Dip molding
Discover what is the manufacturing process Dip Molding and its usage in the industry.
Introduction to Dip Molding
As its name implies, dip molding is a plastic manufacturing process that takes heated metal molds and dips them into a PVC liquid called plastisol to form a plastic part. The liquid can either be heated or at room temperature. The part is then cooled, drained, hardened, and stripped from its mold to produce the finished product. The molds can go underwater multiple times to achieve the desired thickness. For certain materials, a curing process may be necessary.
Dip molding can produce parts at a fraction of injection molding cost and at an accelerated pace. It is suitable for short runs of prototypes as well as for high-production orders. Plastisol is an affordable material and is available in a broad range of custom and standard colors. It is also flame retardant, UV and mildew resistant, and relatively resistant to scratching and abrasion. Besides plastisol, dip molding materials include latex, ieneoprene, polyurethanes, silicones, and epoxy. The main drawbacks include the time required to produce a part and the difficulty of controlling the thickness.
The range of possibilities with dip molding is vast. However, some typical applications for dip molding include caps and plugs, gasoline nozzle covers, gloves, protective ax covers, socket holders, and many more.
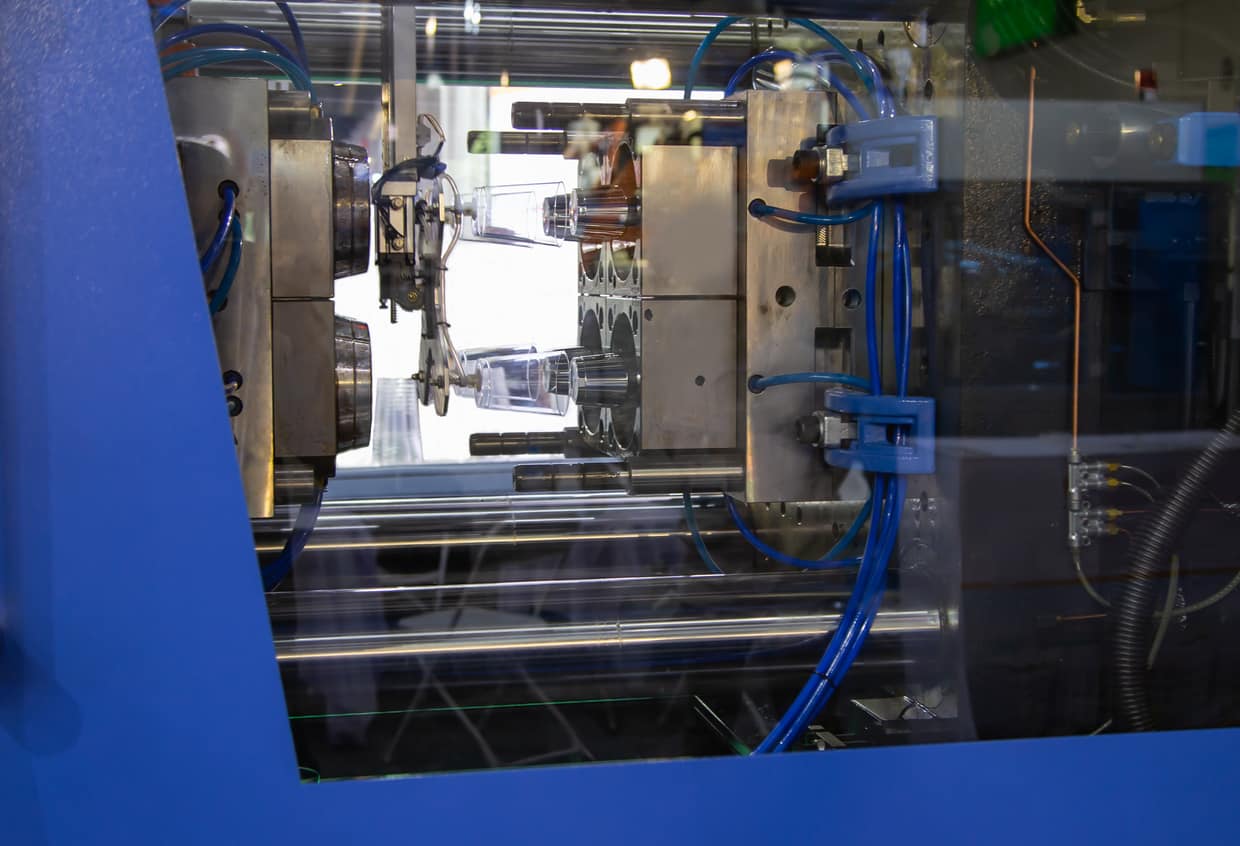
Get multiple quotes for your parts in seconds