Stamping - Pressing
Discover what is the manufacturing forming process Stamping - Pressing and its usage in the industry.
Introduction to Stamping Pressing
Stamping, also known as pressing, entails using a stamping press to form a net shape from either blank or coil form flat sheet metal using a tool and die surface. Like the processes used to create sheet metal, stamping also encompasses punching (with a machine or stamping press), blanking, embossing, bending, flanging, and coining. It is possible to carry out a stamping process in either a single operation or a series of stages.
Historically, the bicycle industry started to use stamped for mass-produced in the 1890s. Stamping replaced die forging and machining, resulting in great cost reduction. Although weaker than die forged parts, they were good enough for that purpose at the time.
Embossing is a stamping process used to produce raised or hollowed designs or relief in sheet metal. The method performs with a combination of heat and pressure depending on user requirements. Male and female roller dies are fit with a pattern or design and operate by drawing in a sheet of metal that embosses the design. The pressure and combination of heat work like “ironing” while raising the image higher than the substrate to make it smooth. It is possible to emboss ductile metals and for use in medium-to-high production runs. Likewise, it is possible to maintain the same metal thickness before and after, produce unlimited patterns (depending on roll dies), and uniformly produce a product.
Coining uses sufficiently high stress to precision stamp a workpiece by inducing malleable flow on the surface of a material. It is particularly beneficial for reducing the surface grain size and surface hardening while retaining toughness and ductility in the material more profound in the part. The term coining originates with the process initially used to manufacture coins.
In addition, stamping presses can also perform piercing and cutting. Progressive stamping combines the above methods done with a set of dies in a row through which a strip of the material passes one step at a time.
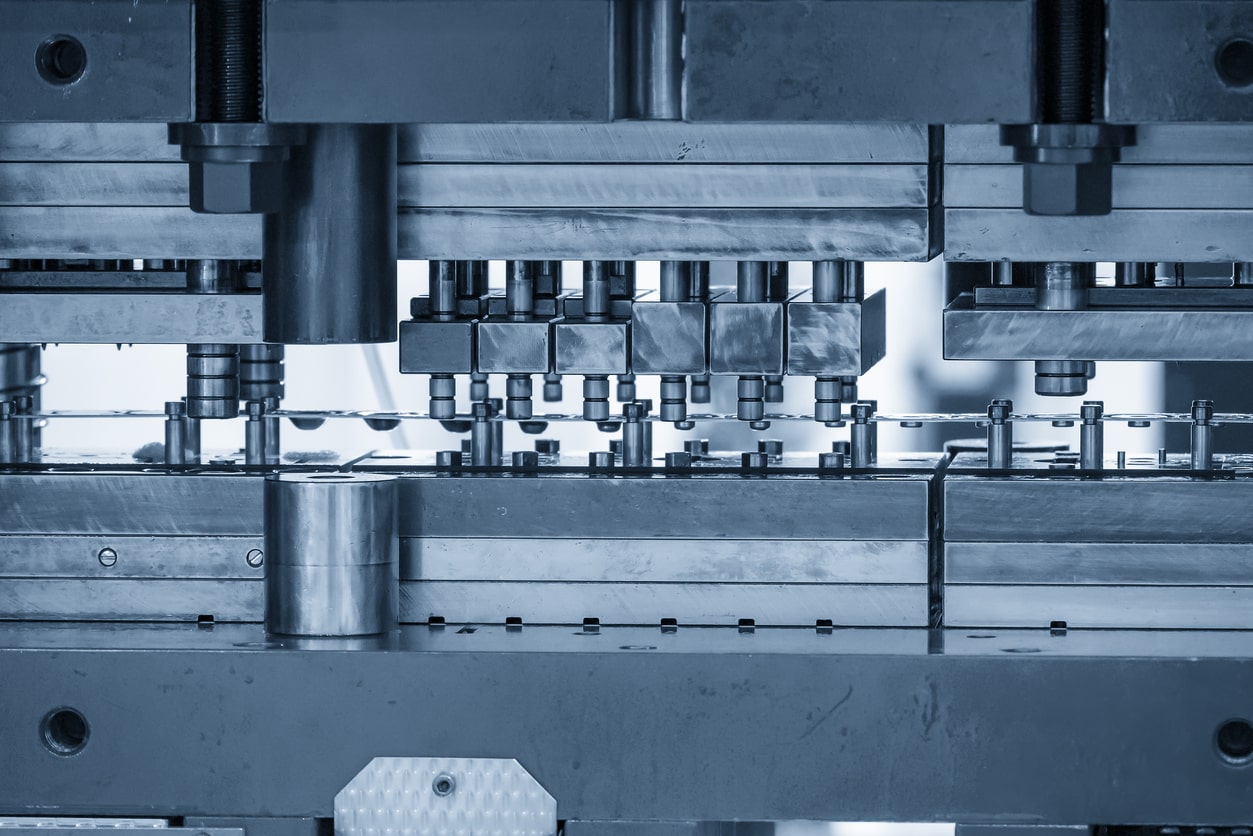
Get multiple quotes for your parts in seconds