Metal manufacturing
Upload your design, get your metal manufacturing quote, choose your manufacturer and receive your parts!
SECURE PAYMENTS
Via payment card or purchase order
PROTECTED IP
Your data is confidential and secure with us. Use your own Non Disclosure Agreement
INSTANT QUOTE
For 3D Printing and CNC Machining, get quote in few seconds.
Metal manufacturing with 3DEXPERIENCE Make
3DEXPERIENCE Make is an On-Demand metal Manufacturing platform, which connects designers or engineers with industrial 3D Printing service providers. Our service providers are mostly based in North America (the United States and Canada) and in Europe (United Kingdom, France, Netherlands, Germany, etc...). We offer metal manufacturing options across multiple processes such as 3D printing, CNC machining, Laser cutting, and Injection molding.
Metal manufacturing is well suited for products where heat resistance and higher strength are key. Metal is also a material able to be fabricated through a high number of processes which gives a higher versatility.
Thanks to our powerful algorithm, you can get a quote in seconds for your metal manufacturing project from dozens of metal manufacturing providers.
Our metal manufacturing network of service providers is handling projects in various industries such as Aerospace & Defense, Business Services, Construction, Consumer goods & retail, Energy & Materials, High-Tech, Home & Lifestyle, Industrial Equipment, Life Sciences & Healthcare, Marine & offshore, or Transportation & Mobility.
Our network of service providers offers dozen of metal materials for your projects such as Aluminium, Nickel, Stainless, Steel, Titanium and a lot more to be found on 3DEXPERIENCE Make.
Discover How 3DEXPERIENCE Marketplaces Boost Your Design to Manufacturing Process
You’re in good company. Thousands of leading companies from all industries use our solutions.
Our network of metal manufacturing providers
- United States
- Canada
- United Kingdom
- France
- Germany
- Netherlands
and many more...
Online manufacturing service: how does it work?
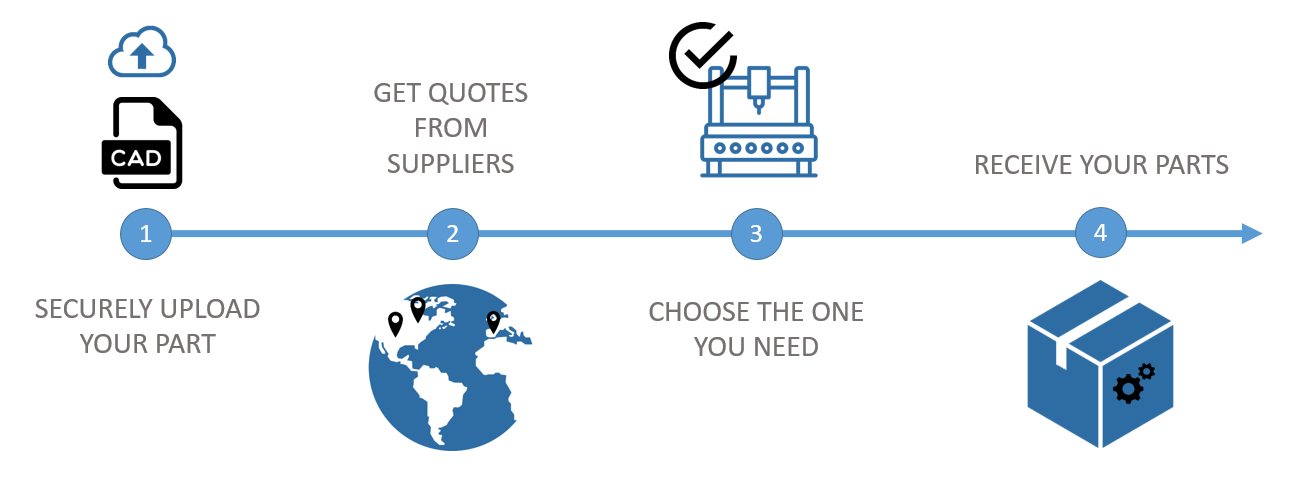
- Securely upload your part
- Get quotes from suppliers
- Choose the one you need
- Receive your parts
Metal materials available with our service providers
Metal materials for 3D printing processes
- 17-4
- 316/316 L
- ALSI10mg
- INCONEL 625
- INCONEL 718
- TI6AL4V
Metal materials for CNC machining
- Aluminium
- Nickel
- Stainless
- Steel
- Titanium
Metal materials for Injection Molding processes
- Aluminium
- Stainless
Metal materials for cutting & forming processes
- Aluminium
- Steel
What are the metal manufacturing processes available at 3DEXPERIENCE Make?
