Photopolymerization
Discover how Photopolymerization, also known as VAT, SLA, DLP, CDLP, works.
Introduction to Photopolymerization - VAT, SLA, DLP, CDLP
What is Photopolymerization ?
Photopolymerization 3D printing technology encompasses several processes that rely on the same basic strategy: a liquid photopolymer contained in a vat (or tank) is selectively cured by a heat source. Layer by layer, a 3D physical object is built until completion.
Lasers are the base of multiple types of curing devices in addition to the oldest technique. Digital Light Processing projectors and even LCD screens are now a popular way of photopolymerizing materials given their low cost and very high resolution. One of the advantages of these two techniques compared to lasers is their ability to cure a full layer of resin simultaneously. In contrast, the laser needs to illuminate the whole surface by drawing it progressively.
The most popular vat photopolymerization 3D printing technologies include the following:
- StereoLithogrAphy (SLA) SLA, also known as SL, optical fabrication, photo-solidification, or resin printing. During the SL manufacturing process, a concentrated beam of ultraviolet light or a laser focuses onto the surface of a vat filled with a liquid photopolymer, creating each layer of the desired 3D object utilizing cross-linking or degrading a polymer.
- Digital Light Processing (DLP) For the DLP 3D printing process, a digital projector screen flashes a single image of each layer across the entire platform at once. Because the projector is a digital screen, the image of each layer is composed of square pixels, resulting in a layer formed from small rectangular bricks called voxels. DLP can achieve faster print times for some parts, as each layer is exposed simultaneously rather than drawn out with a laser.
- Continuous Liquid Interface Production (CLIP) by Carbon The CLIP vat photopolymerization technique uses a tank of resin as base material. Part of the vat bottom is transparent to ultraviolet light and therefore called the window. An ultraviolet light beam shines through the window, illuminating the precise cross-section of the object. The light causes the resin to solidify (photopolymerize). The object rises slowly enough to allow the resin to flow under and maintain contact with the bottom of the object. An oxygen-permeable membrane lies below the resin, which creates a dead zone. This persistent liquid interface prevents the resin from attaching to the window, which means the photopolymerization is inhibited between the window and the polymerizer. Unlike standard SLA, the 3D printing process is continuous and claims to be up to 100 times faster than commercial 3D printing methods.
