Additive vs. Subtractive Manufacturing
Additive vs. Subtractive manufacturing compares product manufacturing methods. Learn more now!
Introduction: Additive vs. Subtractive Manufacturing
Additive manufacturing is a process that builds parts from the base up by adding successive layers to manufacture a product. 3D printing is the technology most associated with additive manufacturing. Subtractive manufacturing removes material to manufacture a part. This process traditionally uses Computer Numerical Control (CNC) machining.
Both technologies can utilize computer-aided design (CAD) software models to produce products. These manufacturing technologies have tremendously impacted prototypes and production and continue to make advancements.
This article discusses Additive vs. Subtractive Manufacturing, their difference, expenses, applications, and the hybrid process.
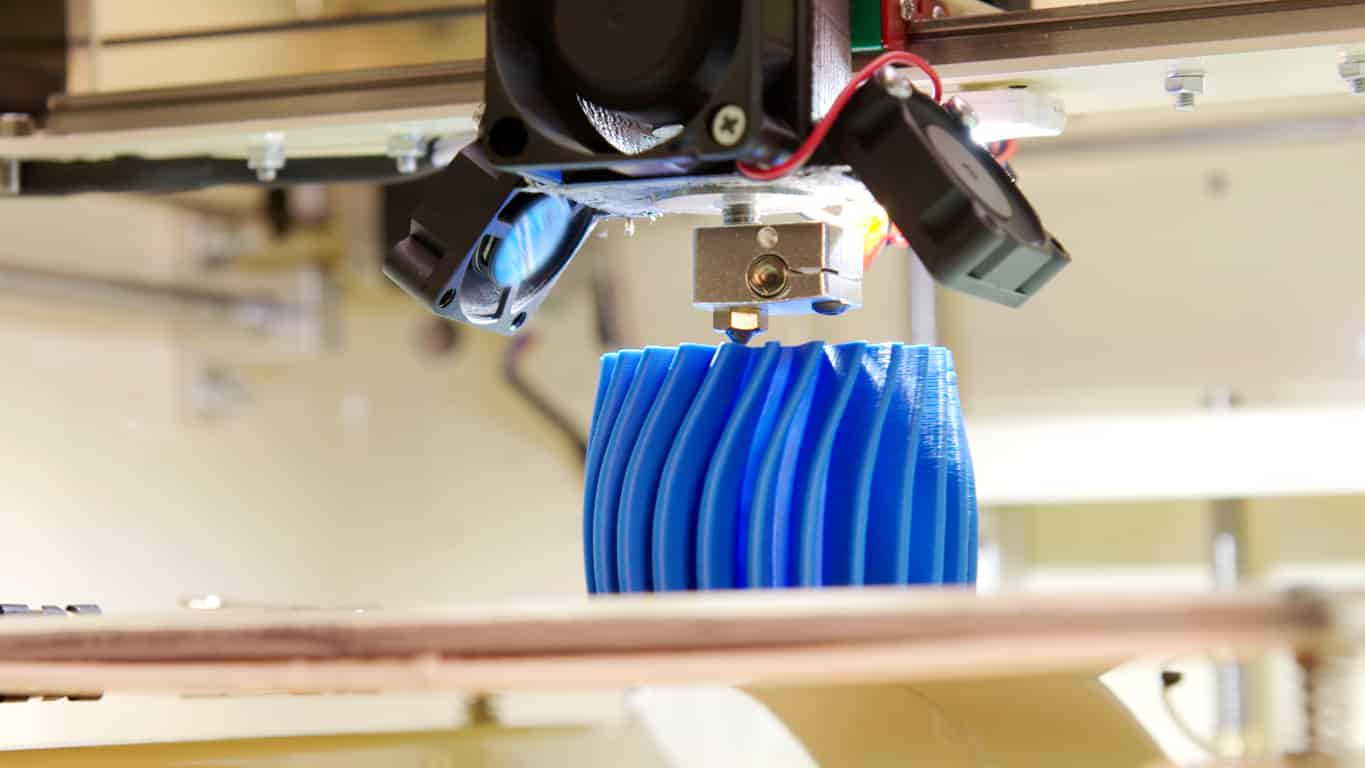
Additive Manufacturing vs. Subtractive Manufacturing: What are Their Differences?
