How custom manufacturing is beneficial
Learn more about how custom manufacturing ( with 3D printing, CNC machining,..) can be beneficial to your business
Custom Manufacturing: an Introduction
In general, manufacturing consists of two overarching types, off-the-shelf, mass-produced items, or custom manufactured, one-off items. Mass production came about during the industrial revolution when manufacturers, such as Henry Ford, determined that efficiency and less costly products can be established when producing the same components or assemblies repeatedly. Conversely, custom manufacturing is all about allowing the consumers to tailor physical part details, within the capabilities of the manufacturing processes and materials. While custom manufacturing may be more expensive, there are many circumstances where it is useful or the optimal manufacturing method. With today’s technological offerings for part production, custom manufacturing can be simple and straightforward, serving a market that is booming.In general, manufacturing consists of two overarching types, off-the-shelf, mass-produced items, or custom manufactured, one-off items. Mass production came about during the industrial revolution when manufacturers, such as Henry Ford, determined that efficiency and less costly products can be established when producing the same components or assemblies repeatedly. Conversely, custom manufacturing is all about allowing the consumers to tailor physical part details, within the capabilities of the manufacturing processes and materials. While custom manufacturing may be more expensive, there are many circumstances where it is useful or the optimal manufacturing method. With today’s technological offerings for part production, custom manufacturing can be simple and straightforward, serving a market that is booming.
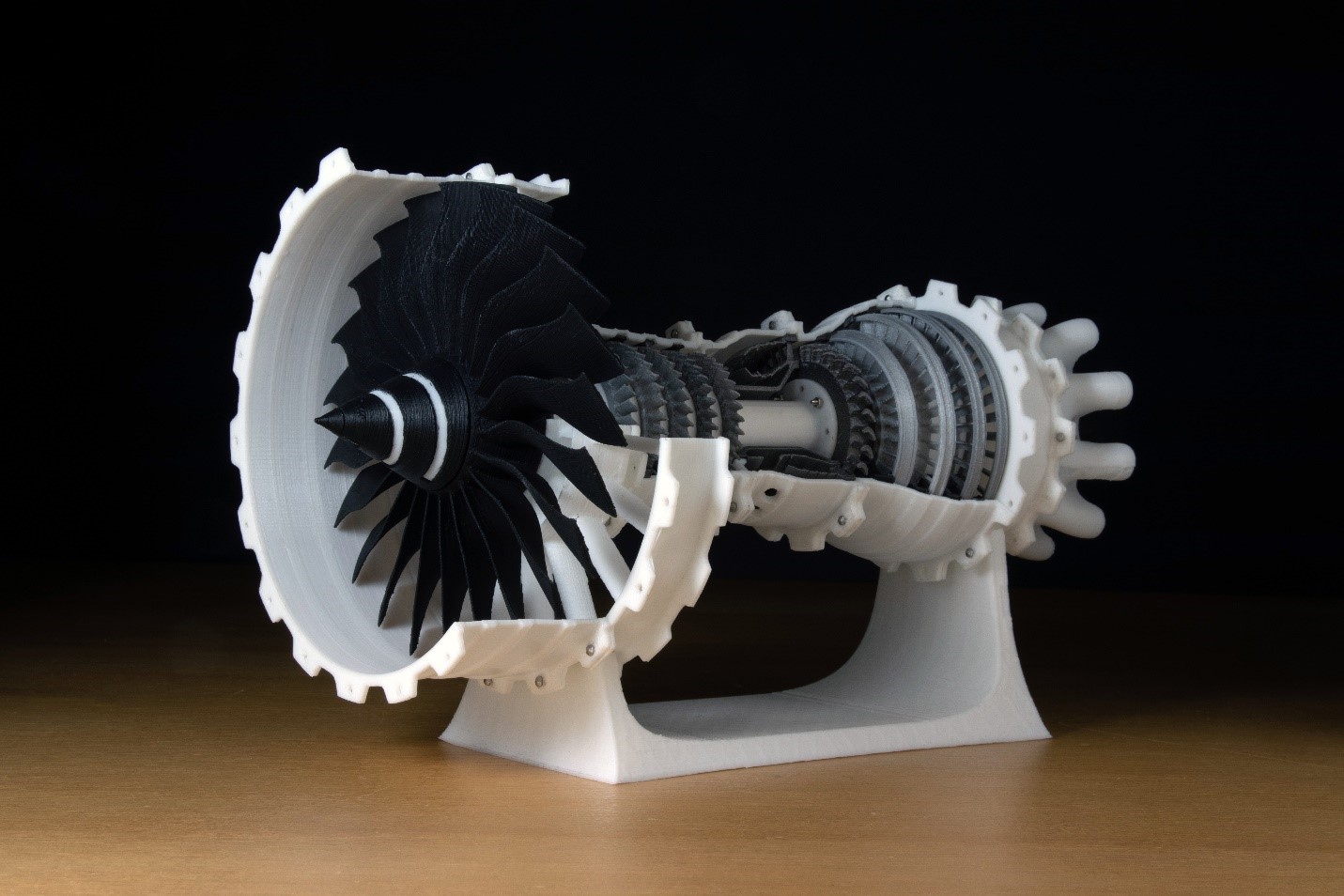
Challenges with Custom Manufacturing
While custom manufacturing offers the highest availability in product flexibility, having the capability to customize the manufacturing of a component or assembly comes with its own challenges. It is important to develop a viable solution for each of the following:
- Processing
- Efficiency
- Quality
The process itself is the first task challenge to tackle. The desired product features, quality, and functionality or use of the final product must all be considered when the custom manufacturing process is designed. Often, rapid prototyping, such as 3D printing is a manufacturing process utilized to bring custom manufactured parts to fruition. CNC machining may also be a practical alternative if the parts to be manufactured do not require extensive fixturing.
