Maintenance
Strengthen Your Industrial Maintenance with Augmented Reality
Industrial Maintenance Operations with Augmented Reality
Maintenance of equipment or installations can be a real challenge when dealing with complex elements, when intervention time is limited, and when costs can be quickly high. Technicians must thoroughly know each piece of equipment and work quickly to minimize downtime. DELMIA Augmented Experience enables technicians and quality managers to diagnose and solve problems faster, reduce service costs and increase customer satisfaction with reliable and accurate augmented reality technology.
The maintenance of complex equipment can be lengthy and costly, with the risk of errors and lack of traceability. It requires giving a product status before starting repair tasks by identifying defective elements, accurate disassembly/reassembly instructions, or inspecting equipment before redelivery. DELMIA intervenes in each step, assisting operators through interactive digital work instructions powered by augmented reality to improve efficiency throughout the maintenance process. Maintenance tasks can be complex, with documentation that is difficult to interpret, and the risk of missing a defect or making a mistake during the repair operation is high. DELMIA Augmented Experience guides operators through maintenance operations via interactive step-by-step instructions displayed in AR directly on the part.
AR provides precise visual guidance to maintenance personnel, allowing them to accurately identify and locate components, connections, or faulty parts. This minimizes errors and ensures that maintenance tasks are performed correctly the first time, reducing the likelihood of rework or additional repairs. The real-time feedback and visual cues provided by AR technology enhance accuracy and precision in maintenance operations. On top of that, AR can be utilized as a powerful training tool for maintenance personnel. AR-based training enhances knowledge retention, reduces training time, and accelerates the learning curve for new technicians, ensuring a skilled workforce.
- Control Upon Arrival of Assembled Equipment
- Assistance to Disassembly & Reassembly
- Final Inspection Before Redelivery
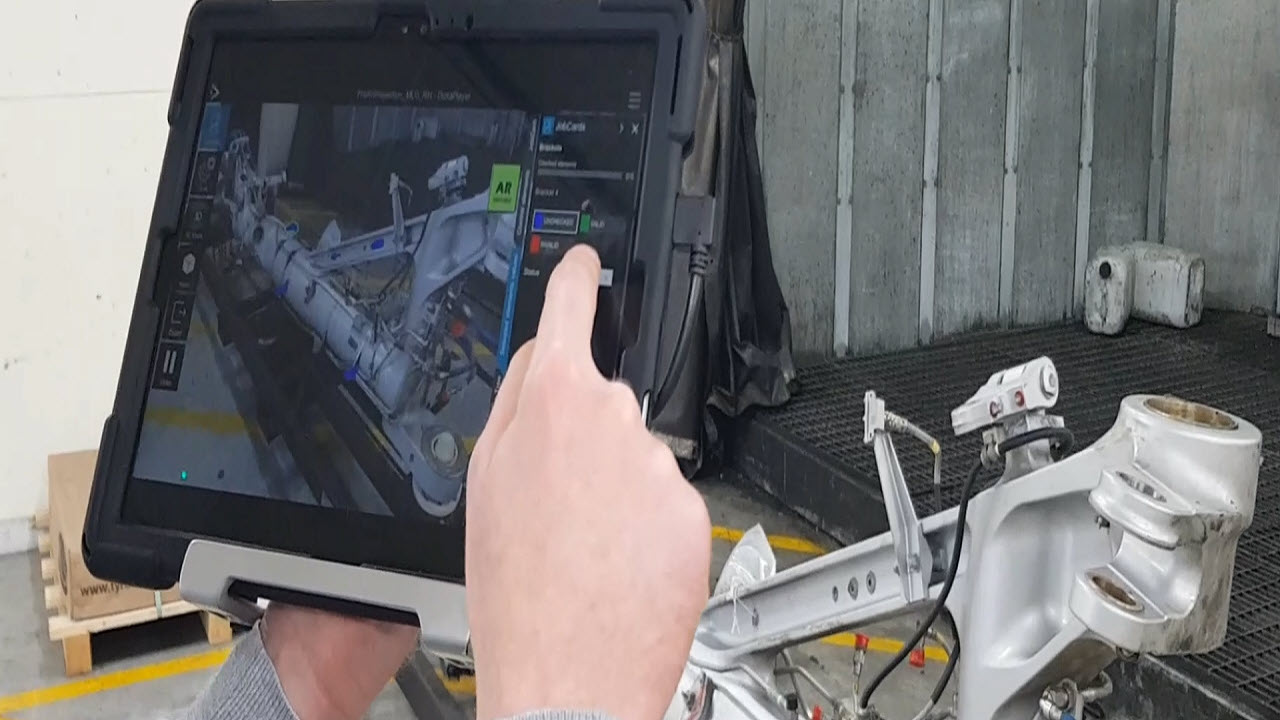
The incoming inspection process to map defects and future repairs is often lengthy and sometimes incomplete. It requires extensive paper documentation and can lead to internal communication difficulties with repair teams and customer dissatisfaction through improperly anticipated repairs and costs. Digital inspection instructions are displayed through augmented reality (AR) to capture all checkpoints for compliance and ensure the completeness of the task. The precise location of the identified defects is captured in the 3D model with the automatic generation of an inspection report. The result is faster inspection and reporting to identify defects quickly, collect data to improve traceability, and ensure end customer satisfaction.
