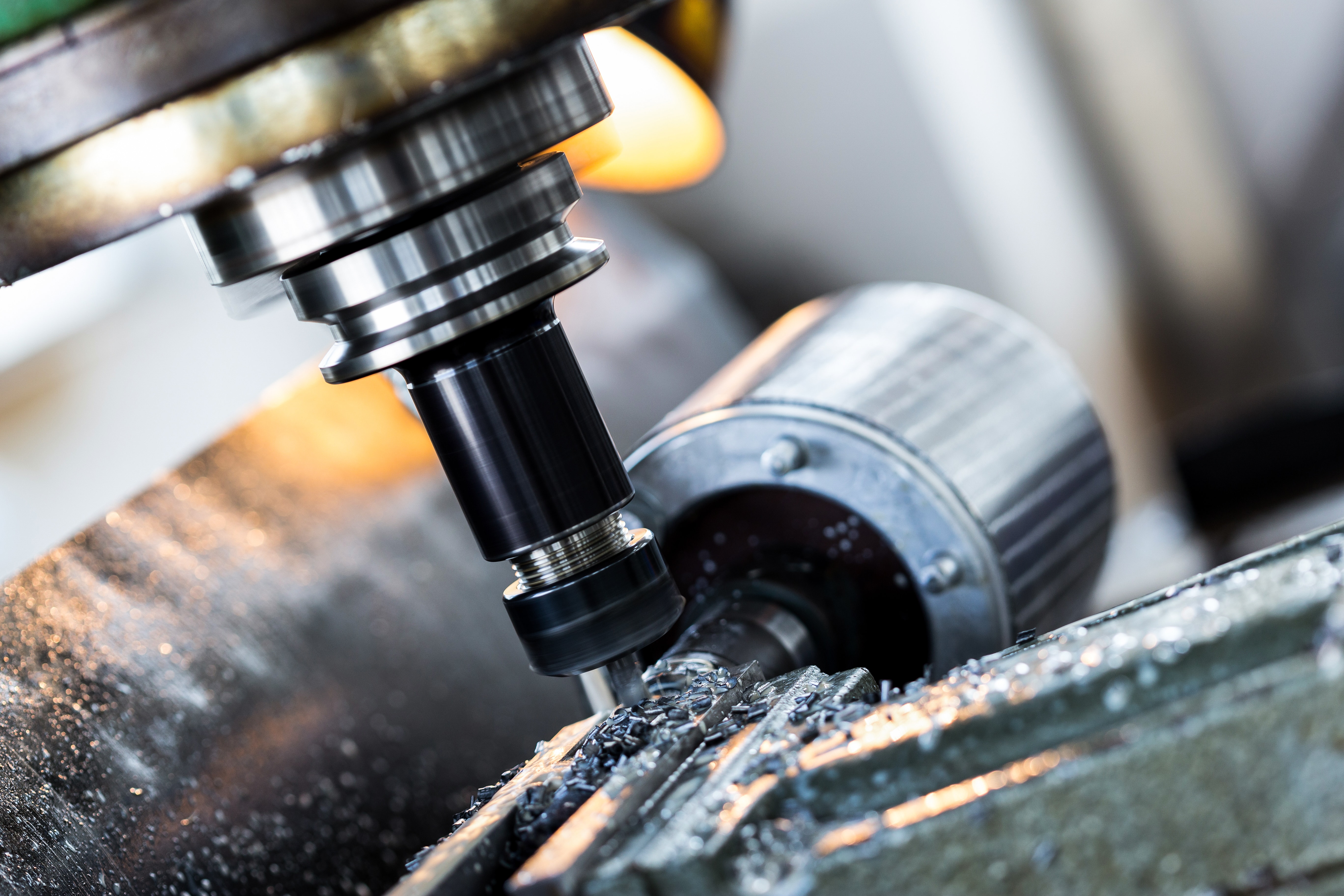
Which material to choose for CNC machining?
The CNC machining process is suitable for various engineering materials, including metal, plastics, and composites. The optimal material choice for CNC manufacturing depends mainly on its properties and specifications.
What are the specifics of different CNC materials?