The differences between additive manufacturing and subtractive manufacturing are significant. Additive manufacturing, often referred to as 3D printing, adds successive layers of material to create an object. Subtractive manufacturing removes material to create an object.
Additive Manufacturing
Both technologies utilize CAD drawings to create parts; additive manufacturing melts or fuses powder or cures liquid polymer materials to form parts based on the CAD drawings. Additive processes are slower to manufacture, and several technologies require post-manufacturing methods to cure, clean, or finish the product. The surface finish is not as smooth as subtractive manufacturing, and the tolerances aren’t as precise. These processes are ideal for lighter parts, material efficiencies, rapid prototyping, and small to medium-batch manufacturing.
Complex geometries, including the printing of articulating joints with additive manufacturing, are available. The geometries are more complicated, and set-up is quick and easy, with no operator required during the printing process. The most common materials used in additive manufacturing are plastics and metals. The equipment cost is less than subtractive manufacturing, and various material colors are available for most 3D printing operations.
The additive technologies include:
- Binder Jetting — The process uses liquid bonding agents selectively deposited to join powder materials. Materials include metal, plastic, ceramic, and sand.
- Directed Energy Deposition (DED)—DED utilizes focused thermal energy to fuse materials as they are deposited. Materials include Wire and powder.
- Material Extrusion—Extrusion selectively dispenses material through a nozzle or orifice in layers. Materials include plastics, nylons, FDM, FF, and sand.
- Material Jetting—Droplets are selectively deposited to form products. Material includes photopolymers, wax, sand, and poly-jetting material
- Powder Bed Fusion—Thermal energy selectively fuses regions of a powder bed. Materials include metals, polymers, and fibers.
- Sheet Lamination—Sheets of material are bonded to form an object. Materials include metal, paper, wood, and plastics.
- Vat Photopolymerization—Pre-deposited photopolymer is selectively cured by light-activated cross-linking of adjoining polymer chains. Materials include photopolymers.
Subtractive Manufacturing
Subtractive manufacturing involves material removal with turning, milling, drilling, grinding, cutting, and boring. The material is typically metals or plastics, and the end product has a smooth finish with tight dimensional tolerances. A wide variety of materials are available. Change-overs are longer, but automatic tool changers help reduce time-consuming delays. The processes can be fully automated, although an attendant may oversee two or more machines.
The equipment costs are higher and usually require additional jigs, fixtures, and tooling. It is best suited for large production with reasonably fast manufacturing time but lengthy changeovers. Material handling equipment helps both processes with material loading and removal. Geometries are not as complex as additive manufacturing processes.
Subtractive manufacturing technologies include:
- Abrading—This manufacturing process uses friction to wear the material surface by grinding and polishing products.
- CNC Machining Centers — The computerized manufacturing process to control complex machinery via pre-programmed software to regulate the machining equipment to cut and shape parts. This equipment includes milling, turning, drilling, boring, grinders, and 5-axis CNC machining centers.
- Electrical Discharge Machining (EDM)—Also known as “spark machining,” “wire burning,” or “wire erosion,” EDM is a non-traditional machining process that utilizes electrical discharges ranging from 80.00ºC to 12,000ºC to remove material from a workpiece placed in a dielectric liquid.
- Laser Cutting—This manufacturing method utilizes a gas laser, often CO2, for energy. The laser beam is guided by mirrors and directed toward the workpiece to remove material. The laser beam output is between 1,500 and 2,600 watts.
- Waterjet Cutting—Waterjet cutting is an accelerated erosion process using a high-pressure water stream. This CNC method of cutting objects uses energy from ultra-high-pressure water that becomes hypersonic at speeds up to 2,500 mph (Mach 3).
Materials for the subtractive manufacturing processes include hard metals, soft metals, thermoset plastics, acrylic, wood, plastics, foam, composites, glass, and stone.
