3D Printing Aerospace
3D Printing Aerospace is transforming aircraft production by enabling engineers to rapidly design and develop parts that are stronger, lighter, and more cost-effective.
What is 3D printing?
3D printing, or additive manufacturing, is a production technique that creates a three-dimensional object from a computer-aided design (CAD) file. The term covers several different processes, all involving one or more materials – most often plastic, metal, wax or composite – being deposited layer by layer to build a shape.
The entire process is computer controlled, which makes 3D printing a cost-effective, efficient and accurate method to create objects of almost any geometry or complexity. Today, 3D printing is used in every industry to produce everything from prototypes, tools and jigs to components and end-use parts.
3D printers come in various sizes, from small enough to fit on a benchtop to large-format industries machines.
Large printers can produce bigger objects but the machines take up more space and are significantly more expensive compared to benchtop printers. Achieving a successful print is also more complex on large-format machines due to the volume of material and printing time involved.
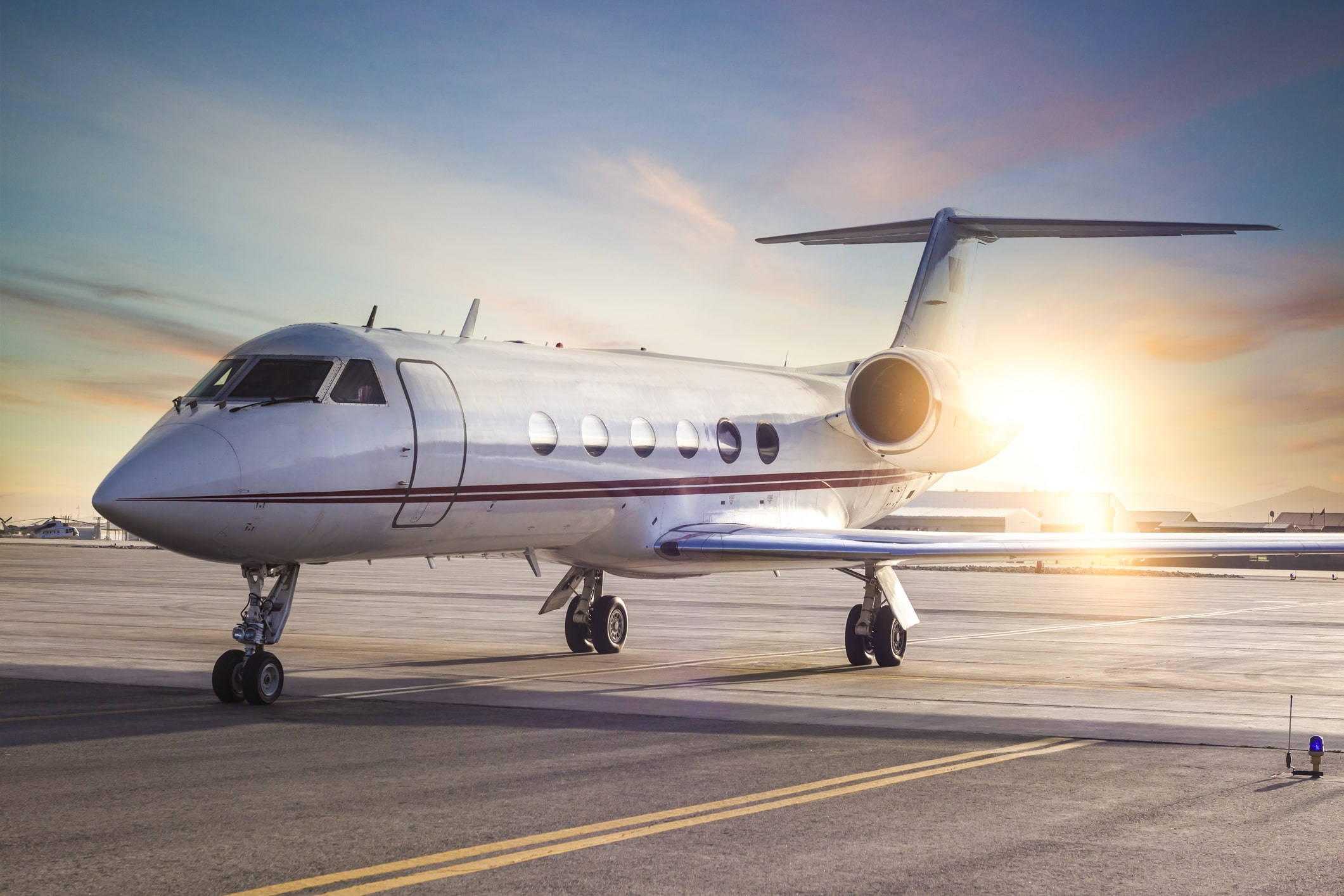
How is 3D printing transforming the aerospace industry?
