CNC Machining in the medical sector
The precision, personalization, and rapid prototyping capabilities of CNC machining have revolutionized the medical sector and transformed patient care.
What is CNC machining?
Computer Numerical Control (CNC) machining is a production technique that uses computer-controlled machines to accurately cut, shape and form parts. It can create complex geometries from materials such as metal (aluminum, steel, titanium), plastic or wood.
The term CNC machining covers several processes, including cutting, milling, turning, drilling, grinding, routing and polishing. By following pre-programmed instructions, CNC machines ensure high levels of consistency, accuracy and reliability.
CNC machining is very cost-efficient as waste material, defects, manual work and setup times are all minimized. This makes it suitable for both large and low-volume production and for creating one-off custom pieces. Modern CNC machines boast advanced features like multi-axis capabilities, automated tool changers and advanced automation, further optimizing production efficiency.
The versatility of CNC machining has seen it adopted in every manufacturing sector, including automotive, aerospace, electronics, medical and more. Additionally, the advent of desktop-sized CNC machines has made the technology accessible to hobbyists and makers. These miniaturized machines are usually more user-friendly and tailored for smaller-scale projects.
To learn more, visit our 3DEXPERIENCE GUIDE TO CNC MACHINING
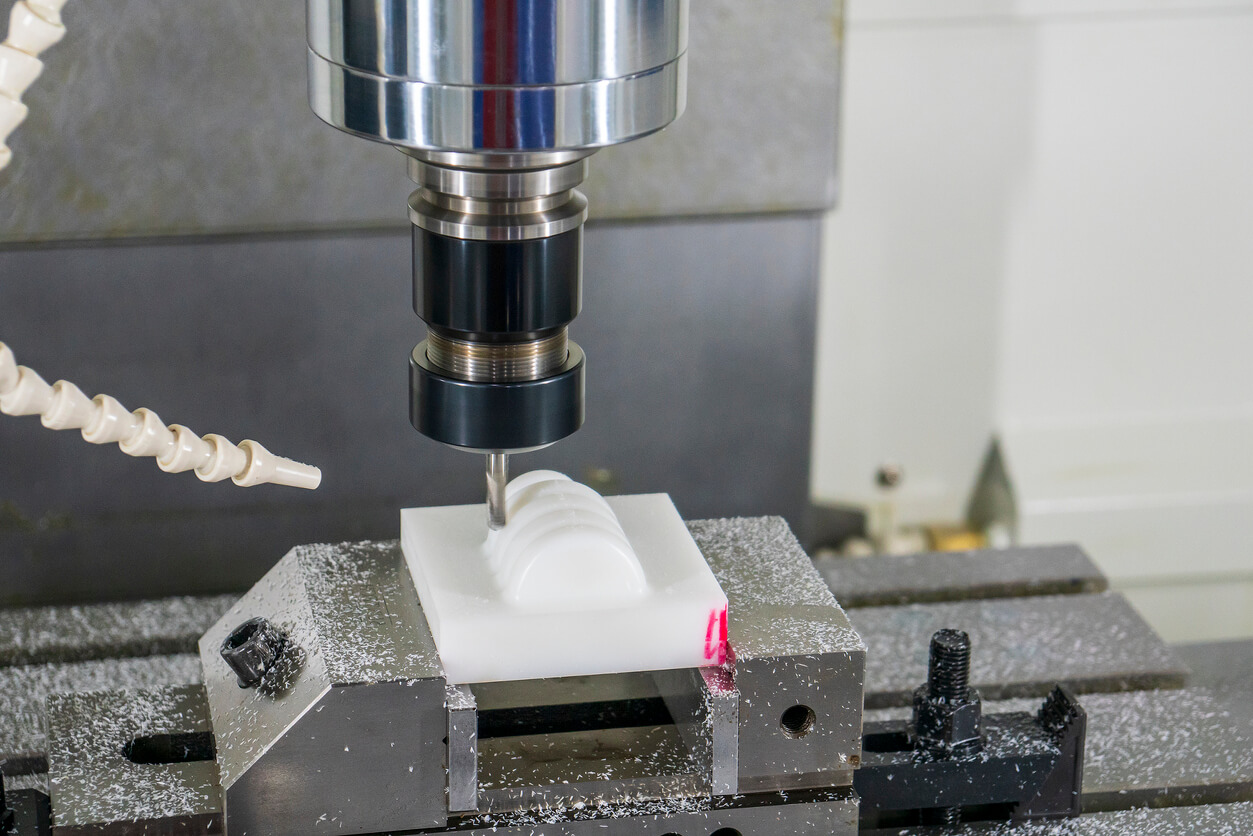
How CNC machining transformed the medical sector
How CNC machining transformed the medical sector
CNC machining has, revolutionized how medical devices and equipment are designed, manufactured, personalized and used. The precision, customization and speed of CNC machining have transformed patient care, enabling personalized treatments and improved surgical outcomes.
