Urethane Casting Services
3DEXPERIENCE Make Online Urethane Casting Service | Dozens of expert manufacturers.
SECURE PAYMENTS
Via payment card or purchase order
PROTECTED IP
Your data is confidential and secure with us. Use your own Non Disclosure Agreement
INSTANT QUOTE
For 3D Printing and CNC Machining, get quote in few seconds.
Urethane Casting service with 3DEXPERIENCE Make
3DEXPERIENCE Make is an On-Demand Manufacturing platform, which connects designers or engineers with industrial 3D Printing service providers. Our service providers are mostly based in North America (the United States and Canada) and Europe (United Kingdom, France, Netherlands, Germany, etc.). Urethane Casting service is today mostly used for Prototyping or Small Series.
Discover Our network of Urethane Casting service providers offers hundreds of materials for your project.
Discover How 3DEXPERIENCE Marketplaces Boost Your Design to Manufacturing Process
You’re in good company. Thousands of leading companies from all industries use our solutions.
Online Urethane Casting service: how does it work?
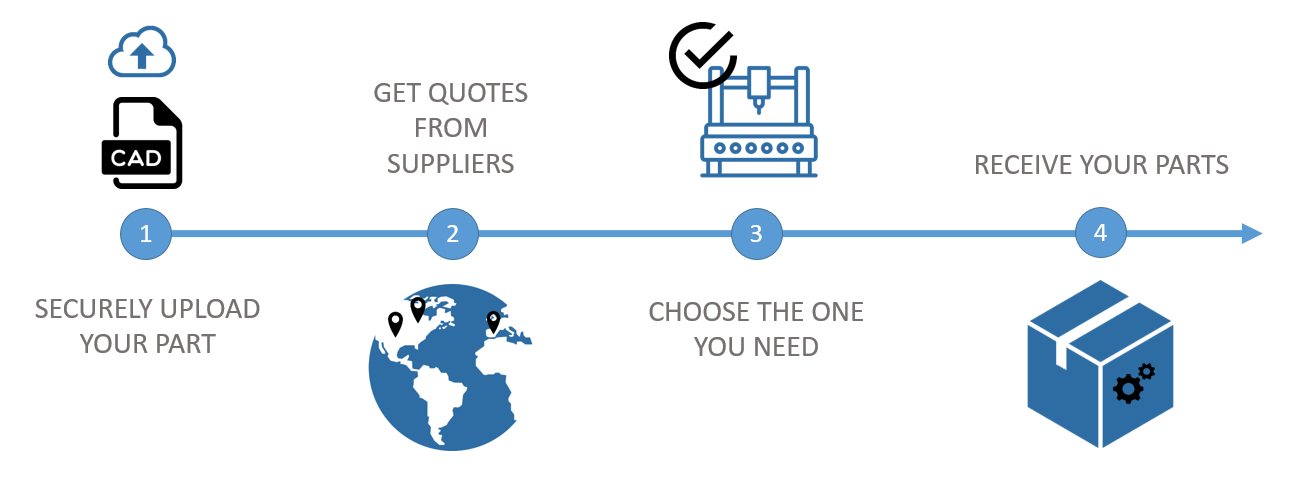
Features to help you
Check & repair or Geometry check is a feature that helps you to understand Geometry issue of your part and could repair it live and online.
Check & Repair
Check & repair or Geometry check is a feature that helps you to detect geometry issue on your part and repair it online and live.
Manufacturability Check
This feature is available only for 3D Printing service. It helps you check the manufacturability of your part, depending on the materials and the process.
Instant quote engine
Receive in seconds several quotes thanks to our instant quote engine.
What is Urethane Casting?
Urethanes are versatile compounds comprised of nitrogen, hydrogen, and oxygen; it is a crystalline compound, an ester of carbonic acid (heated with alcohol and an acid catalyst). Urethane is a common sealant because of its natural resistance to water, oil, and oxidation. The material is abrasion and extreme-temperature resistant. Urethane is also an excellent choice for casting low volume, durable parts while maintaining production-level quality. Read on to learn more about urethane casting utilizations and design strategies.
In basic terms, urethane casting involves designing the master part pattern, making a mold from the pattern then pouring or casting the resin to produce urethane casting parts or urethane casting prototypes. Each step involves multiple processes and can be rather complex.
Making the Master Part Pattern
The first portion of making the master part pattern is to perform the design of the component utilizing mechanical engineering principles and a 3D modeling platform, such as SOLIDWORKS. The CAD model of your part will be utilized to make the Master Part Pattern for the part to be cast. For the 3D model design, one should consider how the part will be molded and how the urethane casting material will be removed from the mold. The following tips are helpful when making the Master Part Patter CAD model:
- Since the mold for urethane parts is likely comprised of silicone, you do not need to design mold relief or draft angles.