3D printing technology helps the aerospace industry in seven key ways:
Streamlines and simplifies the design workflow
Produces lighter, stronger parts
Consolidates multiple parts into one single part
Minimizes waste of extremely expensive raw materials
Accelerates time to market
Improves cost and resource efficiency
Optimizes inventory and logistics
The aerospace industry was among the first to embrace 3D printing in the late 1980s and continues to be a leading contributor to its continued development and adoption.
Aircraft manufacturers and suppliers are among the largest users of 3D printing. All the leading commercial aircraft makers (Airbus, Boeing, Bombardier and Embraer) and engine suppliers (GE Aviation, Pratt & Whitney, Rolls-Royce and Safran) have adopted 3D printing in their processes. Several even have business units dedicated to working with and further developing 3D printing hardware, software, materials and use cases.
Despite being 40 years old, it’s only recently that 3D printing has made the leap from niche to more mainstream use. Today, examples of aerospace 3D printing can be found in every stage of production, from research and development (R&D) and manufacturing to final parts and maintenance.
That is true for many industries but particularly those closely aligned to aerospace like defense, space and automotive, where weight is a critical performance factor.
Aerospace 3D printing is ideally suited to the needs of industry because of its:
relatively low production volumes,
complex part geometries
demand for lighter, more efficient parts
need for process and cost efficiencies to meet challenging delivery schedules
3D printing is making air travel more sustainable
The E-Jet E2 family are medium-range aircraft developed by Brazilian manufacturer Embraer. The E2 entered service in April 2018 and succeeds the original E-Jet.
Thermoplastic, one of the most common aerospace 3D printing materials, was used at the beginning of the E2 program to replace the time-consuming and manual processes in which parts and tooling were produced.
Today, those same parts take 50% less lead time to produce and generate 65% less waste. The result is a better, lighter, more sustainable part that costs less and is quicker to manufacture.
Aerospace 3D printing is used to build 37 interior part numbers on the E2s. These include air conditioning grills, harness protection units, suction toilet flanges and air ducts, alongside tooling items and jigs. Embraer also uses 3D printing to test proof-of-concept parts from cup holder assemblies to wing leading edges.
The company currently produces around 1,800 pieces a year by 3D printing for the E2 program, and its engineers are working to develop 3D-printed metal parts. Their studies have identified several metal components where aerospace 3D printing can generate similar and potentially even higher time, weight, cost, and environmental savings as thermoplastic material.
The potential applications for aerospace 3D printing are “enormous" according to a company spokesperson, with Embraer evaluating its effectiveness on a wide range of items including airframe; hydraulic, electrical and air conditioning systems; landing gear; interior; functional prototype and tooling, to name a few.
How is 3D printing being used in aerospace?
The four most common applications of 3D printing in aerospace are:
PROTOTYPING
Prototyping is a crucial step in the product development process. As good as digital design tools are, there is still no substitute for holding and viewing a physical object.
An early-stage model allows engineering team to see how a product looks and feels. It provides the opportunity to see how different components relate to each other and to assess whether a product functions properly and meets the design specifications.
Prototypes used to be made by hand or using molds that needed to be designed and manufactured, often by an external company. That was expensive and could take weeks or even months.
3D printing shortens the product development cycle by allowing aerospace engineers to design and print prototypes in a fraction of the time that it would take using traditional manufacturing methods.
Reducing the period between design refinements allows more testing to be conducted in the same or shorter time and helps to highlight potential issues earlier. It enables aerospace companies to accelerate their time to market and stay ahead of the competition.
TOOLING, JIGS AND FIXTURES
One area of production where aerospace 3D printing is proving especially beneficial is the creation of low-cost rapid tooling, jigs and fixtures. Aircraft contain millions of separate components and subassemblies, many of which are complex and must be fitted precisely to the airframe (the basic mechanical structure of an airplane).
