Composite
Discover what is Composite, a manufacturing material, and its usage in the industry.
Introduction to Composite
Composite materials are a better choice than some traditional materials for strong, lightweight, and more affordable properties. Composite is a material created with two or more constituent materials. They exhibit very different physical and chemical properties. When combined, they deliver characteristics that are different from each component.
Scientists classify the two constituent materials into two categories: the matrix (binder) and the reinforcement. A composite material requires both a matrix and a reinforcement. The matrix serves to support the reinforcement material by surrounding it to maintain its relative position. The reinforcement depends on its unique mechanical and physical properties to reinforce the matrix properties. This creates an enhanced synergy that would otherwise be nonexistent in the individual constituent materials. It also enables product designers to optimize the composite combination.
Fiber-reinforced composite materials have become prevalent in high-performance products for their lightweight, yet strong properties despite the generally high cost. They can withstand the stringent loading conditions in various items. Industry use them in aerospace components, boat and scull hulls, bicycle frames, or race car bodies. Fishing rods, storage tanks, swimming pool panels, and baseball bats could also contain them. The new Boeing 787 structure, which includes the wings and fuselage, largely comprises composites. Likewise, they are gaining popularity in the world of orthopedic surgery.
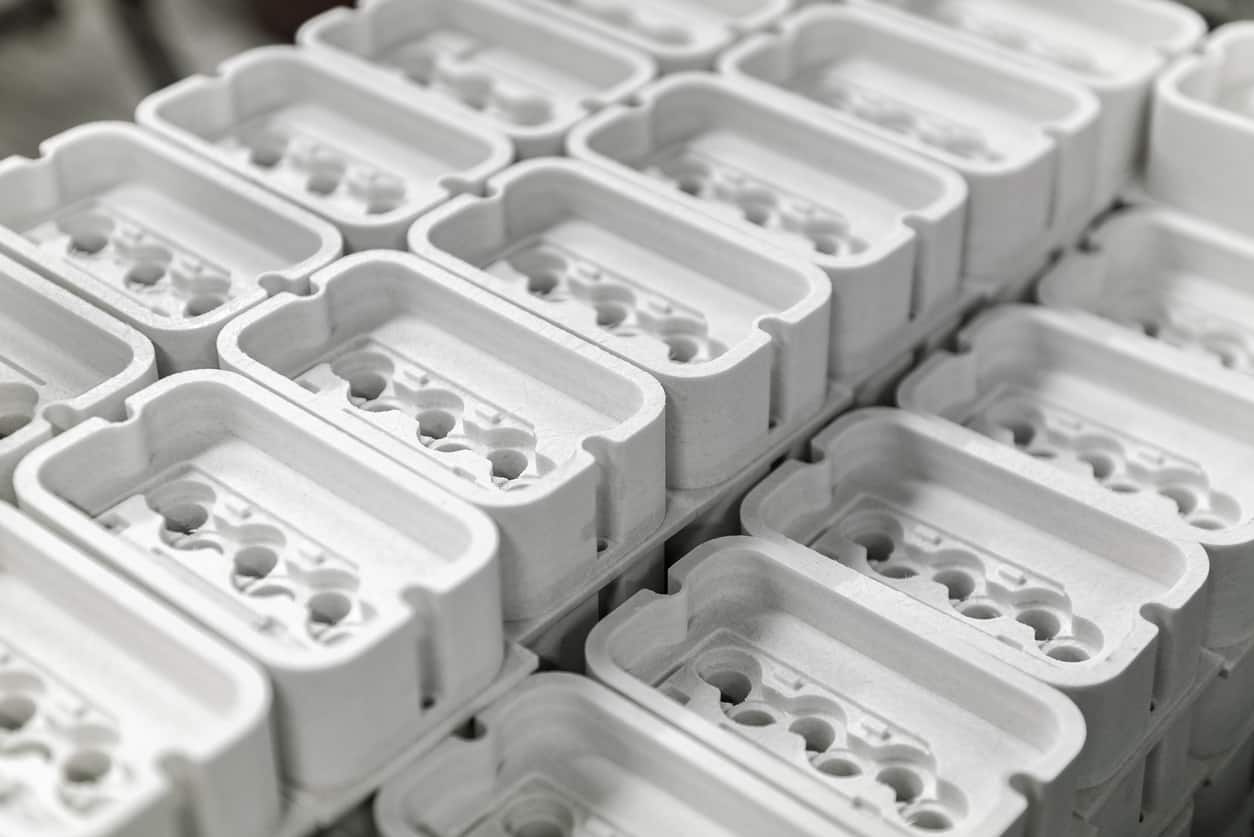
Generic Composite Materials
The most common artificial composite is concrete, typically composed of loose stones (aggregate) and bound with a matrix of cement.
