Automotive 3D Printing
Automotive 3D printing is transforming vehicle production by enabling engineers to design and manufacture parts that are stronger, lighter and more cost-effective.
What is 3D printing?
3D printing, or additive manufacturing, is a production technique that creates a three-dimensional object from a computer-aided design (CAD) file. The term covers several different processes, all involving one or more materials—typically plastic, metal, wax or composite—being deposited layer by layer to build a shape.
The entire process is computer controlled. This makes 3D printing a cost-effective, efficient and accurate method to create objects of almost any geometry or complexity. Today, 3D printing is used in every industry to produce everything from prototypes, tools and jigs to components and end-use parts.
3D printers come in various sizes, from small enough to fit on a benchtop to large-format industrial machines.
Large printers can produce bigger objects but the machines take up more space and are significantly more expensive compared to benchtop printers. Achieving a successful print is also more complex on large-format machines due to the volume of material and printing time involved.
To learn more, visit our 3DEXPERIENCE GUIDE TO 3D PRINTING
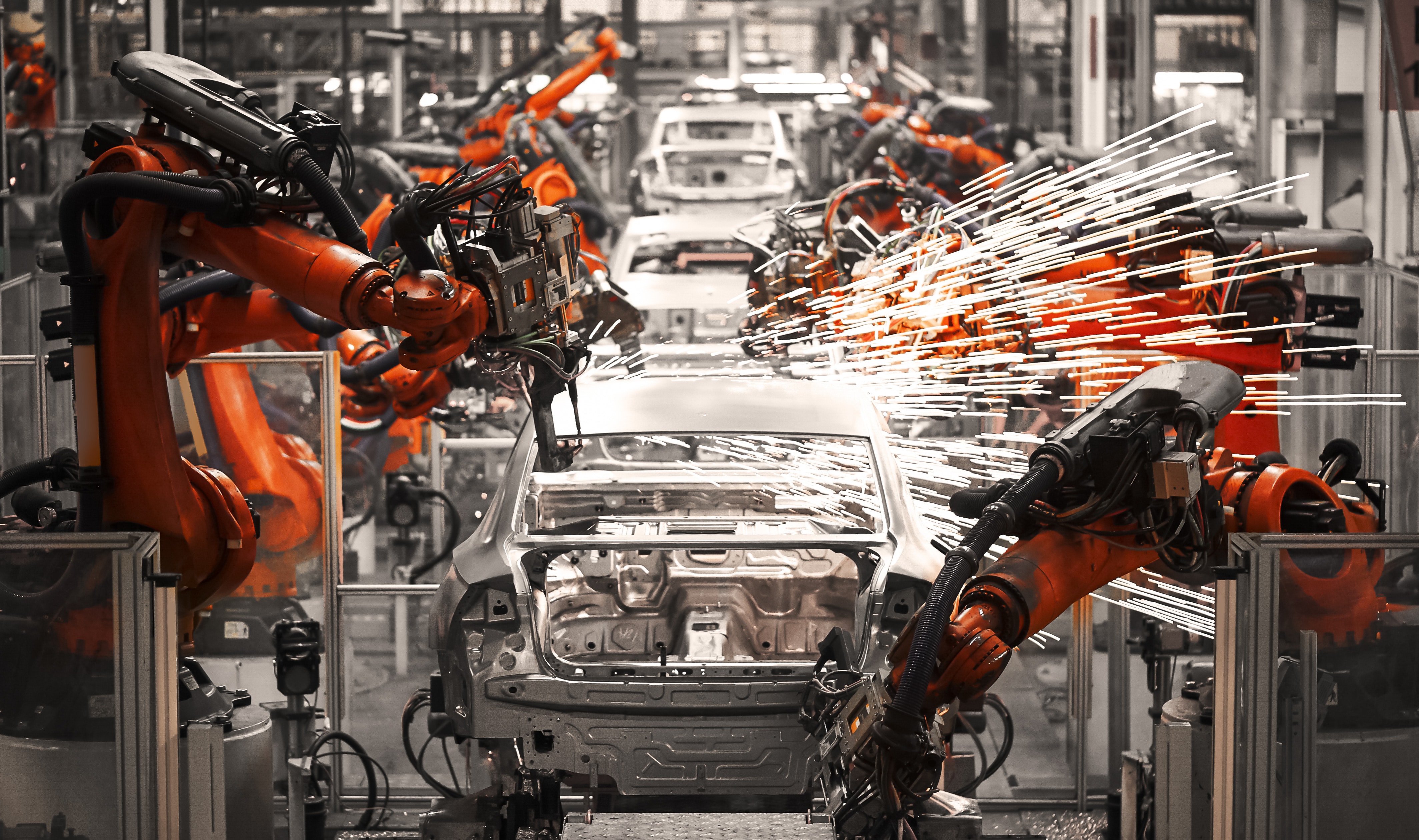
How is 3D printing transforming the automotive industry?
