Powder coating
Learn more about Powder coating, a finishing process, how do they work and what are the usages in the industry.
Introduction to Powder Coating
Powder coating uses a free-flowing, dry powder to coat workpieces. The most common usage of powder coating is for coating metals to create a harder, tougher finish than conventional paint. Some of the most common metals that undergo the powder coating process include household appliances, aluminum extrusions, drum hardware, automotive and bicycle parts.
Typically, thermoplastic or thermoset polymers are electrostatically applied and cured with heat, letting them flow and develop what’s known as a “skin.” Curing time is significantly faster than it is with a liquid coating. Unlike conventional liquid paint, powder coating can keep the binder and filler parts in a liquid suspension form without the need for a solvent. Thanks to technological advancements, a greater scope of materials, such as Medium-Density Fiberboard (MDF), can be applied as part of the powder coating process.
Powder coating can produce thicker coatings than conventional liquid coatings and, because of its powdered state, it is free from running and sagging. The absence of solvents means that powder coating releases little or no Volatile Organic Compounds (VOC) into the atmosphere, providing remarkable cost savings in pollution control equipment. Aesthetically, there are fewer differences between horizontally and vertically coated services when compared to liquid-coated items. Powder coating is also distinctly unique in that it facilitates many specialty effects.
The process is similar to the conventional liquid spraying method. It begins with preparing the workpiece and the equipment to be used. Before applying powder coating, the workpiece must be free from oil, dirt, lubrication greases, metal oxides, etc. Several possible application processes include an electrostatic gun, electrostatic fluidized bed, and electrostatic, magnetic brush powder coating. The final step of the process is the curing process.
The most common application process for metal objects involves spraying the powder with an electrostatic, or corona, gun. A wide variety of spray nozzles are available.
- Electrostatic spray guns also called liquid electrostatic sprays, pertain to the concepts of charge and electric fields. The finishing technique of applying a coating to a metal surface has origin of the law of attraction between positively and negatively charged particles. The paint becomes positively charged, while the painted support is wired to a negatively charged strong electric field.
- The electrostatic fluidized bed process is similar to the conventional fluidized bed dip process, except, in this process, the powder depth in the bed is shallower.
- Lastly, Electrostatic Magnetic Brush (EMB) uses a roller to apply the powder coating to flat materials, resulting in relatively high speeds and accurate desired thickness layers.
Curing thermoset powders involves exposing the workpiece to elevated temperatures for a set duration so that the powder melts, flows out, and chemically reacts to harden and dry. The process, known as crosslinking, requires exposure to elevated temperatures for a certain length of time to fulfill the desired properties.
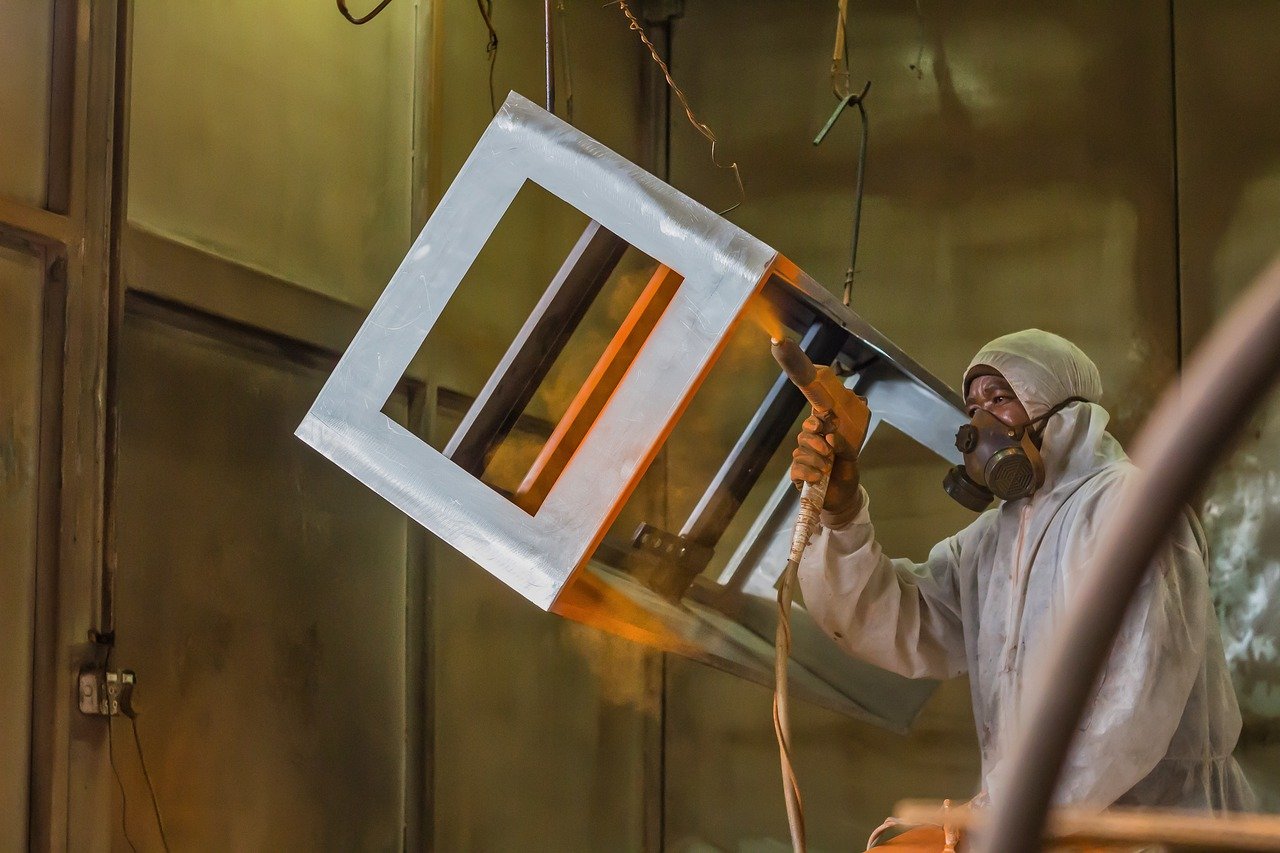
Get multiple quotes for your parts in seconds