Directed Energy Deposition
Discover how the manufacturing 3D Printing process Directed Energy Deposition, also known as DED, LENS, EBAM, works.
Directed Energy Deposition
The Directed Energy Deposition (DED) 3D printing technology, also known as Direct Energy Deposition, creates parts by directly melting materials and deposing them on the workpiece, layer by layer. This additive manufacturing technique is an essential element with metal powders or wire source materials. Other popular terms for DED include laser engineered net shaping, directed light fabrication, direct metal deposition, Laser Deposition Welding (LDW), and 3D laser cladding. Besides the capability to build parts from scratch (often with the hybridization of a mill/turn CNC tool), DED can also fix complex damaged parts, such as turbine blades or propellers.
Most DED 3D printers are industrial machines with very large footprints requiring a closed and controlled environment. Therefore, typical Directed Energy Deposition consists of a nozzle mounted on a multi-axis arm inside a closed frame, which deposits melted material onto the workpiece surface, where it solidifies. The process is similar in principle to the material extrusion 3D printing technique. Still, with DED, a nozzle can move in multiple directions, with up to five different axes compared to only three for most FFF machines.
The different technology of Direct Energy Deposition
The Direct Energy Deposition term can encompass several different technologies. They distinguish themselves by how the machine fuses the material, each suited for different and specific purposes. The most popular are as follows:
- LENS Technology by Optomec. LENS 3D manufacturing systems use lasers to build objects layer by layer directly from powdered metals, alloys, ceramics, or composites. The LENS process must take place in a hermetically sealed chamber filled with argon so that the oxygen and moisture levels stay very low. This keeps the part clean and prevents oxidation. The metal powder material is directly delivered to the material deposition head. Once a single layer has been deposited, the material deposition head moves on to the next layer. By building up successive layers, the machine is constructing the whole part. When complete, the component is removed and can be heat-treated, hot isostatic pressed, machined, or finished in any required fashion.
- Aerosol Jet Technology by Optomec. Optomec Aerosol Jet 3D printing technology provides a cost-effective, scalable process to print functional antennas and sensors directly onto consumer and industrial components, making them smart Internet of Things (IoT) devices. The possible printed antennas include LTE, NFC, GPS, Wifi, WLAN, and BT. This technique is closer to simple deposition techniques but suited for complex compound curved surfaces.
Aerosol Jet systems are ideally suited to develop, fabricate, enhance and repair high-performance electronic and biological devices for consumer electronics, semiconductor packaging, displays, aerospace/defense, automotive, and life sciences end-use products. Aerosol Jet technology can function with many materials, including conductive nanoparticle metal inks, dielectric pastes, semiconductors, and other functional materials. - Electron Beam Additive Manufacturing (EBAM) 3D Printing Technology by Sciaky. Electron Beam Additive Manufacturing (EBAM) is an additive manufacturing technology that produces large-scale metal structures. The Sciaky company’s proprietary Electron Beam (EB) gun deposits metal via a wire feedstock, layer by layer, until the part, reaches near-net shape and is ready for finish machining. Material deposition rates range from 3 to 9 kg of metal per hour. Compatible metals include titanium, tantalum, and nickel. Manufacturers can also use this DED technique to repair damaged parts.
- Laser Deposition Welding (LDW) and Hybrid Manufacturing by DMG MORI. The Laser Deposition Welding (LDW) additive manufacturing process uses the metal deposition by powder nozzle, which can be up to 10 times faster than PBF technology. Furthermore, the DMG MORI company has integrated its LDW additive manufacturing technology into a 5-axis milling machine. This innovative hybrid solution combines the flexibility of the laser metal deposition process with the precision of the cutting process and thereby allows additive manufacturing in milling quality. This combination renders the manufacturing of high-precision metal parts for various sizes possible.
Metals can be 3D printed through the DED additive manufacturing technique and notably include aluminum, copper, titanium, stainless steel, tool steel, copper, nickel alloys, and several steel alloys. Each sub-technique of the Directed Energy Deposition section has its own limitations and compatibility.
