Material Jetting
Discover how the manufacturing 3D Printing process Material Jetting, also known as MJ, NPJ, DOD, works.
Introduction to Material Jetting — MJ, NPJ, DOD
The Material Jetting 3D printing manufacturing technique is often similar to the standard 2D ink-jetting process. Utilizing photopolymers, metals, or wax that solidify when exposed to light or heat (in a similar fashion to stereolithography) ensures that physical objects are built up one layer at a time. The material jetting manufacturing process allows different materials to be 3D printed within the same part.
Material jetting dispenses a photopolymer from hundreds of tiny nozzles in a printhead to build a part layer-by-layer. This allows material jetting operations to deposit build material in a rapid, line-wise fashion, similar to other pointwise deposition technologies that follow a path to complete the cross-sectional area of a layer, also called a slice. Machine deposits droplets to the build platform, then UV lights directly cure and solidify them. Material jetting processes require support, which is often 3D printed simultaneously during the build from a dissolvable material. During the post-processing step, manufacturers remove the support material.
Material Jetting: 3 subprocesses
Several techniques make up the material jetting term, the most popular being:
- Drop On Demand (DOD) DOD material jetting printers have two print jets: one to deposit the build material and another for dissolvable support material. Like all additive manufacturing machines, DoD 3D printers follow a predetermined path and deposit material in a pointwise fashion to build the cross-sectional area of a component. These machines also employ a fly cutter that skims the build area after each layer to ensure a perfectly flat surface before printing the next layer. DoD technology is typically an important element to produce waxlike patterns for lost wax casting/investment casting and mold making applications, making it an indirect 3D printing technique.
