Understanding the power of parametric modeling
Professional architects, construction experts, and mechanical engineers all require powerful computer aided design (CAD) 3D modeling software to create structures, products, and machinery. To plan, visualize, and test their concepts, designers in these sectors use either parametric modeling CAD software or direct modeling CAD software.
What is parametric CAD modeling?
Does it have any advantages over direct modeling? Are there any drawbacks to using parametric 3D modeling? Why do some designers prefer direct modeling? We take a deep dive into parametric modeling and why it is such an essential tool for designers and engineers. A straightforward parametric modeling definition is that it is a CAD software tool that creates digital models based on sophisticated algorithms and rules known as ‘parameters’. These parameters form scripts that the CAD software uses to automatically create 3D shapes and models.
Parametric rules are used to define the relationships between different design elements. In this way, parametric modeling software automates much of the design process, unlike the direct modeling technique which requires the designer to manually create shapes themselves.
Consider this example: A parameter is created for an architectural design that imposes the rule that walls must be of a certain height and width to exactly fit between the floor and the ceiling. If the dimensions of the main model are changed, then the software will automatically create component models based on the updated algorithm. For instance, if the designer decides the height and width of the room must be increased, the parameters of the walls will be automatically expanded so that they fit the new room dimensions perfectly. In essence, the final 3D model is an exact representation of the parameters as defined by the designer.
Discover our parametric modeling solutions in the store
All Dassault Systèmes parametric modeling solutions work in conjunction with the 3DEXPERIENCE platform, a cloud-based environment where designers can easily and securely store, access, and share projects. Visit the Dassault Systèmes Store to explore all of our incredible parametric modeling software for yourself.
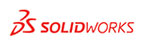
3DEXPERIENCE SOLIDWORKS
From mechanical 2D or 3D design to manufacturing, accelerate your processes at an affordable price.
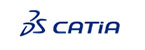
CATIA Mechanical Designer
Design on your terms with expert applications that cover the end-to-end mechanical design process
SOLIDWORKS xDesign
Get ready for the next generation of design solution, developed by the same team that brought you SOLIDWORKS 3D CAD
SOLIDWORKS 3D Creator
Create 3D designs with a powerful, collaborative, intuitive browser based solution
CATIA Sheet Metal Designer
