Injection Molding – What are the Advantages?
Advantages and Disadvantages of Injection Molding operations. Learn more now!
Introduction
Injection molding is an additive manufacturing process for mass-producing small to medium-sized parts. Heated plastic granules are injected under pressure into a metal mold and allowed to cool to form the desired product. Injection molding is commonly used for producing high-volume plastic parts and is arguably the most widely used plastic manufacturing method.
This article discusses the Pros and Cons of Lattice Structures for 3D Printing.
Injection Molding Advantages
Injection molding is a popular manufacturing process used to create parts by injecting material into a mold. The most common materials are thermoplastic or thermoset polymers. The mold is usually made of steel or aluminum. Plastic pellets are poured into a chamber where the material is heated and liquified. The liquified material is injected into the molds and allowed to set and harden into the product shape. The injection molding process can produce complex, intricate shapes with good material tolerances in mass production. For thermoplastic materials, defective parts, runners, sprues, and other waste are typically recycled as "regrind" material. Virgin plastic pellets may be combined with recycled plastic pellets in specific percentages usually determined by quality assurance.
The scrap may be composed of the following:
- Runners
- Gate
- Sprue
- Flash - Overflow material that leaks out of the mold
There are two primary classifications of plastic materials – Thermosets and Thermoplastics:
- Thermoset Materials – These materials are a type of polymer cross-linked with other materials to form a solid, non-malleable material. Once cured, thermoset materials cannot be remolded or reheated without breaking down. Examples of thermoset materials include epoxies, polyurethanes, phenolic resins, and silicones. Thermoset materials are often used in applications that require high strength and stability. Thermoset materials are commonly used in applications that require a strong, durable material that can withstand high temperatures and have good chemical resistance. Examples of thermoset materials include epoxy, phenolic resins, polyester, and vinyl ester.
- Thermoplastic Materials – These polymer materials can be repeatedly melted and formed into products in the injection molding process. Excess materials and defective parts can be reground into tiny particles, remelted, and formed into new products numerous times. The materials are typically lightweight, durable, and have a wide range of applications. This includes consumer products, packaging, automotive parts, and medical items.
The numerous advantages of the injection molding process include the following:
- Mass Production/Low Cost per Part – The ability to mass-produce products consistently is the key benefit of the injection molding process. The manufacturing cost per piece is inexpensive once the capital expenses are paid. The process is quite desirable as product prices tend to drop drastically as more parts are produced.
- Low Scrap Rates – The injection process produces relatively low scrap rates compared to traditional manufacturing processes.
- Product Consistency – The injection molding process is known for its repeatability and consistency, making it ideal for mass production.
- Efficient Process – This process is fast, consistent, and has rapid cycle times. Multi-cavity molds further increase the rapid production cycle.
- Material Selection – A large selection of materials is available for the molding industry. In addition, plastics, rubber, and silicone are available materials.
- Dimensionally Accurate – Parts can be produced to tight tolerances. Dimensional tolerances of +/- 0.005" are not uncommon.
- Little/No Post Processing – Typically, minimal post-production is required.
Injection molding is a widely popular manufacturing process that produces parts for several industries, including the following:
- Transportation (including automotive and aerospace) - Injection molding manufacturers provide a wide variety of parts, including fuel caps, knobs and switches, handles, brake pads, and body panels.
- Food and Beverage – Food and beverage products must meet high Food and Drug Administration (FDA) standards. Injection molding manufactures food and beverage companies to meet these standards by producing products with food-grade materials and plastics.
- Pharmaceutical – Injection molding is used to produce various pharmaceutical products, including syringes, vials, inhalers, stoppers, diagnostic kits, etc. These parts also comply with industry and governmental standards for material composition, sterilization, uniformity, and quality.
- Medical – Injection molding provides a significant amount of medical products, including medical instruments, implants, prosthetics, diagnostic test kits, device packaging, surgical prep products, stethoscope parts, x-ray components, and medical research tools. They follow the same strict standards as pharmaceuticals and food and beverage.
- Consumer Products – There are a plethora of items manufactured for consumer products by plastic injection molding. These include household items, electronic housings, components, toys, automobile parts, recreational items, gardening tools, power tool enclosures, computer and phone accessories, musical instruments, etc.
- Telecommunications – This includes adapters, connectors, cable clips, antenna brackets, and other communication and data cable items.
- Construction – Molded parts in the construction sector include drainage and plumbing fittings, window and door frames, roof tiles, cladding, trim, other architectural features, insulation components, electrical junction boxes, and other components.
