3D Printing in the energy Sector
3D printing has the potential to transform every aspect of the energy sector, from helping to make traditional power generation more sustainable to making renewable energy sources and storage more viable.
What is 3D printing?
3D printing, or additive manufacturing, is a production technique that creates a three-dimensional object from a computer-aided design (CAD) file. The term covers several different processes that see one or more materials – typically plastic, metal, wax or composite – being deposited layer by layer to build a shape.
The entire process is computer controlled, making 3D printing a cost-effective, efficient and accurate method to create objects of almost any geometry or complexity. Today, 3D printing is used in every industry to produce everything from prototypes, tools and jigs to components and end-use parts.
3D printers come in various sizes, from small enough to fit on a benchtop to large-format industrial machines.
Large printers produce bigger objects, but the machines take up more space and cost significantly more than benchtop printers. Achieving a successful print is also more complex on a large-format machine due to the volume of material and printing time involved.
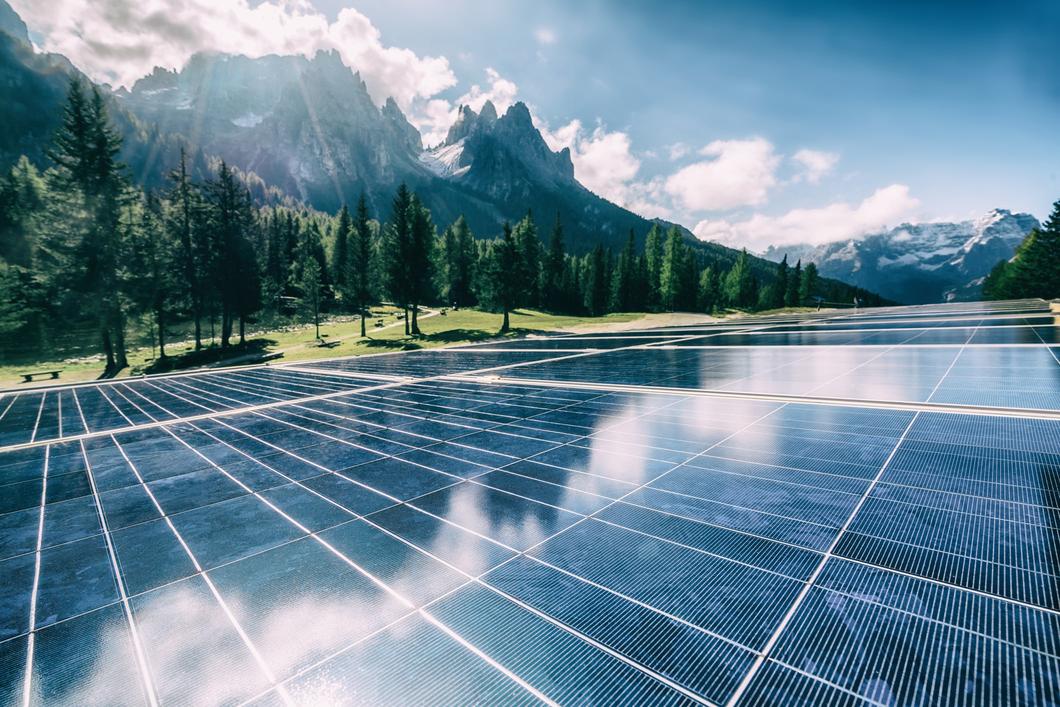
How is 3D printing transforming the energy sector?
3D printing brings many advantages to the energy sector, including:
- Streamlining product development
- Greater design flexibility
- Accelerating time to market
- Producing lighter and better performing parts
- Minimizing raw material wastage
- Consolidating previously separate parts into a single unit
- Optimizing inventory and supply chain management
The energy sector is steadily moving towards more renewable and sustainable sources such as wind, solar, tidal, hydro, geothermal and biomass. While this transition occurs, many countries will continue to consume energy produced by burning fossil fuels like oil, natural gas and coal.
3D printing holds the key to accelerating the adoption of renewable energy and helping to make traditional energy sources cleaner in the meantime. Something the energy sector has switched on to. You can now find 3D printing laboratories within most key players, including BP Global, Chevron, Exxon Mobil, GE Power and Shell Global.
The technology is also being utilized by start-ups and market disruptors, from energy distribution companies and university spin-outs to battery manufacturers.
Yet, the use of 3D printing in the energy sector is relatively low compared to automotive, aerospace and healthcare. Energy companies mostly use 3D printing for rapid prototyping and modeling rather than manufacturing final parts.