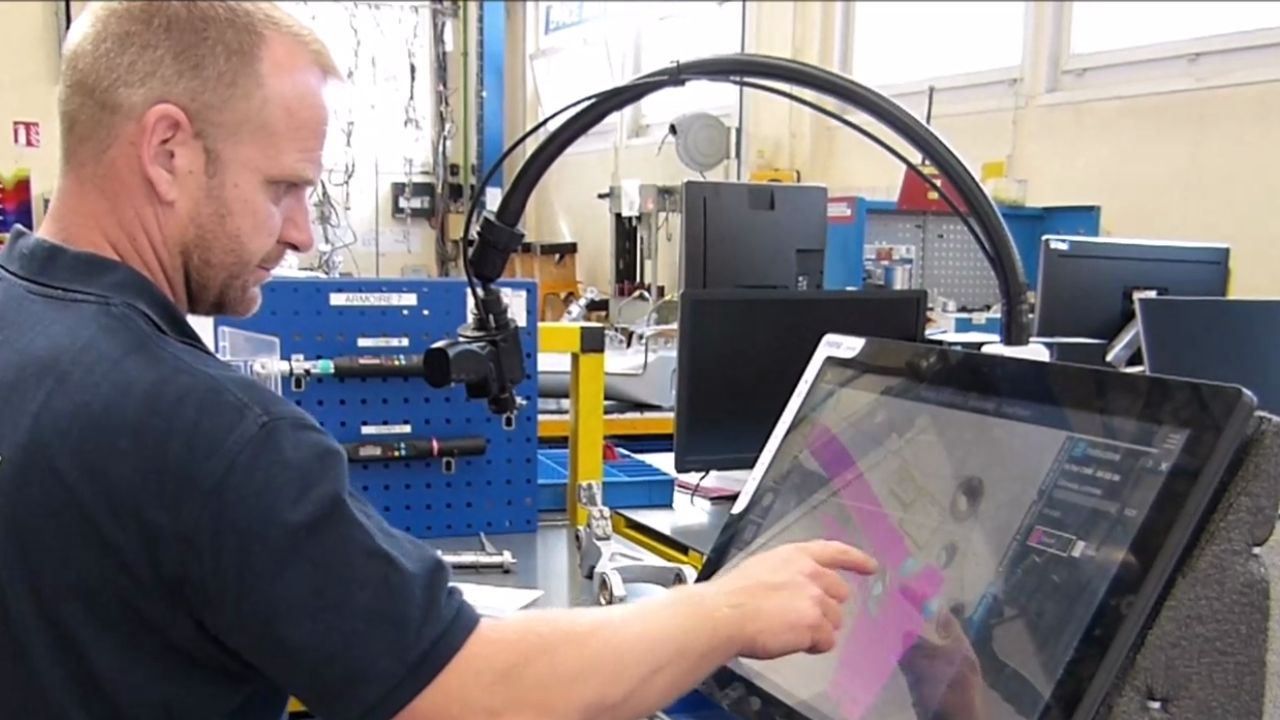
Disassembly and reassembly processes include dismantling equipment, replacing defective parts, and reassembly to ensure optimal equipment operation. The challenges are numerous and can significantly impact the equipment's life, performance, safety, and reliability. Operators are guided step-by-step through digital work instructions that assist them with disassembly, repair, and reassembly tasks. Each step is displayed via augmented reality on a screen or directly on the equipment. As a result, users achieve improved quality and productivity of the maintenance tasks.