The technology has paved the way for groundbreaking innovations in prosthetics, instruments and treatments and driven advances in many areas of healthcare.
CNC machining brings many advantages to the medical sector, including:
- PRECISION AND ACCURACY
CNC machines operate with extraordinary precision. This level of accuracy is crucial in the production of surgical instruments, implants and micro-devices used in minimally invasive surgery. The precision and consistency offered by CNC machining improve performance and reduce the risk of complications during medical procedures.
This is especially important for surgeons, who rely on ultra-precise and reliable instruments to perform delicate tasks. From scalpel handles to robotic surgical assistants, CNC machining delivers high-quality tools that enhance precision and patient safety.
- CUSTOMIZATION AND PERSONALIZATION
CNC machining enables the creation of personalized medical parts and devices tailored to a patient’s unique anatomy. This capability enables the creation of personalized orthopedic implants, dental prosthetics, hearing aids and other devices.
Using patient-specific data, such as 3D scans or MRI images, CNC machines can precisely fabricate items that perfectly fit a patient’s body. This improves comfort, functionality and treatment outcomes and accelerates patient recovery.
- COMPLEX SHAPES AND STRUCTURES
CNC machining can produce complex geometries and intricate internal structures that other manufacturing methods often struggle to achieve. The ability to precisely carve out internal cavities, channels and delicate features is particularly valuable when fabricating implants, micro-devices and surgical instruments.
- RAPID PROTOTYPING
Prototyping allows medical engineers and designers to create functional models of parts and devices, enabling them to assess the design, fit and function before starting production. The combination of computer-aided design (CAD) software and CNC machines enables digital designs to be quickly converted into physical prototypes.
This allows for iterative design improvements and helps ensure medical devices are thoroughly tested and optimized ahead of release. In a constantly evolving field, rapid prototyping enhances innovation and helps bring new medical advancements to market faster.
- PROCESS OPTIMIZATION
The integration of CNC machining with advanced technologies such as automation and artificial intelligence (AI) has minimized errors and automated quality control processes. This has led to increased efficiency, reduced production times and improved product quality, all of which help to enhance patient outcomes.
Additionally, automated CNC systems can operate continuously with minimal human interaction between operations. Some CNC machines are also capable of multi-axis machining and performing tasks on different surfaces of a part at once.
By reprogramming machines, manufacturers can rapidly switch between producing one component and another. This reduces changeover time and means different parts can be made on the same machine during a single shift. These capabilities help accelerate production cycles, reduce downtime and increase overall output.
- FLEXIBLE MATERIAL CHOICE
CNC machining is compatible with a range of materials, including metals, plastics, and composite materials. This versatility allows manufacturers to choose the most suitable materials for specific medical applications, considering factors like biocompatibility, durability and functionality.