Plywood
The term “plywood” has its roots in the thin layers known as “plies” of wood veneer glued together. Sheets of plywood are glued with their wood grains rotated up to 90 degrees to one another to achieve strengthening properties. We classify plywood as an engineered wood in the manufactured board family and includes Medium-Density Fiberboard (MDF) and particle board (chipboard). The two composite constituents of plywood are resin and wood fiber sheets comprised of long, robust, and thin cellulose cells.
Cross-graining, which alternates the grains, reduces the tendency of the wood to split upon nailing at the edges and reduces expansion and shrinkage to improve dimensional stability. It also delivers more consistent strength across all directions of a panel. In order to minimize warping, an odd number of plies is typically present to assist with balance. Cross-graining an odd number of composites also reinforces the strength of the wood so that bending it perpendicular to the grain direction of the surface ply becomes difficult.
Fiberglass
Fiberglass is a common type of fiber-reinforced plastic (FRP) reinforced with glass fiber. The glass fibers are embedded into the material by either arranging sporadically, compressing into a flat sheet, or interweaving into a fabric. The plastic matrix is either a thermoset polymer matrix (epoxy, polyester resin, or vinyl ester) or a thermoplastic. Fiberglass is a more cost-effective and flexible alternative than carbon fiber. Likewise, it is stronger than many metals and can be molded into complex shapes.
A broad spectrum of applications uses fiberglasses such as aircraft, automobiles, bathtubs and enclosures, boats, casts, cladding, external door skins, hot tubs, pipes, roofing, septic tanks, surfboards, swimming pools, and water tanks. Fiberglass is sometimes called Glass-Reinforced Plastic (GRP), Glass-Fiber Reinforced Plastic (GFRP), or GFK (from German: Glasfaserverstärkter Kunststoff). One important distinction to make is between glass fiber and fiber-reinforced plastic because sometimes the glass fibers themselves can be called “fiberglass.”
Carbon Fiber
Carbon fiber is an extremely strong and light fiber-reinforced plastic comprised of carbon fibers. While it tends to be costly, it’s generally applied to industries that require high strength-to-weight ratios and rigidity, such as aerospace, automotive, civil engineering, and sporting goods. Increasingly, their application is advancing in various consumer and technical applications. The binder in carbon fiber is generally a thermoset resin such as epoxy but can also be thermoplastic polymers such as polyester, vinyl ester, or nylon.
The composite can also contain other fibers such as aramid (Kevlar, Twaron), aluminum, ultra-high-molecular-weight polyethylene (UHMWPE), glass fibers, and carbon fiber. Carbon fiber is sometimes called graphite-reinforced polymer or graphite fiber-reinforced polymer. Other common names include Carbon Fiber Reinforced Plastic or Carbon Fiber Reinforced Thermoplastic (CFRP, CRP, CFRTP) or often called carbon fiber, carbon composite, or even carbon.