Doing so requires hundreds of specific manufacturing jigs, fixtures, guides and templates for each airplane. 3D printing these onsite or close-by can result in substantial time and cost savings of between 60% and 90% compared to conventional production techniques.
PRODUCTION PARTS
There are two main categories of 3D printed production parts used in aerospace:
- Interior aircraft parts – like air ducts, wall panels, trim pieces, endcaps, seat backs, handles, light fittings and cabin accessories. These are usually made from a thermoplastic or polymer material such as ABS, nylon or resin.Interior parts currently represent the majority of flying 3D printed parts as they are classed as non or low-critical for flight. This makes gaining certification for them from civil aviation authorities relatively straightforward. However, interior parts are often visible to passengers and may need to be interacted with. That requires them to be not only functional but also aesthetically pleasing.
- Mechanical aircraft parts – like fuel nozzles, mounting brackets, wishbones, aerofoils, hatches and housings. The mechanical and temperature stresses these parts experience, especially those associated with engines, mean they are usually made from a metal such as titanium or aluminum.
Only a handful of parts have so far been granted flight-safe status due to the approval process being more stringent for flight-critical components. That number is steadily increasing thanks to continued research into new materials and processes and as regulators and manufacturers become more accustomed to 3D printing technology.
MAINTENANCE SPARES AND REPAIRS
Maintenance, repair and overhaul (MRO) is a vital part of the aerospace industry. The term encompasses all the service and inspection activities undertaken to ensure an aircraft can safely operate.
An aircraft becomes revenue-generating when flying. Minimizing ‘time on the ground’ is therefore paramount for MRO providers. Doing so requires having the right part in the right location with minimal time delay.
Aerospace has one of the most notoriously long supply chains of any industry. Having parts available when needed leads companies to stockpile large quantities of components in warehouses at considerable expense.
The speed, flexibility and efficiency of aerospace 3D printing enable manufacturers to produce replacement parts on-demand. That is drastically quicker and more cost-effective than ordering it through standard supply channels with the added benefit of custom parts fit for purpose. Not only does this help optimize inventory levels, but it also eliminates the need to maintain storage facilities. Also, engineers can take hard to obtain or obsolete components and redesign them to be 3D printed. This can deliver time, cost and labour savings, as well as lighter parts that perform better.
3D Printing is helping expand aircraft lifespans
The availability of spare parts can mean the difference between an aircraft operating or prevented from flying. With the average airplane containing millions of components, ensuring a secure supply of replacement parts over the 30-year operating life of an aircraft can prove challenging.
Satair, an aircraft component and service company based in Denmark and a subsidiary of Airbus, has used metal 3D printing to overcome the issue. In 2020, the company provided one of its airline customers in the US with reportedly the first certified metal 3D printed flying spare part.
The specific part was no longer in production by the original supplier but redesigning the part to be made produced using conventional manufacturing methods like machining was found to be too costly and take too long.
Using a new certification process, Satair was able to recertify the former cast part within five weeks and adapt it to titanium, a qualified airworthy additive manufacturing material.
Four parts (a full set for one aircraft) are printed simultaneously, which takes 26 hours, thereby reducing the cost and printing time per part. After printing, the part undergoes post-processing to become airworthy, making it a one-to-one replacement for the original component while meeting the same safety requirements.
Overall, aerospace 3D printing has delivered higher flexibility, shorter lead times and a more economical means of production. Furthermore, the certification time is forecast to come down from five weeks as the technology becomes more widely adopted.