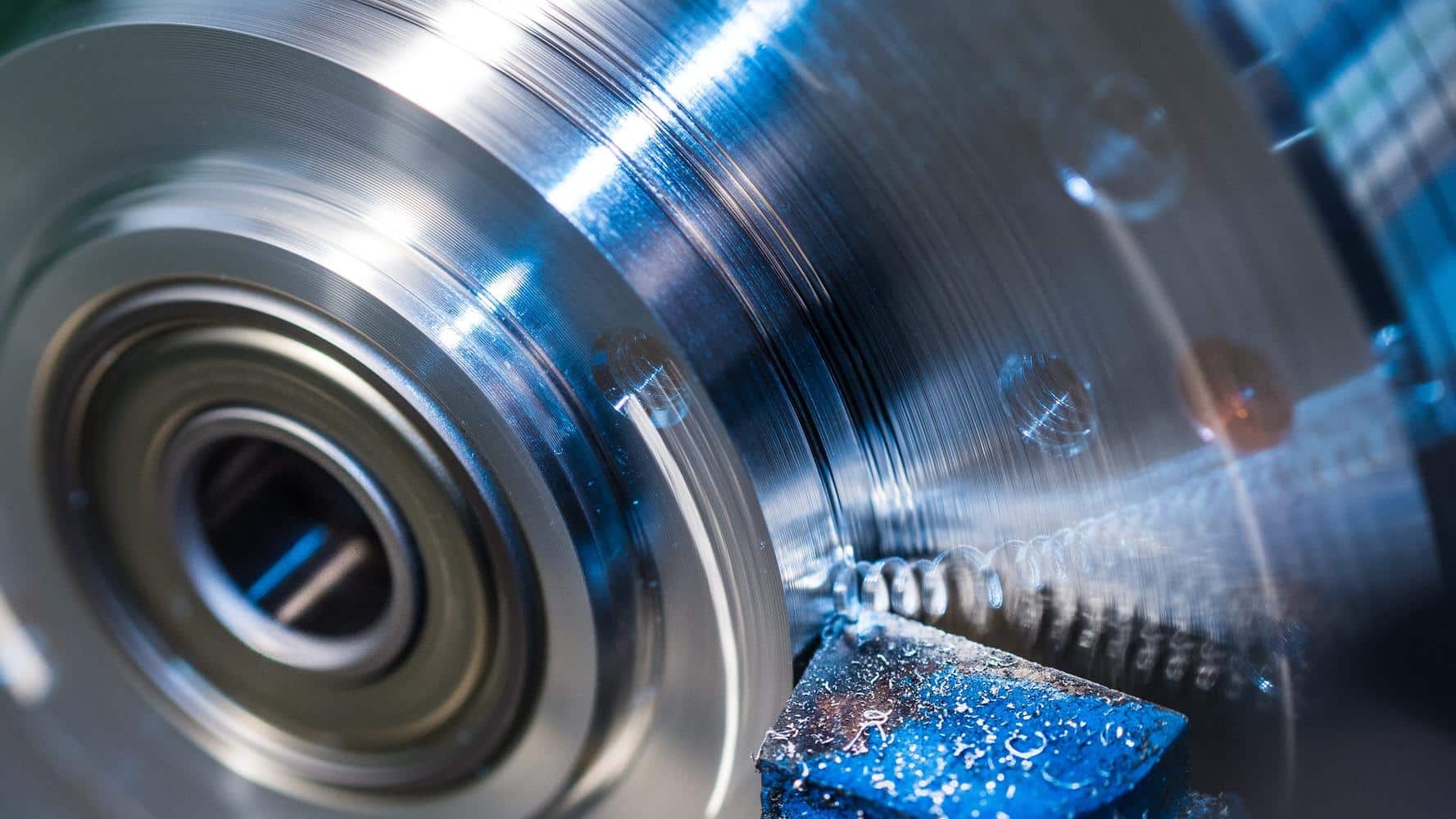
Comparison Table Between Additive Manufacturing vs. Subtractive Manufacturing
Additive Manufacturing |
Subtractive Manufacturing |
|
Process: |
Builds an object by adding layers of material. |
Removes material from a larger piece or material to create an object. |
Equipment: |
This process includes digital manufacturing, 3D printing, and additive fabrication, such as binder jetting, powder bed fusion, sheet laminate, directed energy deposit, material extrusion, and material jetting. |
This process includes traditional machining, CNC machining, laser cutting, EDM, abrading, plasma cutting, and waterjet cutting. These processes include turning, milling, drilling, grinding, cutting, and boring. |
Production: |
Suitable for prototypes and small batch production. |
Best suited for mass production |
Equipment Costs: |
Professional Desktop Printers: $3,500+ Industrial Printers: $100,000—$400,000+ |
Hobby Grade Mills and Lathes: $2,000+ Entry Level CNC Machining Center: $60,000+ Industrial 5 Axis Machining Centers: $500,000+ |
Accuracy: |
Tolerance as small as 0.004″ |
Tolerance as small as 0.001″ |
Area Requirements: |
Desktop printers can operate in most offices or workshops. Industrial printers often require a large footprint on the manufacturing floor. A controlled environment is often required. |
Small machines often operate in garages and workshops. Industrial machines require a large footprint on the manufacturing floor. |
Additional Equipment: |
Post-processing systems for curing, finishing, and cleaning are required with certain printers. Industrial applications may have material handling systems. |
Various tooling, fixtures, robotics, and material handling systems may be required. Coolant systems, tool changers, and waste removal are also necessary. |
Complexity: |
Extremely complex designs are achievable, including articulating parts. |
Ideal for intermediate geometry parts. |
Cost: |
Typically, more expensive than subtractive manufacturing, although plastic prototyping is much quicker. |
Less expensive for metal manufacturing. |
Materials: |
Primarily plastic materials. Other materials include metals, ceramics, plasters, graphite, carbon fiber, nitinol, polymers, and paper. |
Materials include hard metals, soft metals, thermoset plastics, acrylic, wood, plastics, foam, composites, glass, and stone. |
Properties: |
Thermoset plastics have a potential structural weakness at the layers. |
Metals are structurally sound with excellent heat resistance. |
Set-Up: |
Little/no set-up required. |
Set-up is often substantial but can increase the speed with automatic tool changers. |
Speed: |
Printing processes are slower than machining but operate faster with thermosets than with metal materials. It is preferred for prototyping and small-batch production. |
A relatively fast process. Best for large production due to extensive set-up time. |
Surface Finish: |
The surface can be slightly rough depending on the material and printing speed. |
The finish is smooth. A variety of finishes are available for machining. |