CNC machining can produce parts from almost any metal or plastic. The properties of interest of these materials are:
- mechanical strength: expressed by the tensile yield strength;
- machinability: the ease of machining influences the price of CNC;
- the cost of the material;
- hardness: mainly for metals;
- temperature resistance: mainly for plastics.
CNC Metals
Applications that require high strength, hardness, and thermal resistance exploit metals or, rather, metal alloys.
- Aluminum: used to create custom metal parts and prototypes.
- Stainless steel can be easily welded, machined, and polished.
- Mild steel, or low-carbon steel: used for machine parts, jigs, and fixtures.
- Alloy steel contains other alloying elements in addition to carbon to improve hardness, toughness, fatigue, and wear resistance.
- Tool steel is advantageous for fabrication tools such as dies, stamps, and molds.
- Brass is ideal for applications that require low friction and architecture to design gold-looking parts for aesthetic purposes.
CNC Plastics
Plastics are lightweight materials with different physical properties, often used for their chemical resistance and electrical insulation characteristics.
- ABS: often used to manufacture prototypes before mass production by injection molding.
- Nylon, or polyamide (PA): mainly used for technical applications because of its excellent mechanical properties, impact strength, and high resistance to chemicals and abrasion.
- Polycarbonate is generally optically transparent, making it ideal for many applications, such as fluid devices or automotive glazing.
- POM (Delrin) is the material of choice for CNC machining when parts require:
- high precision
- high rigidity
- low friction
- excellent dimensional stability at high temperatures
- very low water absorption.
- PTFE (Teflon) has resistance to operating temperatures above 200 °C and is, therefore, an outstanding electrical insulator.
- High-density polyethylene (HDPE) is suitable for outdoor use and piping.
- PEEK: mainly used to replace metal parts due to its high strength-to-weight ratio. Medical grades are also available, making PEEK also suitable for biomedical applications.
CNC Composite Materials
Composites, in simple terms, are multiple materials with different physical and chemical characteristics that are combined to create a stronger, lighter, or sometimes more flexible product.
One of the best-known composites on the market is reinforced plastic. Today, plastic is used in a pure form in most products, such as in toys and water bottles. However, it can be reinforced with fibers from other materials. This technique makes some of the strongest, lightest, and most versatile composites available.
A common use of composites is to reinforce a purer material with fiber from another pure or a composite one. The manufacturer will often add carbon or graphite fibers to a composite. Carbon fibers are conductive, have a remarkable combination of high modulus and tensile strength, have a very low (slightly negative) CTE (coefficient of thermal expansion), and offer good resistance to high temperatures. These characteristics make carbon an excellent fiber for various businesses, and it fuses easily with multiple materials.
In addition to carbon, fiberglass is a fairly common fiber reinforcement material. Fiberglass is not as strong or rigid as carbon fiber, but it does have specific attributes that make it desirable in many applications. Glass fiber is nonconductive (i.e., an insulator) and is generally invisible for most types of transmissions. This makes it a good choice for electrical or broadcast applications.
Resins are an essential part of composites. They are the matrices that hold the separate materials together without them being completely fused into a single pure material.