3D Printing - Additive manufacturing
FDM, SLS, MJF, BJ, SLA...
Cutting
Laser cutting, Water cutting, Blade
Forming
Sheet Metal, Extrusion, Forming, Stamping
(Milling, turning & spark machining)
CNC Machining - Substractive
Milling, turning & spark machining
Features to help you
Check & repair or Geometry check is a feature that helps you to understand Geometry issue of your part and could repair it live and online.
Check & Repair
Check & repair or Geometry check is a feature that helps you to detect geometry issue on your part and repair it online and live.
Manufacturability Check
This feature is available only for 3D Printing service. It helps you check the manufacturability of your part, depending on the materials and the process.
Instant quote engine
Receive in seconds several quotes thanks to our instant quote engine.
What is metal manufacturing?
Metal manufacturing has been used by humans over the millennia. Some objects have even been traced as far back as thousands of years BC, depending on the metal.
Metals are generally hard, opaque, and shiny materials that exhibit good electrical and thermal conductivity. Although approximately 91 of the 118 elements of the periodic table are metals, they can be either elements, compounds, or alloys. They are generally malleable so that they can be shaped by hammering or pressing without breaking or cracking. Metals are also fusible, meaning they can be fused or melted and exhibit a ductility that makes it possible to stretch them out into a thin wire. Consequently, metals are an important part of our lives and can be found at every facet where they are used in high-rise buildings, bridge construction, automobiles, home appliances, jewelry, tools, pipes, railways, and many other places.
Metal manufacturing is the driving force for the technical advancement of metalworking. It aims to apply the science behind the metal to the most appropriate application, for instance, in consumer and manufactured products, transportation, railway, aeronautics, marine, and many other fields. As 3D Printing technology has advanced, so have the choices of applicable metals. Many different processes are used to shape metal including, casting, forging, rolling, laser cladding, extrusion, sintering, machining, fabrication, and 3D printing. Metals for standard manufacturing processes.
What is metal?
Metals are opaque materials that appear shiny when polished. They are good conductors of heat and electricity and have a relatively high melting point.
Most are generally hard, but soft enough to be shaped by hammering or pressure without breaking or cracking.
They are versatile enough to be fused or mixed and can be shaped into large solid blocks and sheets or stretched into long thin strands (a property known as ductility).
About 95 of the 118 elements in the periodic table are metals, 80 of which are commonly used in manufacturing.
Where do metals come from?
Metals are found in ores, usually in rocks, throughout the earth's crust. They may be found in pure form, such as aluminium, copper and gold, or mixed with other elements that will need to be separated.
The method of extraction and separation will depend on the metal and the impurities present. Most involve a combination of methods:
Mining - Once the metal or ore is located, it is extracted from the ground using explosives or excavators.
Crushing and grinding - Powerful mechanical crushers and grinders pulverise the rock into a fine powder to facilitate the extraction of metals.
Extraction - Various techniques are used to separate the metal or ore from other minerals and impurities. These include mixing with water, dissolving the ore with solvents and using magnets.
Refining - The remaining impurities are separated using more complex methods. These include smelting, which uses heat and a chemical agent, and electrolysis, which uses an acid and electricity. The result is a purer form of the metal, but it may still contain impurities.
