DLS 3D Printing by Carbon
DLS 3D printing is a groundbreaking additive technology that is enabling new part designs previously thought impossible by product engineers.
Introduction to DLS 3D Printing
Parts manufactured with DLS 3D printing utilize a groundbreaking process known as CLIP. At first glance, the process may seem similar to traditional photopolymer 3D printing such as SLA, but DLS is unique and more complex resulting in game-changing high-quality parts.
This greater complexity of DLS 3D printing enables the utilization of a wider variety of engineered materials. Moreover, all DLS parts are isotropic. As a result, cost-effective applications using advanced materials are now possible thanks to this new additive technology.
What is DLS 3D Printing?
DLS 3D printing—commonly called Carbon DLS—stands for digital light synthesis (DLS). DLS 3D printing is a type of additive manufacturing that utilizes light to map the printed parts, which subsequently complete a curing process using heat to achieve the intended material properties. DLS 3D printing is notable for its ability to balance design flexibility and speed of production with desirable plastic material properties that are not obtainable with other types of 3D printing.
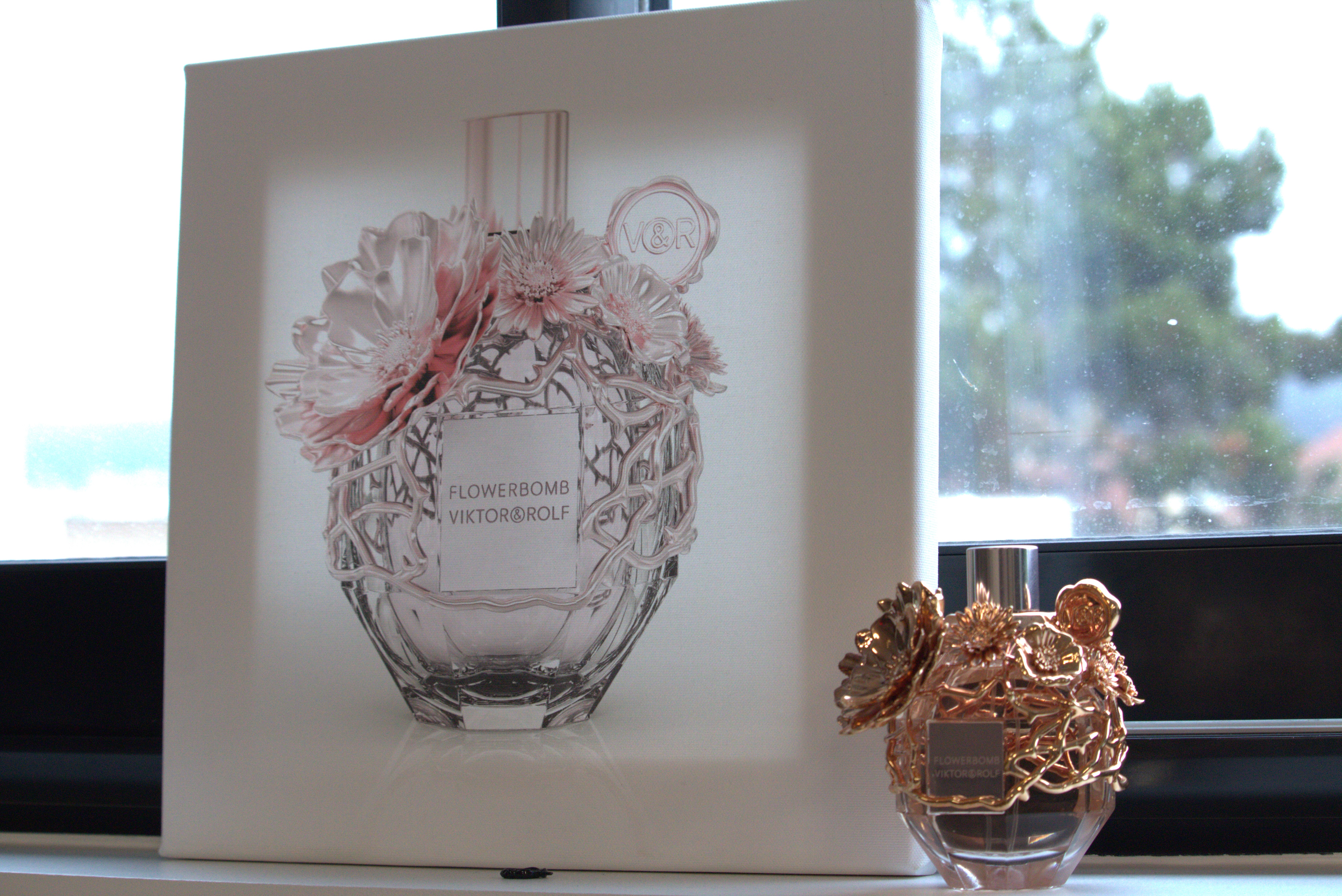
How DLS 3D Printing Works: Understanding CLIP