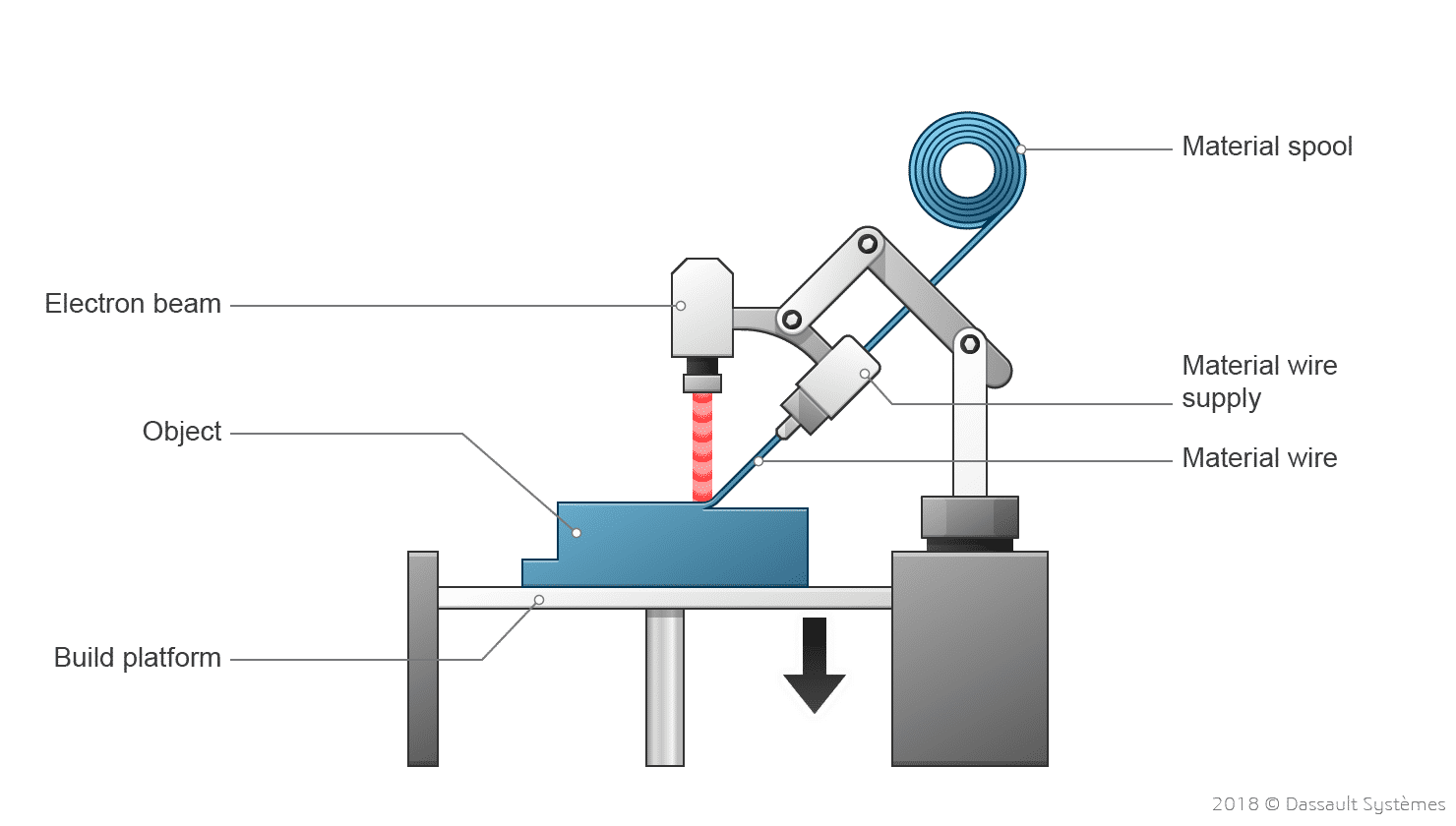
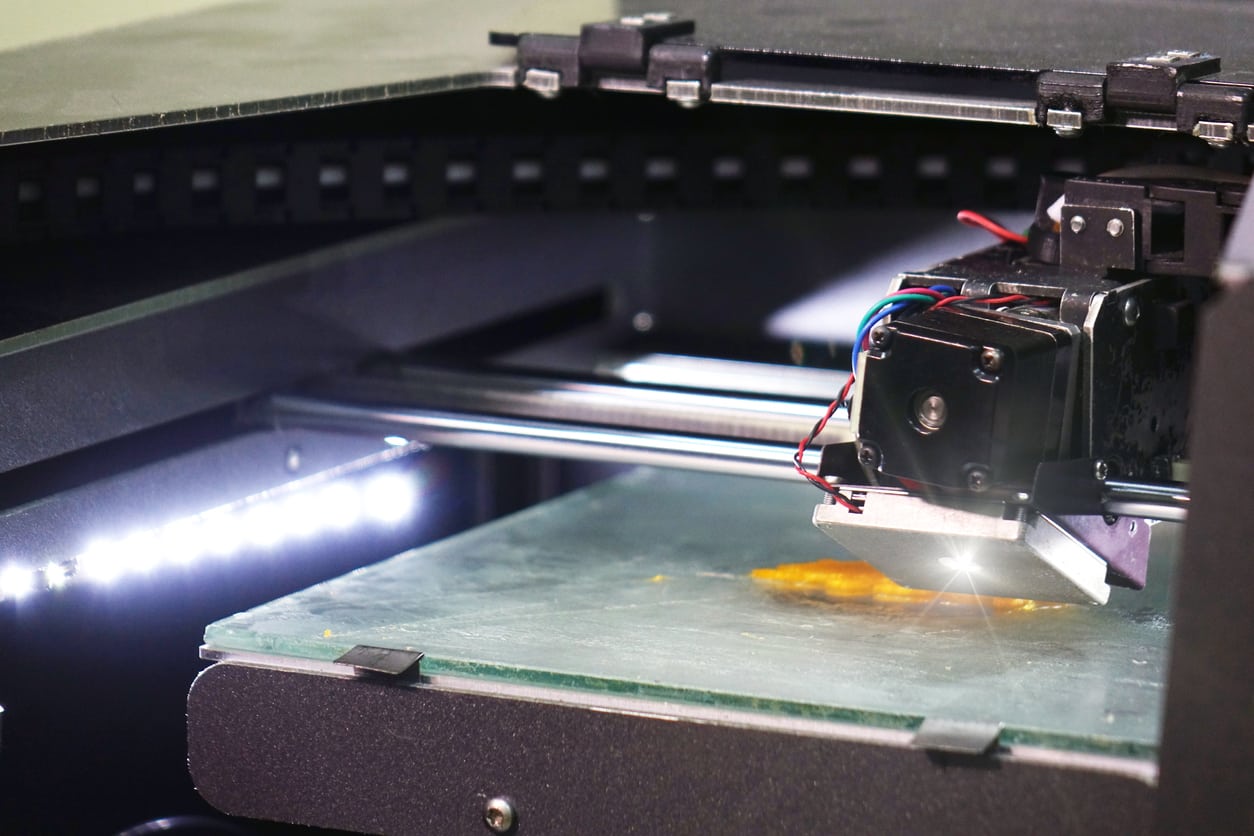
Get multiple quotes for your parts in seconds