From mechanical design to manufacturing, accelerate your processes at an affordable price.
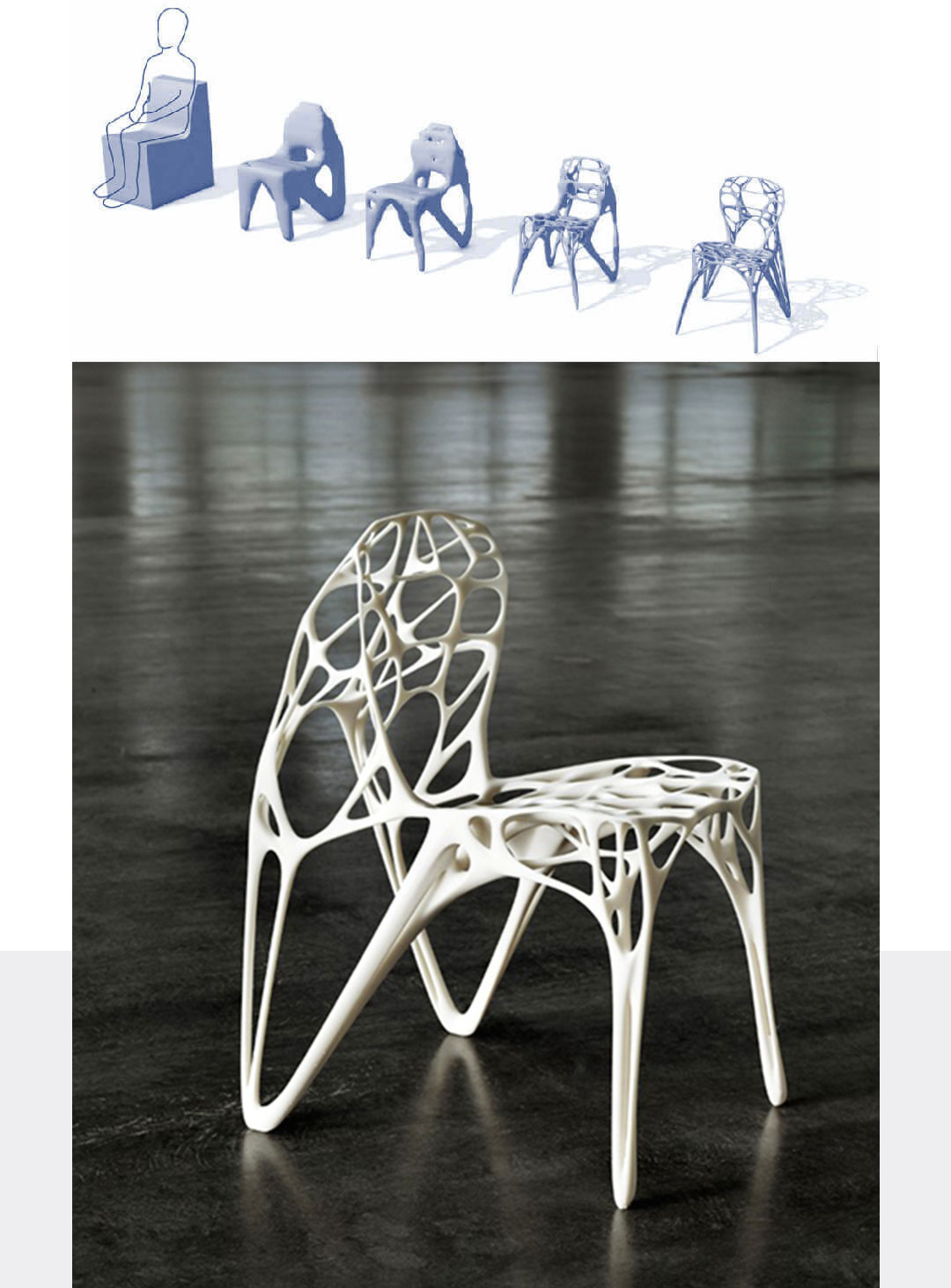
What type of projects is parametric modeling software used for?
Parametric modeling is most commonly used for design tasks that require the creation of multiple precisely rendered components. It is often used for producing families of products or parts that are based on variations of a core design.
The ability of parametric modeling to quickly and continuously create highly accurate models makes it a preferred tool for engineers and designers that work in the manufacturing sector. Parametric modeling is also widely used in the automotive industry and aerospace industry.
A recent example of parametric design in the automotive industry is Hyundai’s Tucson C-SUV which was designed using a concept that Hyundai describes as ‘Parametric Dynamics’. NASA also uses a specialized parametric aerospace design tool to develop aircraft components that enhance lift and create less drag.
Many large-scale construction and architectural projects use parametric modeling software. The renowned architect Frank Gehry is famous for his use of parametric design principles and parametric modeling software. The Walt Disney Concert Hall in Los Angeles was designed by Gehry using parametric modeling software.
Who uses parametric modeling software?
Many professional engineers and designers across a wide range of industries use parametric modeling software to develop concepts, vehicles, products, artwork, and structures.
Browse all the Dassault Systèmes store applications
We feature in our store some of our best software to design, collaborate and innovate throughout the entire product lifecycle.
Content related to parametric modeling
The advantages of parametric modeling software
A main advantage of parametric modeling is that it saves a great deal of time during the design process. The design automation capabilities of parametric modeling software mean that designers do not have to redraw a design each time the dimensions of a model change. Multiple parameters can be adjusted by making a few minor changes. Iterations of designs can be created much faster with much less effort than if a direct modeling approach was used.
Accuracy and precision are also major advantages of using parametric modeling software. Since each component of a 3D model is created automatically using algorithms the chance of human error is greatly reduced.
Parametric modeling enables designers to automatically create component or product families. It can be easily integrated with manufacturing processes, resulting in more streamlined production processes and reducing time to market.
Because parametric modeling has the capability of quickly processing highly complex geometric data, it is often used for structural analysis or to analyze the kinetics of machinery.