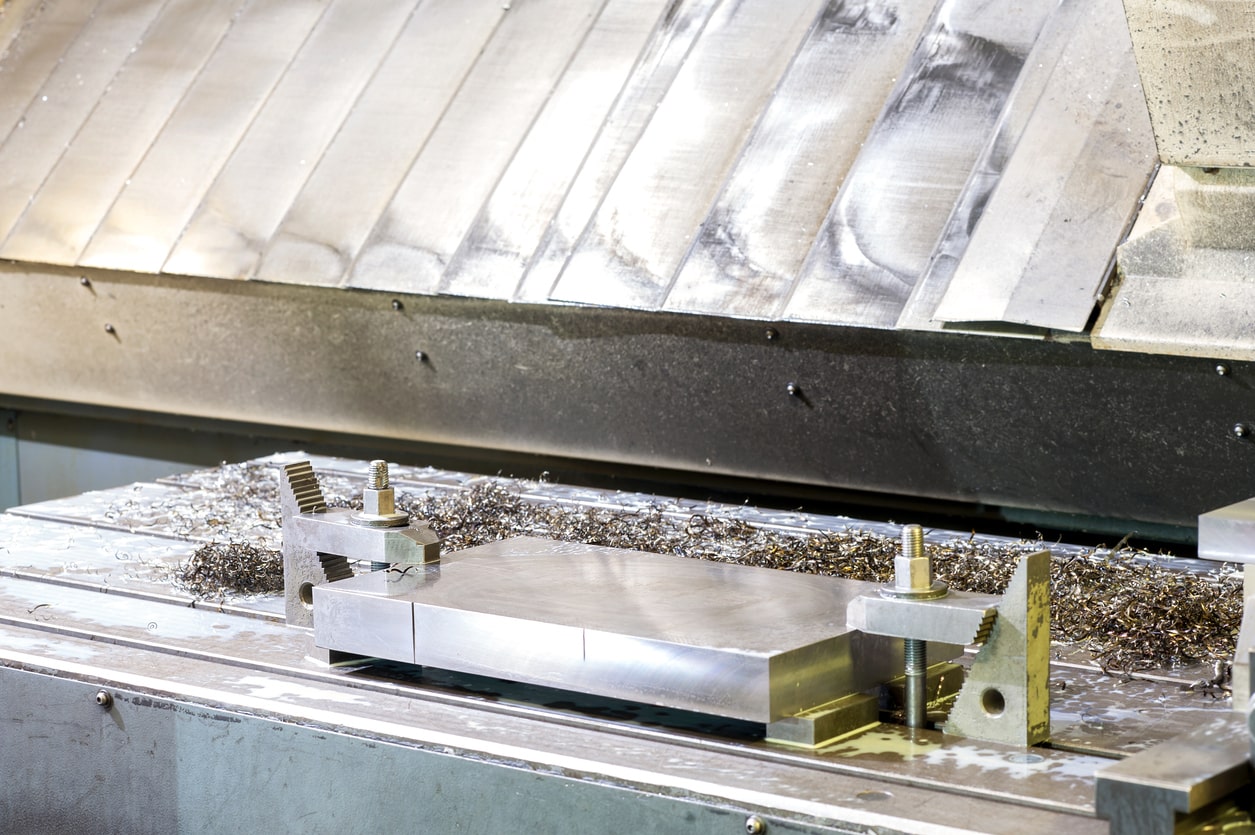
Which industries operate CNC machining?
CNC machining creates complex components required in a variety of industries. Its ability to accurately design with the help of a computer drives many companies to seek CNC machining for their operations. Everything from the medical industry to transportation and more relies on machining parts. This process allows for more complex custom designs than other production methods, thanks to technological advances.
The Aerospace Industry
CNC machining is used extensively in the aerospace industry, which often requires high tolerances, complex geometries, and the use of materials that do not lend themselves easily to other manufacturing methods.
In December 2009, Boeing flew the 787 Dreamliner for the first time, and one of its main advantages was its low weight. Its structure is made up of 50% composite materials. Since June 2013, Airbus has been conducting flight tests on the A350XWB. Among its long list of new features, Airbus uses 53% of composite materials. Leveraging composites has generated two significant benefits for the company. Not only has it saved money on fuel and panels, but it has also reduced fossil fuel emissions. The company has shortened flight times, meeting the Advisory Council for Aviation Research and Innovation (ACARE) goal of reducing CO2 by 50%, perceived noise by 50%, and NOx by 80%.
The Medical Industry
The medical industry relies on customized products to meet the many needs of patients. However, many devices used in the medical sector are disposable to protect patients from infectious diseases. Companies' installations in this sector require precision, speed, and high volumes.
A wide range of parts can be created using CNC machining. These correspond to the various materials and devices needed in the medical field—for example, implants, orthoses, MRI machines, medical instruments, etc.
Galen Robotics is a Californian medical technology developer offering new solutions for non-invasive surgery. The start-up uses CNC machining to create technology that stabilizes a surgeon's hands during delicate and precise nose, throat or ear operations. The company succeeded in building a robot using various parts, from sensor holders to end effector housings. This CNC manufacturing model provided the low-volume mix of parts needed to make this prototype at a competitive cost and time frame.
The Transportation Industry
While the aerospace industry requires high-speed performance engines, the transportation sector seeks durable and robust components. These qualities are necessary to move goods across the country.