DLS 3D printing utilizes a UV laser projection to cure liquid plastic resins into solid parts. In DLS 3D printing, a laser at the bottom is projected into a resin reservoir by passing through an oxygen-permeable window. UV images are projected on the resin in layers and the part takes on a solid form as the build platform rises. The technical term for this process is continuous liquid interface production (CLIP):
- Step 1 — A dead zone is created by placing a layer of liquid resin between the print and the oxygen-permeable window.
- Step 2—Light passing through the dead zone cures the resin above it but does not cure the part onto the window itself. As the name continuous liquid interface implies, the continuous flow of uncured resin below the cured resin continues as the printing process moves towards completion. It's worth noting that Step 2 is what makes DLS 3D printing distinct from other types of Vat polymerization processes.
- Step 3—Once printing is completed, the part is heated in an oven. Baking triggers a chemical reaction in the resin, enhancing the part's mechanical properties.
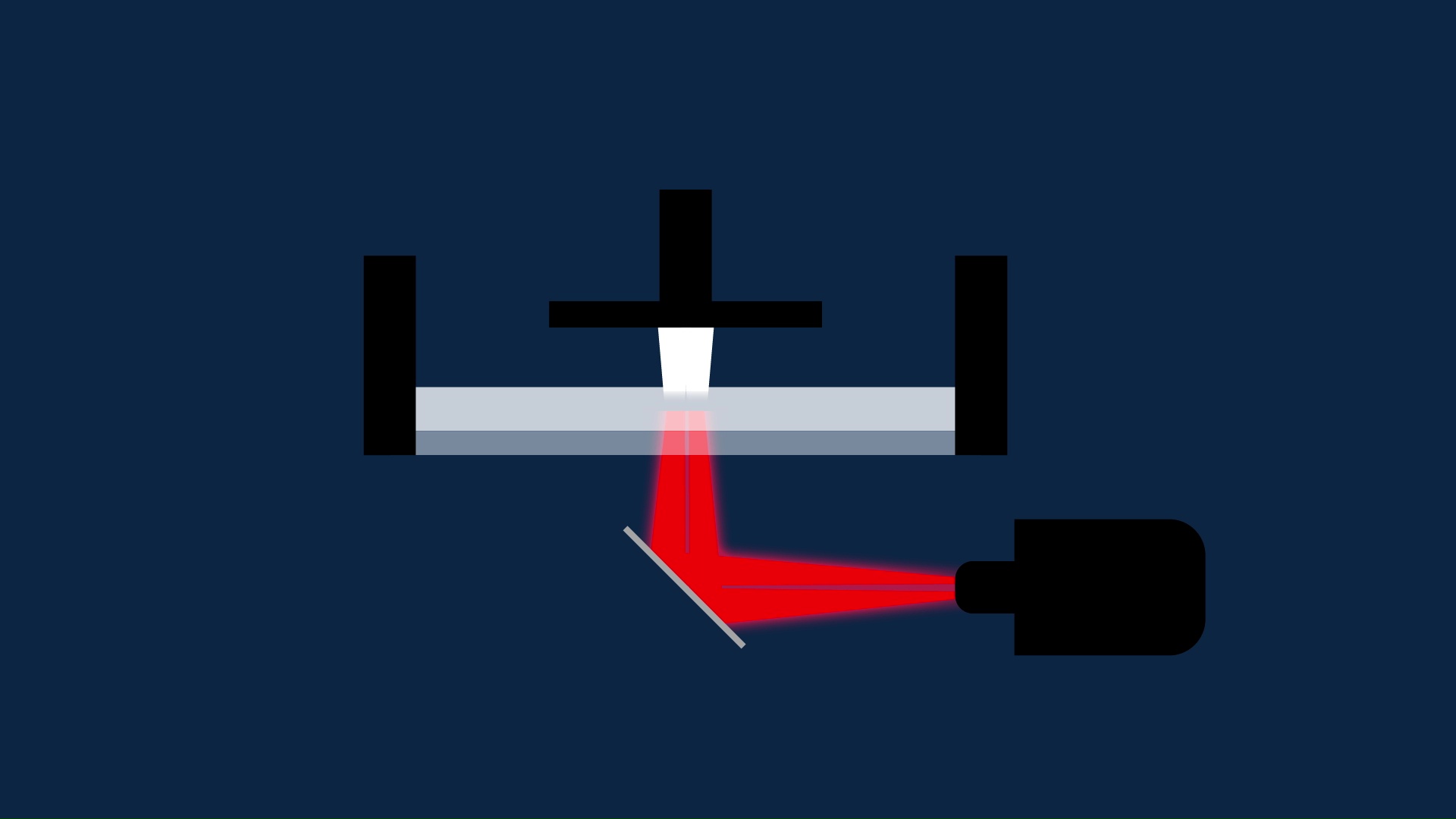
The Materials and Applications of DLS 3D Printing
DLS UMA 90
UMA 90 is a multi-purpose photopolymer that has similar degrees of rigidity as SLA resins. As such, UMA 90 is great for manufacturing fixtures and jigs. Moreover, these parts can be manufactured in a wide range of colors, which is great for making prototypes with specific aesthetic requirements.
