Heat Treatments for CNC Machined Parts
There are several different types of heat treatments that can be used with CNC machining. Learn which type is best for your part today!
Introduction to heat Treatments for CNC Machined Parts
Heat treatments are often used in coordination with CNC machining during the manufacturing process to enhance certain properties of metal alloy material such as strength, hardness, or machinability. Heat treatments effect these property changes in alloys by modifying the microstructural and chemical characteristics of the material.
Heat treatments utilize a process where metal alloys are heated to very high temperatures and are subsequently cooled under specific conditions. The specific temperature used during heating, the length of time the material is heated, and the method of cooling all play a role in determining the final properties of the material post-heat treatment.
Understanding Different Heat Treatments and Their Benefits
-
Annealing, Tempering, and Stress Relieving
Annealing, tempering, and stress relieving use high temperatures to heat metal alloys and then these metals are cooled at very slow rates. These three processes utilize different temperatures during the heating phase, as well as a different order in the manufacturing process as follows:
- In annealing, the intended microstructure is realized by heating the alloy to an extremely high temperature and then slowly cooling it. Generally speaking, annealing is done after forming and before any additional processing such as softening or increasing machinability. Most of the time if a certain type of heat treatment is not specified, CNC machined parts will have properties consistent with annealing.
- Tempering heats parts at temperatures that are lower than annealing. Typically, tempering is done after another type of heat treatment called quenching, which we will discuss in the next section. Tempering is done after the quenching of mild steels (A36 and 1045) and alloy steels (4240 and 4140) to enhance their mechanical properties and reduce brittleness.
- Stress relieving heats parts at temperatures that are lower than annealing and this heat treatment is typically done after CNC machining in order to eliminate stress from the manufacturing process. As a result, there is greater consistency in the mechanical properties of the parts.
-
Quenching
In quenching, the metal is heated extremely high and then cooled very quickly by submersion in water or oil or the application of cool air. This fast cooling helps to solidify the microstructural changes that occurred during heating. The end result is a part with a high degree of hardness.
Most of the time parts are quenched after CNC machining because the resulting hardness would make the metal too challenging to machine. For example, tool steels are quenched post-machining because they become very hard and durable as a result of the heat treatment. Moreover, a tempering treatment as described earlier can be subsequently used to offer a degree of control over the level of hardness. This tempering can extend the service life of the part because it reduces the degree brittleness.
-
Precipitation Hardening
Precipitation hardening—also known as “aging”—involves applying high heat to the material, then quenching it, and then heating the material again at a lower temperature for an extended period of time. Precipitation hardening is notable because the discrete alloy elements dissolve and are thus distributed in a uniform fashion throughout the metal matrix.
Precipitation hardening causes a substantial increase in the hardness and strength of the alloy. It’s important to keep in mind that not all alloys can be heat treated using an aging process. Those metals that can are called “superalloys” because they are utilized in high-performance applications.
-
Case Hardening and Carburizing
Case hardening refers to a distinct group of heat treatments intended for parts that require a high degree of surface hardness while maintaining a soft interior. Case hardening stands in contrast to quenching where hardness is increased on both the surface and the interior of the part. The most common type of case hardening process is carburizing.
Carburizing heats mild steels in a carbon-rich environment and then quenches them to solidify the carbon in the metal matrix. The result is an increased surface hardness of steels that is similar to the anodization of CNC aluminum parts.
