3D Printing Supports
The use of 3D printing supports is often necessary to achieve the desired design for your printed part. Learn more in this helpful guide!
Introduction to 3D Printing support
3D printing is a ground-breaking technology that is revolutionizing the additive manufacturing world. Part of the reason for this is its ability to create parts and products with highly complex geometric patterns and designs. However, achieving this complexity with 3D printing isn’t always easy. In fact, many times 3D printing supports need to be added to the part design so that the print will come out as you intended and not fail during the 3D printing process.
When it comes to planning for incorporating 3D printing supports in your next print project, part designers often have questions. In this guide to 3D printing supports we answer some of the most common questions such as when to use 3D printing supports, what are the different types of supports available, how to remove the supports after printing, and much more!
3D Printing Supports: When to Use Them?
Determining when to use 3D printing supports depends largely on the specific type of 3D printing technology you are using. For example, fused deposition modeling (FDM) 3D printers extrude filament layer by layer. Therefore, if your print design has an overhang that doesn’t have inherent support underneath, your 3D print will not come out correctly. In these cases, 3D printing supports are incredibly beneficial for part designers. Other examples include selective laser sintering (SLS) and multi jet fusion (MJF) 3D printing. These 3D printing technologies print with powder that surrounds the part and acts as a support. In these cases, supports aren’t necessary when it comes to planning your part design.
Another factor to consider when deciding when to use 3D printing supports is the degree of complexity of your part design. For example, for overhangs you will need to assess the degree of tilt. If the tilt is 45 degrees or less, most FDM printers can print the overhang without supports. On the other hand, if the overhang angles are greater than 45 degrees, you may need to plan for the use of supports otherwise your overhangs will probably be deformed. Another common example is if a part design has a bridge over a gap between two areas. If this bridge is longer than 5 mm, you will most likely need to include support structures in the gap in your part design.
What are the Different Types of 3D Printing Supports?
The type of 3D printing support that you use will be determined by the specific type of 3D printing technology you select. For example, FDM 3D printing technologies utilize tree and lattice types of supports. Lattice supports are great options for holding parts in place and building columns, which is especially helpful for parts with steep overhangs in their designs. In fact, lattice supports are extremely common because of how efficiently they can be produced and their high level of compatibility for most 3D printed parts.
Additionally, tree supports, as the name implies, start with thick trunks and get thinner as they get closer to the part like tree branches. Tree supports are great for parts that need a more selective form of support such as designs that have overhangs that are strictly vertical.
Additionally, if you’re using a 3D printer with two-extrusion heads, soluble supports are an option. With soluble supports, materials that are dissolvable such as limonene will be extruded along with the 3D printing material. Soluble supports are a great choice if your budget allows because they can be washed away by simply soaking them in water.
These dissolvable supports are the ideal solution for ensuring a great surface finish because they remove the need for additional steps during post-processing, which decreases lead time and reduces overall project costs. It’s important to note that 3D printing material and soluble support material can’t be extruded together. Therefore, if your 3D printer only has one print head, soluble supports aren’t an option.
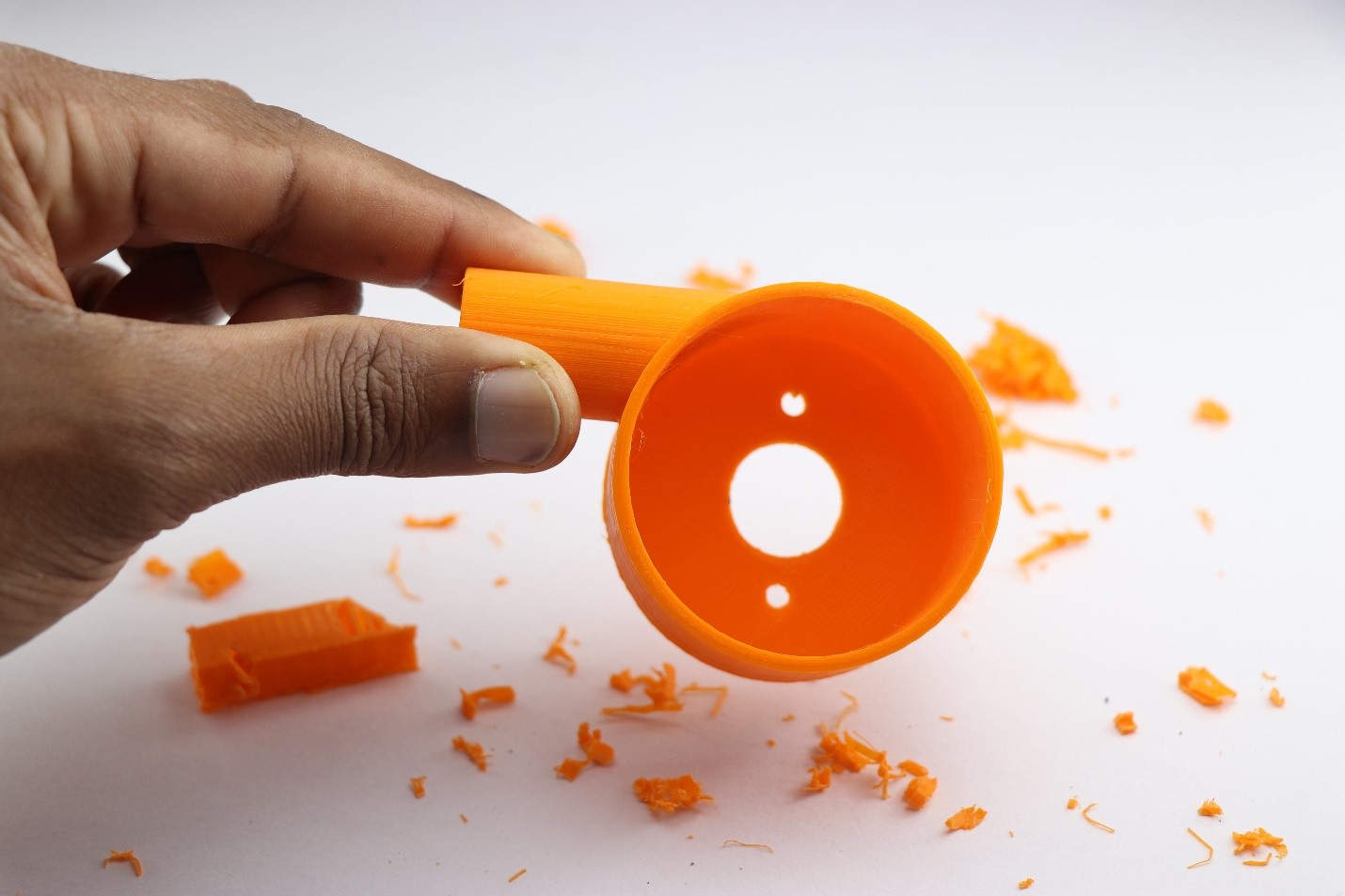
Removing Your 3D Printing Supports
One of the most important factors to understand when it comes to 3D printing supports is how they are removed from your part after printing. As mentioned above, the ease of support removal can impact your project lead times and cost. Moreover, the more locations on your part that are connected to supports, the more potential there is for marks and breaks to occur at the support locations.
