Rotomolding
Discover what is the manufacturing molding process Rotomolding and its usage in the industry.
Introduction to Rotomolding
Rotomolding, also called rotational molding, entails filing a charge, or shot weight, of material into a heated hollow mold, followed by slowly rotating the mold, causing the softened material to disperse and adhere to the mold’s walls. The mold continues to rotate at all times during the heating phase to achieve and maintain an even thickness throughout the part. This rotation also prevents sagging, or deformation, during the cooling phase.
The distinct advantage of rotomolding is that it is an easier process than any other when producing large, hollow parts, such as oil tanks or chairs. Also, the molds used in rotomolding are significantly less expensive than different types of molds. Rotomolding generates much less wasted material; excess material can often serve for another usage, making it economical and ecological.
Another advantage lies in the molds themselves; they necessitate less tooling. Consequently, companies could put into production much faster than other molding processes. This is especially valuable for complex parts. Rotational molding is also the choice process for short runs and rush deliveries. The operator can exchange the molds quickly or use different colors without purging the mold. With other processes, purging may be necessary to swap colors.
The main drawbacks are the hard-to-reach areas in the mold and a long cooling duration that leads to significant mold downtime.
The history of Rotomolding
The first application of biaxial rotation and heat was documented in 1855, mainly to produce metal artillery shells and other hollow vessels. The initial objective of using rotation was to create wall thickness and density consistency. Eventually, the usage of rotational molding was for hollowing wax objects; shortly thereafter, chocolate factories fabricated chocolate eggs thanks to rotomolding. There were subsequently applications with the use of plaster-of-Paris in the 1920s. In the 1950s, it started with plastics and was slow to receive industry adoption because of its sluggish productivity rate and the limitation caused by few suitable plastics. The first rotomolded products were doll heads. It helps develop other plastic toys, road cones, marine buoys, and car armrests. The resulting popularity accelerated the development of larger machinery and eventually led to the creation of a worldwide trade association called The Association of Rotational Molders (ARM).
New plastics like polycarbonate, polyester, and nylon were introduced to rotational molding in the 1980s, leading to new applications for the process, such as fuel tanks and industrial moldings. Most recently, the development of plastic powders and process control improvements has led to a considerable increase in its application.
The various rotational molding machines have a broad spectrum of equipment sizes. Generally, a rotational molding machine contains molds, an oven, a cooling chamber, and mold spindles. Uniform coating of the plastic inside each mold is achieved with the spindles being mounted on a rotating axis. The quality of the molds, usually aluminum-based, depends directly on the quality and finish of the final product.
What kind of Rotomolding machines?
The different rotomolding machines are as follows:
- Rock and roll machine
- Clamshell machine
- Vertical or up-and-over rotational machine
- Material jetting
- Vertical or up-and-over rotational machine
- Shuttle machine
- Swing-arm machine
- Carousel machine
The rock-and-roll machine is specialized to produce long, narrow parts mainly. The clamshell machine is a single-arm rotational molding machine that heats and cools in the same chambers and takes up less space than the shuttle and swing arm machines. Vertical rotational machines are small-to-medium in size (compared to other rotomolding machines) and are energy-efficient, thanks to their compact heating and cooling chambers.
Although a single-arm shuttle machine exists, most shuttle machines have two arms that alternate the molds between the heating chamber and cooling station. The arms are independent of each other and they turn the molds biaxially. The swing-arm machine is beneficial for companies with prolonged cooling cycles or lengthy demolding times. It can have up to four arms with a biaxial movement. Each arm is independent of the other since it’s unnecessary to operate all the arms simultaneously. The carousel machine is one of the most common biaxial machines in the industry. It can have up to four arms and six stations and is available in a wide range of sizes.
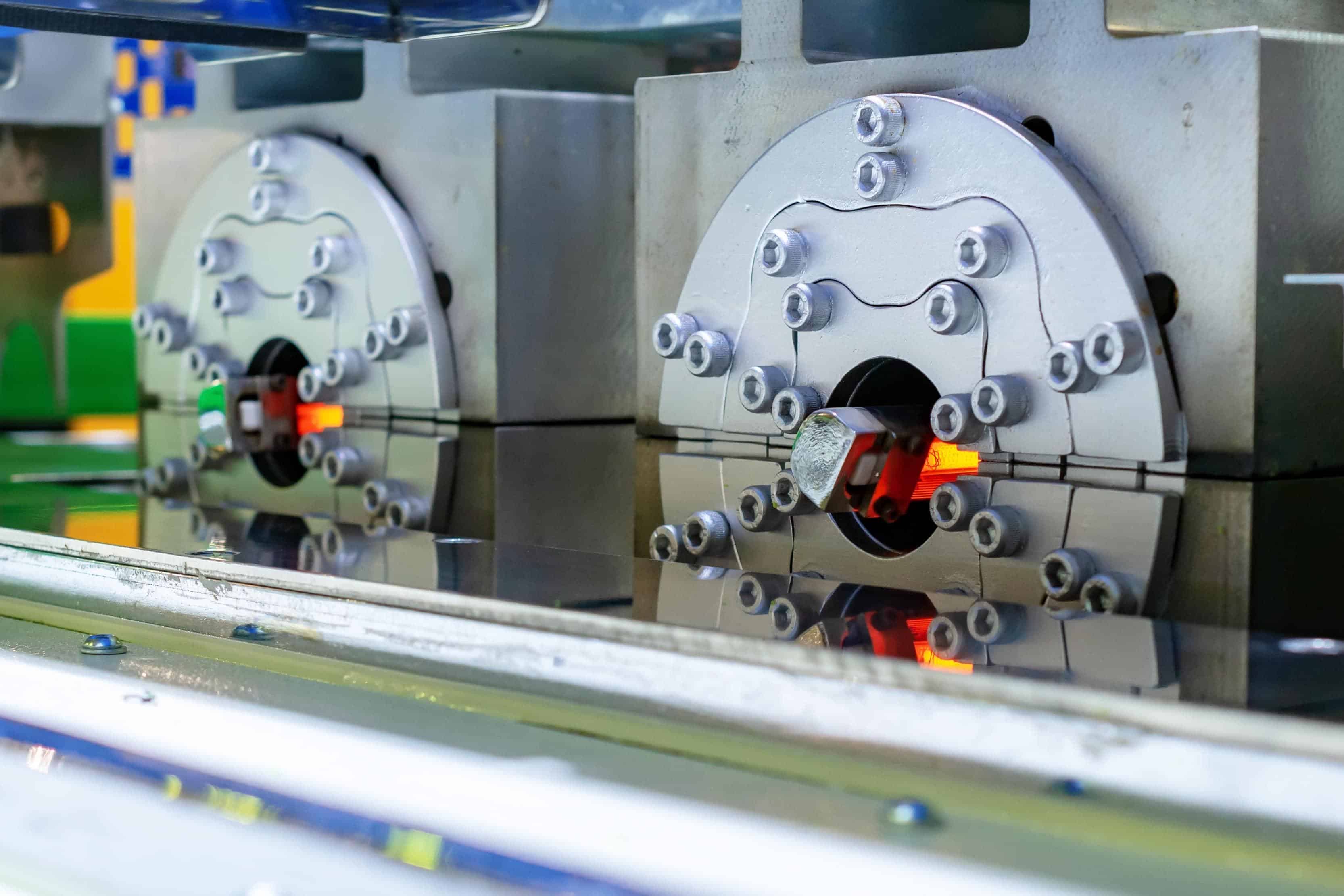
Get multiple quotes for your parts in seconds