DLS Epoxy—EPX 82
EPX 82 is an epoxy-based photopolymer providing fantastic durability and strength. In fact, the strength of EPX 82 is similar to glass-filled thermoplastics. For these reasons, EPX 82 can be used to make connectors and brackets.
DLS Cyanate Ester — CE 221
CE 221 is one of the more complex resins used in DLS 3D printing. It provides extremely high chemical and temperature resistance. As a result of this high resistance, CE 221 is great for parts exposed to corrosive fluids at high pressures and temperatures, such as fluid manifolds and compressor screws.
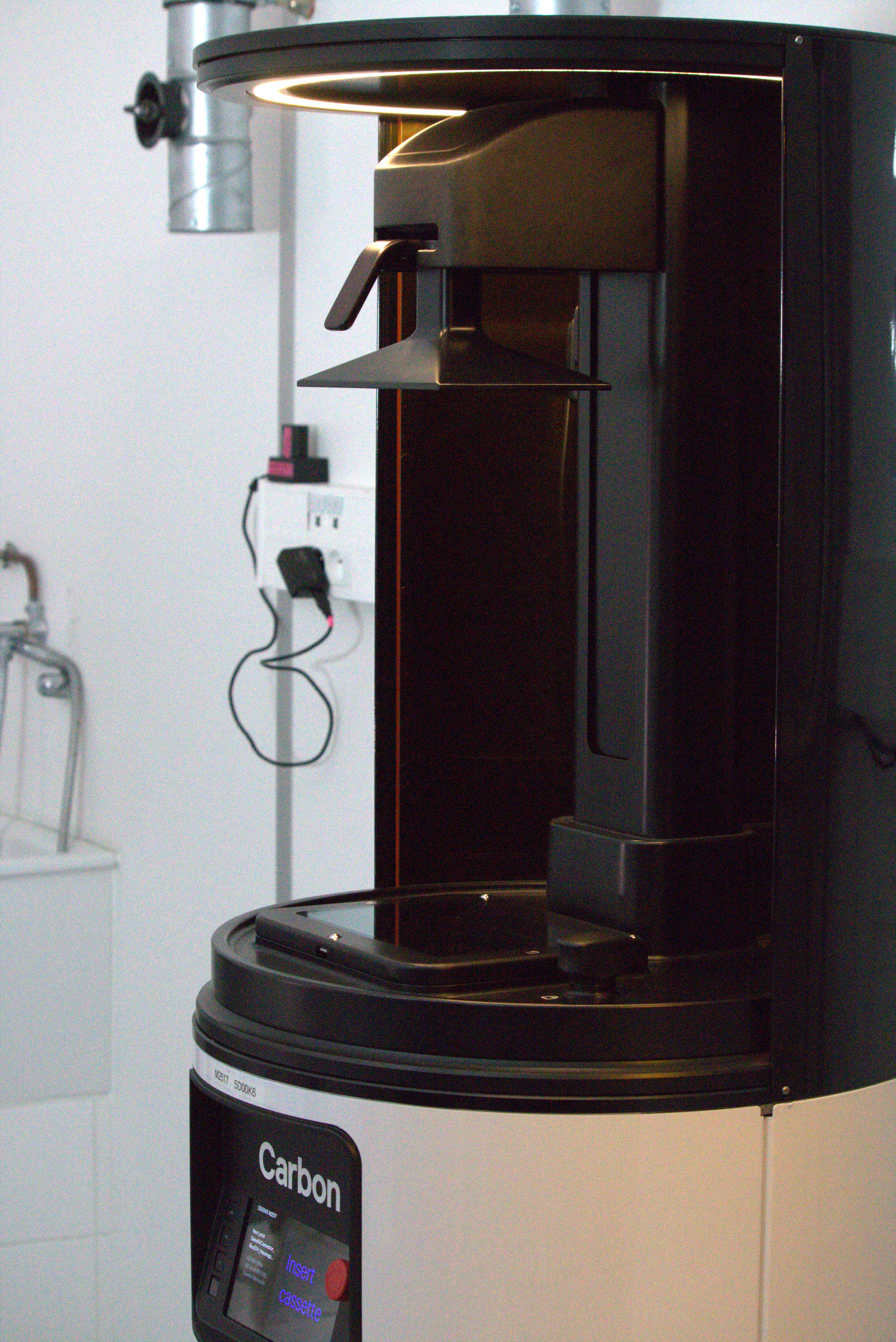
DLS Rigid Polyurethane—RPU 70
As its name implies, RPU 70 is rigid and offers general thermoset plastic benefits, including durability, impact resistance, and heat resistance. RPU is commonly used for equipment housings and push-in rivets.
DLS Flexible Polyurethane—FPU 50
FPU 50 is notable for its flexibility, as well as superior impact and abrasion resistance. FPU 50 is a great option for parts that endure lots of loading and unloading, such as living hinges or friction fits.
DLS Elastomeric Polyurethane—EPU 40
EPU 40 is extremely elastic, making it similar to conventional casting thermosetting elastomers. This resin offers amazing energy-return properties and is superior when it comes to elongation and tear strength. For these reasons, EPU 40 is ideal for sealing applications and vibration isolation requirements.
DLS Silicone—SIL 30
SIL 30 offers a low degree of hardness and high tear resistance. Additionally, SIL 30 is a biocompatible resin. SIL 30 is great for consumer products such as headphones, wearables, and other products that make contact with human skin.
The Future of DLS 3D Printing
The future is indeed very bright for DLS 3D printing technology. DLS 3D printing is excellent for both high-volume production and the creation of functioning prototypes. These prints are useful in a wide range of industries including automotive and consumer products. Plus, DLS 3D printing is poised to unlock previously unopened doors in manufacturing thanks to its ability to test dozens of product designs in the time it usually takes to produce one using other manufacturing methods.
The future of DLS 3D printing is truly as big as you can dream. Previously unheard-of geometries on part designs are now possible as the technology of DLS 3D printing continues to evolve. This is because moldability restrictions present with other additive technologies are lifted thanks to DLS. This means you can benefit from the freedom of easily using undercuts and straight walls without having to sacrifice manufacturability. Moreover, in addition to being able to make parts of the highest quality, DLS 3D printing provides a speed of manufacturing that has no equal in additive technology.