For example, lattice supports provide complete surface support, but as a tradeoff they are difficult to remove without negatively affecting the quality of your part’s surface. By contrast, tree type supports, which are used more sparingly and in more precise locations, will result in less contact locations on your part and a much easier removal process.
After printing is completed, pliers can be used to carefully twist, grab, and pull your supports off your print. Moreover, if the support you are removing is larger and easily accessible, you can also carefully begin removing it with your fingers. After your supports are removed, if aesthetics are an important consideration, you can sand the areas of your part that were in contact with the supports to create a smooth surface finish.
The Downsides of Using 3D Printing Supports
While 3D printing supports enable the creation of more complex parts, they do come with some downsides. The use of supports requires careful removal, the potential for post processing, and increased project lead times. Depending on the specific 3D printing support type that you use, its level of complexity and size will have a bearing on your overall production time. In this respect, tree support types can be more demanding on your printer. Moreover, the post-processing steps that may be required (depending on your intended use) will need to be taken into consideration since support removal and sanding can be somewhat labor intensive.
In addition to the increased lead time, another downside associated with 3D printing supports is the cost of the supports. The reality is 3D printing supports require more material to be used for your project. For example, if steep overhangs are prominent in your design and lattice supports are needed, you can end up spending a considerable amount of money on the material used to create the supports. As a result of the increased lead time and costs associated with 3D printing supports, there are some alternatives that you can consider for your next 3D printing project.
Alternatives to Using 3D Printing Supports
For some part designers, the added lead times and increased costs associated with 3D printing supports are too burdensome. In these cases, there are alternative options you can explore with 3D slicers and your 3D printer.
When it comes to creating supports for your 3D printed parts, you ideally want to balance the thickness and density of the supports with the actual speed at which they are cooled. In other words, the longer your supports are exposed to high heat, the longer they will take to cool off and the more they will have adhered to your print. Therefore, the cooler you can keep your supports, the easier they will be to remove. In addition to following proper cooling methods, the density of 3D printing supports also impacts their temperature. For this reason, if you have the option to reduce the density of your supports, they will more easily release heat.
This is where 3D slicers can help you make valuable adjustments. A 3D printing slicer prepares your design for the 3D printer by creating a G-code. A 3D slicer cuts the model into 2D layers and provides the coding instructions to the 3D printer to print each slice. 3D slicers are only used for desktop 3D printers. For commercial online 3D printing services, 3D slicers are not necessary, and the process is much simpler as a result.
However, there are some important support design considerations that you need to keep in mind. This includes determining which orientation is the most consistent when it comes to support creation. Perhaps you’ve already attempted to adjust the orientation of your part, but it still needs a lot of supports. In this case, you could try modifying the overhangs. Additionally, you could consider separating your design into two separate components. The drawback to this approach of course is that you will have to add time for assembly after printing. Another alternative is that you could consider using a different 3D printing technology that doesn’t require the use of supports. For example, SLS 3D printers allow designers to achieve complex geometries without the use of 3D printing supports.
Get multiple quotes for your parts in seconds