Small series manufacturing — A Beginner's Guide
Small series manufacturing is a flexible and reliable method that overcomes the cost and lack of customization associated with mass production.
Introduction to Small Series Manufacturing
Small series manufacturing centers on making many different products in low quantities. It prioritizes variation, agility and the ability to react quickly to opportunities.
It is the opposite of high-volume manufacturing where the focus is on making very large numbers of identical goods.
Manufacturing in small batch sizes isn’t a new concept, but the constraints of manual production techniques have always limited its use. Advances in computer-aided design, automated machining and 3D printing have overcome those limitations by offering superior speed, flexibility and control.
Increasingly affordable technologies like these are helping companies to produce goods in low volumes that can be easily adapted and customized in response to today’s fast-moving world.
Small series manufacturing has traditionally been favored by small businesses and artisans, largely because they couldn’t afford the high investment in machinery and buildings required for mass production.
Large companies are now switching on to the advantages of small series manufacturing. The method aligns with the growing trend of establishing multiple mini-factories close to customers rather than serving the world from a centralized mega-factory.
This guide will help you to understand:
- What is small series manufacturing?
- How does small series manufacturing differ from high-volume manufacturing?
- What tools are commonly used in small series manufacturing?
- What are the benefits of small series manufacturing?
- What are the limitations of small series manufacturing?
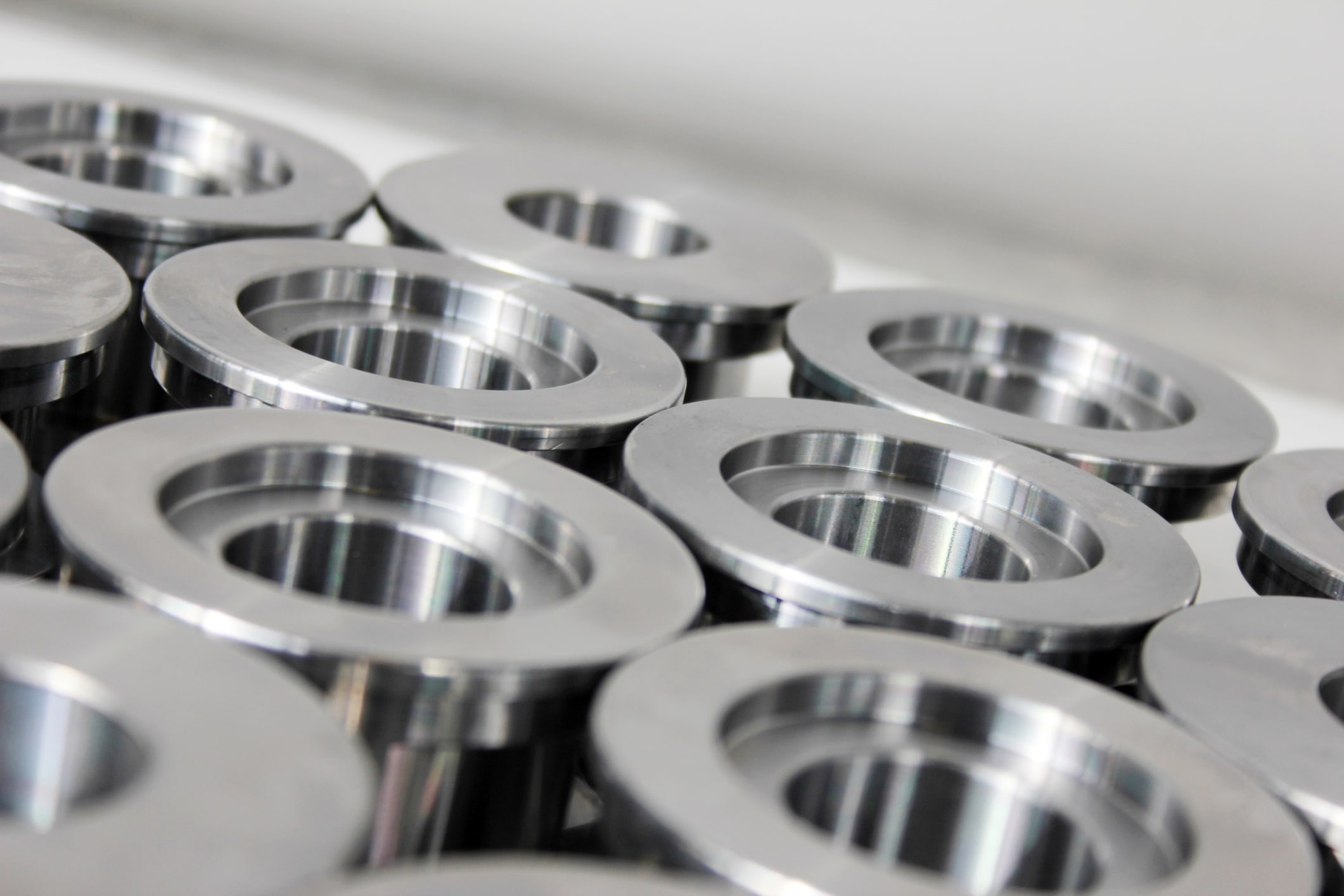
What is small series manufacturing?
