Can 3D Printing Replace Injection Molding?
3D printing and injection molding are both commonly used to produce plastic parts, but which manufacturing process is the best?
Introduction
When it comes to plastic parts, injection molding and 3D printing are two of the most commonly used manufacturing processes for production. As you are considering your next parts project, you likely have questions about which of these processes is the best fit for your design. In this article we compare injection molding to 3D printing and we answer the question as to whether 3D printing can actually replace injection molding.
A few questions regarding 3D printing and Injection molding
What is 3D Printing?
3D printing is an additive manufacturing process that builds parts and prototypes layer-by-layer in the printer. 3D printing produces parts by receiving computer design instructions and then printing the part using filament or powder material.
What is Injection Molding?
Injection molding is a manufacturing process where molten build material is poured into a mold that is the inverse of the part design. After the molten material has cooled, it becomes solid in the mold and the mold is removed leaving behind the manufactured part.
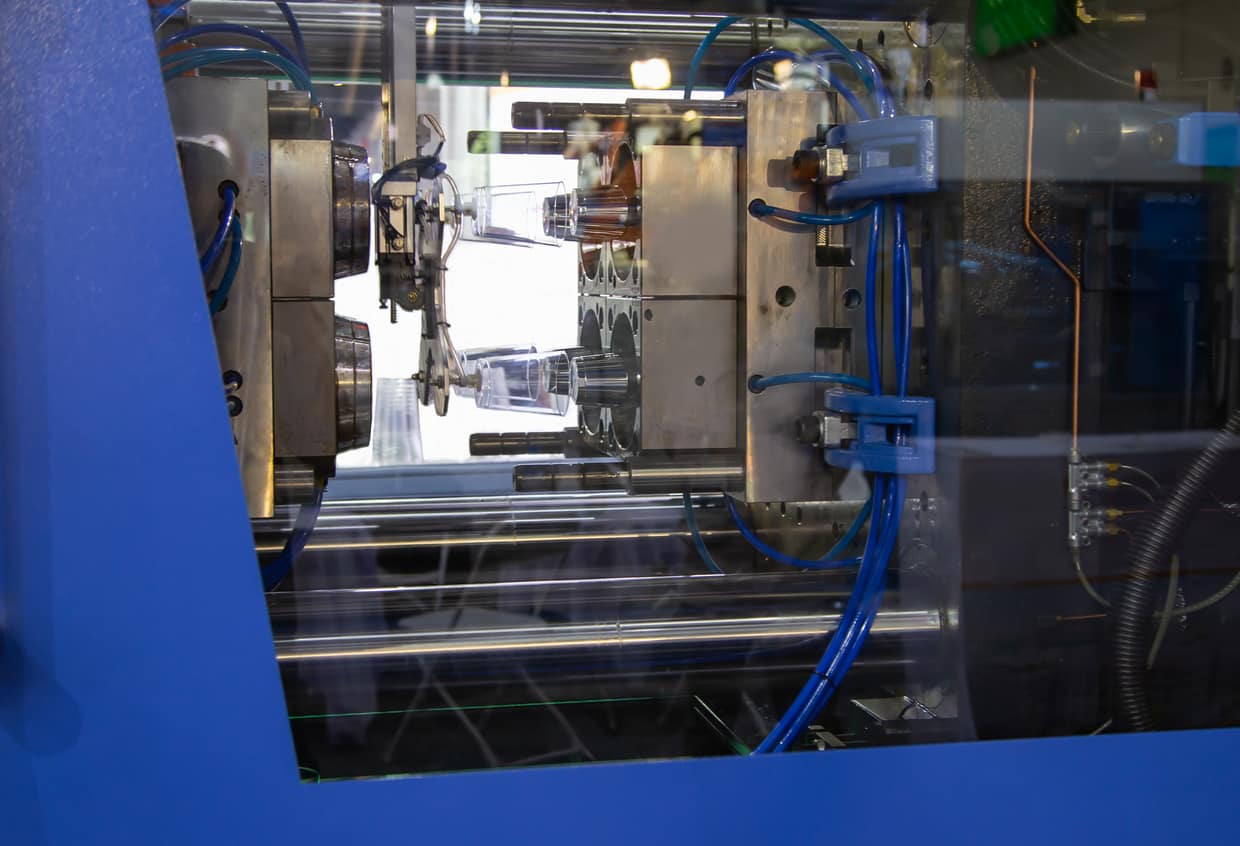
Comparing 3D Printing vs. Injection Molding
Production Volume
Production volume is one of the most important factors to consider when deciding which process is right for your project. Injection molding is very cost-effective for high volume parts production—generally defined as 1,000 parts or more per run. On the other hand, for lower production volumes, 3D printing tends to be the most cost-effective solution. For example, 3D printing processes such as FDM or SLS that utilize affordable plastics like ABS, PC, and Nylon are great options for the production of small quantities of parts—no matter if the parts are identical or not. For medium size production runs, MJF 3D printing is an option for consideration because of its cost-effectiveness and relatively scalable operations.