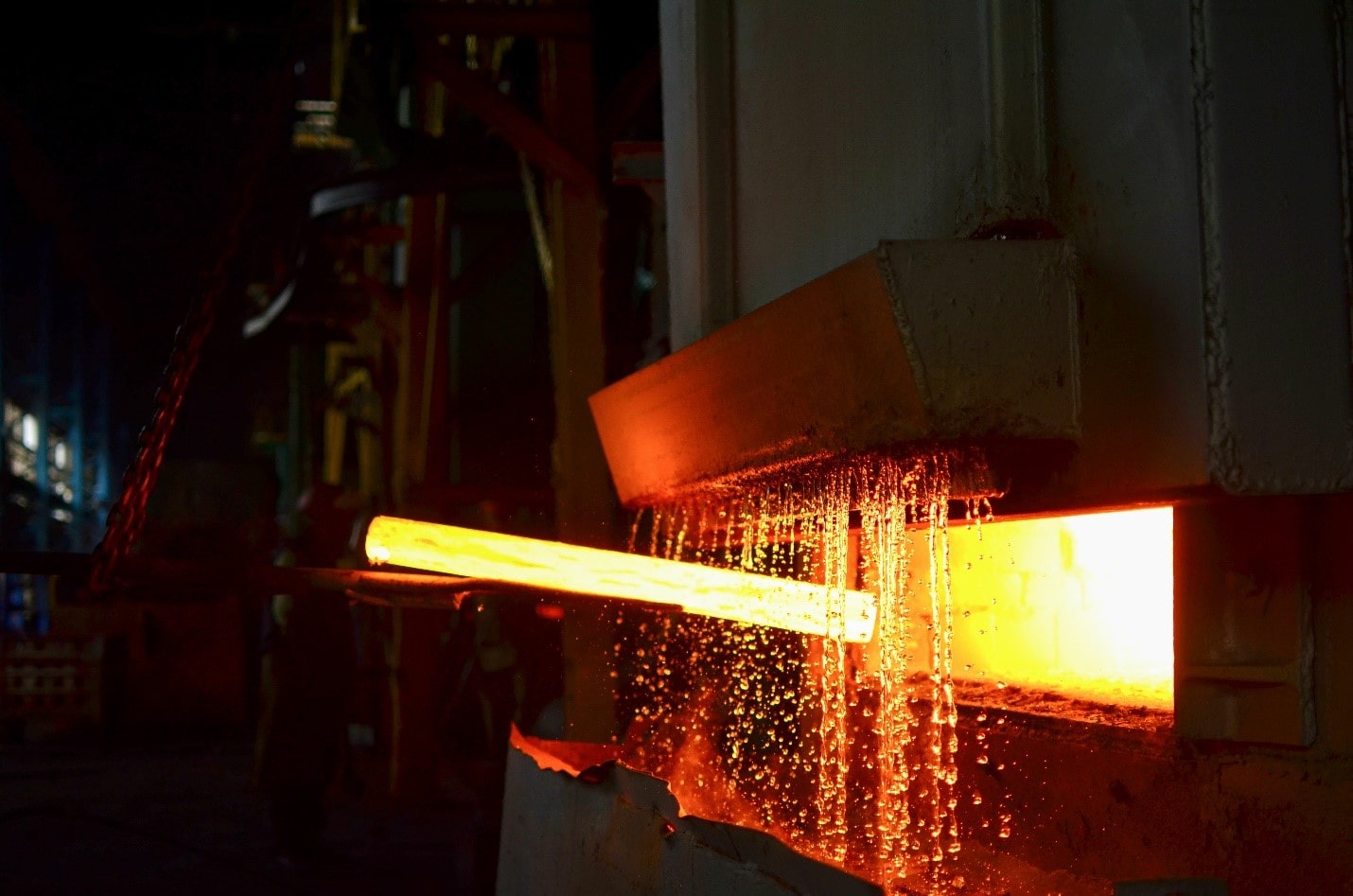
When are Heat Treatments Applied to CNC Materials?
Different heat treatments can be utilized on metal alloy materials at various points during the manufacturing process. When it comes to CNC machined parts, heat treatments can be done either before or after CNC machining as follows:
- If the metal alloy being used is readily available, the CNC machining company will use stock material that has already been heat treated prior to machining. This method is advantageous because it is the fastest and, therefore, reduces project lead times.
- Since some heat treatments dramatically increase the hardness of the material, they are done after machining otherwise machinability is too difficult. A common example is for tool steel parts where heat treatment is done after CNC machining. Additionally, if a heat treatment is being used as a post-processing method, then it will naturally take place after CNC machining.
Get multiple quotes for your parts in seconds