CNC Machining milling aluminum
CNC Machining Aluminum milling is a common manufacturing process that is used to produce a wide variety of aluminum parts.
Introduction to CNC Machining Milling Aluminum
CNC Machining Aluminum milling is a manufacturing term that covers different types of milling processes used to produce aluminum parts. There are many important factors that part designers need to understand when it comes to planning their next aluminum parts project. These factors include the type of cutting tools, aluminum grades, preset parameters, and much more. In this article we take a closer look at the most important aspects of milling aluminum so that you are well prepared for your next project.
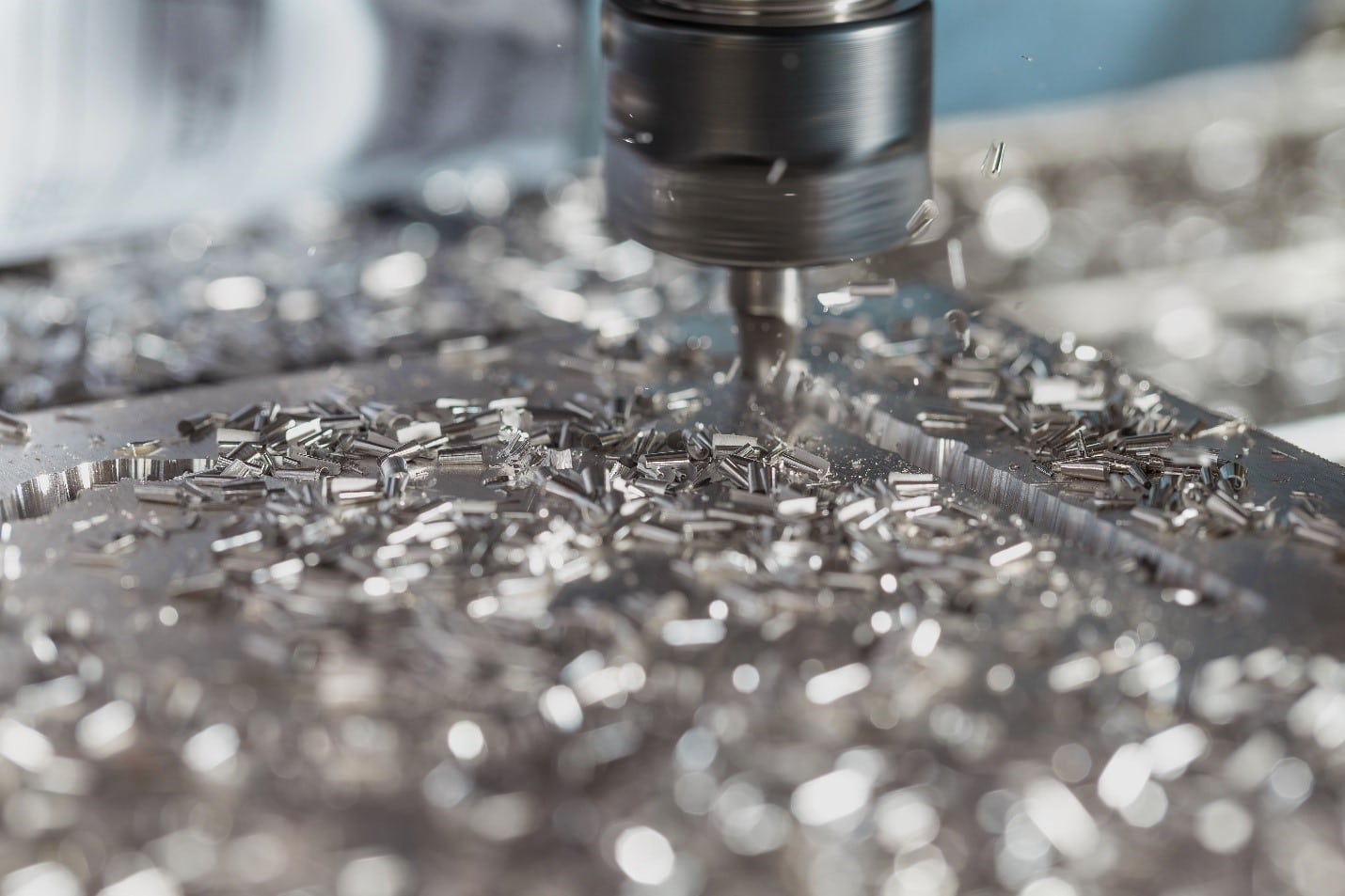
Discover 3DEXPERIENCE SOLIDWORKS for Makers
Common Types of Aluminum Milling
Aluminum milling encompasses multiple processes for machining aluminum material into parts and components. These processes are subtractive, meaning the mill removes raw material to form the intended features on the part. These methods utilize specific types of cutting tools such as end mills, drills, reamers, and more.