Automotive 3D printing brings many advantages to the industry, including:
- Streamlining the design workflow
- Producing lighter, stronger parts
- Consolidating previously separate parts into a single unit
- Minimizing raw material wastage
- Shortening time to market
- Optimizing inventory and supply chain management
- Simplifying ways for customers to personalize vehicles
Automotive is a major user of 3D printing technology, second only to aerospace. That makes sense given how similar the two industries are in terms of their core objectives. Like aircraft manufacturers, automotive brands are highly focused on improving fuel efficiency and performance while reducing weight.
3D printing is well suited to achieve these goals thanks to its ability to produce lighter parts that are as strong if not stronger than those made using traditional manufacturing methods.
Furthermore, 3D printing brings a new level of design freedom. The technology can produce highly complex part geometries that would be hard if not impossible to make any other way. It also provides a cost-effective and efficient means of making a vehicle unique to each customer through bespoke interior trim pieces, for example.
Little wonder automotive 3D printing is now firmly established in every car maker, from Audi to Volvo. Examples can be found in all operational areas, from research and development (R&D) and assembly to aftersales support and classic car restoration.
Although the mass-produced cars of today contain few 3D-printed parts, the range of applications continues to expand and we’re likely to see much greater use of automotive 3D printing shortly.
Case study 1: ONE MILLION 3D-PRINTED PARTS IN 25 YEARS
Volkswagen has been using 3D printing for 25-plus years, with an initial aim to accelerate vehicle development and reduce costs.
Today, there are 13 units at the Wolfsburg Volkswagen Factory—the Group’s global HQ and one of the largest manufacturing plants in the world—all using 3D printing processes to make both plastic and metal parts.
Typical examples of plastic components are for prototypes such as center consoles, door cladding, instrument panels and bumpers. Printed metal parts include intake manifolds, radiators, brackets and support elements.
To date, Volkswagen has produced more than one million 3D-printed parts.
Its latest 3D printing innovation, a metal binder jetting process, co-created with external partners, is helping to make automotive 3D printing more cost-effective and suitable for production-line use.
Whereas conventional automotive 3D printing uses a laser to build a component layer by layer from metallic powder, the binder jetting process uses an adhesive. The resulting metallic part is then heated and shaped.
The first components made using this new process were parts for the A-pillar of the Volkswagen T-Roc convertible. These weigh almost 50% less than conventional components made from sheet steel. This reduction alone makes the process especially interesting for automotive production applications.
How is 3D printing used in the automotive industry?
The four most common applications of automotive 3D printing are:
-
PROTOTYPING
Whether simple mock-ups or detailed scale models, rapid prototypes are a vital part of product development. These early-stage concept models allow engineers to see how a product truly looks and feels. Crucial elements where visual appeal and driver experience are paramount.
Rapid prototyping also provides the opportunity to see how different components relate to each other and to assess whether a part functions correctly and meets the design specification.
Prototypes used to be hand-made or created using molds that also needed to be designed and manufactured, often by an external company. This was both expensive and time-consuming.
Automotive 3D printing accelerates product development by producing design iterations in a fraction of the time versus traditional manufacturing techniques. This allows more testing to be conducted in the same or shorter period and helps to highlight potential issues earlier.
For example, placing a scale model in a wind tunnel to measure the aerodynamic forces created by a particular vehicle design. Advantages such as these enable automotive manufacturers to stay ahead in a fast-paced, competitive market.
-
TOOLING, JIGS AND FIXTURES
The creation of low-cost rapid tooling and manufacturing aids is one of the most common uses of automotive 3D printing.
A car contains many thousands of separate components and subassemblies. Fitting each of these to the vehicle frame becomes much faster, easier, safer and more consistent thanks to manufacturing aids such as jigs, grips, fixtures and templates.
3D printing these tools quickly onsite or close-by generates substantial time and cost savings compared to conventional production methods.