After selecting the general manufacturing process, the process must be further optimized according to the base material required, shape, size, strength, and product life. The more complex the product and design, the more difficult the custom manufacturing process will be. In the manufacturing world, complexity and difficulty usually translate to higher costs. To get the process off to the best start, choosing simpler custom manufacturing designs with readily available material that meets the product requirements will result in optimized manufacturing. For example, in custom manufacturing produced by 3D printing, performing design optimizations to reduce the print time can yield a better price and sometimes higher quality.
The efficiency of custom manufacturing is the next challenge to overcome. With “cookie cutter” designs and processes, maintaining quality and process efficiency is relatively standard and stable. When creating a custom manufacturing 3D printing design for a product, therein lies the challenge. It will require a customized efficiency standard to compare the final product. When the custom manufacturing 3D printing process has been simplified and standardized, it will be much easier to improve and streamline the manufacturing process. Custom manufacturing 3D print design process efficiency is achieved when the final product is produced at the lowest cost per unit without sacrificing quality for its intended use. In order to achieve this, it is important not to “over-design” the final product.
Using an expensive 3D printing material when a standard cheaper grade plastic, like PLA or ABS, is efficient and sufficient enough to meet final product requirements would be an example of gross inefficiency.
The last challenge to consider is the quality of the custom manufacturing 3D printing final product. To understand whether a product would be of good or bad quality, the use, lifespan, and production volume requirements must be considered. Custom manufacturing processes may require a more frequent quality inspection for parts, equipment, and final products as the custom manufacturing process is made more complex. For example, ensuring quality may require temperature monitoring to ensure base starting pellet materials are properly stored, dried, and processed at the correct temperature to ensure the product remains free of discoloration, surface cracks, or even mechanical product failures.
Advantages of Custom Manufacturing
Although custom manufacturing seemingly has a multitude of challenges associated with it, there are an enormous number of benefits.
Benefit One: Ability to Prototype
Without custom manufacturing, the prototyping process or new product development would be inexplicably difficult and cost prohibitive. With the made-to-order methodology of custom manufacturing, prototype iterations are simple. Designing a product or assembly is much simpler with the utilization of tools like 3D printing. Simply upload a product design and receive a printed, true-to-size prototype shortly thereafter.
Benefit Two: Cost-Effective
Custom manufacturing allows engineers to work out the issues with production, prior to large investments for a product’s design or testing are finalized. This results in a cost savings in the form of quality control or scrap costs. When the product’s design is finalized prior to release to final production, the processing steps have also been solidified and it is likely that design changes will not be needed.
In addition, custom manufacturing also saves money because it prevents companies from spending large amounts of money on equipment to manufacture small runs of products. Outsourcing to a custom manufacturer, such as Dassault Systèmes is an excellent way to obtain the highest quality, custom manufactured product for the most cost-effective price.
Benefit Three: More Focus on Producing the Best Products
Custom manufacturing typically involves more communication between the job shop and the client requesting the manufactured products. Therefore, the customer tends to receive a little bit more attention and focus on their products. This early communication between client and job shop may result in optimization in Design for Manufacturing. For example, when a product is sent to a 3D printing service provider, the engineering team will likely review the print for manufacturability and make suggestions to improve the quality of the 3D printed parts. This is not something typically performed in mass manufacturing, as the fine-tuning of designs or even manufacturing processes to accomplish specific goals are not modifications that can be made.