CNC machines can create parts from many types of materials, everything from brakes to engine parts and even tools. High speed puts additional pressure on the vehicles in high-speed trains, requiring even greater precision in the fit of the parts used on the cars and engines.
The Oil and Gas Industry
The petrochemical industry requires well-machined parts that fit together precisely to manufacture the large machines used in refineries and on drilling platforms. A valve may leak without a perfect fit, a piston may not create pressure, or a cylinder may not fill.
Unlike other installations, drilling rigs are located in isolated areas. If a component does not function as it should, replacing or repairing it could interrupt production for several days. Rigs must produce optimized, ready-to-use components. They must be resistant to salt fog from the sea, dust from the desert, or snow from the northern plains.
The Military and Defense Industry
As the petrochemical industry, the defense sector uses parts that must be robust enough to withstand the harshest environments. In addition, military products must comply with government regulations.
The military encompasses so many industries that the products and parts created for defense may resemble those manufactured for other sectors, such as aviation, transportation, electronics, marine, medical, etc. More specifically, CNC machining can be used to design pins, casings, artillery, missiles, and fighter aircraft components.
The army is one of the industries with regularly updated CNC machines to have the latest technology at its disposal and thus protect the territory in the best possible way.
The Electronics Industry
The electronics industry needs CNC machining to create small components. Some even require laser precision to achieve the necessary fineness of up to 10 micrometers.
Most of the electronic devices we know today are manufactured by CNC machining. This is the case for custom electronic enclosures and the printed circuit boards inside these devices, as well as smartphones and tablets. CNC machining is particularly advantageous for printed circuit boards. This manufacturing model does not involve the use of chemicals, which demand other manufacturing processes.
The casing of the Apple MacBook laptop is CNC-milled from a single piece of aluminum. This method gives it the rigidity and performance of a solid one-piece material. This essential piece of Apple hardware has been part of the production line since 2008.
The Maritime Industry
The marine industry needs most of its components to be water-resistant, as they will be exposed either directly to water or to a wet environment. Electrical devices require housing to prevent water damage. In addition, seagoing vessels must be resistant to the corrosive effects of saltwater.