- Consider incorporating more complex features, such as deep/narrow holes, internal cavities, and channels, with secondary, post-cast processes.
- Gates should be designed for resin and curatives to be injected. The size and location will be dependent upon the volume of the cast part and the profile of the casting pattern.
- Vents should be designed to allow the escape of trapped air inside the mold.
- When splitting your part into segments, you need to have locators on the mating surfaces to prevent the shifting of the mold halves. Shifting can change the parting line of the molds and create issues with dimensioning or tolerancing of the final parts.
Ultimately you should simply design the master part pattern with the end goal of production of urethane cast parts.
Manufacturing the Master Part Pattern
Once the CAD model is finalized, it is sent to a manufacturing provider which typically chooses to print the Master Part Pattern. Most often the printing is accomplished by the PolyJet 3D (PJ3D) Fused Deposition Modelling (FDM), or Stereolithography (SLA) methods. CNC machining may be utilized to create the master part pattern but 3D printing is typically more cost-effective. The main goal of the master part pattern printing is to create an accurate silicone mold for the urethane molded parts.
Making the Urethane Part Mold
Most urethane part molds are made from pouring liquid silicone around the parts to create a mold. First, a box is constructed which will be utilized to hold the master part for the pouring of silicone around it to create the mold. Next, the master part is securely placed in the box. Thirdly, the liquid silicone materials are poured into the box, around the master part pattern. The silicone is cured in typically several steps. Curing is often accomplished utilizing one of two methods: condensation curing or addition curing. Typically, the mold is split in two for the removal of the master part, or the molding process is designed to create a two-part, mating mold. Another option for a silicone mold is called a skin mold and it is created by pouring liquid silicone on the master part pattern, layer by layer until the desired thickness is achieved. Sometimes, features to be molded that may be susceptible to fatigue are replaced with stronger materials.
Casting the Urethane Part
Urethane casting of parts involves the utilization of a type of polyurethane or urethane casting resin to fill a silicone mold for part production. The urethane casting material is typically two components, resin, and curative agent, which chemically react upon mixing to form the urethane material. The two components are mixed in a container and degassed, to remove any air bubbles. The molds may be filled with urethane utilizing pouring or a pressure-fill method, such as screw injection. The urethane cast part is then cured and the mold is split into two parts so that the cast part may be removed.