Casting - Metals can be transformed and/or combined with other elements to form alloys. This is usually done when the elements are in liquid form. Once the final metal is obtained, this molten mixture will be cast into moulds or mechanically extruded into various forms.
The most common are sheets, billets, rods, tubes, plates, bars and wire. These are then cut into different shapes and sizes depending on the intended end use and shipped to manufacturers to be processed into countless products.
What are the most common metals?
- Aluminium is a soft, non-magnetic, ductile and light metal that is extremely resistant to corrosion. It is the second most produced metal after iron. Aluminium and its alloys are essential to the aerospace, transport and construction industries, and have many other uses ranging from beverage containers to electrical transmission lines.
- Cobalt is a hard, shiny metal that has been used for centuries in jewellery, paints and to add a distinctive blue tint to glass. Today, cobalt is mainly used to create high performance alloys that are strong, magnetic and durable. It is also used in the production of batteries, catalysts and pigments, and in radioisotopes.
- Copper is a soft, malleable and ductile metal. Its main industrial use is as a conductor of heat and electricity. Copper is also used in buildings, mainly for roofing, and as a compound for pigments, antibacterial agents, fungicides and wood preservatives.
- Gold is a precious metal that is dense, malleable and ductile. Its main industrial use is in the manufacture of electrical contacts and connectors. Gold is also used for infrared shielding, coloured glass production, gold leafing and tooth restoration, and is often alloyed for use in jewellery.
- Iron is one of the most common elements on Earth and is therefore the cheapest metal. Nearly 90% of all metal refined today is iron, mainly to make alloy steel and civil engineering structures. Iron is very susceptible to oxidation (rusting) when it comes into contact with oxygen. It is an essential mineral for the health of all living things and an adult human body contains about 4 grams of iron.
- Molybdenum exists in different oxidation states in minerals. As it rapidly forms hard and stable carbides in alloys, most of the world's molybdenum production is used in steel alloys. It is commonly found in structural steel, stainless steel, chemicals, tool steels and cast iron. In its pure state, it is also used as a fertiliser, in medical imaging and as a means of detecting pollution in power stations.
- Nickel is a hard, ductile metal and mainly an alloy. It is mainly used in nickel steels and nickel castings because of its tensile strength and toughness. Nickel is also used in coins, rechargeable batteries, for plating (when a thin layer of metal is added to the outside of a material) and as a green tint in glass.
- Niobium is a soft, ductile metal used mainly in alloys, including the special steel used in gas pipelines. It is also an important superalloy for jet and rocket engines because of its thermal stability. Other applications include welding, electronics, optics and jewellery.
- Platinum is a dense, malleable and ductile precious metal. It is one of the least reactive metals and is highly resistant to corrosion, even at high temperatures. It is used in catalytic converters, laboratory equipment, electrical contacts and electrodes, dental equipment and jewellery.
- Silver is a soft precious metal with the highest electrical and thermal conductivity and reflectivity of any metal. It is used in solar panels, water filtration, tableware, ornaments and jewellery. Silver compounds are used in photography, X-rays, disinfectants and medical instruments. In an industrial context, silver is used to produce electrical contacts and conductors, specialised mirrors, window coverings and as a catalyst for chemical reactions.
- Tantalum is a rare, inert, hard and highly corrosion-resistant metal. It is used to produce alloys for jet engine components, chemical processing equipment and nuclear reactors. Tantalum capacitors are found in electronic equipment such as mobile phones, video game consoles and computers.
- Titanium is one of the strongest and most expensive metals. Titanium alloys are used by the aerospace, automotive and marine industries for their lightness and strength properties. The chemical and petrochemical industries use it to produce process equipment because of its high corrosion resistance. It is also found in sporting goods and eyewear, and titanium oxides are commonly used for pigments, additives and coatings.
- Tungsten is a very stable rare metal found naturally on Earth, almost exclusively in chemical compounds, with the highest melting point of all the elements. It is mainly used to produce hard materials, notably tungsten carbide, as well as in the production of electronics and in alloys and steel.