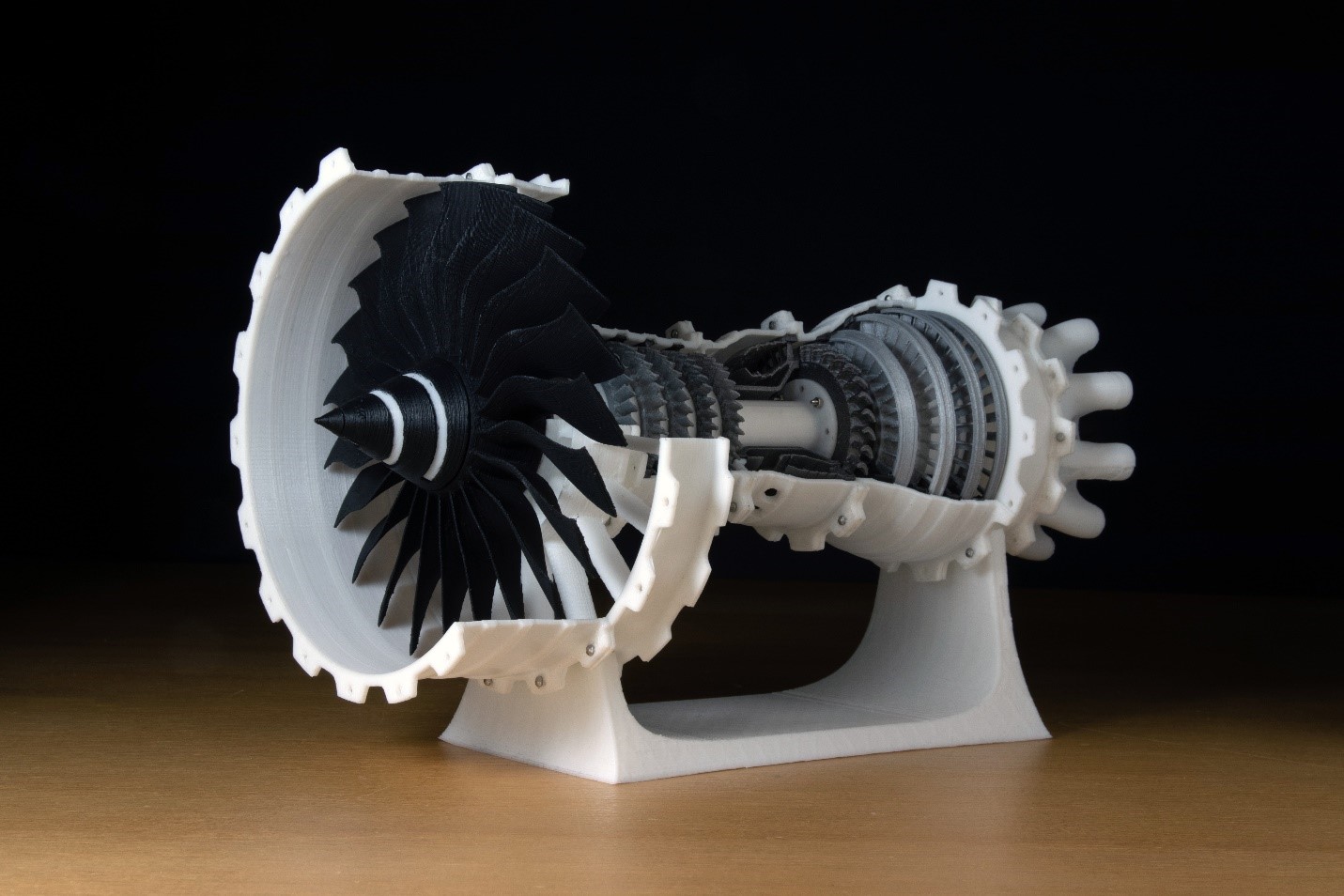
What are the growth opportunities for aerospace 3D printing?
Improvements in the size of industrial printers, the speed at which they print and greater design and material flexibility are helping make 3D printing a more viable manufacturing method – especially for low to medium-volume production runs of high-value, geometrically complex items.
As a result, new applications for aerospace 3D printing are continuously emerging. Some of the areas expected to see sizeable growth over the next five to ten years include:
GREEN AVIATION
Aerospace, like every industry, is under pressure to become more sustainable. A clear advantage 3D printing provides concerns lightweighting – a term that describes using lighter parts to reduce the total weight of a vehicle and therefore reducing fuel consumption. A 20% weight reduction in a commercial aircraft will generate roughly a 10% improvement in fuel efficiency, for example.
In such a way, aerospace 3D printing is helping produce lighter, faster aircraft that can potently fly further on the same amount of fuel. The technology also eliminates the carbon emissions generated by having to ship parts around the world. Instead, companies can instantly send CAD files to be used by printers anywhere in the world.
3D printers also have dramatically less material loss during the manufacturing process compared to machining, for example, where as much as 98% of a block of metal can be machined away.
Something closely aligned with the aerospace industry becoming more sustainable is the introduction of battery-powered aircraft. The development has gained serious attention from both start-ups and established leaders such as Airbus and Rolls-Royce.
