Forging
Discover what is the manufacturing forming process Forging and its usage in the industry.
Discover 3DEXPERIENCE SOLIDWORKS for Makers
Introduction to forging
Forging is a manufacturing process that forms metal using compressive forces and a hammer, most often a power hammer or die. The hammer delivers what we called a “blow.” The forging process is classified according to a temperature such as cold, warm, or hot forging. When working at increased temperatures, metal is heated, usually in a forge.
Presses or hammers perform present-day industrial forging powered by compressed air, electricity, hydraulics, or steam. They’re not your ordinary hammer—featuring reciprocating weights in the thousands of pounds. In art smithies, smaller power hammers feature reciprocating weight of 500 lbs (230 kg) or less, while hydraulic presses are standard. Steam hammers have mostly become obsolete, although a minimal amount is still necessary, with the advancement of more convenient and powerful tools.
While today forging is a major worldwide industry, it is one of the oldest known metalworking processes performed by smiths throughout the millennia. Traditionally, forging was the preferred process for hand tools, jewelry, kitchenware, hardware, and edged weapons. Since the Industrial Revolution, the forging process is wherever a part requires strength, usually machining into a finished part. Although forged parts are generally more robust than their equivalent cast or machined parts, significant expenditure capital is necessary for furnaces, machinery, tooling, facilities, and personnel.
Temperature plays a crucial role in forging, even if the above processes can be performed at various temperatures. They are classified either as above or below the recrystallization temperature and in one of three categories: hot, warm, or cold. Hot forging is faster and more precise, while cold forging usually results in work hardening of the piece.
Three main classes of forging process
There are three main classes of forging processes:
- Drawn out means the length increases, and the cross-section decreases.
- Upset means that the length decreases and the cross-section increases.
- Squeezed in closed compression dies, meaning that multidirectional flow is produced.
Discover all forging subprocesses
Automatic hot forging, cogging, impression die forging, open die forging, press forging, roll forging, swaging, and upsetting are the most common forging processes.
- Automatic hot forging involves feeding mill-length steel bars (typically 7 m [23 ft] long) into one end of the machine at room temperature, and hot forged products emerge from the other end.
- Cogging is the successive deformation of a bar along its length using an open-die drop-forge. The common application is to work a piece of raw material to the desired thickness.
- Open die and impression die (also called closed die) forging are drop forging processes, meaning there is a need of a raised hammer then “dropped” onto the workpiece to deform it according to the shape of the die. As their names imply, the difference between the two depends on the shape of the die, with open die not fully enclosing the workpiece and closed die enclosing it.
- Unlike the nearly immediate impact of drop hammer forging, press forging involves a slow application of continuous pressure or force. Press forging can be either hot or cold. The amount of time that the dies are in contact with the workpiece is measured in seconds in contrast to milliseconds with drop hammer forging.
- Roll forging is a forging process where there is a reduction of round or flat bar stock in thickness and an increase long.
- Swaging a forging process in which the operator alter the dimensions of a workpiece thanks to dies into which the workpiece is forced. Usually considered a cold working process, swaging may also be hot worked.
- Upsetting also called upset forging, increases the diameter of the workpiece by compressing its length. It is the most widely practiced forging process based on the number of pieces produced. Engine valves, couplings, bolts, screws, and other fasteners are some examples of common parts made using the upset forging process.
Get multiple quotes for your parts in seconds
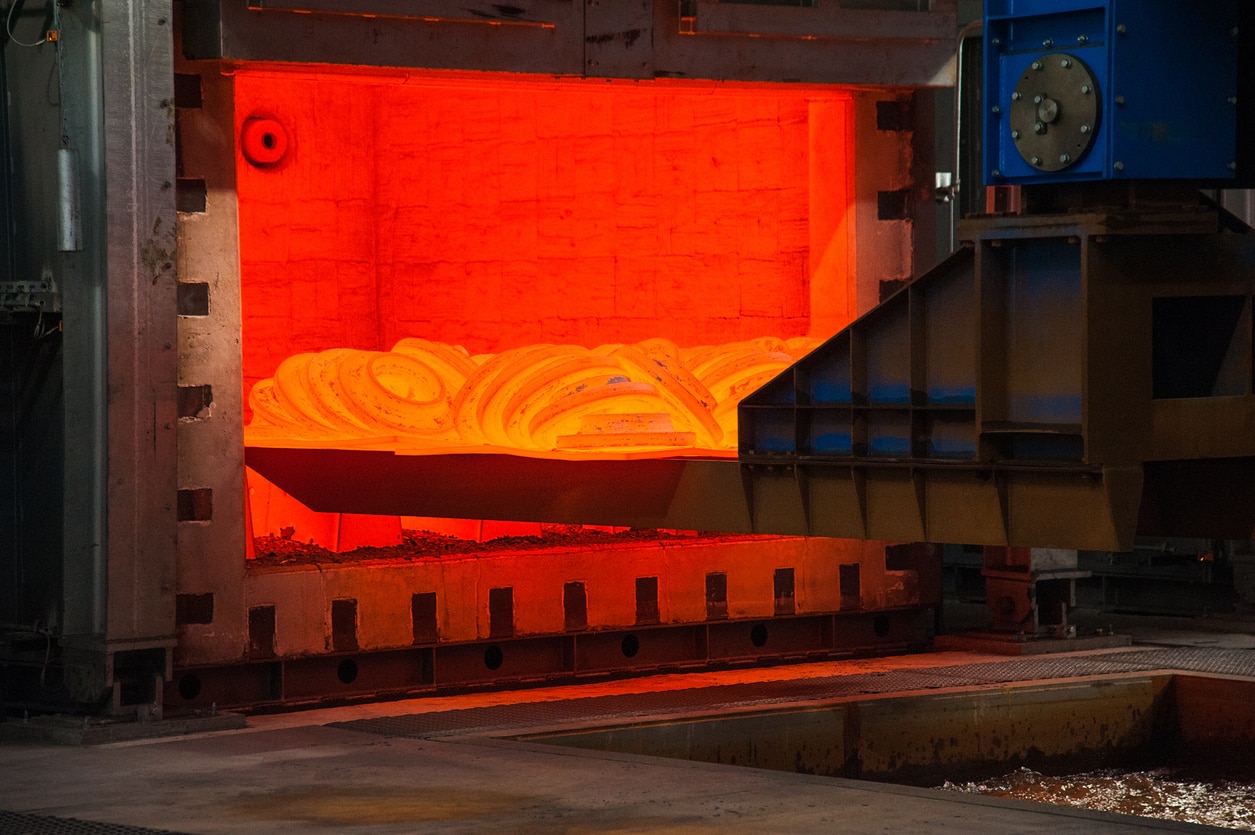