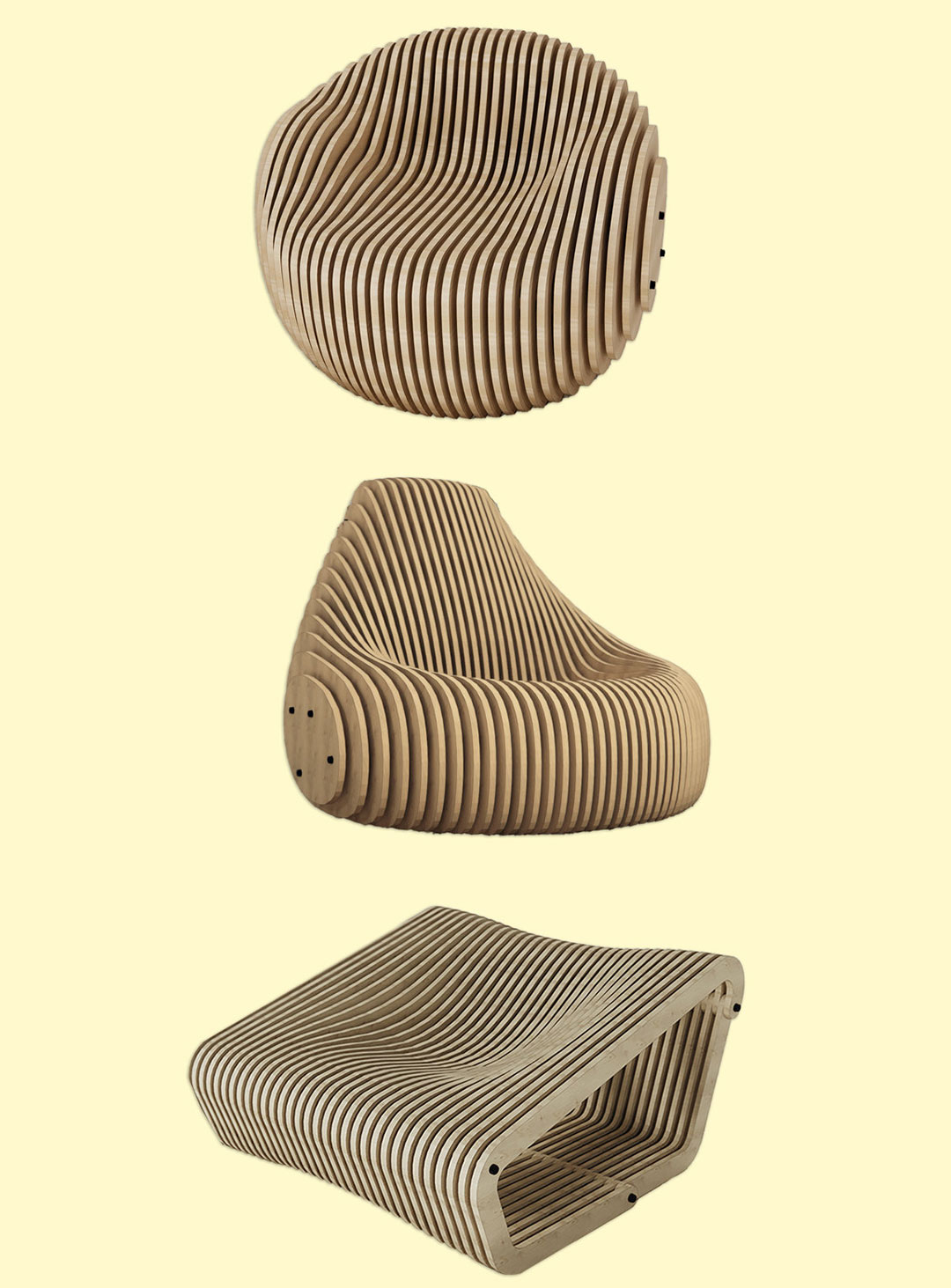
What is direct modeling?
Direct modeling can be said to be the opposite of parametric modeling. Direct modeling is a geometric-based modeling method that is similar to sculpting clay. With direct modeling, designers push and pull the geometry of a shape manually until they arrive at a satisfactory outcome.