Lightweight 3D-printed parts can help offset the added weight of batteries and reduce the overall aircraft weight, which helps increase the maximum potential range.
SMALL AIRCRAFT
All the advantages aerospace 3D printing brings to passenger planes apply equally to smaller aircraft such as satellites, space rockets, unmanned aerial vehicles (UAVs) and drones.
Small aircraft manufacturers are increasingly turning to 3D printing rather than conventional manufacturing methods to meet booming demand.
The use of drones has skyrocketed in recent years, for example. The market is expected to reach more than US$60bn by 2025, up from less than US$5bn in 2018.
Thanks to 3D printing, drones are becoming lighter, faster, more flexible and capable of performing a broader range of applications. It also enables drone designs to be quickly, easily and affordably customized to specific customer expectations and requirements.
3D PRINTED WINGS
Wings are a fundamental part of an aircraft but present several manufacturing challenges. They are one of the most technically complex aircraft structures and their large size makes them difficult to maneuver around a factory and work on.
Trials are underway in several countries to see whether aerospace 3D printing can produce lighter wing components that can be used to build a more aerodynamic wing structure at lower production costs. Such innovations would help further drive fuel efficiency and cost savings.
A team of NASA and MIT engineers has built and tested a “radically” new kind of airplane wing made from hundreds of identical triangles of matchstick-like struts. These tiny subassemblies are bolted together to form an open, lightweight lattice framework which is then covered with a thin polymer layer.
The resulting wing is much lighter and more energy efficient than conventional designs, whether made from metal or composites, the researchers say. The innovation could provide a substantial boost in aircraft production, flight, and maintenance efficiency and could have other applications such as the wing-like blades of wind turbines.
Air Taxis designed for daily life
Population growth, urbanization and underfunded infrastructure are seeing transportation systems in many cities reach breaking point, with residents facing overly congested roads, longer commute times and a lower quality of life. The situation has given new impetus to exciting alternative modes of transport such as air taxis.
Joby Aviation is a California-based pioneer in developing Electric Vertical Take-off and Landing vehicles (eVTOL), or air taxis. Its all-electric aircraft will travel 150 miles on a single charge, allowing a pilot and four passengers to leapfrog the congestion below, emissions-free.
Alongside operating in populated areas, the aircraft could also help increase connectivity for under-served rural communities.
In May 2022, Joby received the first of three approvals – a Part 135 Air Carrier Certificate –the Federal Aviation Administration requires to operate its eVTOL aircraft as an air taxi service across the United States.
The company is currently working on completing the remaining two approvals – a Type Certificate and a Production Certificate – and expects to launch its Uber-like aerial ridesharing service in 2024.
According to a spokesperson, aerospace 3D printing – particularly for metal parts – is “critical” to its manufacturing processes as the company seeks to ramp up production. Key to that is how Job combines custom end-point software with CAD solutions to create a robust workflow with only a single, immutable data file for certification of metal additive manufacturing components.
What are the limitations of aerospace 3D printing?
LACK OF FAMILIARITY
Though growing in prevalence, aerospace 3D printing is not yet ubiquitous – certainly outside of prototyping. That time may come, and possibly sooner than expected but for now the technology remains unfamiliar to many companies.
The complexity and rigorous standards inherent in manufacturing parts for aerospace mean replacing tried and tested conventional machining with something new carries a level of risk some boardrooms are uncomfortable with.
LARGE VOLUMES
In many cases, aerospace 3D printing can produce a single item or small batch of items faster and more efficiently than traditional manufacturing methods. However, each machine can only print a certain number of objects at any one time, depending on machine size and object, so may not be the most suitable or cost-effective method for large production runs.
PART SIZE
3D printers have inherent size constraints that make them incapable of producing large components. In some cases, multiple smaller parts can be joined together, though this may not always be an ideal solution.
Manufacturers of 3D printers are working to address the size limitations of existing machines, such as by printing in an open environment without the barrier present in typical print chambers.
INCONSISTENT QUALITY
3D printers can’t yet print perfect results every time. Failure rates depend on the machine and material used and the object being printed. Also, removing surface irregularities or textures may require extra manual processing steps to achieve the desired finish.
Failure rates and post-processing will likely reduce as 3D printers improve and people become more comfortable with using the technology.
Get multiple quotes for your parts in seconds