Complex Geometries and Features
Injection molding by its very nature requires a mold to be made according to the part’s design. Engineers and product designers alike know firsthand that creating CAD models for injection molding is not an easy task and there are many factors to deal with. For example, right angles in the part make it very hard to remove the part from the mold and also intricate features with fine details have to be removed from molds extremely carefully. All of these factors add up to the reality that injection molding struggles when it comes to producing parts with design and geometric complexity. In contrast, 3D printing does an amazing job at producing complex parts. No matter how intricate the features are, 3D printing is able to produce these parts with great ease. Therefore, if your part is complex and its design can’t be adjusted for compatibility with injection molding, it’s best to produce your part via 3D printing.
Lead Time
Generally speaking, injection molding has longer lead times because of the design refinements needed in order to build the correct mold. For this reason, injection molding can take as long as 2-3 weeks. 3D printing on the other hand is much faster. In fact, once designs are submitted, your 3D printed part could be delivered in just a few days.
Modifying the Design During Production
After a mold has been set for injection, it takes significant amounts of time and money to go back and modify the mold. For this reason, changing and customizing certain features of your part can prove difficult with injection molding. For prototypes and parts that need to be adjusted along the way, 3D printing is a much better solution because all you have to do is adjust the CAD file, which is then uploaded into the 3D printer.
Part Strength
One of the biggest advantages of injection molding is that the parts are manufactured through a single poured layer. This cohesive structure adds strength to the parts because there are fewer points of weakness. With 3D printing, parts are printed layer by layer, which reduces the overall strength. In fact, 3D printing can cause there to be structural faults that usually don’t happen with plastic injection molding. For these reasons, if strength is one of the top priorities for your part, it’s best to use injection molding to produce your part if possible.
Surface Finish
Another advantage that injection molding has over 3D printing is the surface finish. The reason is that 3D printing produces noticeable layers in your part, which causes there to be a somewhat rough surface. This roughness can be problematic for certain applications that rub together such as machine parts. For these applications, you will have to do some post-processing of your 3D print to achieve a smooth surface. By contrast, with injection molding there is not multiple layers and, therefore, the surface of injection molded parts is very smooth. For these reasons if your part needs to have a smooth surface finish, it’s easiest to use injection molding instead of 3D printing.
Wasted Material
3D printing requires the use of support structures to produce some parts. As a result, there can be quite a bit of wasted material in high volume production because these support structures are removed. This wasted material results in increased costs to your project. In contrast, there is very little wasted material in injection molding because you only pour the material that you need to fill the mold. For these reasons, for high volume production injection molding is superior to 3D printing because less material is wasted.
Is 3D Printing Going to Replace Injection Molding?
The question is sometimes asked, could 3D printing replace injection molding? The short answer is no. The truth is each of these manufacturing processes has distinct advantages over the other. What this means is that deciding between injection molding and 3D printing should be done on a case-by-case basis depending on the specific priorities of each part.
Get multiple quotes for your parts in seconds