- Zinc is a hard, brittle metal that is an essential mineral for the health of all living things. One of its main uses is in iron plating (hot-dip galvanising) because of its resistance to corrosion. It is also used in electric batteries and is a common alloy in brass.
- Zirconium is a soft, ductile and malleable metal that is strong at room temperature, although it is hard and brittle at lower purities. It is highly resistant to corrosion by alkalis, acids, salt water and other agents. As a metal, zirconium is used in the nuclear and aerospace industries, and its isotopes are used in medical imaging. As a compound, it is used in high temperature and biomedical applications.
What are the most common alloy metals?
The properties of pure metals can be enhanced by mixing them with other metals or elements to make alloys.
- Brass is an alloy of copper and zinc that is frequently used in musical instruments because of its acoustic properties and ductility. It is also used in a wide range of applications that seek a less expensive substitute for precious metals.
- Bronze is an alloy composed mainly of copper and about 12% tin, mixed with other metals and non-metals. Common applications include coins and medals, sculptures, musical instruments, bearings, electrical connectors and springs.
- Cast iron is a group of iron-carbon alloys with a carbon content of more than 2%. Although cast iron tends to be brittle, its relatively low melting point, good flowability, castability, machinability and resistance to deformation and wear make it a common engineering material. Applications include pipes, structures, machinery and automotive parts. It also has a high resistance to oxidation.
- Cast steel is made by melting wrought (hammered) iron with charcoal. It is similar to cast iron but contains much less carbon, between 0.1 and 0.5%. Cast steel is more difficult to cast and shrinks more than cast iron, requiring a more thorough inspection process.
- Ferrous alloys are iron-based alloys used in the production of steel, iron and alloys.
- Low melting point alloys (or fusible alloys) are used as coolants because of their stability to heat, and are also used in the bonding of nuclear reactors and in automatic fire sprinklers.
- Non-ferrous alloys are alloys that do not contain much iron. Although they are more expensive than iron-based (ferrous) alloys, they weigh less, are non-magnetic, have higher conductivity and are corrosion resistant.
- Steel is an alloy of iron, carbon and other elements. It is a major component of buildings, infrastructure, tools, ships, automobiles, machinery and appliances because of its high tensile strength and low cost. There are several grades of steel, including long steel, flat carbon steel, weathering steel (COR-TEN), stainless steel and low carbon steel.
- Stainless steel is a steel alloy with a chromium content of more than 11%, which prevents the material from rusting and gives it heat-resistant properties. It is extremely resistant to corrosion and is widely used in the production of industrial equipment, cutlery, kitchen utensils, surgical instruments, architecture, large appliances and 3D printing.
- Tool steel refers to a variety of carbon and alloy steels that are extremely wear resistant and capable of maintaining a sharp edge at high temperatures. It is therefore an ideal material for making tools that cut, press, extrude or stamp metals or other substances.
What are the metal manufacturing processes?
The techniques used in metal fabrication vary, but almost all start with the material in the form of sheet, billet, rod, tube, plate, bar or wire.
- Turning - A cylindrical piece of metal is held in a lathe and rotated while a cutting tool is held against it at different points and depths to precisely remove material to form the desired shape.
- Forming - High-powered mechanical presses use pressure and heavy loads to bend, stretch, cut, roll and form metal parts.
- Milling - Rotating milling cutters mounted on or in a machine efficiently and accurately cut the material of a metal part into the desired shape. Traditional "milling machines" evolved into "machining centres" in the 1960s with the advent of computer numerical control (CNC) and automatic tool changers.
- Forging - Metal is shaped by hammering, pressing or rolling. Historically done by hand, modern forging is done with hammer presses powered by compressed air, electricity, hydraulics or steam. Forging is generally classified according to the temperature at which the process is carried out, either cold, warm or hot.
- Welding - Two or more pieces of metal are melted and joined together by the application of high heat and pressure. Welding uses a number of different heat sources, including gas flame, electric arc, laser, electron beam, friction and ultrasound.