While parametric 3D models are incredibly precise and can be generated quickly, models made using direct modeling techniques are not as accurate. Direct modeling is much better suited to creating conceptual drawings, organic models, or working on designs where flexibility and speed are prioritized over precision.
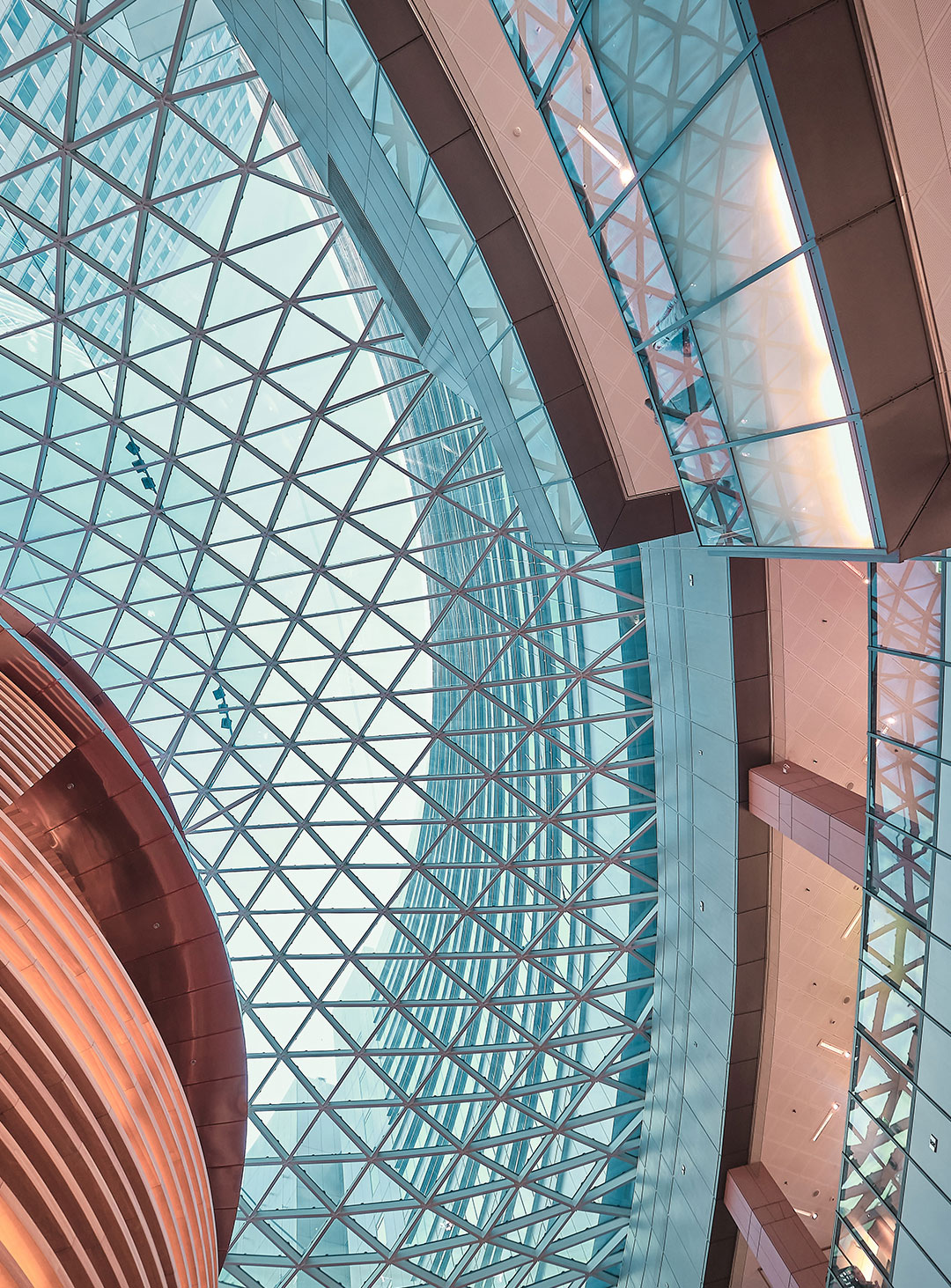
The drawbacks of parametric modeling software
Despite its many advantages, there are some drawbacks and limitations to using parametric modeling software. During conceptual phases, parametric modeling can be cumbersome. Truly capturing design intent using parametric modeling software can sometimes be difficult.