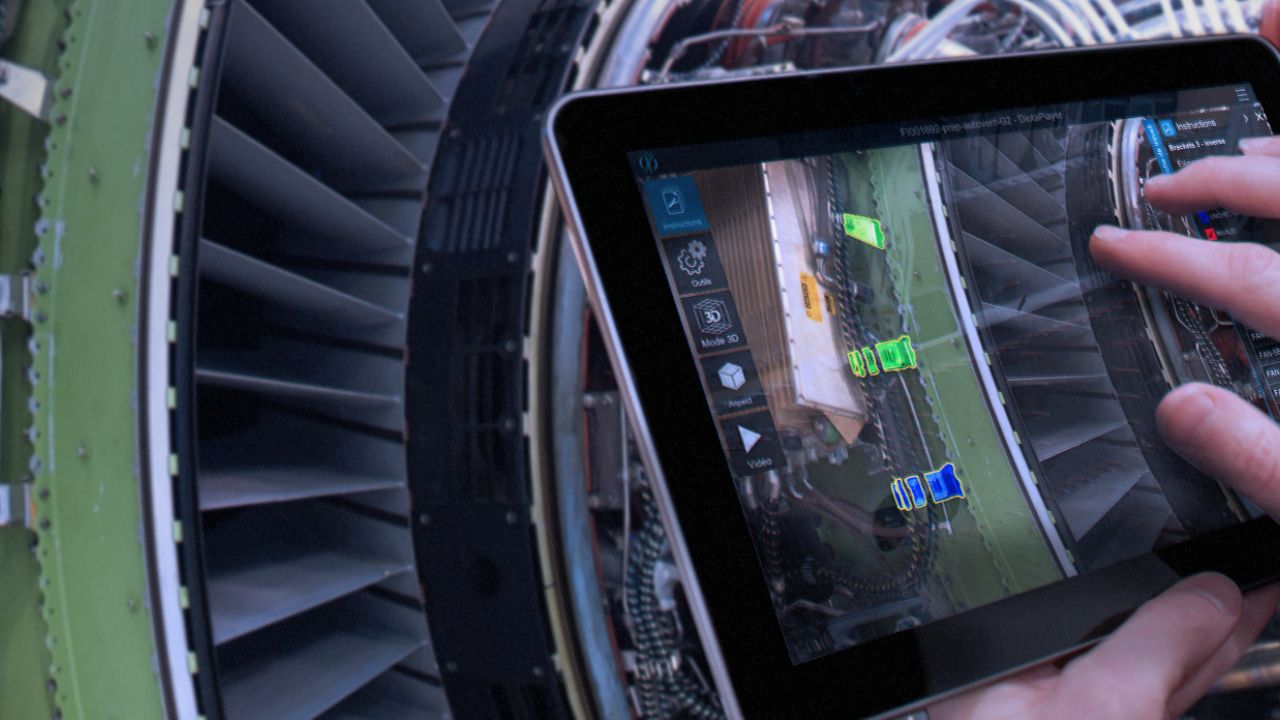
Before redelivering equipment to a customer after performing maintenance operations, a final inspection is required to ensure that the product meets quality and safety standards. Inspection instructions based on the 3D model are brought directly into the field to guide operators. Augmented reality verifies the conformity of the equipment and allows the detection of manufacturing defects (positioning, absence/presence of elements, etc.). This saves time, improves inspection quality, and ensures equipment conformity before redelivery.
Start Your Journey
The world of manufacturing & operations is changing. Discover how to stay a step ahead with DELMIA.
FAQ about AR in Industrial Maintenance
Augmented reality (AR) in industrial maintenance offers numerous benefits, revolutionizing traditional maintenance practices. AR technology enables maintenance technicians to access real-time information and instructions overlaid onto their field of view. Technicians can quickly identify components, view step-by-step repair instructions, and access relevant data without interruption, reducing downtime and improving overall productivity.
In summary, augmented reality in maintenance offers benefits such as enhanced efficiency, improved accuracy, remote assistance and collaboration, knowledge transfer and training, equipment visualization, and streamlined documentation and data management. By leveraging AR technology, organizations can optimize their maintenance operations, reduce downtime, increase productivity, and achieve cost savings.
Also Discover
Learn What DELMIA Can Do for You
Speak with a DELMIA expert to learn how our solutions enable seamless collaboration and sustainable innovation at organizations of every size.
Get Started
Courses and classes are available for students, academia, professionals and companies. Find the right DELMIA training for you.
Get Help
Find information on software & hardware certification, software downloads, user documentation, support contact and services offering