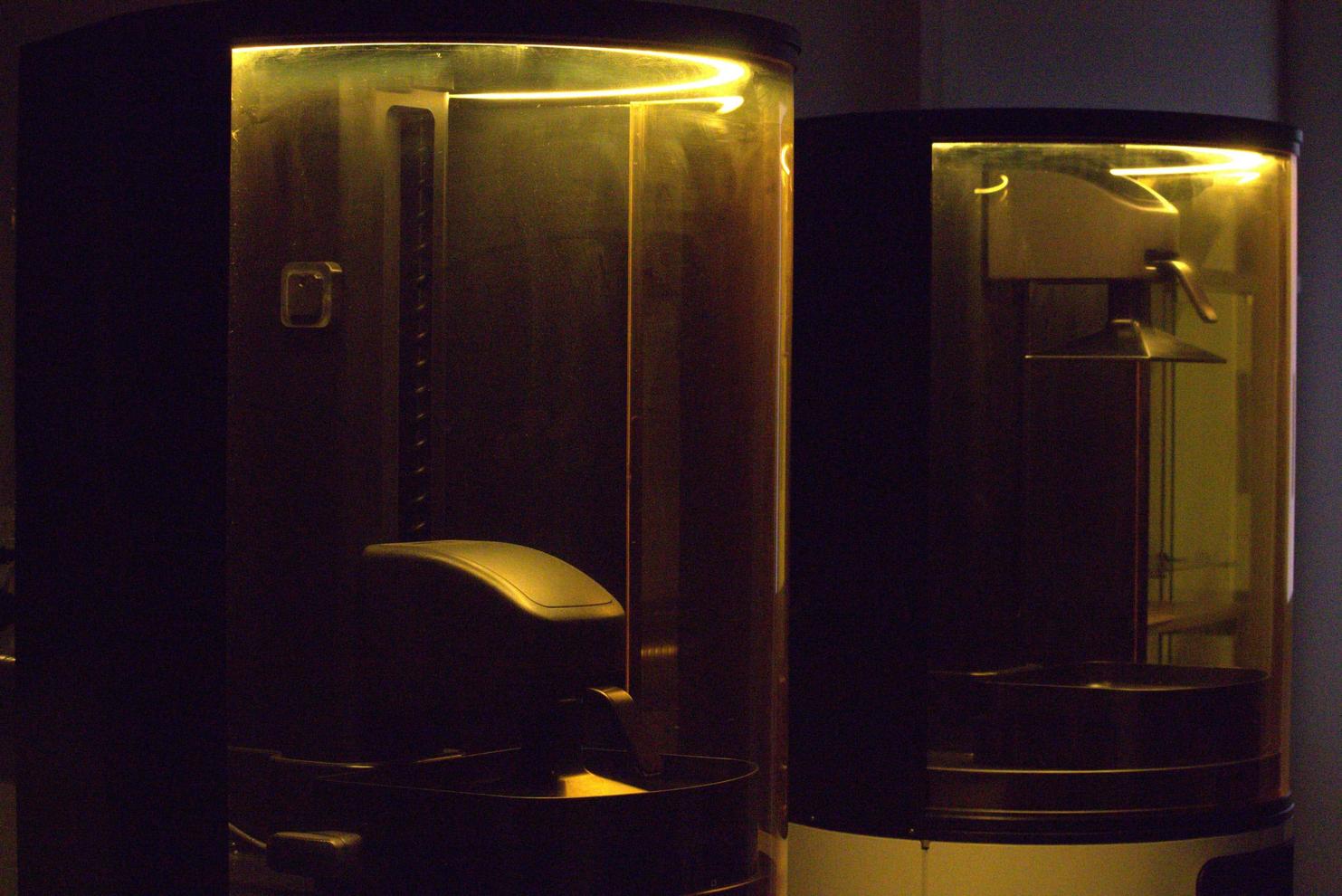
Get multiple quotes for your parts in seconds