With parametric modeling software, designers must be able to anticipate design changes and set the parameters accordingly. Any unexpected alterations to a design can be hard to implement. Last-stage design changes, for example, can take a great deal of time.
Highly complex parametric modeling designs may necessitate more computing power as additional features and updates require increased processing. Without a sufficiently powerful computer, updating a large design can be a slow process.
There is also the cost and complexity of parametric modeling software to consider. Many CAD 3D parametric modeling programs have steep learning curves and are much more expensive than direct modeling tools. Also, some CAD programs use suite-specific files, so sharing designs may be difficult.
Explore Dassault Systèmes solutions
Discover the powerful browser-based modeling solutions from Dassault Systèmes. You can design whatever you wish, wherever you are with 3DEXPERIENCE.
Connecting data & people to foster innovation
The 3DEXPERIENCE platform on the cloud gives you access to a various set of applications that allow you to design, simulate, inform and collaborate on a project.
How to choose the right parametric 3D modeling software
Regardless of their skill level, a designer or engineer must ensure that their chosen parametric modeling software meets their needs. A person who wishes to design custom jewelry will require a different set of tools than an aerospace engineer, for example. When choosing which CAD parametric program to use, it is helpful to first come up with a set of criteria targeted towards your own particular requirements.
Consider the following questions when evaluating parametric modeling software:
- Is the software suitable for your project?
- Does the software contain tools that will allow you to complete your design?
- Will the software enable you to easily collaborate with colleagues?
- Is the software compatible with your devices?
- Does the software require licensing?
- Will the software provide sufficient return on investment?
Discover effective parametric modeling solutions in the Dassault Systèmes store
Industry professionals across the globe choose to use Dassault Systèmes range of powerful parametric modeling solutions. The features of Dassault Systèmes parametric modeling software are suitable for experienced engineers and designers as well as students and hobbyists. These exciting parametric modeling solutions work in conjunction with the 3DEXPERIENCE platform, a cloud-based environment where designers can easily and securely store, access, and share projects.
Visit the Dassault Systèmes Store to explore all of our incredible parametric modeling software for yourself.
- SOLIDWORKS xDesign
- 3D Creator
- CATIA Mechanical Designer
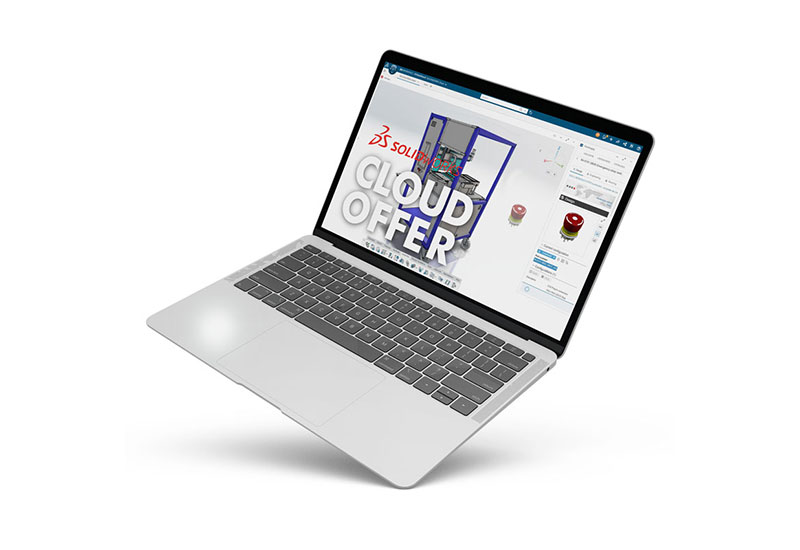
SOLIDWORKS xDesign
The SOLIDWORKS parametric CAD package provides users with the ability to create complex 3D models and photorealistic product renderings. Every stage of the design process can be achieved from the initial ideation process to collaborative design work with colleagues, simulations and testing, right through to the final construction or manufacturing phase.