- Casting - The metal is heated to a liquid state and then poured into a mould. The mould and metal are allowed to cool until the liquid metal solidifies, after which it can be removed from the mould. Casting is the preferred process for producing complex shapes that would otherwise be too difficult or too expensive to make by other methods.
- Extrusion - Hot or cold metal is pushed through a die of the desired shape or profile. The material can be pushed continuously to produce a single long line, or semi-continuously to create many separate parts. This process is useful for creating very complex cross-sections, with the added benefit of creating a quality surface finish, a strong final object and a high degree of design freedom in the shape of the die.
What are the advantages of metal?
- Versatility - there are many different metals and alloys, each with its own properties and characteristics.
- Ease of manufacture - metal is relatively easy to work with, can be formed into objects of any size and shape, and can be finished in many different ways.
- Low cost - goods made from metal are easy and affordable to mass produce using a wide range of different processes, although the source material is relatively complicated to extract and refine.
- Conductivity - Metals conduct electricity, making them essential for wires and electronic components.
- Strength - Most metals used in manufacturing are strong, durable, heat resistant, have a high melting point and are easy to clean. Combining metals to create an alloy can further enhance these properties.
- Reuse - With the exception of lead and mercury, almost all other metals can be, and increasingly are being, recycled. For example, nearly 700 million tonnes of steel and over 30 million tonnes of aluminium are recycled each year worldwide.
What are the limits of metal?
- Mining - The processes used to extract metal from the ground can have a negative impact on the environment.
- Limited resources - Only a certain amount of metal is found in the earth's crust and huge quantities are currently unavailable because they are too deep underground.
- Corrosion - Some metals rust over time, which weakens them structurally and affects their appearance.
- High costs - The start-up costs associated with the manufacture of metal parts are high, particularly for large volumes, as it requires expensive machinery and specialised tooling. In addition, some of the chemicals used in the various forming and finishing methods are hazardous and are therefore controlled substances that require a licence to use.
- Better alternatives - Metals can be much stronger than most plastics, but plastics are generally lighter, easier to machine, do not require as much post-production finishing and are more resistant to corrosion. Using metal in a building, for example, can be much more expensive and time-consuming than using a material like concrete.
What metals can be used for 3D printing?
3D printing, sometimes referred to as 'additive manufacturing', covers a number of different processes and techniques. All involve a material, usually plastic or metal, being deposited in several thin layers to create a shape.
Plastic 3D printing dates back to the 1980s. Metal 3D printing emerged in the 1990s, after the invention of laser fusion and sintering (heating without fusion) techniques.
As the technology evolved, so did the choice of metal material:
- Aluminium - Ultra-fine grains of aluminium powder are laser sintered to produce end-use metal parts that are just as good as their machined counterparts. This technique is commonly used to produce fully functional parts, replacement parts and jewellery. The two main 3D printing techniques for aluminium are direct metal laser sintering (DMLS) and selective laser melting (SLM).
- Brass - typically used to produce detailed miniatures, sculptures, jewellery or pre-print tests (to shape before producing with gold or silver).
- Bronze - an affordable and strong material for metal printing, commonly used for the same applications as brass.
- Copper - used in printing to produce small decorative designs such as coins, medals, connectors and statutes.
- Gold - is mainly used for printing 14K or 18K solid gold jewellery mixed with an alloy for durability.
- Stainless steel - offers a high level of detail and strength, making it suitable for items such as miniature figures, jewellery, key rings and bolts.
- Sterling Silver - 3D printed silver models are made up of 92.5% pure silver and 7.5% of another metal, usually copper. Its most common use in 3D printing is in jewellery.
- Steel - the most affordable form of metal 3D printing; steel powder is infused with bronze to form a material capable of making very strong and large objects.
- Titanium - 3D printed objects made from titanium are very strong, accurate and just as good as their machined counterparts. This material shares the same properties and applications as aluminium.
Discover our other materials for manufacturing
Get multiple quotes for your parts in seconds