Post-casting operations such as grinding, cutting, CNC machining, drilling, or milling may be performed on the urethane cast parts as needed. Gates or vents may be smoothed or cut. Holes or channels can be added. But the urethane cast parts do have a low melting point so coolants must be utilized during machining as a preventive measure.
Urethane Casting Applications
Urethane parts may be utilized for a wide variety of components from automobile parts to medical devices to consumer products and even prototypes. Here are a few examples of common urethane casting parts:
- Shore D urethanes can be utilized to make tough and durable parts such as enclosures, cases, consumer electronics, medical devices, packaging, and even toys.
- Softer urethanes, Shore A urethanes, with higher elasticity are useful for flexible, yet impact-resistant parts. Examples include rubber gloves, overmolds, buttons, keypads, rubber boots, and buttons.
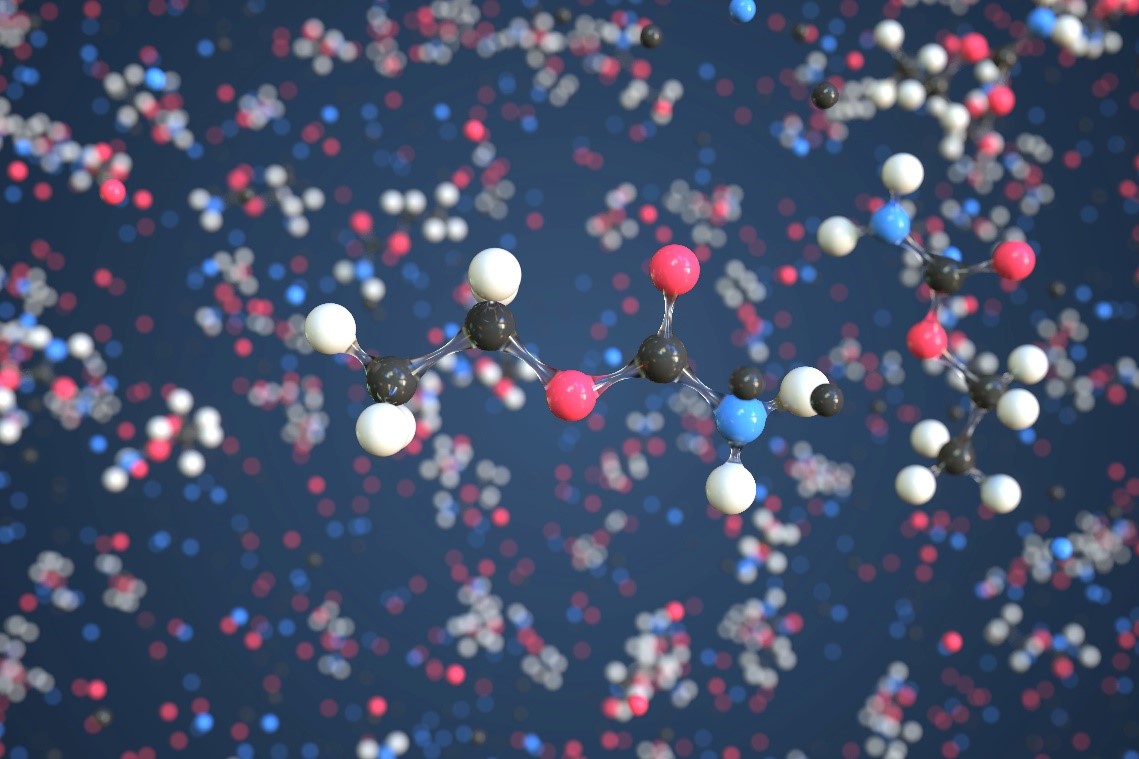
Urethane Casting Materials
Urethane parts may be cast utilizing a variety of materials. Material selection should be based on several factors including cosmetic considerations, durability, part life, price, utilization or application requirements, strength, physical properties, chemical properties, environmental exposure, and chemical resistance. Urethane materials may also be referred to as polyurethane materials. There is no difference between the two terms; they may be utilized interchangeably. A polymer is just a group of repeating units that are chemically linked. A polyurethane part simply contains multiple urethane groups. The following table summarizes some of the most utilized urethane casting resins:
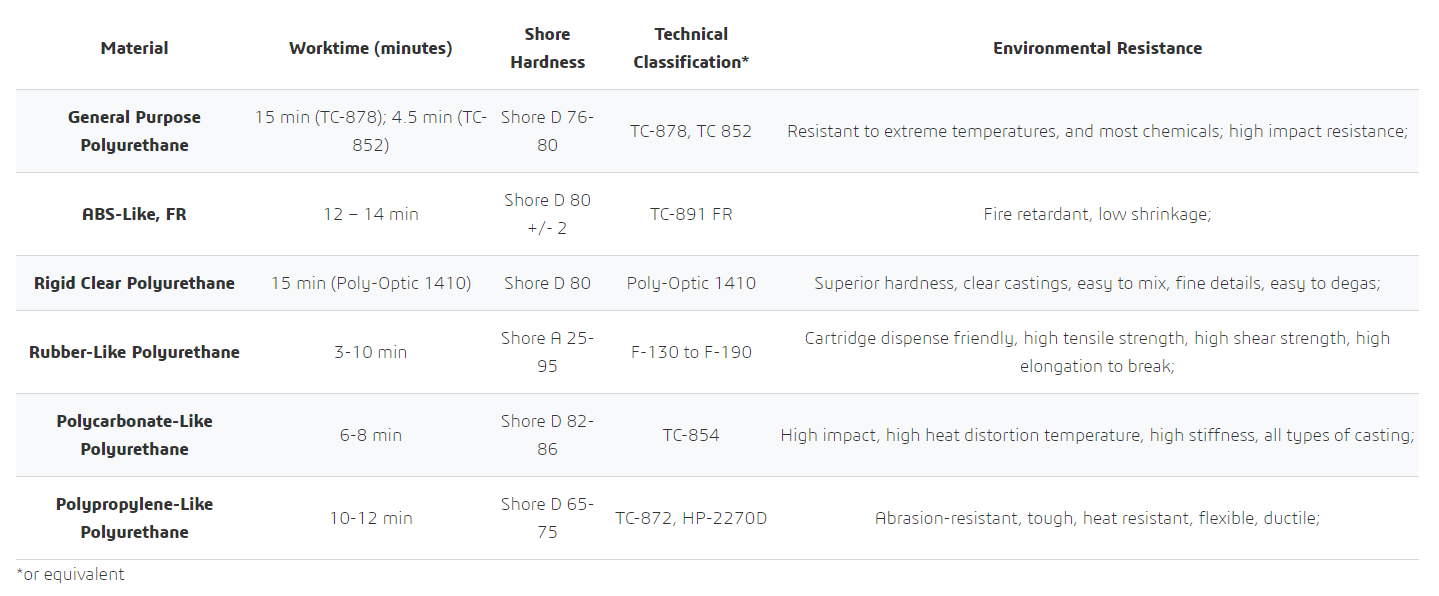
Benefits and Challenges of Urethane Casting
Urethane casting offers a significant number of benefits. It requires a simple set-up of easy-to-obtain materials and simple processing. The investment cost is low for starting a urethane casting operation. Silicone molds are cheaper and easier to produce than metal tools or molds. Therefore, prototypes can be made faster and for lower costs. Urethane molds are faster to create than hard molds, around three days versus one to two weeks. In addition, there are a wide variety of urethane/polyurethane materials to choose from for your cast parts, resulting in a wide range of available physical properties.