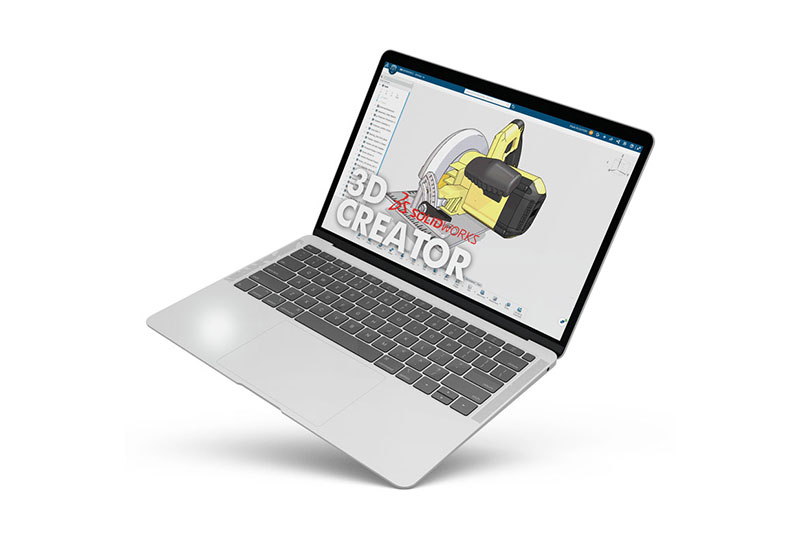
3D Creator
Included in the SOLIDWORK Cloud offer is 3D Creator, a powerful tool that enables users at all skill levels to generate complex geometries. 3D Creator is an ideal 3D parametric design solution that delivers unmatched design flexibility. The built-in version control eliminates the need for repetitive steps and ensures that all users have access to the most current data.
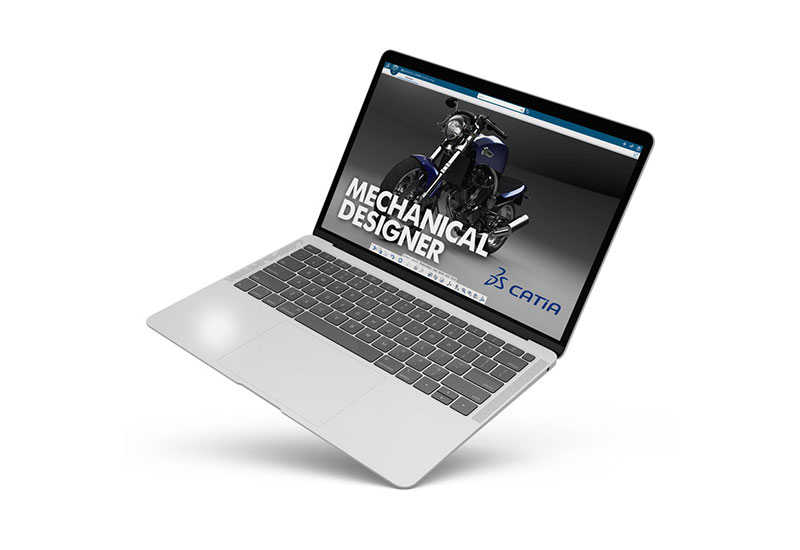
CATIA Mechanical Designer
CATIA Mechanical Designer is another innovative parametric design tool available via the Dassault Systèmes store. With CATIA Mechanical Designer, mechanical designers and engineers can create highly complex products and components. Efficient kinematics and dynamics simulations can analyze how components will move and function under real-world conditions. CATIA Mechanical Designer provides end-to-end solutions for the entire mechanical design process.
Why choose Dassault Systèmes for your parametric modeling needs?