Additionally, 3D printers are employed to make tools such as thermoforming molds used to form heated sheets of extruded plastic. This is a common technique to manufacture form-fitting packaging for all manner of components.
-
PRODUCTION PARTS
There are two main categories of 3D printed production parts used in automotive:
-
- Vehicle trim such as dashboards, seat frames, control panels, trim pieces, cooling vents and ducting, light fittings, covers and console accessories. These are typically 3D printed using a thermoplastic or polymer material such as ABS, nylon or resin.
Vehicle trim currently represents the majority of 3D-printed parts found in vehicles as they are non-safety related. This makes gaining approval from automotive regulatory bodies relatively straightforward.
However, these parts are often visible to the driver and passengers and frequently interacted with. This requires them to be not only functional but also visually pleasing.
A key advantage automotive 3D printing offers is the ease at which it can produce very low volumes or even one-off items, bringing a wide range of personalization options to the mass market.
In the past, producing bespoke parts such as a gear stick, key fob, seat or set of pedals was highly expensive and time-consuming. This meant customization was largely reserved for luxury car brands.
Thanks to 3D printing, items such as these can be easily, quickly and affordably customized to suit a buyer’s specific demands.
-
- Mechanical components such as mounting brackets, housings, suspension wishbones and brake components. The mechanical and temperature stresses these parts experience mean they are usually 3D printed from a metal such as titanium or an aluminum alloy.
Only a handful of parts have so far been approved as road-safe as the validation process for safety-critical components is far more stringent. That number will increase as automotive 3D printing becomes a more trusted technology by manufacturers and regulatory authorities.
-
MAINTENANCE SPARES AND REPAIRS
Ensuring the availability of spare parts has long been a challenge for the automotive industry. There have been thousands of different cars makes and models over the past 130-plus years, from single-digit concept cars to those mass-produced in their millions. Each one contains tens of thousands of components sourced via notoriously complex, extended supply chains.
Having the right part in the right location with minimal time delay leads to stockpiling large quantities in warehouses at considerable expense. The alternative is to make to order using traditional manufacturing methods, which can be costly and have a long lead time (the period between ordering and delivery)
In the case of rare or classic cars, spare parts may be prohibitively expensive or not available. Original tooling or build specifications may have been lost or suppliers may have closed their doors.
The speed, flexibility and efficiency of automotive 3D printing enable replacement parts to be quickly and cost-effectively manufactured on-demand. Furthermore, digital CAD files can be stored on servers and simply downloaded when needed. This helps to optimize stock levels and eliminates the need to maintain storage facilities.