This is changing, however, as the energy sector becomes more familiar with 3D printing technology and the many advantages it can provide. The range of potential use cases is also expanding thanks to research into new 3D printing materials and processes.
Additionally, initiatives are underway to develop the necessary industry standards, quality assurance processes and certification for 3D printed parts to be used in demanding environments such as an offshore oil platform or wind farm.
As a result, we’re likely to see much greater use of 3D printing in the energy sector in the near future.
3D printing is improving mission-critical metal parts
Oklahoma-based Duncan Machine Products (DMP) is a full-service precision-machining company that has become a key supplier to the oil & gas industry.
In response to rising customer demand for increased part performance and shorter lead times, DMP has partnered with Velo3D to manufacture 3D-printed industrial parts.
Velo3D’s printers are known for producing high-quality parts with low-angle geometries without support structures. This helps companies like DMP to bid on a larger portfolio of projects as customers don't need to redesign parts.
DMP has already received orders to 3D print a minimum of 1,500 parts for downhole tools used in onshore and offshore exploration; an order which could increase by 10-times in the next 24 months.
The conditions under which downhole tools must perform are hostile and include extreme pressure and high-temperature situations, requiring a robust and dependable manufacturing solution.
For this specific program, DMP is using metal additive manufacturing (AM) to replace investment casting as the manufacturing process.
According to a DMP spokesperson, metal AM is very compatible with the oil & gas industry, given its complex engineering requirements. The technology is also helping to lower costs, improve quality and cut delivery times.
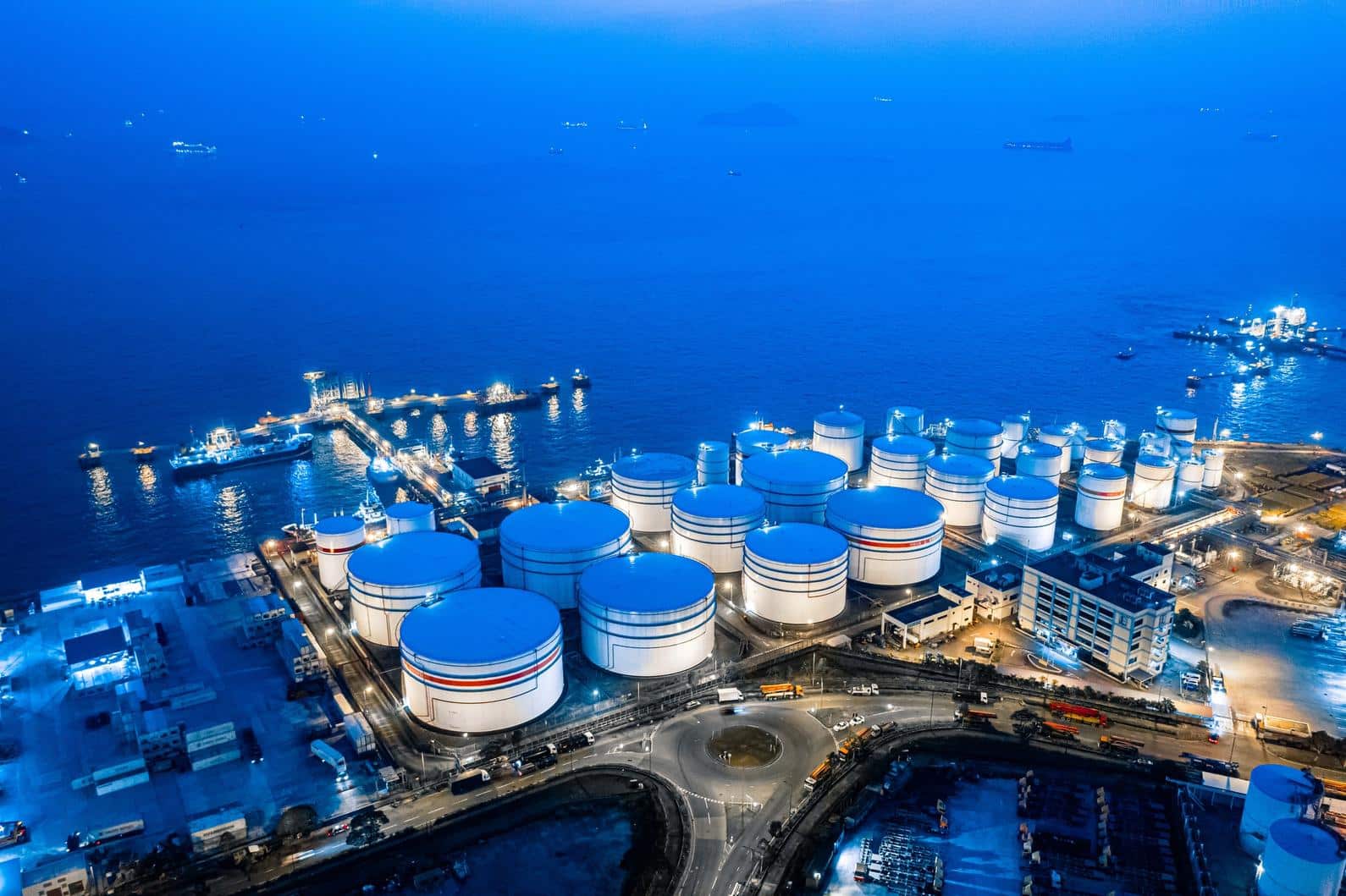
How is 3D printing used in the energy sector?
