Material Extrusion
Discover how Material Extrusion, a 3D Printing process, also known as FDM, works.
Introduction to Material Extrusion - FDM
Material Extrusion 3D printing technology uses a continuous filament of thermoplastic material as a base material. The filament is fed from a coil through a moving heated printer extruder head, abbreviated as an extruder. The molten material is forced out of the extruder’s nozzle and deposited first onto a 3D printing platform, heated for extra adhesion. Once the first layer is complete, the next step is to part away from the extruder and the platform, and then the following step is to deposit the second layer onto the growing workpiece directly. The extruder head moves thanks to computer control. At least three axes are required for the extruder to move in Cartesian architectures, but polar and delta systems are becoming increasingly popular. One layer is deposited on top of a previous layer until the object’s fabrication is complete.
Material extrusion is known as Fused Filament Fabrication (FFF) and is one of the most popular processes for hobbyist-grade 3D printing. Stratasys started to commercialize in 1990 the proprietary term Fused Deposition Modeling (FDM), created by S. Scott Crump in the late 1980s. With the expiration of this technology’s patent, there is now a large open-source development community called RepRap, as well as commercial and DIY variants, which utilize this type of 3D printing technology. This has led to a measurable price decrease. However, the material extrusion technique has dimensional accuracy limitations and is very anisotropic.
Material Extrusion and Materials