Additionally, hard-to-obtain or obsolete components can be digitally scanned and reverse-engineered to be 3D printed. This brings substantial time, cost and labor savings and frequently results in lighter parts with superior performance.
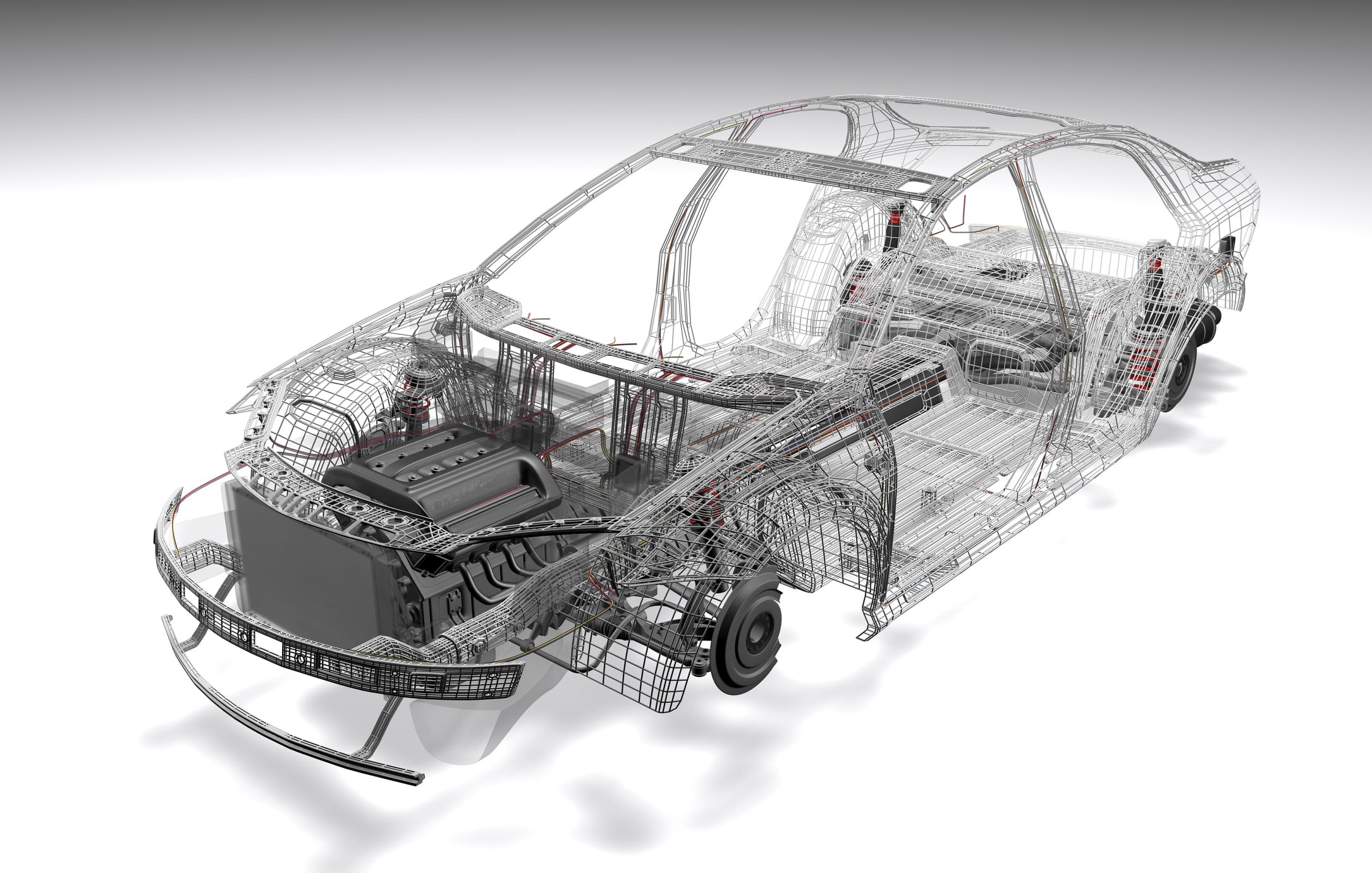
Case Study 2: 3D PRINTING INNOVATION MEETS AUTOMOTIVE HERITAGE
For collectors of rare classic cars, the availability of spare parts can mean the difference between driving a vehicle or being forced to keep it in storage. The rarity of these vehicles means part demand is both limited and infrequent.
In some cases, specific parts are reproduced using the original tools and techniques. However, sometimes new tooling is needed. Investing the required time and money to manufacture new tools can be hard to justify against such small production volumes.
Porsche Classic has overcome this challenge by utilizing 3D printing to produce rare parts that are only required in low volumes.
For example, the clutch release lever on the Porsche 959. This component, made from gray cast iron, is subject to stringent quality requirements but is in very low demand—not least because fewer than 300 of these super sports cars were ever produced.
This makes the part an ideal candidate for metal additive manufacturing. Indeed, Porsche is currently manufacturing several such parts using 3D printing—both steel and alloy and plastic.
All 3D printed parts are rigorously inspected to ensure they meet the quality requirements of the original production period as a minimum, though they usually meet higher standards. Accuracy in terms of size and fit is ensured by performing tests with the part installed.
Porsche Classic is currently testing whether 3D printing is suitable to produce a further 20 components. According to a spokesperson, as the quality of the technology continues to improve with costs generally decreasing, this form of manufacturing presents a very real “economic alternative for the production of small quantities.”
What are the growth opportunities for automotive 3D printing?
Improvements in the size of industrial printers, the speed at which they print and greater design and material flexibility are all helping to make automotive 3D printing a more viable mainstream manufacturing method. This is especially true for low to medium-volume production runs of high-value, geometrically complex components.
As a result, new applications for automotive 3D printing are continuously emerging. Some of the areas expected to see substantial growth over the coming years include:
-
GREEN MOBILITY
Automotive, like every industry, is under pressure to become more sustainable. A clear advantage 3D printing provides is lightweighting—i.e., using lighter parts to reduce the total weight of a vehicle and therefore reducing fuel consumption without comprising performance or safety.
A rough guideline is that a 10% weight reduction generates a 6% improvement in fuel efficiency. For electric vehicles, fuel economy improvements can be even greater. A 10% weight saving in an EV can boost driving range by up to 14%.