-
RAPID PROTOTYPING
Prototypes, whether simple mock-ups or detailed scale models, are a vital part of product development. Early-stage concept models allow engineers to validate a design and see how different components interact with each other. This helps highlight potential issues earlier in the manufacturing process and ensures the final project adheres to the design specification.
Prototypes used to be hand-made or created using molds that also needed to be designed and manufactured, often by an external company. This process was expensive and could take weeks or even months.
3D printing compresses the product development cycle by allowing parts to be designed and printed in a fraction of the time and cost of traditional manufacturing methods.
Reducing the time between design refinements allows more tests to be carried out in the same or shorter period. This enables companies to accelerate time to market and stay ahead of the competition.
The speed, accuracy and affordability of 3D printed models are also making the construction of new energy projects faster and more efficient. For example, the Stones deep-water oil and gas project is the world’s deepest, operating in 2,900 meters (9,500 feet) of water in an area of the US Gulf of Mexico.
Subsea infrastructure pumps oil and gas from beneath the seabed to a floating production, storage and offloading vessel (FPSO). 3D printing helped the Stones project team prototype the system that will connect the FPSO to pipelines from the seabed. This allowed them to demonstrate the system to US authorities which had to approve its use for the first time in the region.
-
PRODUCTION PARTS
3D printing is used to produce a growing range of high-value, critical components for the energy sector. Particularly those of high complexity and/or required in low volume, which makes traditional manufacturing techniques unsuitable.
These include gas turbine nozzles, impellors, pistons, pumps, rotors, and parts for control valves, flow meters, heat exchangers and pressure gauges.
Many of these components operate in harsh environments and must withstand extreme mechanical and temperature stresses. This means that 3D printed parts for the energy sector are usually made from a metal or alloy rather than plastic or resin.
Only a handful of end-use components have so far been approved for use in the energy sector. Power generation is a vital part of daily life, and a hardware failure poses a serious potential threat to people, wildlife and the environment.
As a result, energy companies and regulatory bodies are risk-averse when it comes to replacing proven methods with new alternatives, despite the advantages they offer. That may change as 3D printing becomes more trusted and industry-specific standards become published.
-
MAINTENANCE SPARES AND REPAIRS
Downtime is a serious issue in any industry but especially so in the energy sector. Just 1% of downtime, 3.65 days, costs oil & gas companies an estimated $6.6 million a year. Offshore companies average almost a month of unplanned downtime, 27 days, costing them almost $50 million annually. It’s thought that almost half of all unplanned downtime is caused by some form of hardware failure or malfunction.
The high cost of downtime means energy companies have historically been forced to stockpile large quantities of components at considerable expense.
Instead, they need a way to access replacement parts reliably and quickly to assets in remote locations without the expense of stockpiling or having to redesign and qualify a new part from scratch.
This is where the speed, flexibility and efficiency of 3D printing really pay dividends. Reliable parts can be printed on-demand at or close-to remote locations. The process is far quicker and more cost-effective than stockpiling inventory or having to redesign and qualify a new part. There also isn’t the need for minimum production orders.
This helps optimize inventory levels and eliminates the need to maintain storage facilities. Hard to obtain or obsolete components can also be digitally scanned and re-engineered for 3D printing. This provides time, cost and labor savings, and frequently results in lighter parts that perform better.
How 3D printed concrete is helping optimize wind farms
Taller and more powerful turbines could help increase a wind farm’s efficiency and energy output. But there are limits on how powerful land-based wind turbines can become. Larger generators require taller, stronger and more substantial towers. This represents a bottleneck to the future growth of the wind industry.
