Green Steel: Can We Make Heavy Industry Have a Lighter Impact?
Steel is one of the most polluting industries in the world. With a combination of hydrogen-based manufacturing techniques and overall process optimizations, we can work to change that.
Steel is everywhere. It is used to build our houses and workplaces. It is in our personal devices and home appliances. It supports our public infrastructure, from the internet to energy grids. It is by far the most important single material in our lives.
Unfortunately, it is also one of the dirtiest. Steelmaking produces around 7% of total global GHG emissions and about 11% of total global CO2 emissions. Why is green steel important? Because it means tackling one of the greatest sources of global carbon emissions at the source.
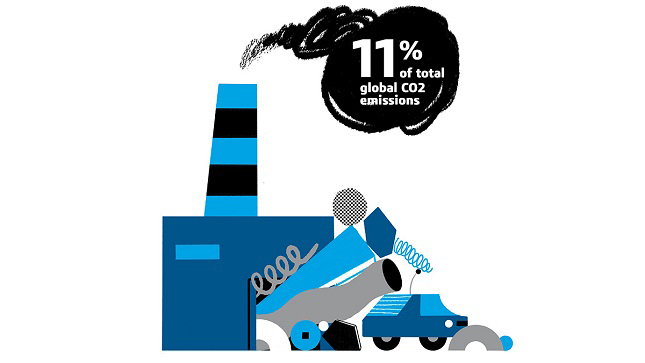
What Is Green Steel?
Green steel refers to steel production processes that use renewable energy sources and innovative technologies to minimize carbon emissions, making the steel industry more environmentally sustainable.
The Basics of Steel Production
The steelmaking process was first discovered around 4,000 years ago in what is today modern Turkey, and while the technology and our understanding of the underlying chemistry has changed greatly in that time, the basic principle remains the same.
The Role of Reduction Reactions
You begin with iron ore – a material rich in iron oxides. In order to extract the pure iron from these oxides, a material is needed that can react with the oxygen, pulling the oxygen out of the compound and leaving the pure iron behind. This is called a reduction reaction.
The material used in steel reduction is a product derived from coal called coke. When it is introduced to the iron oxide inside a blast furnace, the oxygen in the iron ore bonds with the carbon coke to form carbon dioxide (CO2) leaving pure iron behind.
Challenges of CO2 Emissions
This CO2 is then discarded as a waste product, and the pure iron is processed in further steps to form steel, which is then finished, shaped, and exported.
The steelmaking process involves many energy and carbon-intensive steps, but by far the most polluting is the reduction reaction, which produces huge quantities of CO2.
Moving Towards Sustainable Steelmaking
So, what can be done to move towards a more sustainable steelmaking process? Is green steel possible? The good news is that yes it is, and there is a viable solution: Hydrogen.
Hydrogen, like carbon, reacts readily with oxygen. Therefore, by replacing the coke with hydrogen, oxygen can still be extracted from the iron oxide, and pure iron can be produced. And the biproduct? H2O (water).
Making Sustainability a Reality With Hydrogen Steel
While the technical solutions are there, several hurdles need to be overcome to implement hydrogen-based steelmaking in practice. Firstly, green steel facilities are not yet fully developed, meaning they can be expensive and time consuming to design, build, and operate at this early stage in the technology’s maturity.
Secondly, hydrogen reduction can only be a truly clean alternative to carbon reduction if the hydrogen itself is produced using clean processes – so-called, “green” hydrogen. However, green hydrogen production techniques are still in their infancy.
From High-Emission Grey Hydrogen to Sustainable Green Hydrogen
Grey Hydrogen | Blue Hydrogen | Green Hydrogen | |
Production Method | Steam methane reforming (SMR) using natural gas. | SMR with carbon capture and storage (CCS). | Electrolysis using renewable energy. |
Carbon Emissions | High emissions, with CO2 released into the atmosphere. | Lower emissions, with CO2 captured and stored. | Zero emissions, as it relies on clean energy. |
Energy Sources | Fossil fuels (natural gas). | Fossil fuels with carbon capture. | Renewable energy (solar, wind, hydro). |
Environmental Impact | Significant contribution to global warming. | Transitional step with reduced environmental impact. | Fully sustainable and carbon-neutral. |
You cannot just change or transform the current blast furnaces into the new reactors that hydrogen-based steelmaking will need. An effective transition means that the old blast furnaces must be decommissioned, and then a completely new, hydrogen-ready facility must be created in their place.
Undertaking this transition can be costly and time consuming, so you want to make sure you get it right first time. This is where digital solutions are playing a critical role, helping turn innovative plans into practical change.
“At Dassault Systèmes, we provide tools that help steelmakers with the design and the engineering of these new facilities. These tools can simulate the activity of active plants, helping operators make critical choices and trade-offs,” says Bertrand. “Our tools can model everything from the production to the supply chain to warehousing.”