Small series manufacturing, also referred to as small series production or rapid production, takes advantage of modern, high-speed technologies to quickly meet customer demand. Shorter lead times and smaller batch sizes reduce the risk of being left with obsolete inventory or production equipment should those demands change.
The most common technologies used in small series manufacturing include additive manufacturing (or industrial 3D printing), computer-aided design (CAD) software, computer numerical control (CNC) machining, injection molding and laser cutting.
The speed, flexibility and control provided by these tools allow manufacturing to take place quickly and cost-effectively. In many cases, the cost of making one product is the same as making 100, regardless of how complex it is. This allows companies to keep their operating costs low and lead times short, while still supplying unique and customized items quickly and efficiently.
Small series manufacturing can also be an important part of the development process. Companies can release an initial limited run of products to the market and use the resulting feedback to improve the next, potentially larger, batch of products. Manufacturers can do this multiple times in quick succession thanks to the efficiencies gained through rapid production techniques.
How does small series manufacturing differ from high-volume manufacturing?
High-volume manufacturing has done much to improve factory output, product consistency, worker safety and the affordability of a wide range of goods. Yet, its biggest strength is also its biggest weakness.
Mass production happens in huge factories filled with machines, workers and raw materials. These buildings require a lot of space, consume vast amounts of energy and are expensive to set up and operate.
To be cost-effective, these factories create very high numbers of standardized goods. When production volumes go up, the cost per unit comes down. This is because companies can spread costs over a much greater number of products—known as “economies of scale.”
Once manufacturers have produced these goods, they typically store them in a warehouse until sold, which may take weeks or months. If demand fades, they may need to sell them at a discount or dispose of them. All of which add extra costs and eat into profit margins.
These limitations, coupled with soaring demand for customized products, have encouraged companies to embrace alternative strategies such as small series manufacturing.
It also doesn’t have to be an either/or choice. Companies can reap the benefits of both high volume and small series manufacturing at the same time.