Traditional wind turbine towers are made using prefabricated steel tubes transported to the location on flatbed trucks and welded together on-site. Going by road limits how large these towers can be, about 14 feet in diameter. Any larger and they become too wide to fit on many roads.
3D printing the tower foundation from concrete on location would enable the base to be made wider and strong enough to support a taller and more powerful turbine.
Additionally, how effective a turbine is dependent on the height of local terrain. Since printed concrete bases can vary in height, 3D printing can optimize turbine heights to the local terrain and maximize the site layout. The method would also lower transportation costs and open new sites for wind generation.
In April 2022, GE Renewable Energy opened a new research facility in Bergen, New York, that will explore how to 3D print the concrete base of towers used in wind turbines.
The pioneering research will use a new type of printer, the largest of its kind, capable of printing more than 10 tons of concrete an hour. It is the first 3D concrete printer with two X-axes – one for doing the printing and one for doing the reinforcement.
GE Renewable Energy will test the printing process indoors in 2022 and aims to print a full-scale tower segment outside next year. First applications in the field are expected within the next five years.
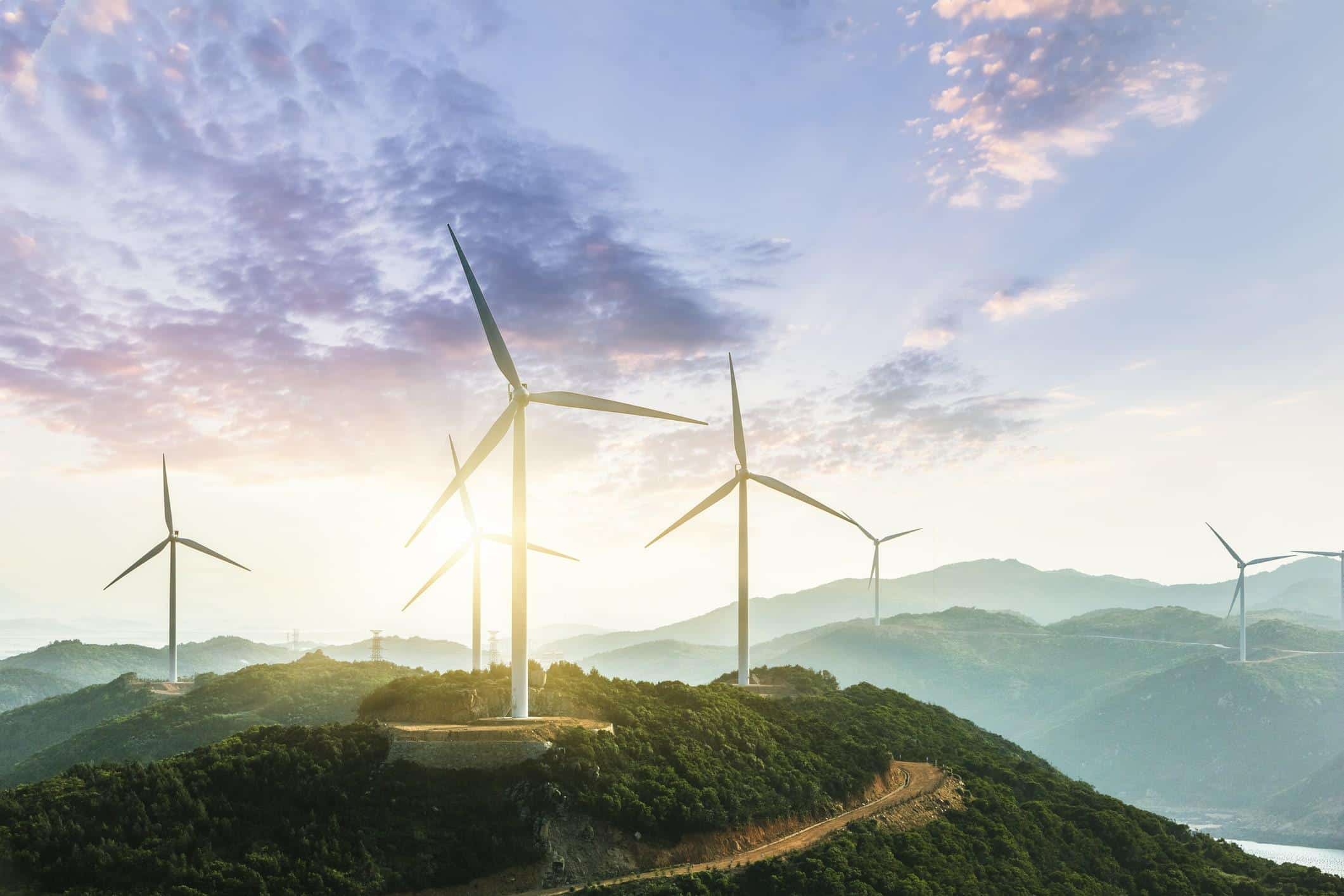
What are the growth opportunities for 3D printing in the energy sector?