3D-printed automotive parts also eliminate the carbon emissions inherent to global supply chains. Instead, digital CAD files can be sent to a 3D printer anywhere in the world with the click of a button.
Furthermore, 3D printers generate dramatically less material wastage during the manufacturing process compared to machining, where as much as 98% of a block of metal can be machined away.
-
ELECTRIC VEHICLES
Closely aligned with the automotive industry becoming more sustainable is the move away from the internal combustion engine to alternative propulsion systems.
Every international car manufacturer has introduced or soon will introduce some form of electric vehicle, from family saloons and futuristic concepts to SUVs and supercars. Industry and consumer interest are accelerating due to many countries and cities stating they will ban the sale of passenger cars powered by fossil fuels.
Lightweight 3D-printed automotive parts can help offset the added weight of batteries and reduce overall vehicle weight. This helps increase the maximum potential driving range and prolong battery life.
Additionally, the buzz surrounding electric vehicles has seen the emergence of many new vehicle manufacturers. These new players won’t be mass-producing cars anytime soon, but they do have the advantage of not being tied to decades-old manufacturing processes and globe-spanning supply chains.
Their search for low to mid-volume production methods that are agile, flexible and scalable has naturally led them to automotive 3D printing technology.
-
3D PRINTED CARS
Fully 3D-printed cars driving on public roads may happen sooner than we think. Several companies are taking the concept extremely seriously.
California-based Divergent, for example, aims to revolutionize automotive manufacturing with its 3D-printed nodes connected by carbon fiber tubing. The result is an industrial-strength chassis that can be assembled in minutes. Its engineering prototype, Blade, has been described as “the world’s first 3D-printed supercar.”
By using lightweight materials to create strong and efficient complex structures, Divergent is looking to cut down on the tooling, cost and time associated with traditional car making, while simultaneously raising sustainability and innovation.
The resulting vehicle may be prohibitively expensive but the technology and thinking behind it could provide a substantial boost to more mainstream car production, as well as prove beneficial to other fields like aerospace and space exploration.
Case Study 3: LUXURY CAR BRAND DOUBLES DOWN ON 3D PRINTING
Bentley Motors recently invested an additional £3 million to double its 3D printing capacity at its headquarters in Crewe, England, where all Bentley models are built.
The high-tech facility has been applied to a range of uses and produced more than 15,000 components in 2021 alone. These include on-the-job assisted tools like lightweight sanding blocks and historically accurate tooling equipment needed to make parts for Bentley’s Blower Continuation model.
Additionally, automotive 3D printing has been employed to create physical components for several prototype Bentleys, including full-scale powertrain models and aerodynamic wind tunnel models.
The advanced techniques have also been used to produce parts for the record-breaking Bentley models that were driven in the demanding Pikes Peak Challenge in America.
The significant expansion to the facility will see the luxury car brand utilize 3D printing technology to create low-volume vehicle components and offer even greater personalization in customer cars.
The state-of-the-art equipment installed enables a 50% cost saving on parts and by operating around the clock, the facility is capable of producing thousands of components in more than 25 different material options.
Employees from across the company are receiving training to understand how they can benefit from using 3D printing in their work, a strong indication of how central the technology is becoming to Bentley’s operation.
A spokesperson called automotive 3D printing a “cornerstone” of Bentley’s “Dream Factory” ambition. They noted that a key benefit of automotive 3D printing is the efficiency improvement it provides by cutting down on the cost and complexity of countless jobs.
