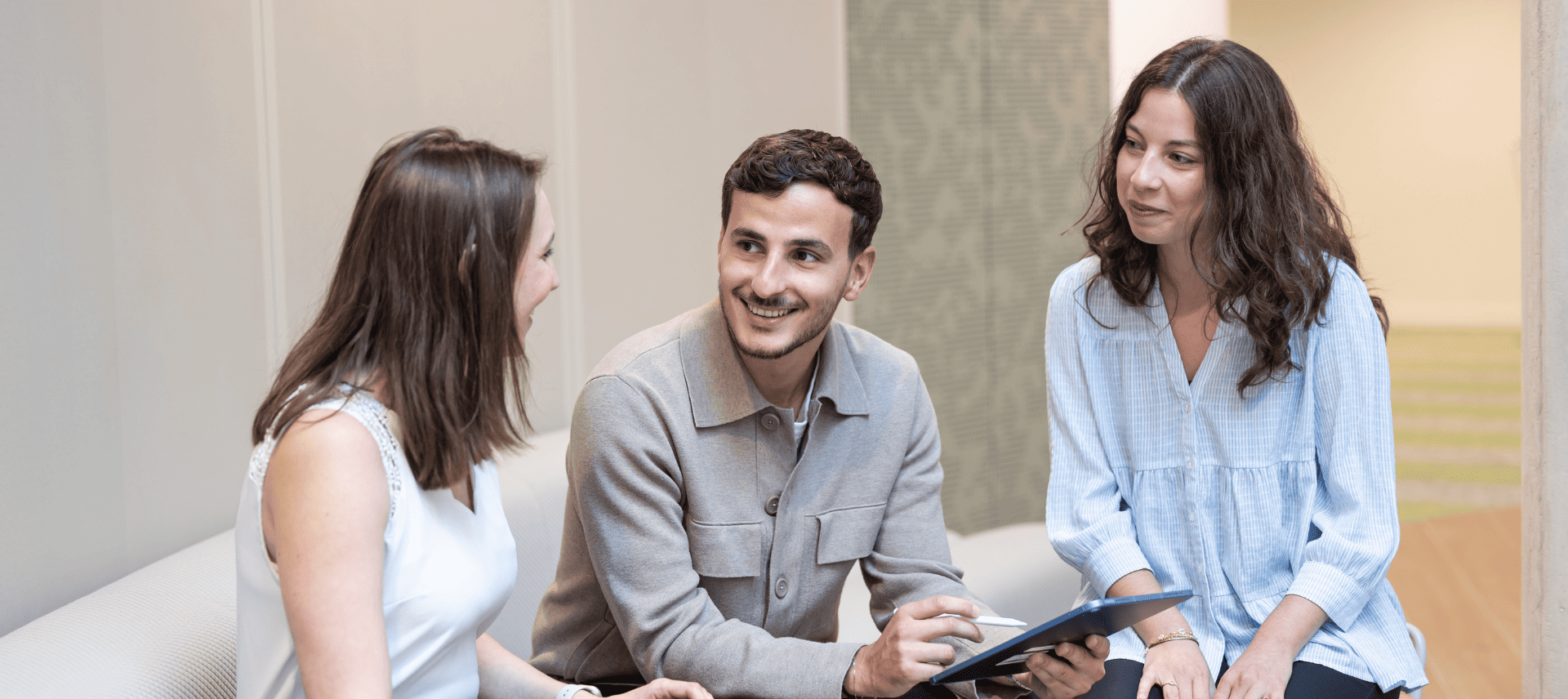
Be the Next Game Changer
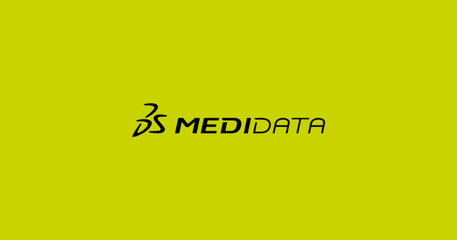
CAREERS - MARKETING & COMMUNICATIONS
Analyst Relations Senior Director (Remote)
United States, NY, New York
Regular
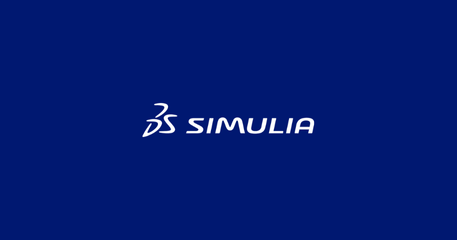
CAREERS - RESEARCH & DEVELOPMENT
Software Engineer – SIMULIA R&D (m/f/d)
Germany, Darmstadt
Regular
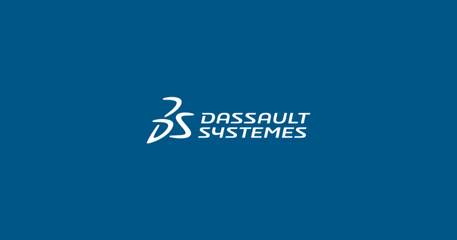
CAREERS - SALES
Sales Transaction Support Specialist
United Kingdom, Warwick
Regular
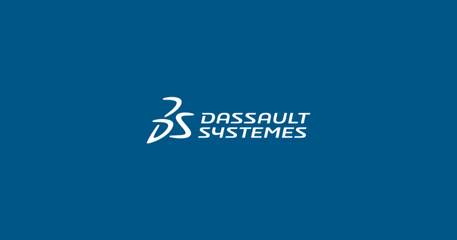
CAREERS - RESEARCH & DEVELOPMENT
Ingénieur de recherche en deep learning (F/H)
France, Vélizy-Villacoublay
Regular
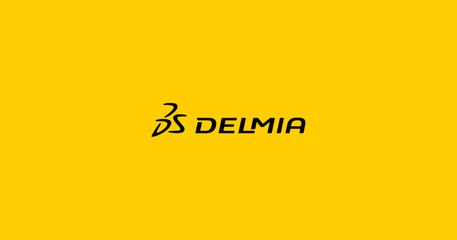
CAREERS - SALES
2025 DELMIA IPC Intern
Korea, Republic of, 11, Seoul
Internship
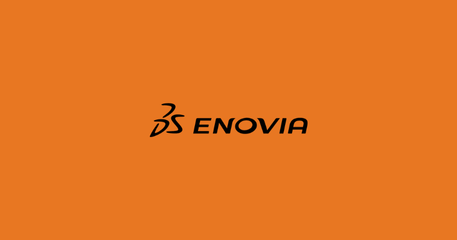