Here are the most common aluminum milling processes that are important for part designers to understand:
Face Milling
In face milling, the radial part of the tool is utilized as the cutting edge. Face milling is often used to cut flat surfaces on a part. During the process, the workpiece is fed in the opposite direction of the rotation of the endmill. This creates a downward force that helps hold the workpiece in place during milling.
Profile Milling
Profile milling utilizes the multi-axis milling of 2D and 3D shapes. There are several types of profile milling including slotting, pocket milling, contour milling, trochoidal milling, and more. Profile milling utilizes end mills so that they have a cutting edge on the sides.
Side Milling
Side milling cuts material vertically to produce a flat surface rather than horizontally. With side mills, the cutting edge is located around the circumferential area of the cutter.
Hole Milling
Hole milling produces hole features on the part. Examples of these features include general holes, countersunk holes, threaded holes, counterbored holes, and spot holes. The cutters used to produce these holes include spade drills, end mills, twist drills, reamers, taps, and more.
Form Milling
Form milling is a customized method that involves forming the cutting tool profile based on the design of the part. In this method the contours of the cutting tool are shaped exactly as the intended form of the part.
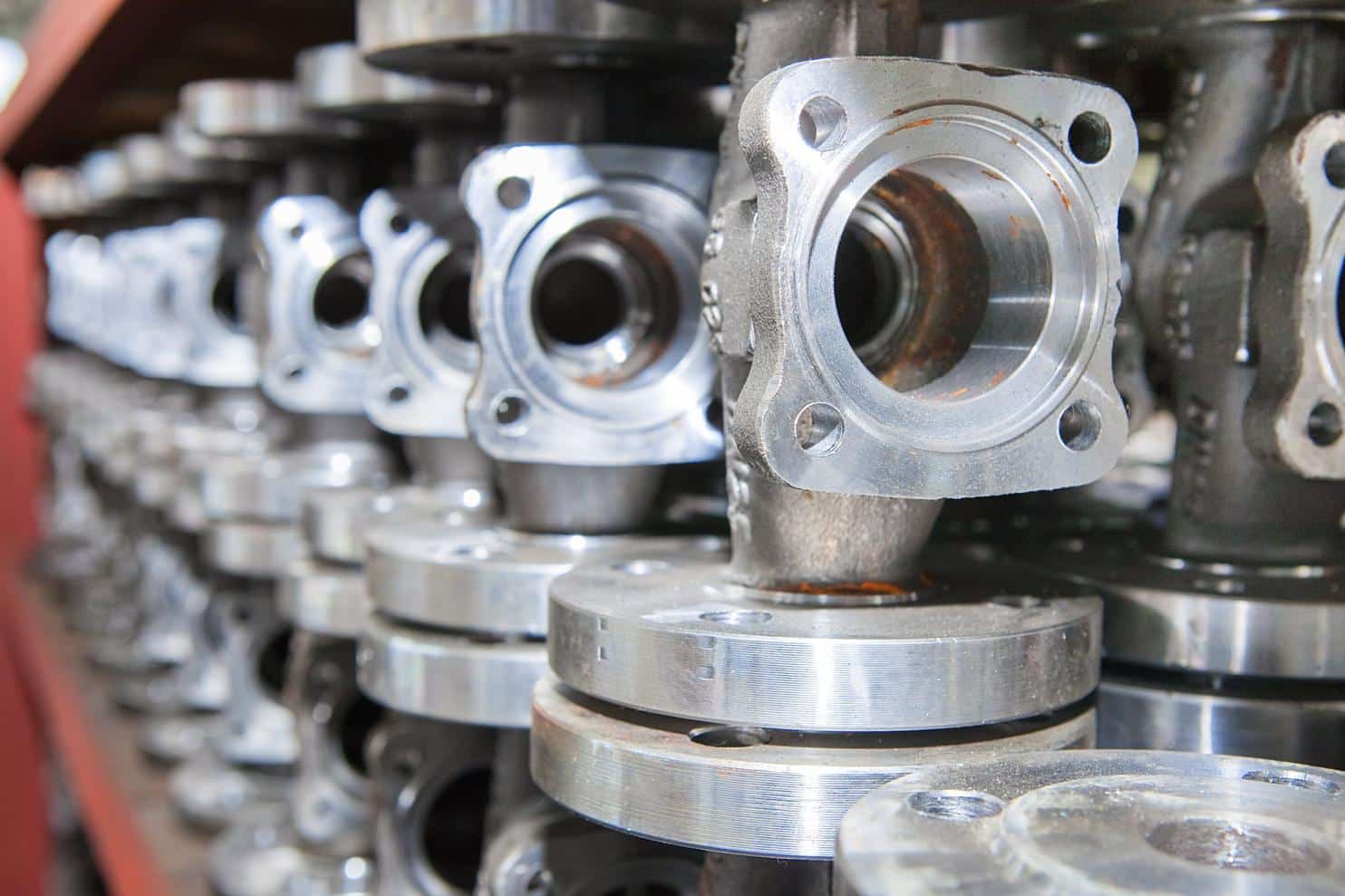
Factors That Impact Aluminum Milling
There are several important factors to understand when it comes to milling aluminum:
Aluminum Grade
The specific grade of the aluminum material has a bearing on the machinability and design of your part. Machinability is determined by the alloying element in each grade of aluminum. These alloys determine properties such as ductility, hardness, and corrosion resistance. Aluminum alloys also have distinct mechanical properties that help determine the material's machinability.
Clamping Rigidity
Clamping is a vital aspect of aluminum milling because it holds the workpiece in place. When done correctly, clamping will prevent shifts in the workpiece during milling, which could compromise the integrity of the part. Rigid clamping of the workpiece enables a smooth milling process because it:
- Decreases vibration of the workpiece
- Fosters dimensional accuracy
- Prevents tool deflection
- Reduces chatter
Machining Parameters
Machining parameters are another key factor in ensuring your part is produced correctly. Different cutting speeds and feeds will have different impacts on aluminum milling. For these reasons, it's paramount that you set the parameters correctly from the beginning of your project to prevent issues such as broken tools, rough surface finishes, and even chatter.
Tooling Geometry
Cutting tools have different geometries such the rake angle, helix angle, land width, number of flutes, flute length, corner radius, and more. Moreover, each type of milling has specific tooling geometry associated with it.
Common Challenges in Aluminum Milling and How to Address Them
There are a few common challenges machinists face when it comes to milling aluminum:
Aluminum Buildup
When aluminum builds up on the edges of the cutting tool it reduces the life of the tool and the ability to machine the parts accurately. You can overcome this challenge by using a faster cutting speed and feed rate. If the cutting speed and feed rate is too slow it can negatively affect the cutting action of the tool and result in increased friction between the tool and the workpiece, which leads to aluminum buildup.
Chatter
Too much vibration creates chatter, which leads to inaccurate dimensions and poor surface finishes on your part. To address chatter, it's vital that you ensure that your workpiece is held securely in place with proper clamping. Moreover, if you are cutting and feeding at speeds that are too fast, it can lead to increased vibrations and chatter. In these cases, it's best to slow down your speeds if you can.
Poor Surface Finish
It's not always easy to achieve smooth surface finishes in aluminum milling. If your cutting tools are dull the surface finish on your part will be rough. Make sure you regrind your cutting tools to keep them sharp and use a high-quality tool material for the cutter if you can. Moreover, if your cutting tool geometry is not appropriate it can lead to recutting of chips and decreased chip evacuation, which will result in a rough surface finish on your part. Additionally, it's important to use the correct cutting depth and speed to achieve the smoothest surface finish possible.