- COST SAVINGS
While industrial CNC machines can be expensive, they offer significant cost-saving opportunities in the long run. By removing the need for dedicated jigs, fixtures and specialized tooling for each part, CNC machining helps minimize setup times, streamline production and reduce manufacturing costs.
The technology also reduces waste and cost through material optimization. This is particularly crucial in the medical sector, with implants often made using high-value materials like titanium and platinum. The improved efficiency and productivity CNC machining provides also contribute to cost savings over time.
Applications of CNC machining in the medical sector
CNC machining is used to produce numerous medical parts and components. Just some of them include:
- SURGICAL TOOLS
CNC machining is extensively used for manufacturing surgical tools with complex geometries and high precision requirements. Scalpels, forceps, retractors and other surgical tools can be precisely machined to meet specific design specifications, ensuring optimal performance and safety during surgical procedures.
- IMPLANTS
CNC machining plays a critical role in producing medical implants, such as orthopedic implants like hip and knee replacements, dental implants and spinal implants. These implants require exceptional dimensional accuracy and surface finish to ensure proper fit, stability and biocompatibility within the patient's body. CNC machining also allows for the production of customized implants tailored to unique patient anatomy.
- PROSTHETICS AND ORTHOTICS
CNC machining is employed to create customized prosthetic limbs and orthotic devices for individuals with limb loss or musculoskeletal conditions. By utilizing patient-specific data, collected via 3D scans and digital images, CNC machines can make prosthetics and orthotics that precisely fit a patient's body, improving comfort, mobility and quality of life.
- MICRODEVICES
CNC machining is utilized in the production of microdevices used in various medical applications, including biosensors and diagnostic systems. These devices often require intricate geometries and ultra-high precision, which can be achieved with CNC machining techniques. The ability to accurately and consistently fabricate microdevices contributes to advancements in diagnostics, drug delivery systems and surgical procedures.
- MEDICAL DEVICE ENCLOSURES AND HOUSINGS
CNC machining is used to produce many enclosures and housings for medical devices, including diagnostic equipment, monitoring devices and portable medical devices. These components require precise machining to accommodate internal components, provide proper structural integrity and ensure ease of use for healthcare professionals and patients.
- DIAGNOSTIC EQUIPMENT
CNC machining is used to produce components and parts for various diagnostic equipment, including imaging systems like MRI and CT scanners, laboratory analyzers and point-of-care testing devices. CNC machining ensures the production of precise and reliable components that contribute to the accuracy and efficiency of diagnostic procedures.
- INSTRUMENTS FOR MINIMALLY INVASIVE SURGERY
CNC machining is employed in the production of instruments used in minimally invasive surgeries, such as laparoscopy, endoscopy and robotic-assisted procedures. These instruments require intricate designs, precise dimensions and optimal ergonomics to enable surgeons to perform procedures with enhanced dexterity and minimal invasiveness. CNC machining ensures the production of high-quality instruments that meet these requirements.
- REHABILITATION AND ASSISTIVE DEVICES
CNC machining is used to produce rehabilitation and assistive devices, such as braces, supports and mobility aids. These devices need to be customized to the patient's specific requirements and provide optimal support and functionality. CNC machining enables the production of precisely tailored devices that assist individuals with physical impairments in their daily activities.
Limitations of CNC machining in the medical sector
While CNC machining is highly versatile and widely used in the medical sector, it does have certain limitations. Although many of these can be overcome through process optimization, tooling advancements and a thorough understanding of the design requirements.
- COMPLEXITY OF SHAPES
CNC machining is well-suited for producing parts with relatively simple to moderately complex geometries. However, when it comes to very intricate or highly contoured shapes, CNC machining may have limitations. For example, there may be constraints related to undercuts, deep cavities or internal features that are difficult to access with standard cutting tools. Complex or highly intricate parts may require specialized tooling or additional operations, adding time and cost to manufacturing.