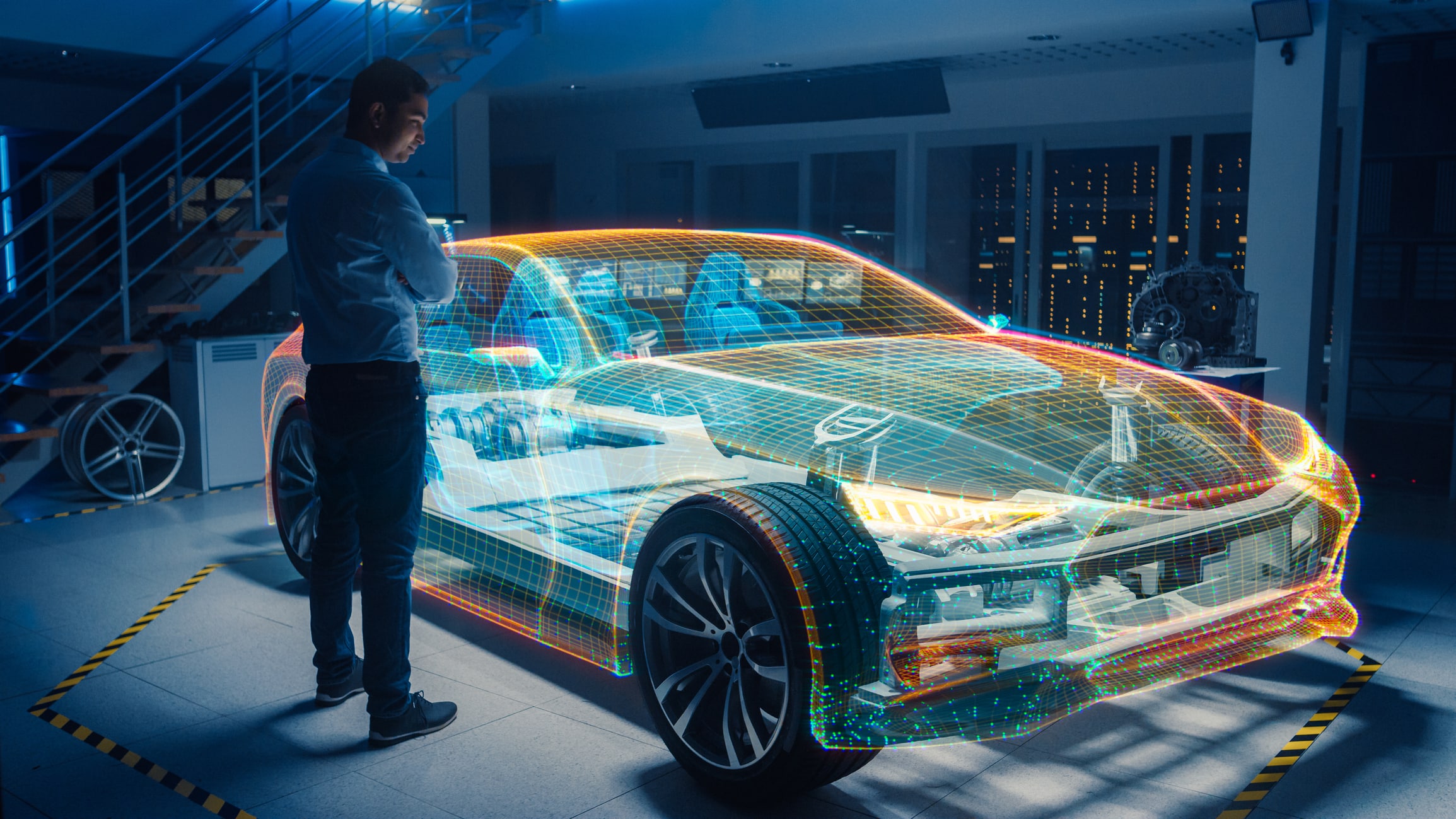
What are the limitations of automotive 3D printing?
-
LACK OF FAMILIARITY
Though growing in prevalence, automotive 3D printing is not yet ubiquitous—certainly outside of prototyping and tool making. That time may come, possibly sooner than expected, but for now, the technology remains secondary to more conventional production methods.
The complexity and rigorous standards integral to manufacturing safety-critical automotive parts mean replacing tried and tested machining techniques with something new carries a level of risk some companies aren’t comfortable with.
-
LARGE VOLUMES
In many cases, automotive 3D printing can produce a single item or small batch of items faster and more efficiently than traditional manufacturing methods. However, each machine can only print a certain number of objects at any one time, depending on machine size and object, so may not be the most suitable or cost-effective method for large production runs.
-
PART SIZE
3D printers have inherent size constraints that make them incapable of producing large components. In some cases, multiple smaller parts can be joined together, though this may not always be an ideal solution.
Manufacturers of 3D printers are working to address the size limitations of existing machines, such as by removing the barriers present in typical print chambers.
-
INCONSISTENT QUALITY
3D printers can’t yet print perfect results every time. Failure rates depend on the machine and material used and the object being printed. Also, removing surface irregularities or textures may require additional manual processing steps to achieve the desired finish.
Factors like failure rates and post-processing will likely reduce as the technology improves and people become more familiar with using automotive 3D printing.
Get multiple quotes for your parts in seconds