The marine industry also requires full portability of everything onboard ships. The components used in the devices must last and resist wear and tear, as no repairs can be made until the boat returns to shore.
The Naval Group, a French industrial group specializing in the naval defense industry and marine renewable energy, has exploited the CNC manufacturing model to create an anti-torpedo in 2019. The idea is to generate 360-degree acoustic signals to protect ships and submarines from torpedoes. CNC machining has made it possible to design very precise parts assembled into complex mechanical systems.
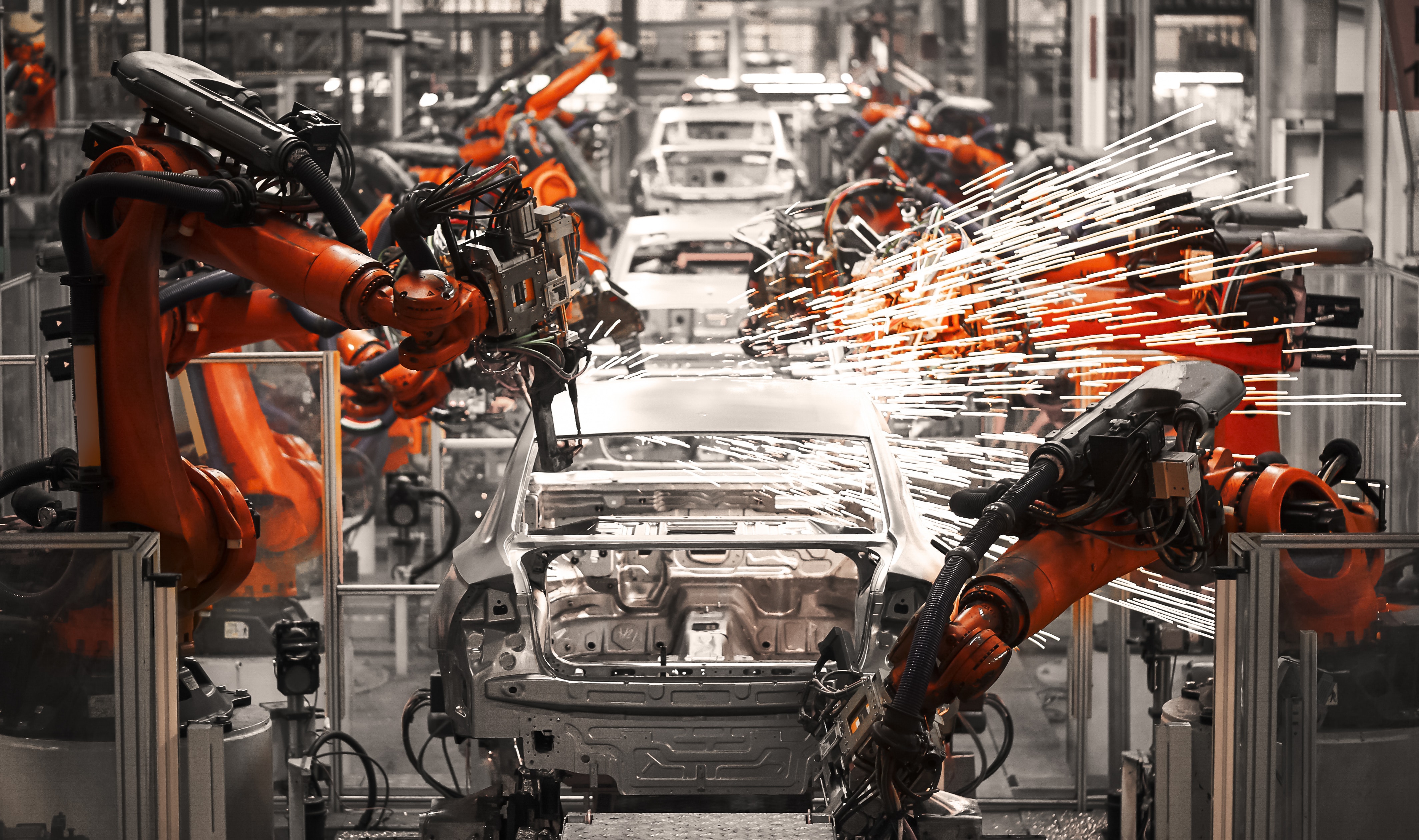
What is the current market for CNC machining?
The global market for CNC machines was estimated at $67.78 billion in 2019. Increasing advances in production technology have reduced the time required for manufacturing and made it possible to design components with a better finish. Newer tools do not require an operator to constantly monitor machine operation, limiting manual labor and saving the company money. Mass production plants have progressively adopted and developed CNC solutions because of their ability to produce high-precision parts. As a result, the market for CNC machining is growing, thanks to the ever-increasing demands of industries, for example, automotive, aerospace, and defense.
CNC Market Overview
Manufacturers are increasingly focusing on current technological trends in CNC machining to improve machine connectivity with operators and increase workshop flexibility. The evolution of the Internet of Things (IoT) and techniques related to Machine Learning lead to new functionalities. For example, it is now possible for an application to notify operators of the status of a machine on smartphones or PCs. In addition, these modern processes, used in CNC machines, reduce the time needed to make parts and limit the risk of errors.
What is the place of CNC machining on the world market?
The machine tool industry is fragmented, and many players hold an important position in the global market. Among the major players are Bosch Rexroth A. G. (Germany), DMG Mori Co, Ltd. (Japan), Fagor Automation (USA), and Okuma Corporation (Japan).
Stakeholders are adopting various strategic initiatives such as mergers and acquisitions, partnerships, and technology and new product development collaborations. For example, in 2016, FANUC, the world's leading manufacturer of industrial robots, announced a partnership with Cisco, Rockwell Automation, and Preferred Networks (PFN). The goal is to jointly develop and deploy the FANUC Intelligent Edge Link and Drive (FIELD) system.
The FIELD platform provides analyses that optimize manufacturing production by connecting to CNC machines, robots, peripherals, and sensors.
Companies are working together to implement systems for leading automotive manufacturers. Customers who have adopted them today are seeing reduced downtime and more significant cost savings.
Which regions of the world use CNC machining?