- PolyJet by Objet PolyJet 3D printing technology was first patented by the Objet company, now a Stratasys brand. Ultra-thin layers jet the photopolymer materials onto a build tray similar to inkjet document printing. Each photopolymer layer is cured by UV light immediately after being jetted. The repetition of jetting and curing steps, layer after layer, produces fully cured models that can be handled and used immediately. The gel-like support material, specially designed to support complex geometries, can easily be removed by hand or by water jetting.
- NanoParticle Jetting (NPJ) by XJet. This material jetting technology, patented by XJet, uses a liquid containing building nanoparticles or support nanoparticles that is loaded into the printer as a cartridge and jetted onto the build tray in extremely thin layers of droplets. High temperatures inside the building envelope cause the liquid to evaporate, leaving behind parts made from the building material. This technique is suitable for metals and ceramics.
Material jetting 3D printing technology is an excellent choice for realistic prototypes, providing an excellent level of detail, high accuracy, and smooth surface finish. Material jetting allows a designer to print a design in multiple colors and several materials in a single print. Separate STL files are necessary to export the model To designate a different material or color to particular areas of the part. When blending colors or material properties to create a digital material, the design must be exported as an OBJ or VRML file. These formats allow the designation of special properties (such as texture or full color) on a per-face per-vertex basis.
The main drawbacks to printing with material jetting technologies are the high cost, and UV-activated photopolymers lose mechanical properties over time and can become brittle.
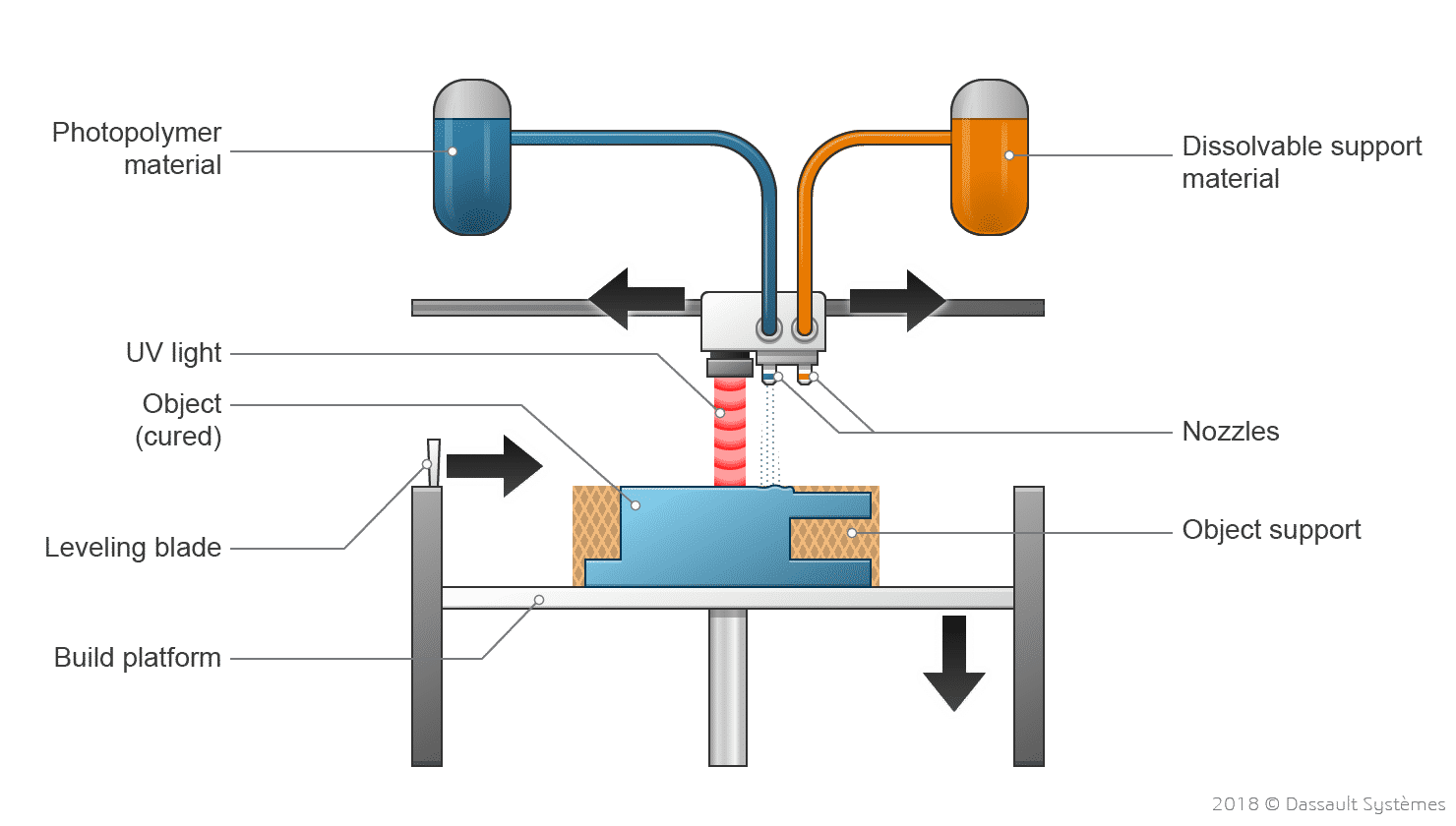
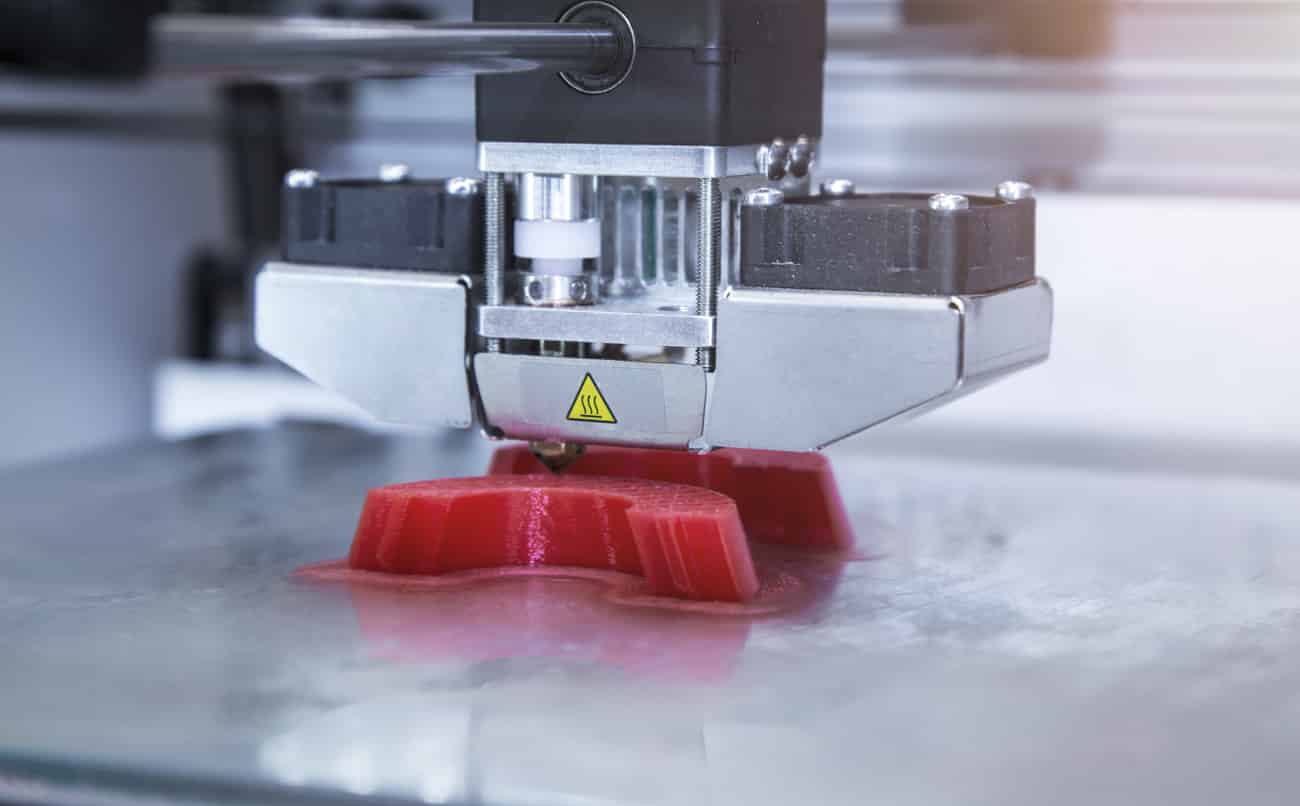
Get multiple quotes for your parts in seconds