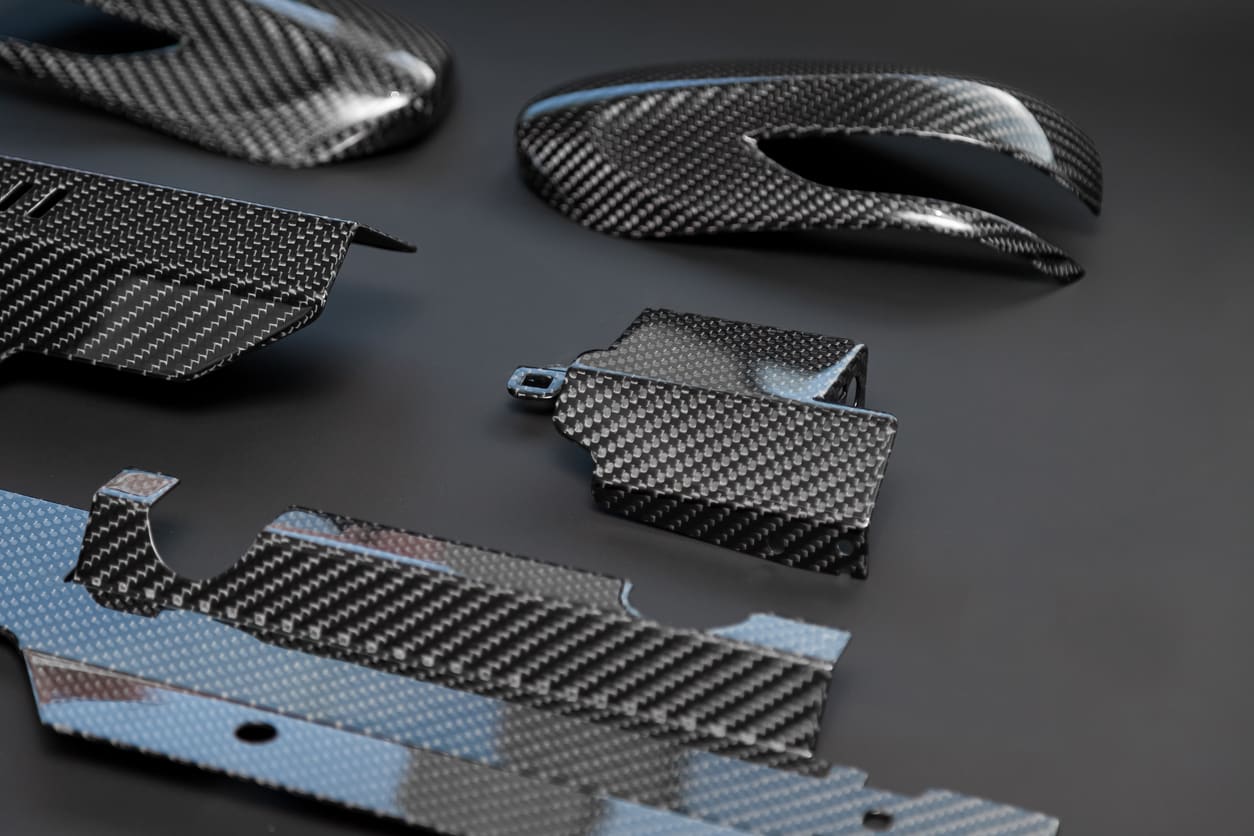
Composite materials for 3D printing processes
Some 3D printer manufacturers tend to develop composite materials with specific branding.
Alumide material is a blend of polyamide and a very low quantity of gray aluminum powder. Laser sintering is the technique used to create complex, concepts, functional, or series strong and relatively rigid models. Models made from Alumide can also absorb minor impacts and resist some pressure under bending conditions. It is ideal for novice designers seeking affordability, maximum design freedom, and greater printing capabilities. Additionally, it delivers greater stiffness than polyamide would by itself and features an aluminum appearance. The surface is slightly porous with a sandy, granular appearance and can be finished in its natural gray matte state or dyed with various colors.
Fiber-Reinforced Nylon makes it possible to 3D print engineering parts as strong as aluminum at the cost of plastic. It is specifically designed with the strength of aluminum and has a higher strength-to-weight ratio than 6061-T6 Aluminum while being up to 27 times stiffer and 24 times stronger than ABS. Fiber-Reinforced Nylon enables users to optimize their printed custom end-use production parts, particularly functional prototypes, tests, structural parts, jigs, fixtures, and tooling, while focusing on strength, stiffness, and weight and temperature resistance. It is not suitable for small parts with intricate designs.