Asia Pacific dominates the market for CNC machines. In 2018, the region had the largest share, approximately 40%, of the global market. This leadership position can be attributed to the increased development of CNC tools in countries such as India, China, and Japan. Major manufacturers such as Okuma Corporation, Yamazaki Mazak Corporation, and DMG Mori Co, Ltd. are based in these countries. China enjoys dual importance as a supplier and user of CNC machines. It accounts for almost 10% of its global production, worth about $6 billion in 2018.
In 2016, China launched a plan called "Made in China 2025" to start the trend of smart factories. It is an industrial strategy that aims to make the country the leading supplier of high-quality and innovative manufactured goods internationally and domestically. In addition, the Indian market is also growing in the area of CNC machines.
In Europe, many companies are increasingly adopting CNC technology to achieve higher levels of accuracy and decrease the costs associated with wasted material. They have developed new milling tools that offer greater flexibility and the ability to perform multiple operations with the same machine. As a result, the companies have reduced their floor space requirements and operate with less workforce in the workplace.
The improved efficiency, speed of operation, and precision offered by metalworking industries, such as automotive and manufacturing, are driving this regional market. Germany is a world leader in the manufacturing sector and has a predominant share in the production and use of European CNC machines.
The United States seems to have stagnated in recent years. Renewable energy sources such as solar panels, wind turbines, and hybrid power plants have taken on major importance due to concerns about global warming and the depletion of conventional natural resources. In addition, the reliance on large-scale automation compels the power sector to deploy CNC machines throughout the region massively.
Which industries are most reliant on CNC machining?
The main sectors that operate CNC machines are the automotive, aerospace and defense, energy, construction equipment, and industrial sectors. They generally require components that demand very high levels of accuracy and good surface finish quality.
What are the current challenges in the CNC market?
The costs associated with purchasing and installing products are a challenge to market adoption.
In addition, in order to operate CNC tools, machinists must be trained and have the appropriate skills to perform the desired tasks.
To maintain parts' surface finish and accuracy, manufacturers must adhere to regular maintenance plans.
Also, low-carbon production or energy consumption and resources are becoming progressively essential to modern manufacturing.
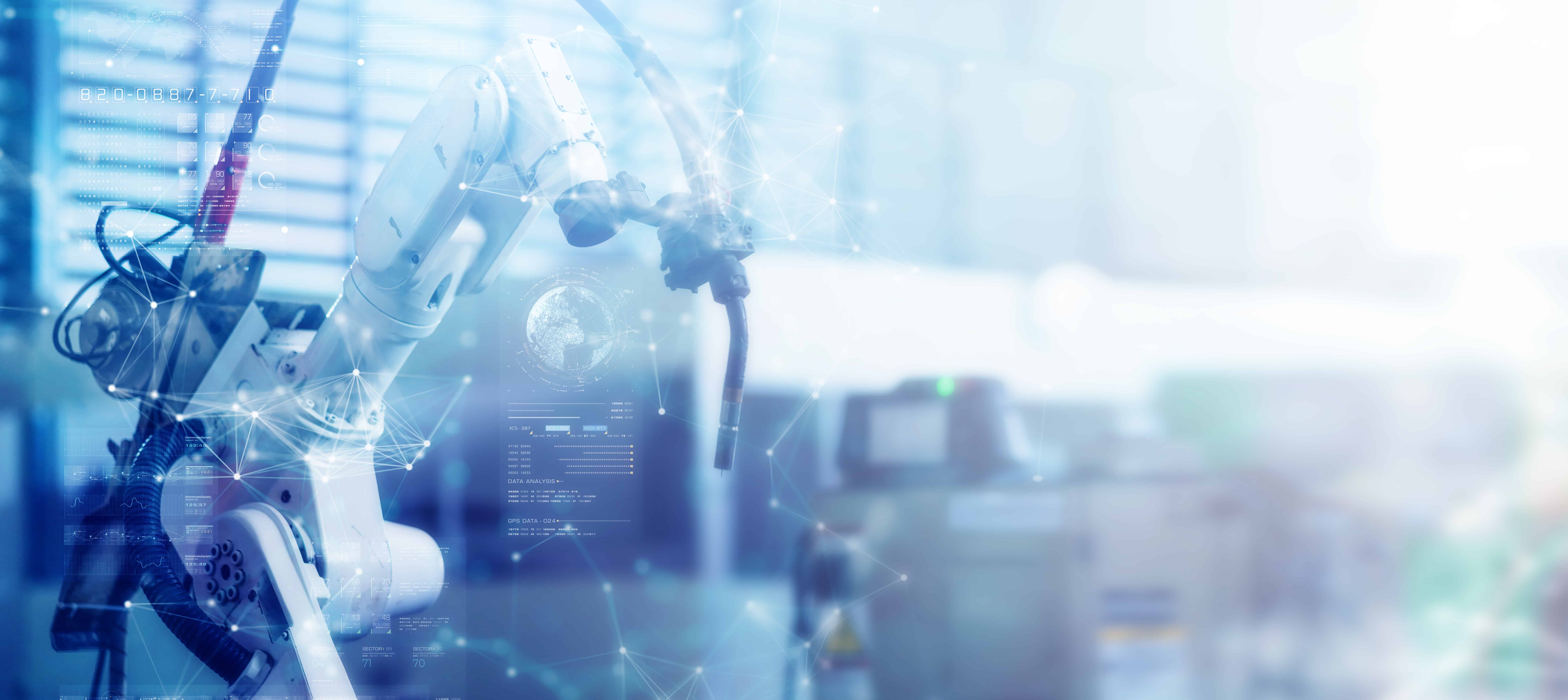
What are the CNC machining market trends?
The CNC machining market was valued at $67.78 billion in 2019. It is projected to reach $103.43 billion in 2025, driven by the ever-increasing demand from the automotive, industrial, and energy sectors. Three major trends stand out:
I. Factory automation