Benefit Four: Higher Quality Assurance
With a higher level of focus on manufacturing custom goods comes a higher level of scrutiny on the product produced. This intense focus often results in a more thorough inspection of the product to ensure all specifically tailored specifications are satisfied. Also, custom manufacturing like 3D printing, tends to happen at smaller job shops where they have in-house metrology and testing departments, ensuring the parts are followed by the same team throughout the manufacturing and quality control steps in the process. All of this combined results in higher quality product at an astonishingly affordable price.
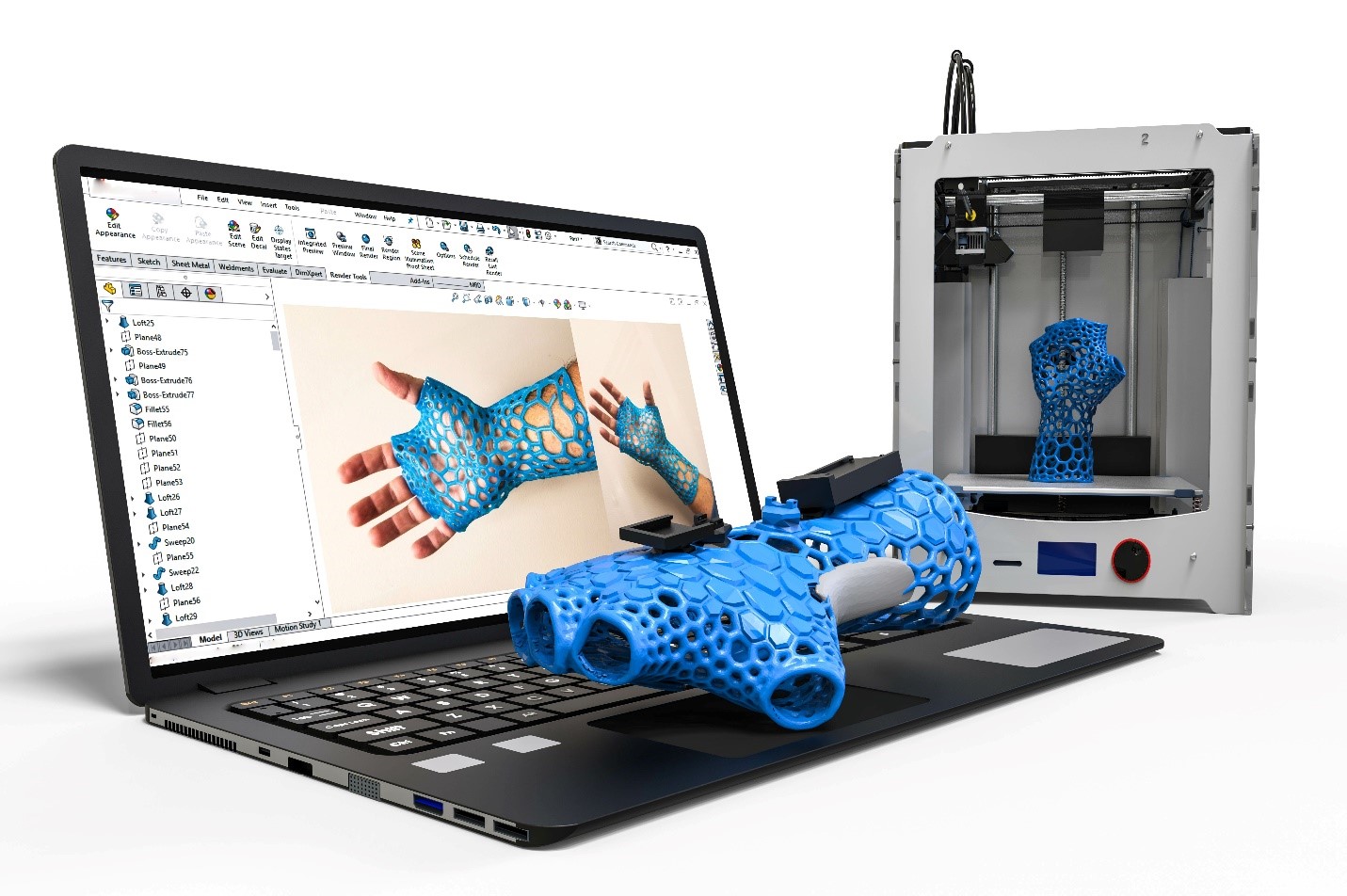
Get multiple quotes for your parts in seconds