Extrusion could apply to a wide variety of materials, the most popular being thermoplastics, such as Acrylonitrile Butadiene Styrene (ABS), Polylactic Acid (PLA), High-Impact Polystyrene (HIPS), Thermoplastic PolyUrethane (TPU), aliphatic PolyAmides (PA, also known as Nylon), and more recently high-performance plastics such as PolyEther Ether Ketone PEEK or PolyEtherimide PEI. Additionally, 3D printing could extrude paste-like materials such as ceramics, concrete, and chocolate.
Composite fabrication became available as it became possible to equip a 3D printer with multiple extruders to speed up the fabrication process or open multi-material capabilities. Composite Filament Fabrication (CFF) is one of them. This term, created by the company Markforged and uses two print nozzles. One nozzle operates following the typical material extrusion process; it lays down a plastic filament that forms the outer shell and the internal matrix of the part. On every layer, the second nozzle deposits a continuous strand of composite fiber (made with carbon, fiberglass, or Kevlar). These continuous strands of composite fibers inside 3D printed parts add strength to the built object comparable to components made of metal. In addition to using composite materials for solid pieces, the strategy used to lay down layers can affect part strength. Markforged distinguishes two methods: isotropic fiberfill or concentric fiberfill.
Composites can be 3D printed with the material extrusion technique on machines equipped with only one extruder. The sole condition is that the base material (a thermoplastic) is present in sufficient quantities to guarantee a fusion between layers. Therefore, a mix of two materials within a single filament made wood 3D printing (wood particles embedded in PLA), metal 3D printing (metal particles embedded in thermoplastic), and even carbon 3D printing (carbon fibers embedded in thermoplastic) are possible.
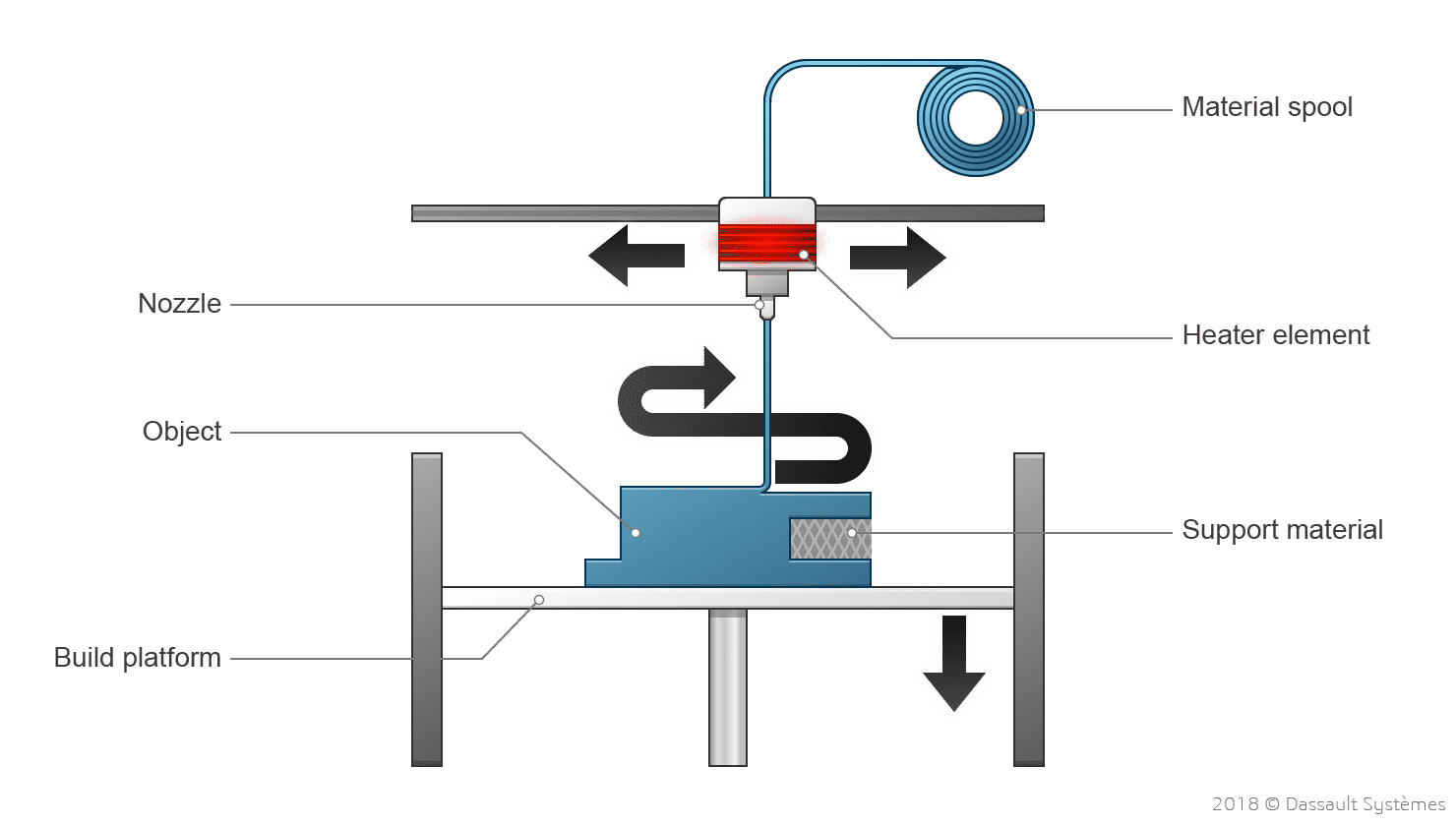
Discover how Material Extrusion works with Bombyx
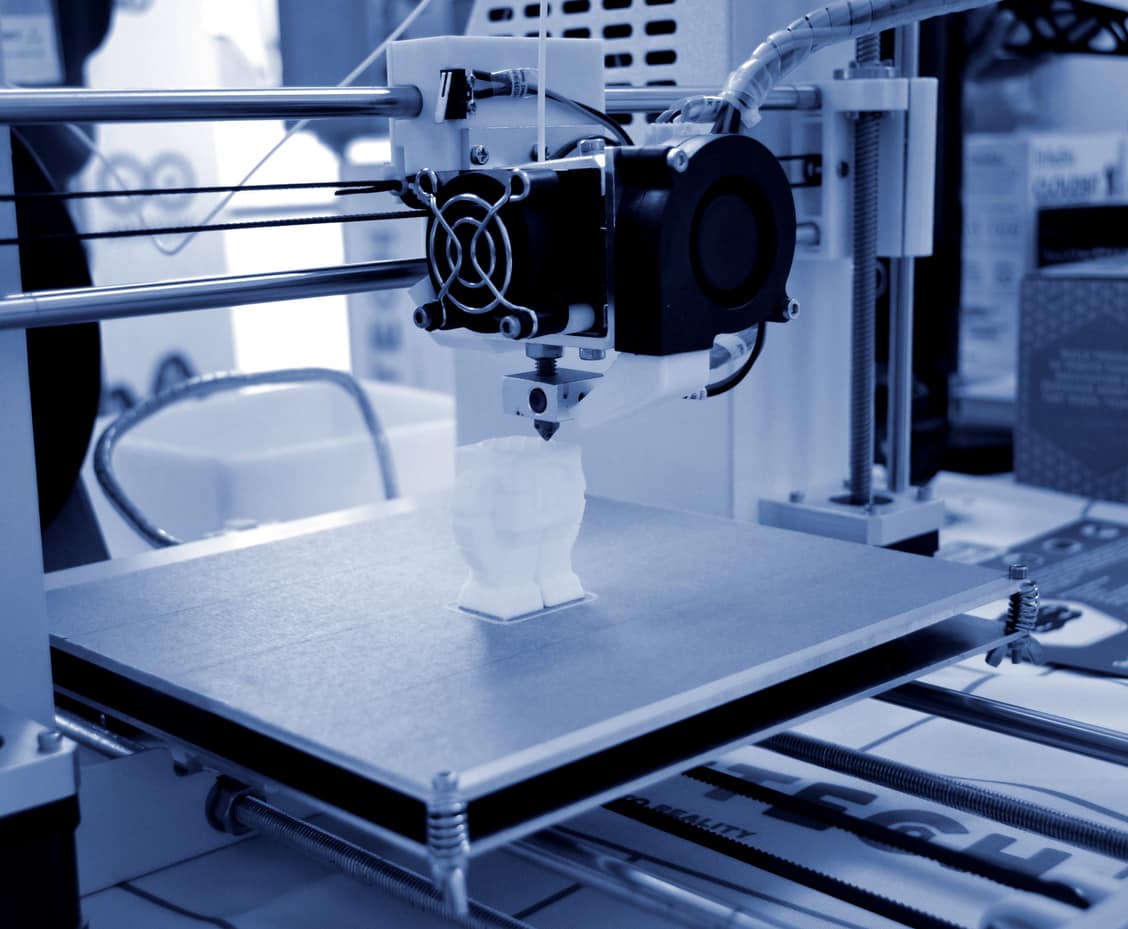
Get multiple quotes for your parts in seconds