- Daylight Polymer Printing (DPP) by Photocentric Instead of using a laser or a projector to cure the polymer, the DPP manufacturing process utilizes an LCD (Liquid Crystal Display). This technique, also called LCD 3D printing, uses unmodified LCD screens and a specially formulated Daylight polymer. The company Photocentric has made this work by developing one of the world’s most sensitive daylight resins.
Two different Photopolymerization processes
Two different approaches are also competing inside the photopolymerization 3D printing technique. Both of them build the part at the interface between the last layer and the surface of the resin tank. The top-down approach consists of placing the heat source below the vat. The 3D printing platform is then progressively raised into the air, and the final part is built upside down. The second technique, called bottom-up, consists of placing the heat source above the vat. Therefore, the printer dips the 3D printing platform progressively in the vat.
Discovered by Japanese and French researchers in the early 1980s, this invention was first industrialized and patented in 1984 by Chuck Hull, the co-founder of the world’s first 3D printing company, 3D Systems Inc.
Photopolymerization is successfully applied to medical modeling, which enables the creation of accurate 3D models of various anatomical regions of a patient based on data from computer scans. The high resolution of this technique also makes it ideal for all types of prototyping, as well as mass production. Vat polymerization processes are excellent at producing parts with fine details and a smooth surface finish. This makes them ideal for jewelry, investment casting, and many dental and medical applications. Material developments have also allowed the printing of low-run injection molds. The main limitations for vat polymerization are the build size and part strength.
Photopolymer resins are available in different colors and exhibit different physical properties, each corresponding to a specific use. The range of resins includes tough resin, low residue resin (for investment casting), transparent resin, and flexible polyurethane resin.
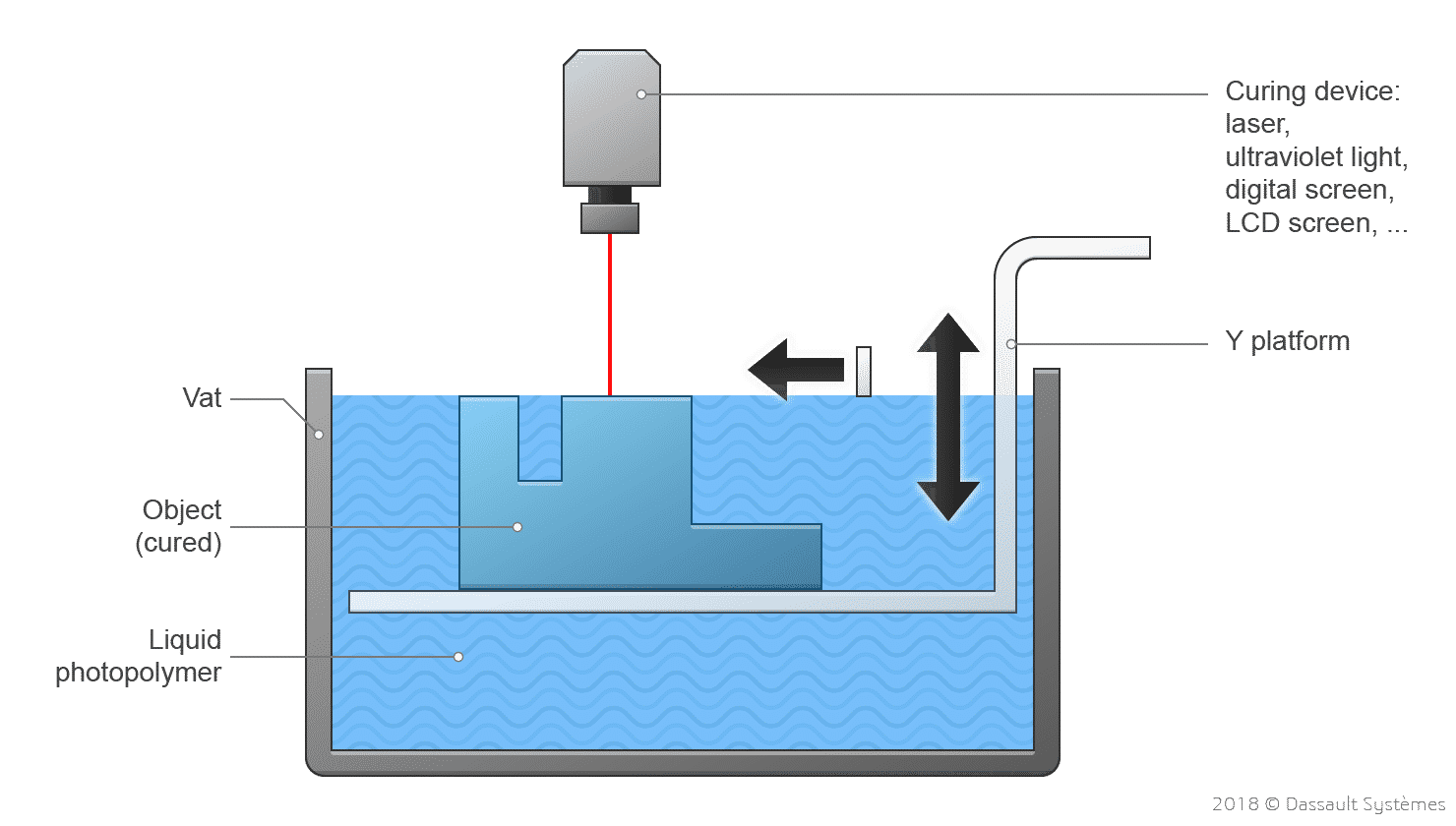
Discover 3DEXPERIENCE SOLIDWORKS for Makers
Discover how Photopolymerization works with Sculpteo
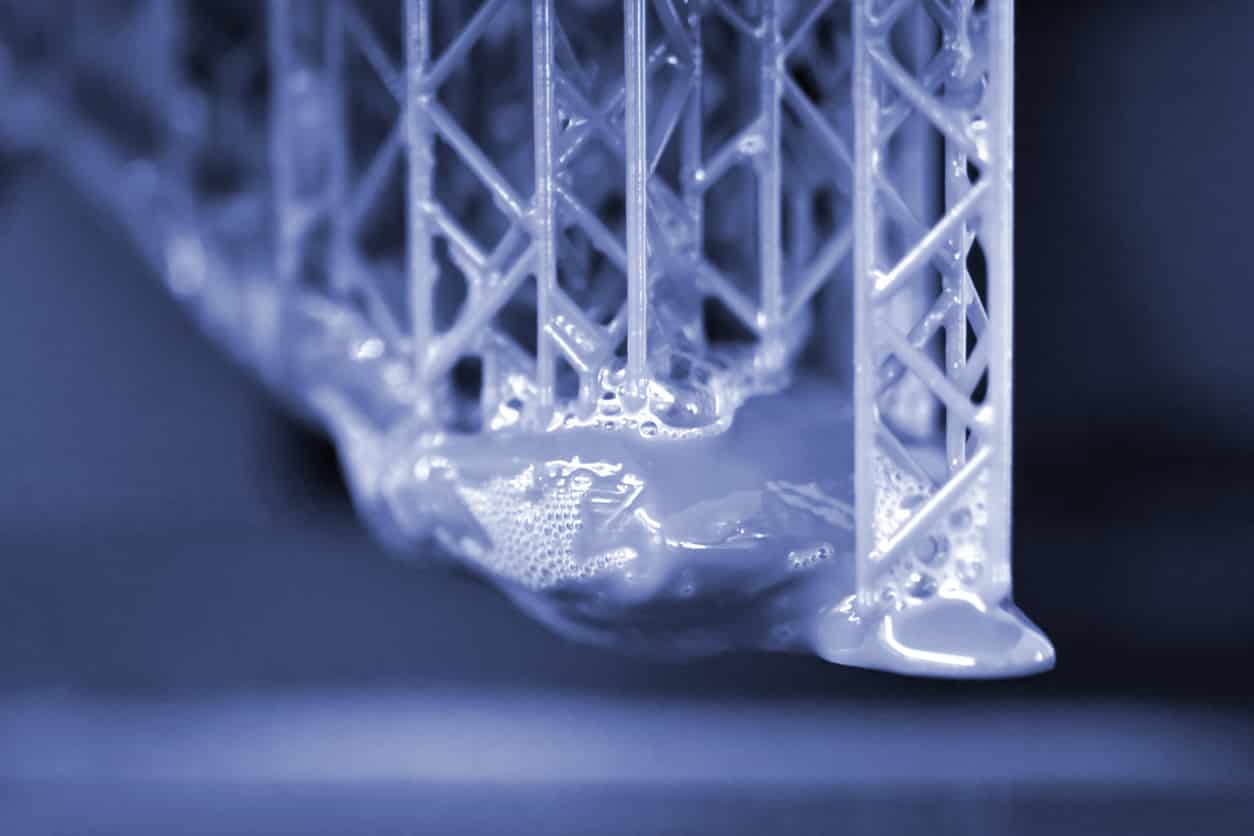
Get multiple quotes for your parts in seconds