Overmolding and Insert Molding
Overmolding and insert molding are two specific types of injection molding that are important for part designers to understand as they plan their manufacturing projects.
Introduction to Overmolding and Insert Molding
Injection molding is one of the most common methods used throughout the manufacturing industry. The process uses a metal mold that contains a cavity in the form of the intended part. Molten plastic is injected into the mold and subsequently ejected. This method can be utilized to produce thousands of identical parts for a single manufacturing project. Nearly all large-volume plastic parts are made with injection molding because of the ease of production on a large scale. Indeed, injection molding benefits include low cost per part, reduced cycle times, a wide selection of materials, and more.
In this article, we take a closer look at two specific types of injection molding, known as overmolding and insert molding, and the important aspects that part designers need to understand about each process.
What is Overmolding?
Overmolding—commonly called “two-shot molding”—is a specific type of injection molding where a part is made in at least two injection cycles using a different material. Overmolding utilizes a base substrate with a softer TPE or TPU material bonded on top. The base substrate can be either plastic or metal. For plastic base substrates, all molding is done in the same production cycle because the elastomer adheres more to a warm, semi-cured substrate.
Overmolding uses a specialized plastic injection molding tool that contains one cavity for the substrate and a separate cavity for the overmold. The first injection cycle forms the substrate with a thermoforming resin, which fills the gate, runner, and cavity of one portion of the mold, while the overmold portion is blocked. Once the thermoforming resin cools, the mold is rotated and hooked up to a separate nozzle, gate, and runner. Then, the remaining portion of the mold is filled with a TPE or TPU elastomer, which creates an overmold that bonds to the base substrate.
What is Insert Molding?
Insert molding is another specific type of injection molding that places metal components into a mold cavity before the plastic injection. The insert is placed inside the mold manually or via robotic technology. After placement of the insert, the mold closes and plastic is molded over the insert, which produces a single part. Insert molding is commonly used to make metal attachment features for fasteners.
These fasteners allow for secure assembly and disassembly without causing damage to the product. Moreover, heat-set threaded inserts are molded into plastic, which decreases the risk of thread damage upon installation. It’s worth nothing that insert molding can also eliminate the requirement for fasteners because the metal parts are included in the mold, which secures the parts in a one bonded component.
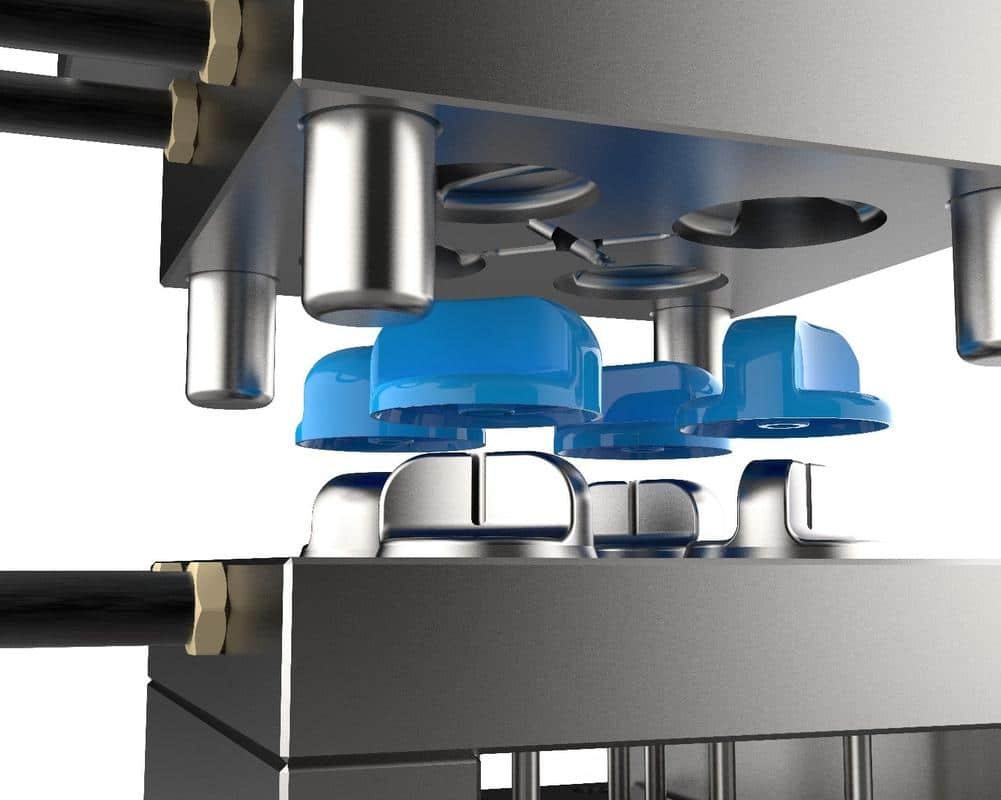
Overmolding and Insert Molding Design Guidelines
When it comes to designing for overmolding and insert molding, there are several key factors to keep in mind.
Overmolding Design Guidelines
Overmolding is typically not utilized for covering the entire base substrate. Instead, overmolding is applied in sections including the following guidelines:
- Verify compatibility of the substrate with the TPU or TPE
- Utilize a TPU or TPE with melt temperatures that are lower than that of the base substrate
- The overmold should be slightly thinner than the substrate supporting it
- The overmold should sit just underneath the surface of the substrate
- Use undercuts and keyways to increase the holding power
Insert Molding Design Guidelines
For insert molding, the benefits of increased strength and versatility must be balanced with the importance of a design for manufacturing approach including:
- Counteracting resin shrinkage with:
- Resin material with low shrinkage rates
- Resin material strengthened with fillers
- Surround the insert with more plastic
- Support the insert with ribs and bosses
- Preheat inserts prior to molding so the resin and the insert can cool and shrink together
- Utilize inserts with knurled surfaces for optimal locking
- Reduce stress by using rounded profiles instead of sharp corners
Overmolding Material Bonding
Bonding between layers of resin prevents separation in parts produced by overmolding. These bonds must be able to withstand forces applied to the part such as:
- Tensile pull that could create separation at a butt joint
- Shearing from a pull parallel to the bonded interface that separates a lap joint
- Peeling starting at an edge and continuing along an interface
The strength of bonds is especially vital when one of the materials is an elastomer, which is flexible enough to be pulled off the substrate. This concern includes both thermoset materials and thermoplastic elastomers. Layers bond in two main ways. One way is chemical bonding between two resin layers. The other way is mechanical bonding, which is dependent on the interface geometry. Optimal bonding involves key elements of part design, mold design, material selection, and the molding process.
As the name implies, chemical bonding occurs at a molecular level and is dictated by multiple factors. For example, better wetting of the substrate by the injected overmolded material enables increased contact between the materials, and, thus, increased bonding. Mechanical bonding is used by itself or in combination with chemical bonding. As the overmolded resin fills holes in the substrate, it cools and binds to the substrate. Additionally, overmolded material can be wrapped around the substrate and the surface area of the interface can be increased with pickets, grooves, and more. Moreover, a porous substrate offers small holes in which an elastomer can fill to produce a mechanical bond.
Insert Molding Capabilities
While overmolding uses two separate shots to create a final part, insert molding utilizes a preformed metal part that is placed into a mold. It is subsequently overmolded with plastic to produce a part with more desirable mechanical and functional properties. Insert molding can be used with threaded inserts, which strengthen the ability of plastic parts to be fastened together. Sleeves and bushings can also be used to enhance part durability for mating components.
Get multiple quotes for your parts in seconds