Vacuum Molding
Discover what is the manufacturing molding process Vaccum Molding and its usage in the industry.
Introduction to Vacuum Molding
Vacuum molding, sometimes called vacuum forming, is a straightforward molding process that uses vacuum pressure to force a sheet of heated and stretched plastic onto a single-surface mold. The plastic is heated to a forming temperature and the suction holds the plastic sheet against the mold until the desired shape is achieved. Vacuum molded components are preferential to complex fabricated sheet metal, fiberglass, or plastic injection molding for kiosks, automated teller machines, medical imaging equipment, engine covers, or interior trim and seat components train wagons.
There is a broad range of possible patterns in vacuum molding. Wood is the most common mold for vacuum molding, mainly because of its affordability and its freedom to perform design changes. Recycled objects can also become molds for their sustainability. Although costly, aluminum molds can accelerate the fabrication process because of their effectiveness with shallow draw parts. Composite molds are more affordable than cast or machined aluminum molds and offer reliable durability while producing high-quality parts. The most suitable materials for vacuum molding are thermoplastics, while the most common and adaptable is High Impact Polystyrene Sheeting (HIPS). Acrylic is a suitable material for vacuum molding, used for its transparency, in applications such as aerospace, for example, with cockpit window canopies.
Finishing operations are necessary to transform the product into a suitable state. Common finishing methods include guillotining, drilling, roller cutting, press cutting, and CNC (Computer Numerical Control) machine cutting.
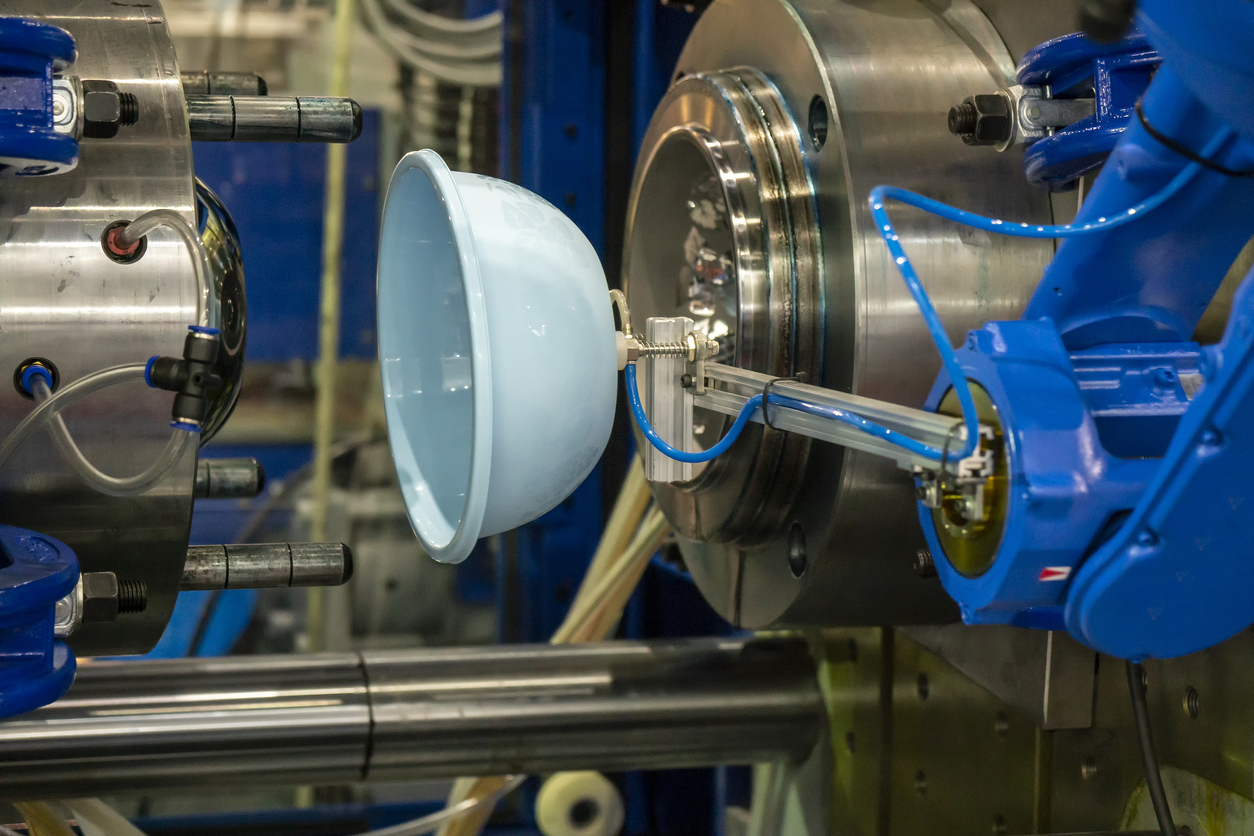
Get multiple quotes for your parts in seconds