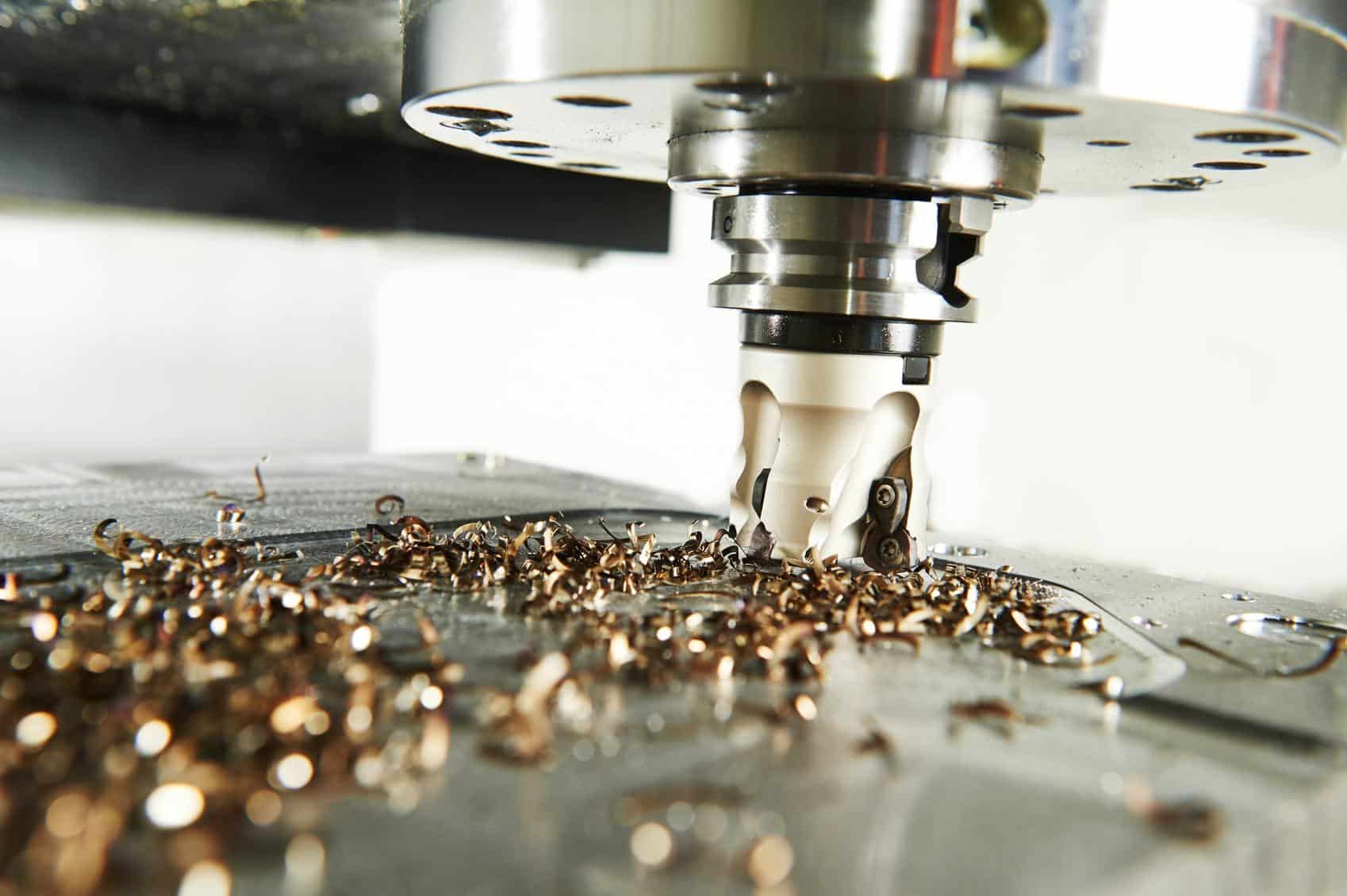
Get multiple quotes for your parts in seconds