Urethane castings do have some challenges associated with them. The cast urethane parts may not be as machinable as their metal counterparts. In addition, the silicone molds utilized for urethane part casting may not be as durable, making the process better suited for low-volume or prototype runs.
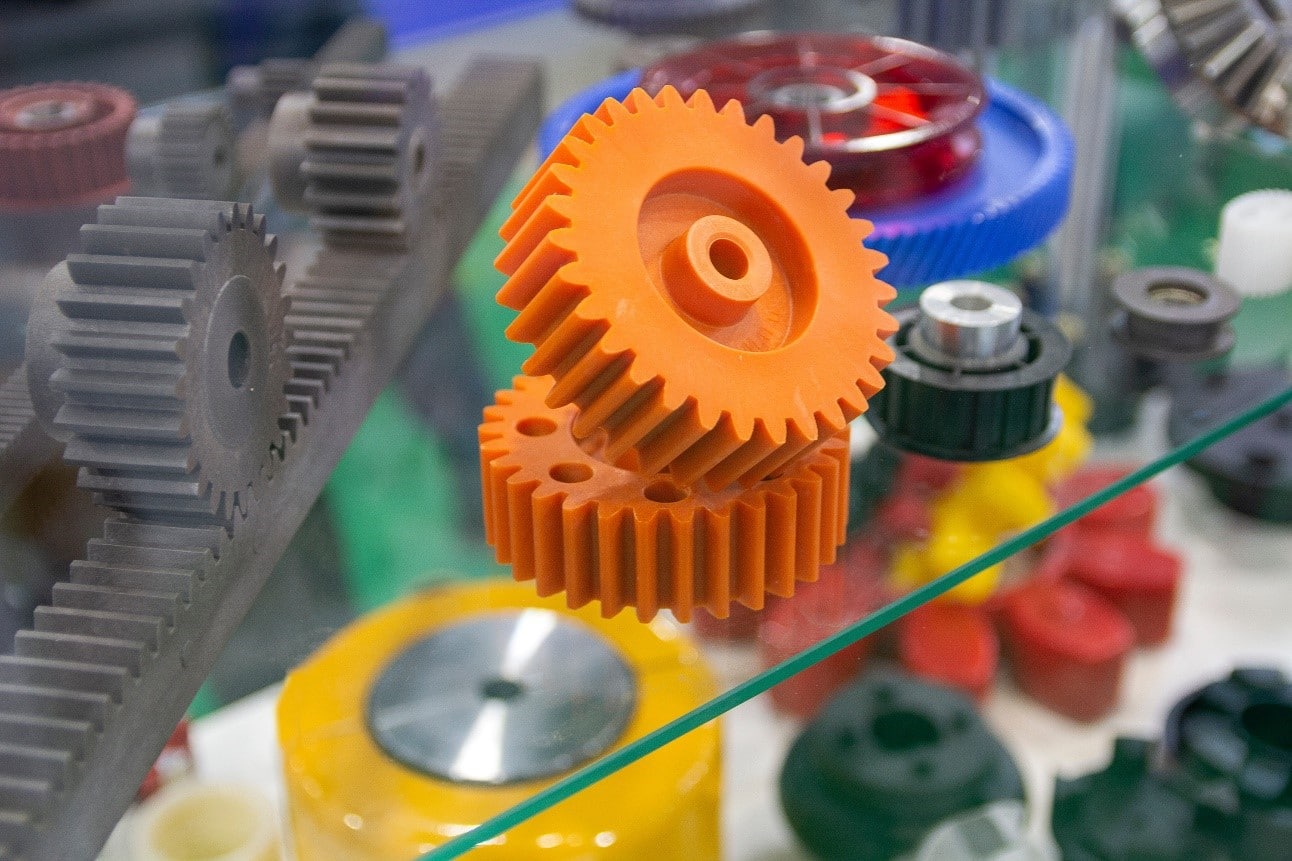
Discover our other materials for manufacturing
Get multiple quotes for your parts in seconds