CAREERS - SALES
Cloud consultant (Database, Infrastructure)
Korea, Republic of, 11, Seoul
Regular
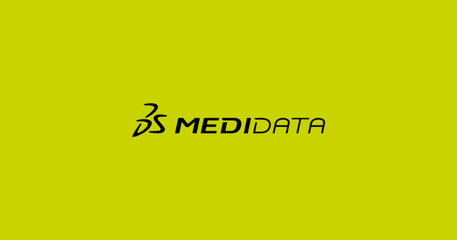
CAREERS - RESEARCH & DEVELOPMENT
Senior Instructional Designer (Learning Solutions Designer)
United States, NY, New York
Regular
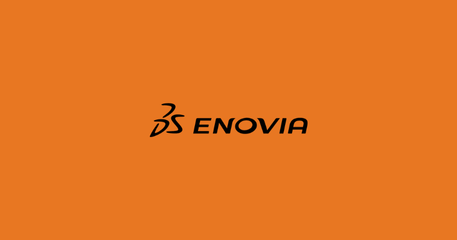
CAREERS - MARKETING & COMMUNICATIONS
INTERNSHIP – Advocacy Marketing Intern (PT Sept - Dec)
United States, MA, Waltham
Internship
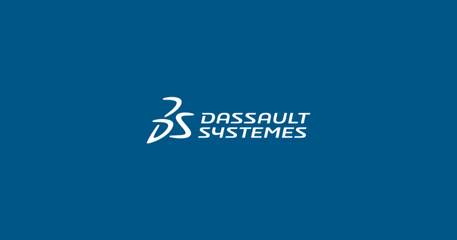
CAREERS - INFORMATION TECHNOLOGY
Senior Network Engineer
United States, MA, Waltham
Regular
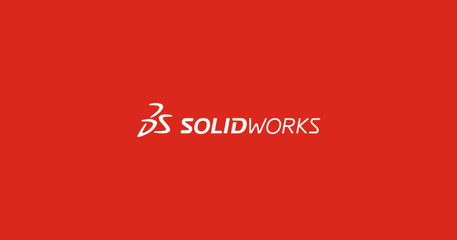
CAREERS - RESEARCH & DEVELOPMENT
SolidWorks Drawings AI Developer
United States, MA, Waltham
Regular
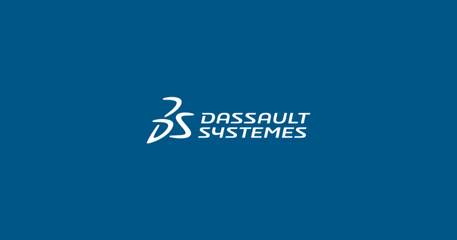
CAREERS - INFORMATION TECHNOLOGY