The 3DEXPERIENCE® suite of manufacturing solutions provide multi-scale virtual twin and simulation technologies. These are based on MBSE (model-base systems engineering) methods and tools, so the complexities of designing, building, and running new steel facilities can be effectively modelled, tested, and costed.
Unlock the Sustainable Value Path for Metals Industry Transformation
How metals producers can transform operations for efficiency, sustainability and future competitiveness
Optimizing Steel Production Today with Digital Tools for a Greener Tomorrow
The transition to hydrogen and electric powered furnaces of course won’t happen overnight. As steel producers plan and prepare for a greener future, the same digital tools that can enable change can help them reduce their current footprint. Virtual twins and manufacturing operation management tools help make the steel production process more energy efficient and cut waste.
For example, in steel milling and steel rolling – the processes by which heated steel produced and rolled or cut into sheets, tubes or coils – 3DEXPERIENCE tools help managers plan and schedule work throughputs, and optimize manufacturing resources.
Just by simply improving how material moves through your processes, substantial efficiencies can be realized. One global steelmaker was able to use 3DEXPERIENCE planning solutions to reduce scrap across their operations by up to 15%.
“We have a solution that reduces the time between the slab production and the time when you need to use it at the rolling mill. This allows to minimize the energy loss, as the steel does not need to be reheated for shaping,” says Bertrand. “It just goes straight from casting into rolling, staying hot and malleable.

The Role of Recycling in Decarbonizing Steel
Of course, one way to reduce steel production’s carbon footprint is to recycle more if it. While around 50% of the steel produced is used for buildings and infrastructure, the remainder will eventually end up as scrap, which can be recycled into new steel products. It is also estimated that recycling steel saves 72% of the energy used for primary production.
However, most steel consists of a unique chemical cocktail, and steel waste needs to be analyzed and broken down before it can be safely and successfully reused. Optimization software can make identifying chemical elements easier and improve the recycling process.
“When you get the scrap back, you can have lots of elements in the steel that you don’t want.” says Bertrand. “For steel to be recycled well, you need to minimize these elements. Dassault Systèmes’ statistical and optimization software can help you identify the origin and composition of the scrap. And then it makes it easier for it to be recycled.
Explore our Solutions
Manufacturing Industries Trends Guide: A Focus on Green Manufacturing
Discover how to set a clear plan of action and achieve steel green manufacturing goals for your operations
FAQ About Green Steel & Manufacturing
Hydrogen-based direct reduction employs hydrogen, not coal, as a reagent to convert iron ore into pig iron, thereby eradicating CO2 emissions compared to the conventional blast furnace method.
Green steel significantly reduces carbon emissions, contributing to a more sustainable environment. It also promotes the use of renewable energy and cleaner production processes, enhancing the overall eco-friendliness of the steel industry.
Aspect | Green Steel | Normal Steel |
Production Process | Uses renewable energy sources (e.g., hydrogen, biomass) in place of fossil fuels. | Relies heavily on fossil fuels, particularly coal in blast furnaces. |
Environmental Impact | Significantly reduced carbon emissions due to the use of clean energy. | High carbon emissions, contributing to global warming. |
Raw Materials | May use recycled steel, direct reduced iron (DRI), and clean hydrogen. | Primarily uses iron ore, coking coal, and limestone. |
Energy Source | Renewable energy (solar, wind, hydro) or green hydrogen. | Non-renewable energy (coal, natural gas, electricity from fossil fuels). |
Cost | Currently more expensive due to the newer technology and smaller scale of production. | Generally less expensive, with well-established processes and economies of scale. |
Market Availability | Emerging and limited, with increasing interest and investment. | Widely available, with well-established global supply chains. |
Lifecycle Impact | Lower environmental footprint across the product lifecycle. | Higher environmental footprint, including extraction, production, and disposal. |
Adoption | Early stages, mainly driven by environmental regulations and corporate sustainability goals. | Mature industry, with slow adaptation to new technologies. |
End Use | Suitable for applications requiring low carbon footprints, like green buildings and eco-friendly products. | Suitable for all traditional steel applications, but with a higher environmental cost. |
Green steel is an eco-conscious method for steel production, prioritizing sustainability. It harnesses renewable resources, emitting far fewer CO2 and pollutants than conventional methods. Furthermore, it boasts enhanced strength and durability, rendering it an excellent choice across various applications.
Currently, green steel averages a 40% higher cost than traditional production. By 2050, there's potential for it to become 5% more affordable than fossil-based methods.
Traditional steel production is one of the largest industrial sources of carbon emissions, contributing significantly to global greenhouse gas levels due to its reliance on fossil fuels. Green steel addresses this issue by using renewable energy sources and cleaner technologies, drastically reducing the carbon footprint of steel production. This shift helps mitigate climate change and promotes more sustainable industrial practices.