-
RENEWABLE ENERGY
Scale will define how quickly and successfully the energy sector transitions from fossil fuels to being 100% sustainably sourced. With energy demand at an all-time high, renewable companies must find ways to manufacture better-performing products, quicker and more cost-effectively.
Little wonder that 3D printing in the renewable energy sector is on a sharp growth curve. 3D printed solar panels, for example, have been proven to be 20% more efficient than traditional ones yet cost about half the price to manufacture.
One of the most time-consuming and labor-intensive stages of manufacturing a wind turbine is making the full-size mock-up of a blade used to make the mold. Research is underway to investigate how 3D printing can improve this process.
Researchers at the US National Renewable Energy Laboratory have taken this one step further and developed a way to 3D print wind turbine blades using thermoplastics. The method creates advanced blades that are lighter, longer, less expensive, and more efficient at capturing wind energy.
-
BATTERIES
Battery storage technologies enable energy from renewable sources to be stored and released when power is needed. Lithium-ion batteries, found in smartphones, laptops and electric vehicles, are currently the most common and economically viable energy storage system.
Solid-state batteries have the potential to offer a lighter, smaller, faster charging, more energy dense and safer solution. 3D printing is helping produce these batteries more efficiently, cost-effectively and at scale.
Start-up Sakuu recently opened a new battery printing and engineering facility in Silicon Valley. The new facility will allow Sakuu to scale its 3D printing battery platform.
According to the company, the solid-state batteries produced there will be up to 50% smaller and 30% lighter than lithium-ion batteries and much less expensive to produce in high volume.
3D printing is making nuclear energy safer
Seattle-based Ultra Safe Nuclear Corporation is developing a Micro Modular Reactor that is smaller, safer and more straightforward to deploy than a traditional nuclear power plant.
The key to its approach is ceramic coated fuel, of which 3D printing performs a vital role. Ultra Safe Nuclear surrounds a standard type of nuclear fuel particle known for its safety with ceramic material. This produces what is known as a micro-encapsulated fuel sphere.
Traditionally, these spheres are placed into a soft graphitic matrix. However, this matrix has barrier and strength limitations. The solution was to replace this matrix with ceramic silicon carbide (SiC) – a technical ceramic often used in aerospace, armor and high-temperature applications.
The conditions within a nuclear reactor are some of the harshest in all of industry, yet SiC doesn’t shrink or excessively swell like the traditional graphitic matrix. It is also very resistant to oxidation and corrosion, enabling it to withstand the demanding conditions of the nuclear reactor core.
The problem with SiC, however, is that it is a difficult material to manufacture or form into complex parts. Despite a long-held desire to work with silicon carbide, there was no viable or affordable method to transform SiC into the shapes and forms needed for nuclear applications.
That has changed thanks to Desktop Metal binder jet 3D printers and their ability to 3D print silicon carbide heat-resistant ceramic particles in unique, complex geometries.
Ultra Safe Nuclear is currently demonstrating MMR energy systems at the Canadian Nuclear Laboratories and the University of Illinois and has started new projects to further deploy its technology in the US, Canada, and Europe.
What are the limitations of 3D printing in the energy sector?
-
LACK OF FAMILIARITY
Though use cases are increasing, 3D printing in the energy sector is not yet mainstream – certainly outside of prototyping and model making. That time may come, possibly sooner than expected, but for now, the technology remains secondary to more conventional production methods.
A rigorous certification and part qualification process is an integral part of manufacturing safety-critical components. Replacing tried and tested production techniques with something new carries a level of risk some energy sector companies aren’t comfortable with.
-
LARGE VOLUMES
In many cases, 3D printing can produce a single item or small batch of items faster and more efficiently than traditional manufacturing methods. However, each machine can only print a set number of objects at any one time, depending on machine size and object, so may not be the most suitable or cost-effective method for large production runs.
-
PART SIZE
3D printers have inherent size constraints that make them incapable of producing large components. In some cases, multiple smaller parts can be joined together, though this may not always be an ideal solution.
Manufacturers of 3D printers are working to address the size limitations of existing machines, such as by removing the barriers present in typical print chambers.
Get multiple quotes for your parts in seconds