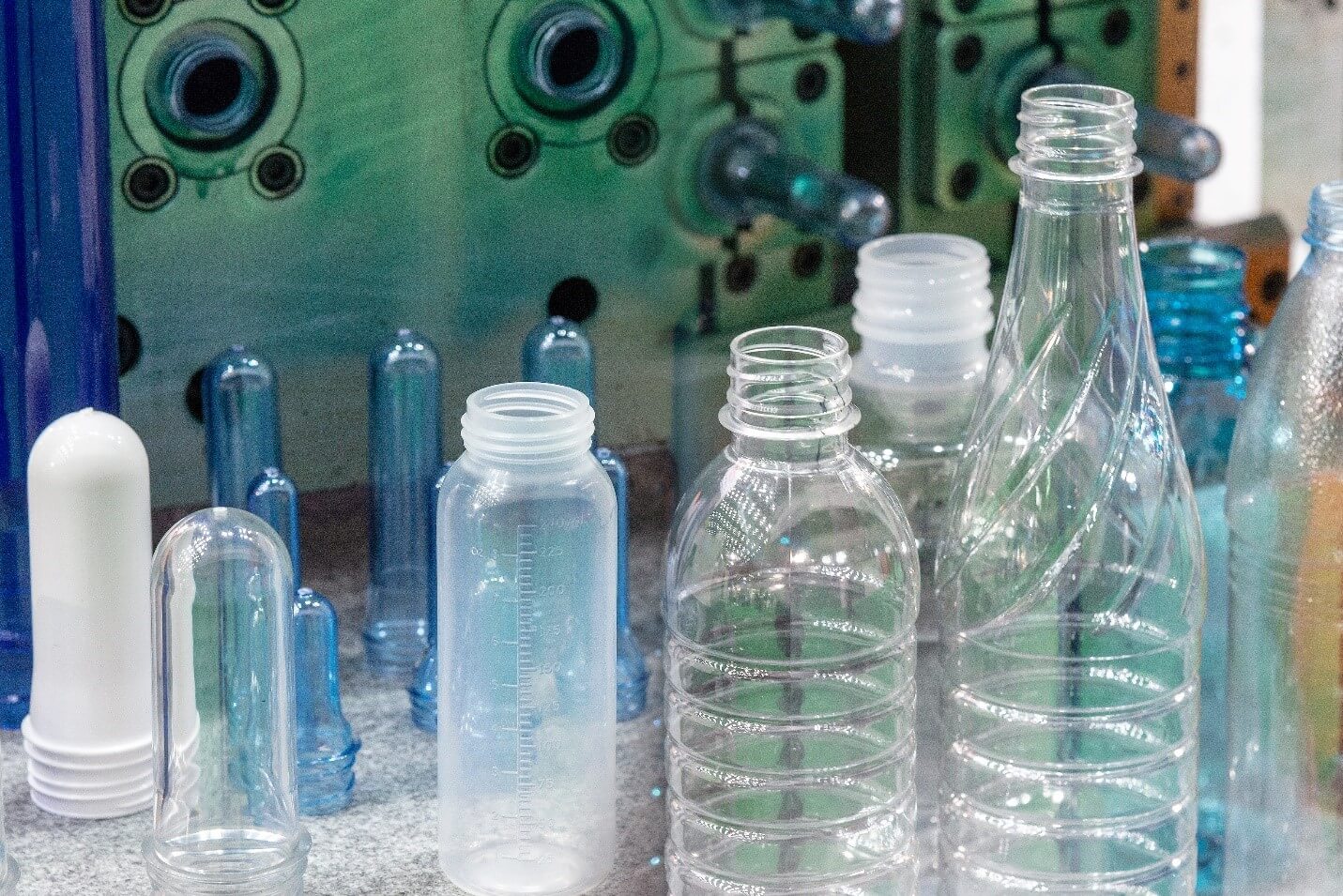
Injection Molding Disadvantages
While there are numerous benefits to the established injection molding industry, as with any mass-produced product, there are some disadvantages. These are listed below:
- High Tooling and Equipment Costs – The costs for Injection molding machines are high. These machines cost hundreds of thousands of dollars. Industrial production molds can run $25,000 - $50,000. Prototype tools are often used in developing expensive tooling.
- Mold Development Process – Tooling lead times can take up to 12 weeks for complex molds that produce accurate parts. Tuning the mold often requires tooling modifications. Gate location, ejectors, etc., are essential aspects of proper product development.
- Product Design – The design process can be complicated, and prototypes are often needed to minimize costs. Large undercuts should be avoided and often add costs to the project. Adequate radii and draft are required in order to eject parts from the mold. Wall thickness must be controlled.
- Material Shrinkage – Shrinkage is caused by a combination of factors including the type of plastic material used, the size and shape of the part being molded, the part's wall thickness, the plastic material's cooling rate, and the molding conditions. These variables must be tuned to optimize the production process.
- Production Defect Risk – If the mold is not designed correctly or the process parameters are not established, defects can occur and pile up quickly if not adequately checked during set-up and production.
- Large Part Restrictions – There are size limitations for injection mold machines and molds.
- Small Runs are Costly – The molding process is geared toward high-volume production to optimize costs. Small runs make it challenging to absorb the costs associated with set-up.
Get multiple quotes for your parts in seconds