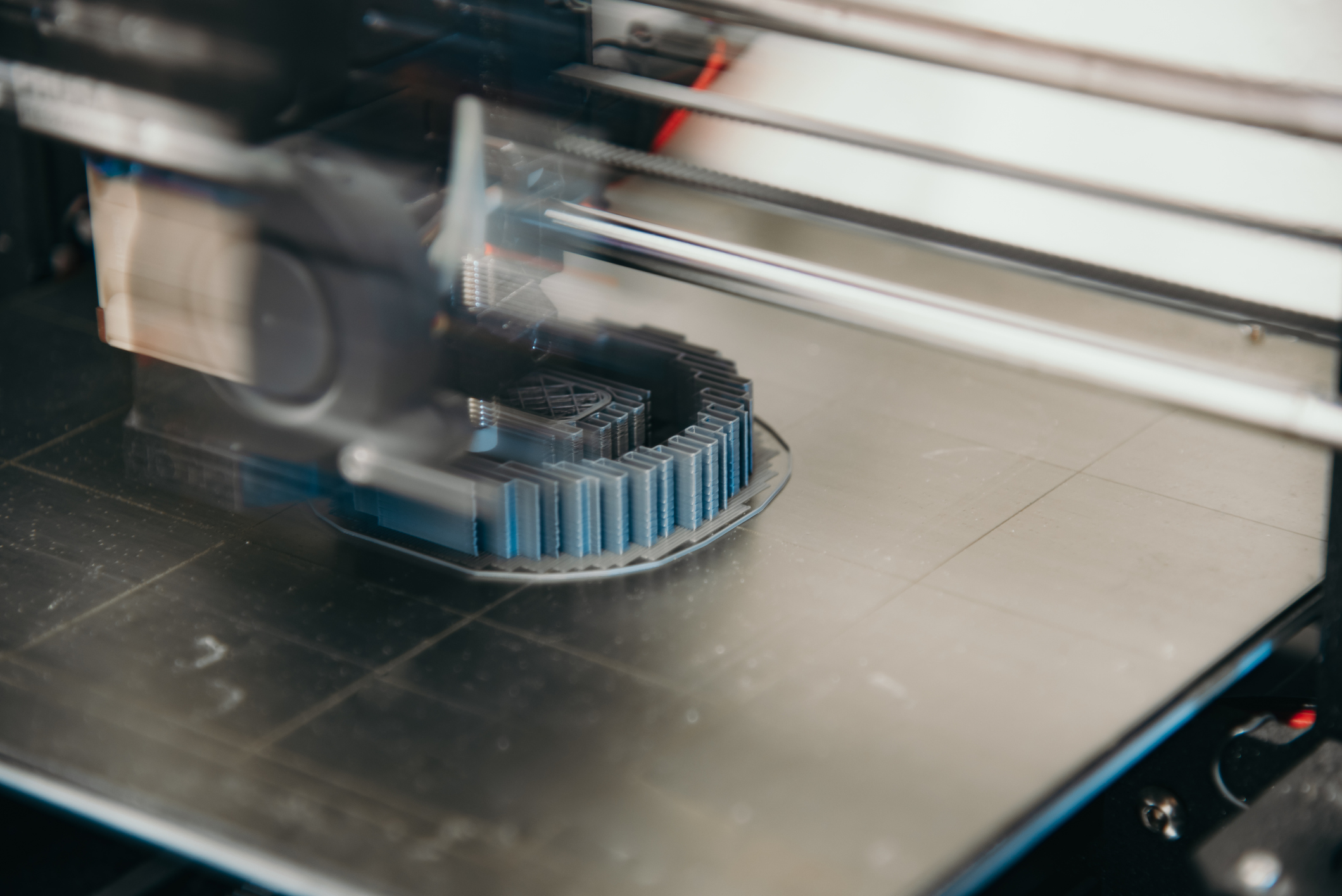
What tools are commonly used for small series manufacturing?
- 3D PRINTERS
3D printing, sometimes referred to as additive manufacturing, encompasses a variety of processes and techniques, all of which involve a material being deposited in multiple thin layers to create a shape.
Plastic and metal are the most widely used materials in 3D printing, but some manufacturers also use certain ceramics, composites, resins and waxes for niche applications.
The entire process is computer-controlled, which makes 3D printing a cost-effective and efficient method to create objects of almost any shape or geometry. Today, the technology is being used to produce models and proof of concepts all the way through to finished objects.
Long printing times and high set-up costs make 3D printers unsuited to mass production, but they are ideal for small series manufacturing.
- CNC MACHINES
CNC machines are highly automated and use computer software to control the precise movement of tools and materials. Common examples include plasma, laser and water cutters, milling and drilling machines, lathes, routers and electrical discharge machines. The most widely used materials are metal, wood, dense plastic and composites.
No other method of manufacturing can produce metal parts as quickly, consistently and reliability as CNC machining. Once the operator has programmed a CNC machine, it can manufacture parts in any quantity and all of them will be identical.
CNC machines can accommodate a wide variety of materials and processes, with multi-function machines and automatic tool changers adding even greater flexibility. Operators can also reprogram machines quickly and easily to produce a completely new product, making them ideal for both low volume and mass production.