Full-color sandstone produces photorealistic full-color models and sculptures and is particularly well suited for architectural models, lifelike sculptures, gifts and memorabilia, and fine arts. It is made essentially from gypsum and incorporates a colored texture on the surface. The material’s brittleness restricts its application as functional or intricately designed parts. This sandstone material is sometimes called multicolor.
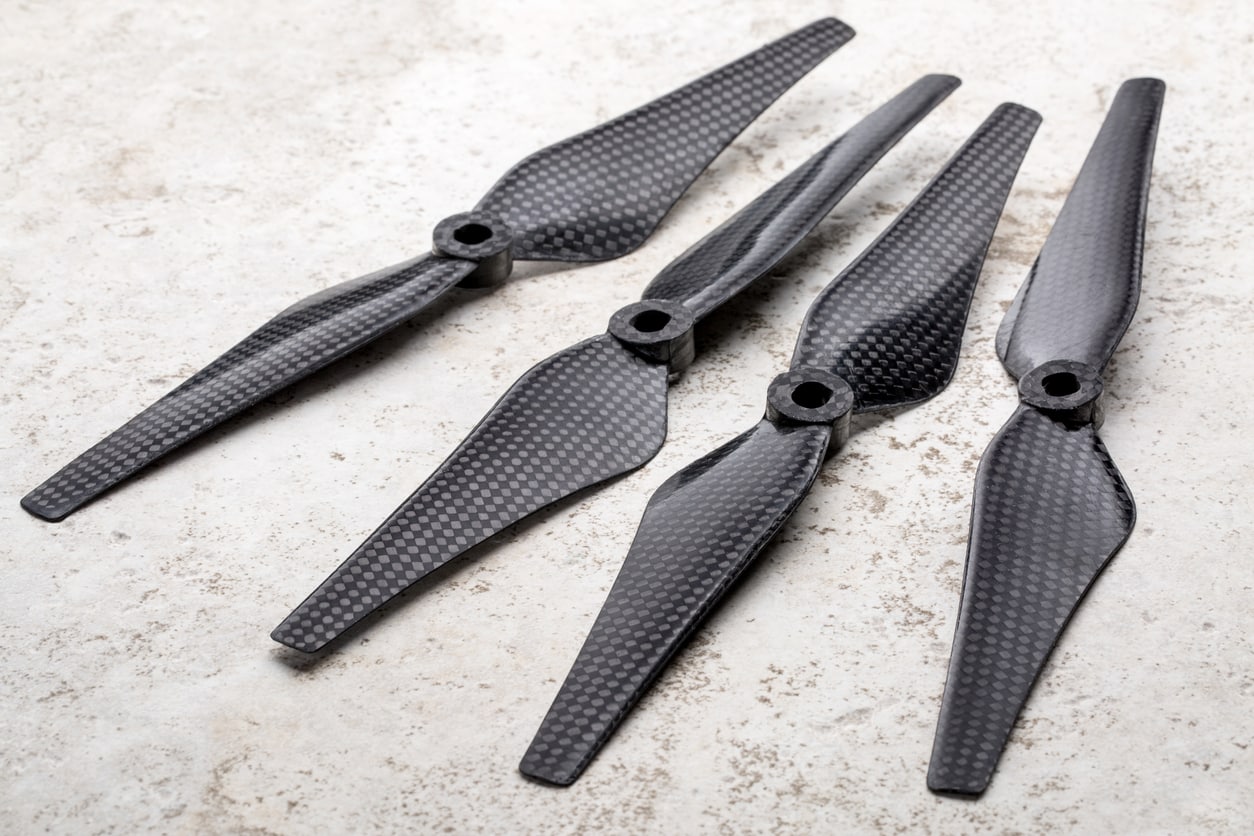
Get multiple quotes for your parts in seconds