- MATERIAL RESTRICTIONS
CNC machining can work with many materials commonly used in the medical sector, such as aluminum, titanium, plastics and composites. Some materials, such as certain ceramics and polymers, may pose a challenge in terms of machinability or may require specialized equipment or tooling. Also, certain heat-sensitive materials can experience thermal deformation during the machining process that could comprise accuracy.
- LIMITED PRODUCTION SPEED
While CNC machines are capable of high precision, the production speed may be slower than other manufacturing methods, especially for complex and intricate designs. This slower production speed can impact overall manufacturing timelines, particularly when large volumes of medical devices are required.
- SIZE LIMITATIONS
Industrial CNC machines come in various sizes. The size of the machine defines the maximum size of parts it can accommodate. Very large or bulk items may exceed the working capacity of standard CNC machines, making alternative manufacturing methods a better option.
- SURFACE FINISHES
While CNC machining can achieve high precision and accuracy, it may not always provide the desired surface finish. Medical parts often have strict surface finish specifications that may require additional processes, such as polishing or surface treatment, to achieve. These extra steps add time and cost to the manufacturing process.
- OPERATOR SKILL AND TRAINING
CNC machining requires skilled operators to program, operate and maintain the machines effectively. The complexity of CNC programming and operation requires proper training and expertise. Finding and retaining skilled CNC operators can be a challenge, particularly where there is a shortage of qualified personnel.
The future of CNC machining in the medical sector
The future of CNC machining in the medical sector looks extremely promising. Advancements in automation, materials, integration with additive manufacturing, digital technologies, customization and quality assurance will continue to drive innovation and lead to the development of safer, more efficient and patient-centric medical devices.
- ENHANCED AUTOMATION AND DIGITALIZATION
Automation is playing an ever-more vital role in CNC machining in the medical sector. The use of robotics, artificial intelligence (AI) and machine learning (ML) technologies will further automate tasks such as material handling and tool changing. This will lead to improve efficiency, reduced build times and increased productivity in medical device manufacturing.
CNC machining will integrate more seamlessly with digital technologies such as computer-aided design (CAD), computer-aided manufacturing (CAM) and simulation tools. This will streamline the design-to-production workflow, enabling faster prototyping and testing, iterative design improvements and enhanced quality control. Real-time data analysis, monitoring and feedback will help ensure the highest quality standards, reduce errors and optimize machining parameters for improved efficiency and accuracy.
- CUSTOMIZATION AND PERSONALIZATION
The future will see an increased emphasis on customized and personalized medical devices. CNC machining will continue to play a crucial role in making of patient-specific implants, prosthetics, and surgical instruments. Integration with advanced imaging technologies, such as medical imaging and 3D scanning, will allow for precise patient anatomical data to be translated into customized device designs, improving patient outcomes and satisfaction.
- REGULATORY COMPLIANCE
As the medical sector becomes more stringent in terms of regulatory compliance and quality standards, CNC machining will need to adapt. Manufacturers will focus on ensuring traceability, validation and documentation throughout the production process to meet regulatory requirements. CNC machining will play a crucial role in maintaining consistency, repeatability and adherence to these standards.
- MINIATURIZATION
The future will see an increased focus on miniaturized and microfabricated medical devices. CNC machining will be vital in fabricating these tiny devices with intricate features and high precision. Such devices can enable minimally invasive procedures, targeted drug delivery and advancements in diagnostics, paving the way for personalized medicine and improved patient outcomes.
- ADVANCED MATERIALS
With ongoing advancements in materials science, manufacturers will have access to novel materials with improved biocompatibility, strength and durability. CNC machining will evolve to meet the challenges associated with machining these materials, enabling the production of innovative medical devices.
- INTEGRATION WITH 3D PRINTING
Integrating CNC machining with 3D printing will lead to new possibilities in the medical sector. Combining the precision of CNC machining with the design freedom of 3D printing can result in complex, patient-specific medical devices with optimized performance and reduced manufacturing time.
Get multiple quotes for your parts in seconds