The level of automation in metal CNC machining means one skilled operator can oversee multiple machines. Additionally, the increased quality and accuracy delivered through automated machining help to lower a manufacturer’s scrap rate. All of these attributes make CNC machines well suited for small series manufacturing.
- RAPID INJECTION MOLDING MACHINES
In rapid injection molding, molten plastic pellets are forced into a heated mold cavity by a mechanical screw, compressed air or centrifugal force. The mold is then clamped and cooled for the plastic to harden into its final shape.
Manufacturers often use these machines in small series manufacturing, despite the time-consuming process of making individual molds. This is because once set up, the machines can produce lots of products very quickly and consistently.
Time is being saved by making molds out of aluminum rather than from the steel typically used. Aluminum molds lack the longevity of steel molds, but companies can produce them far more quickly. They are also durable enough for several thousand pressings and still produce the necessary finish quality.
What are the benefits of small series manufacturing?
Small series manufacturing overcomes many of the challenges inherent to mass production:
- FOOTPRINT
Small series manufacturing doesn’t require enormous factories and all the costs they entail. Production sites have traditionally been located far away from customers because of their need for space, workers and raw materials.
The technologies and tools used in small series manufacturing are more compact and require a much smaller footprint. This enables production to be brought much closer to where the demand is. It also means factories can be set up quickly, easily and affordably, and even relocated should the need arise.
- TIME TO MARKET
Small series manufacturing uses the flexibility, control and automation of modern technology to streamline the process from initial order to final delivery. For instance, a 3D printer doesn’t require operators to manufacture specific tooling before production can begin. Unlike, say, an injection molding machines.
Furthermore, the majority of manufactured goods are transported by sea. This adds many weeks to delivery schedules and bad weather can add further delays. Transportation overland will also likely be needed for goods to reach their final destination. By locating production closer to customers, small series manufacturing offers a way to cut a two-month delivery time down to 24 hours.
- CUSTOMIZATION
Small series manufacturing allows companies to make changes after each run, or even during a run, depending on the machinery they are using. They can also implement customer feedback into the next batch of products, helping them feel more connected to the processes and the manufacturer to gain valuable insights.
Companies operating in niche yet lucrative, which are often ignored or overlooked by mass manufacturers, often use small series manufacturing techniques.
- COST SAVINGS
Small series manufacturing removes the need to make, store and manage excess inventory. This frees up money for more value-added activities such as marketing, recruiting, training, new tools and product development. With companies focused on reducing costs while improving output, adopting a small series manufacturing model can be a profitable strategy.
- PRODUCT INNOVATION
Being able to quickly and affordably produces a small batch provides the flexibility to test new products without needing to invest in large-scale manufacturing. As a result, the time, costs and risks of new product development go down while the likelihood of it being successful goes up.
Additionally, small series manufacturing allows companies to quickly release products to the market and use the resulting feedback to improve the next batch of products.
- LOW RISK
With large production runs, manufacturers run the risk of stock remaining unsold if demand suddenly falls. Small series manufacturing removes much of this risk because, with this strategy, manufacturers only make goods in low volumes. If demand drops, an entirely new or tweaked product can enter production with minimal delay.
Small series manufacturing also means that engineers can identify production issues and solve them without the risk of manufacturing thousands of defective items at great expense.
What are the limitations of small series manufacturing?
- HIGH SET UP COSTS
Equipment such as CNC and rapid injection machines, especially newer models, are more expensive than manually operated equipment. Although, prices are coming down as demand for machines rises.
On top of the initial purchase cost, these machines require coolant, tooling and periodic maintenance. The cost of repairs can also be high depending on the part that needs replacing and often must be done so by a qualified engineer.
- PRODUCTION VOLUME
The primary defining factor of small series manufacturing is small production runs. Manufacturers can gradually increase the size of these runs in response to customer demand, but if it rises too rapidly, it’s unlikely that they can scale up the production line fast enough to match it. This may result in competitors stepping in to meet the demand.
- COST PER UNIT
Small series manufacturing will almost always carry a higher cost per unit than mass production due to the economies of scale involved.
Get multiple quotes for your parts in seconds