The integration of computers into CNC manufacturing has increased the speed and accuracy of the equipment tenfold. Today, everything from milling to turning to precision turning and cutting is done by CNC machining to maximize savings.
Indeed, the players must focus on efficient techniques in the very competitive market. Demand is rising as today's CNC machines reduce production time and minimize human error.
Thus, automated manufacturing is a growing demand, especially from the industrial and automotive sectors.
Leading companies are investing in R&D to improve tool design so that they can perform multiple operations independently, thereby ameliorating plant productivity.
For example, in 2018, Hurco Companies, Inc. invested $4.7 million in an R&D program to significantly improve products and develop new ones. The FIELD system platform connected CNC machines, robots, peripherals, and sensors to provide analysis for manufacturing process optimization. Such initiatives are expected to drive market growth over the next eight years.
II. New technologies
The automotive industry is adopting technologies such as IoT, Artificial Intelligence, Machine Learning, and Robotics, among others, that will meet the needs of users whose demand is already exploding worldwide.
Europe is expected to experience considerable growth, thanks in particular to a large base of automotive companies that should be the driving force. On a vertical industry basis, the automotive segment has the highest CAGR of 7.9% over the forecast period. In addition, the presence of high-end machine manufacturers and leading technology developers, such as Datron AG, Dr. Johannes Heidenahain GmbH, and Sandvik AB, is expected to drive growth in the coming years.
In May 2018, Bonsai, the AI start-up, and Siemens deployed Artificial Intelligence on a machine in a test environment. For the first time, Deep Learning was successfully applied to the self-calibration of CNC machines. This model allowed the tool to self-calibrate 30 times faster than an expert human operator.
CNC machining will continue to modernize. The integration of 3D printing in CNC machines should provide better multi-material capability with a low waste of resources. Virtual and augmented reality will make manufacturing even more immersive. Machining service providers can customize every detail of a product design to maximize its use.
III. The production of renewable energies
Growing concerns about global warming and the depletion of energy supplies are leading companies to turn to 100% renewable energy. CNC machining will help build systems that exploit alternative energy sources like solar and hydraulic energy. CNC machines play an important role in electricity production, as this process requires large-scale automation. Thus, these concerns promote the growth of this market.
In 2018, Flow Power, an Australian commercial energy retailer, signed a contract with ANCA, a CNC machine, and system market leader. This agreement, one of the first of its kind in Australia, employs renewable energy from the Ararat wind farm to provide ANCA with direct access to long-term power at wholesale prices. This renewable energy can be used in real-time to offset grid electricity consumption, saving businesses thousands of dollars in electricity costs and reducing overall emissions.
Get multiple quotes for your parts in seconds