Training: |
Desktop printers are quick to set up, but programming takes some time. Industrial printers require training and an attendant. |
Hobby-grade machines require some training. Industrial equipment requires extensive training, and production can be fully automated with attendant oversight. |
Subtractive vs. Additive Manufacturing Cost: Which Is More Expensive?
Additive and subtractive technologies have a variety of different processes. The costs and capabilities range from desktop machines to large industrial equipment. Prices have dropped significantly in recent years, especially for additive technologies. Compact, easy-to-use desktop additive and subtractive manufacturing tools are available today for professional workspaces, machine shops, and workshops.
Entry-level 3D printers start at several hundred dollars, and the cost of suitable desktop printers for enthusiasts begins at approximately $3,500 up to $20,000. Industrial printers start at $10,000 and cost over $400,000.
Hobbist mills and lathes start at $2,000, and an entry-level CNC machining center can begin at $60,000. Industrial 5-axis machining centers cost $500,000 plus.
Applications of Additive vs. Subtractive Manufacturing
Additive and subtractive manufacturing produce a wide range of products across several industries. Additive manufacturing is preferred for rapid prototyping, small batch production, and on-demand production. Subtractive manufacturing has long produced prototypes but is best suited for large production runs.
Almost every industry uses additive manufacturing products, including aerospace, architecture, automotive, aviation, consumer goods, lifestyle, industrial manufacturing, material handling, robotics, medical and dental, and sports. Products include medical implants, aircraft components, automotive parts, investment casting patterns, tooling, brackets, turbine blades, jewelry, entertainment, biking, and customizable products.
Subtractive manufacturing products are in the same industries and more, including aerospace, architecture, automotive, aviation, consumer goods, food service, lifestyle, industrial manufacturing, material handling, oil and gas, robotics, medical and dental, and sports. These products are often used in harsh environments where robust products are critical. Subtractive manufacturing parts are used everywhere, from pistons to fan blades to steel drums to turbines.
Subtractive and additive components often complement each other in producing tooling, jigs, and fixtures.
Hybrid Process: Implement Design to Prototype
Hybrid approaches combine additive and subtractive processes, taking the best of both worlds and incorporating them into one machine. These hybrids capitalize on both manufacturing systems’ strengths and require specialized equipment. Hybrid manufacturing makes producing complex parts quicker and easier.
An example would be polishing the surface of a 3D-printed part or drilling a hole that requires a tight tolerance.
Get multiple quotes for your parts in seconds