IT Service LAN Operations Engineer
India, MH, Pune
Regular
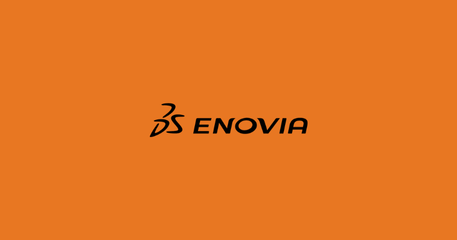
CAREERS - RESEARCH & DEVELOPMENT
JavaScript Developer - Pune
India, MH, Pune
Regular
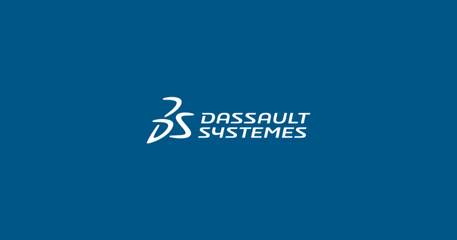
CAREERS - FINANCE
Tax Analyst
United States, MA, Waltham
Regular
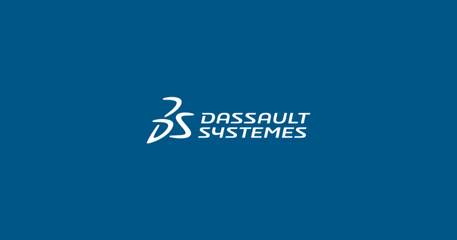
CAREERS - STRATEGY
Trainee Strategy & Market Expansion (m/f)
Switzerland, ZH, Kloten
Internship
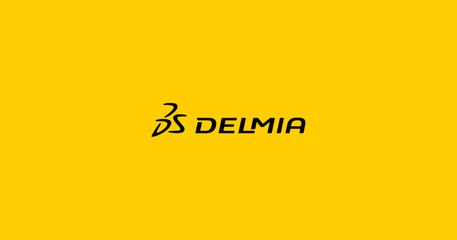
CAREERS - RESEARCH & DEVELOPMENT
DELMIA Robotics QA Engineer
India, KA, Bangalore
Regular
Your Recruitment Journey
We are looking forward to meeting you!

1. Online application

2. Recruiter interview

3. Manager interview
Depending on the role you are applying for:
English test / coding assessment / cognitive test