40 years of experience
Dassault Systèmes, with its 40 years of experience in CAD solutions, is a trusted and reputable company that is well-positioned to provide high-quality parametric modeling and CAD design solutions. One key advantage of working with Dassault Systèmes is its long history of innovation and leadership in the CAD industry. The company has a proven track record of developing and delivering cutting-edge CAD software that is used by many of the world's leading companies and organizations. Additionally, Dassault Systèmes has a strong focus on customer service and support, with a dedicated team of experts who are available to help customers with any issues or questions that may arise.
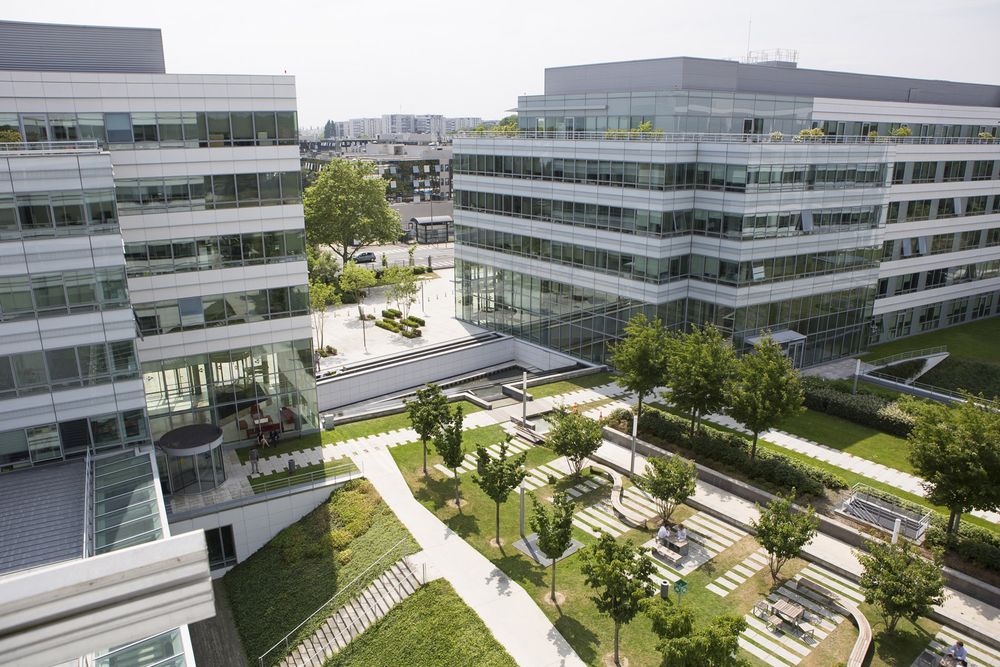
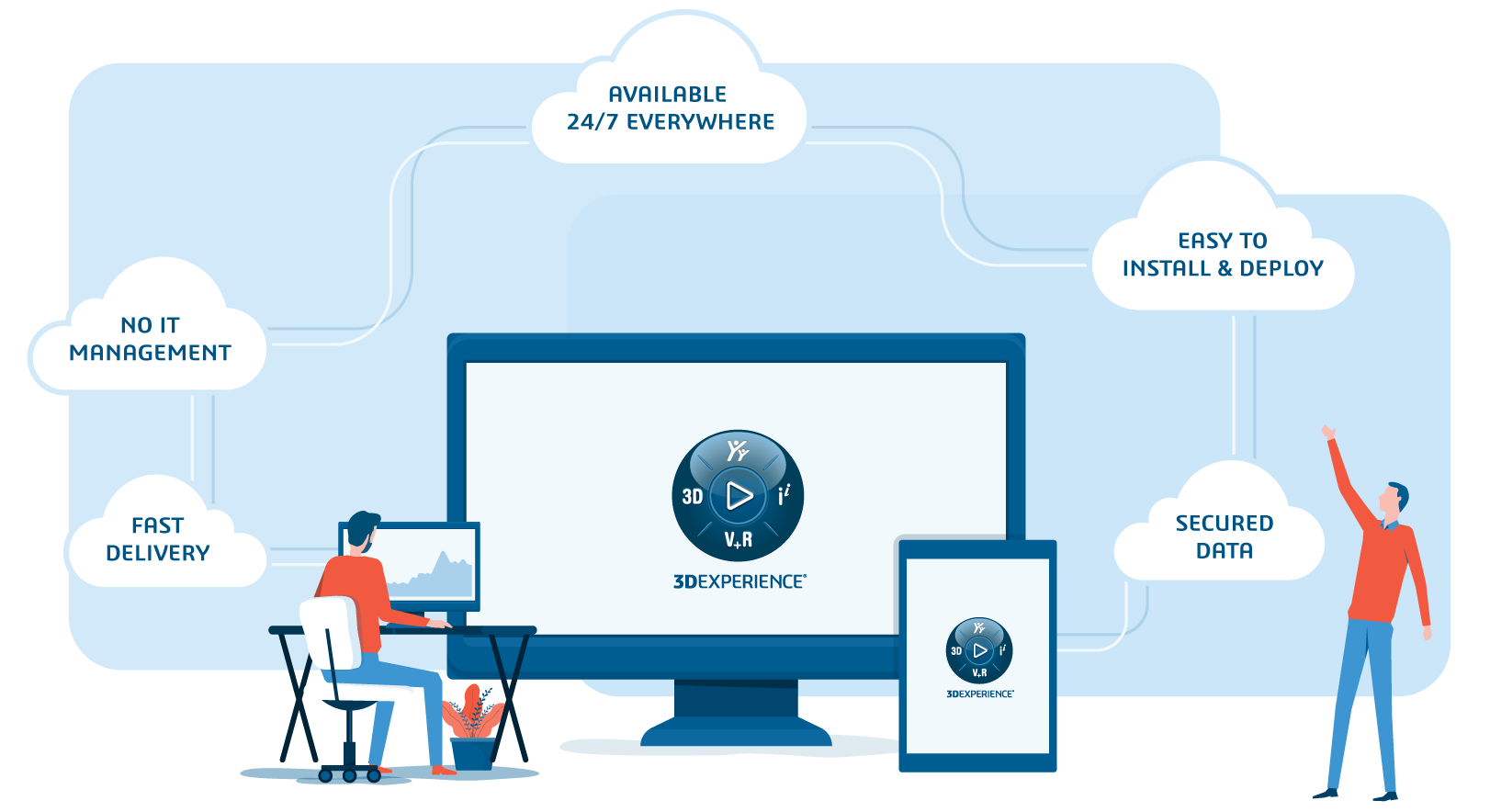
The power of the 3DEXPERIENCE platform
The 3DEXPERIENCE platform from Dassault Systèmes offers a comprehensive parametric modeling solution that allows for efficient design, simulation, and analysis of complex systems. One key advantage of this platform is its ability to integrate multiple design tools and workflows into a single unified environment. This allows for seamless collaboration and data exchange between different teams and disciplines, as well as easy access to a wide range of specialized design tools for tasks such as simulation, analysis, and manufacturing.
Explore inspiring content
Frequently asked questions
Parametric solid modeling is a CAD technique whereby 3D shapes are generated using computer algorithms with set rules. Users can define the parameters of their designs and so quickly and easily create 3D models. Parametric solid modeling enables engineers and designers to change elements without having to completely redraw the design from scratch.
Parametric modeling is used for a wide range of applications. It is used by diverse professionals such as architects, construction experts, mechanical engineers, automotive designers, aerospace engineers, video game developers, and jewelry and fashion designers.
Generally, the parametric modeling process contains a set of eight steps. Designers must:
1. Create the Units and the Part names
2. Decide the base features and the initial solid features
3. Create an initial two-dimensional sketch of the base of the design
4. Apply or modify design constraints, rules, and parameters
5. Create a detailed 3D parametric solid model from the two-dimensional sketch
6. Add any additional parametric features to the 3D model
7. Analyze the 3D model via simulations and update the design as required
8. Generate 2D and 3D drawings of the finished design
SOLIDWORKS is an industry-leading 3D design solution that uses parametric design principles to generate precise 2D and 3D solid models. Its array of powerful tools, its compatibility, and its intuitive interface have made SOLIDWORKS the preferred 3D modeling design solution. SOLIDWORKS is used by professional designers and engineers in a wide range of industry sectors across the globe.