3D-Druck in der Luft- und Raumfahrt
3D-Druck in der Luft- und Raumfahrt verändert die Flugzeugproduktion, indem er es Ingenieuren ermöglicht, schnell Teile zu entwerfen und zu entwickeln, die stärker, leichter und kostengünstiger sind.
Was ist 3D-Druck?
3D-Druck oder additive Fertigung ist ein Produktionsverfahren, bei dem ein dreidimensionales Objekt anhand einer CAD-Datei (Computer Aided Design) erstellt wird. Der Begriff umfasst mehrere verschiedene Verfahren, bei denen ein oder mehrere Materialien - meist Kunststoff, Metall, Wachs oder Verbundwerkstoffe - Schicht für Schicht aufgetragen werden, um eine Form zu erzeugen.
Der gesamte Prozess ist computergesteuert, was den 3D-Druck zu einer kostengünstigen, effizienten und präzisen Methode zur Herstellung von Objekten mit nahezu beliebiger Geometrie und Komplexität macht. Heute wird der 3D-Druck in allen Branchen eingesetzt, um alles zu produzieren, von Prototypen, Werkzeugen und Vorrichtungen bis hin zu Komponenten und Endverbrauchsteilen.
3D-Drucker gibt es in verschiedenen Größen, von kleinen Tischgeräten bis hin zu großformatigen Industriemaschinen.
Mit großen Druckern können größere Objekte hergestellt werden, aber die Geräte benötigen mehr Platz und sind im Vergleich zu Tischdruckern deutlich teurer. Ein erfolgreicher Druck ist bei großformatigen Geräten aufgrund der Menge des Materials und der Druckzeit auch komplexer.
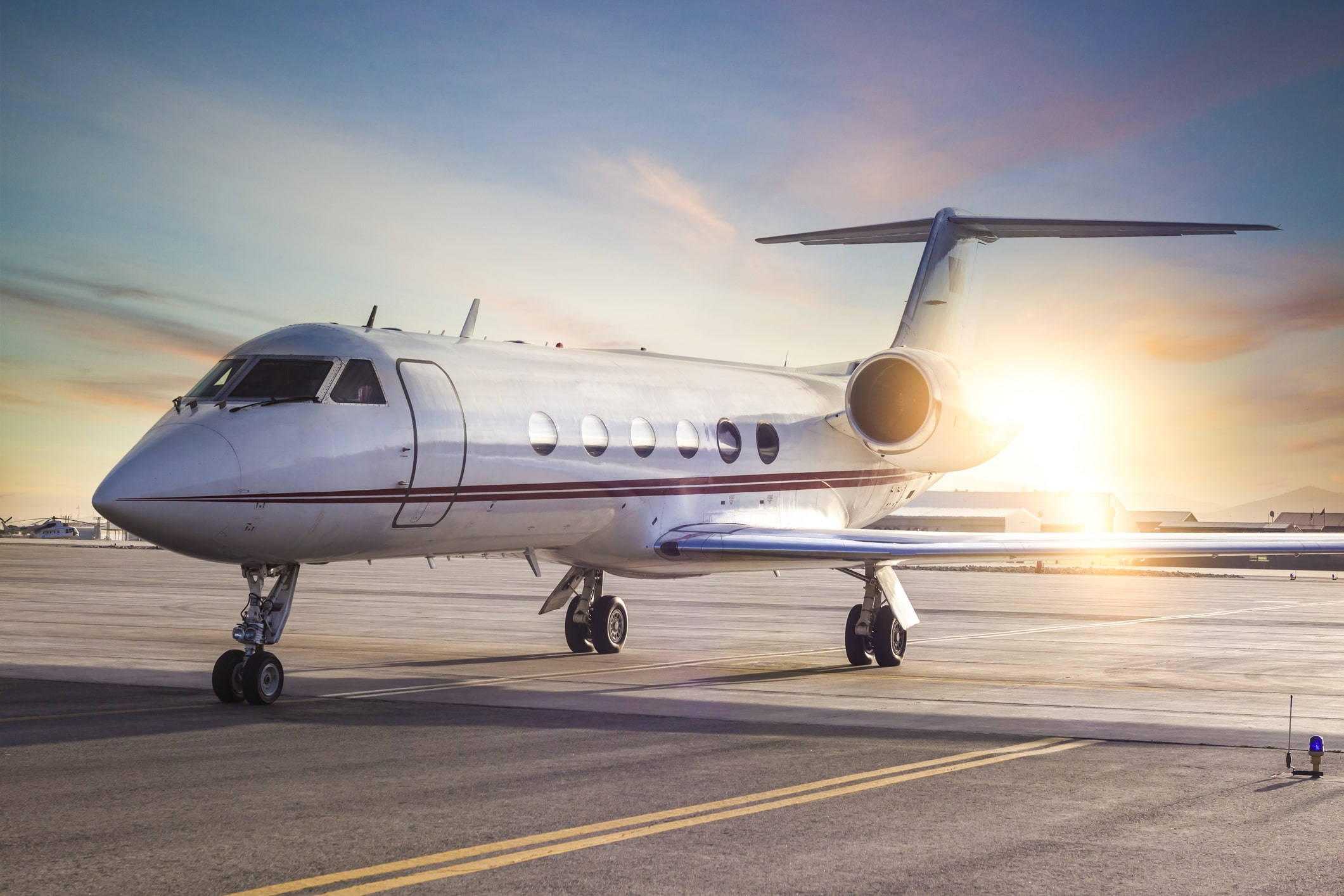
Wie verändert der 3D-Druck die Luft- und Raumfahrtindustrie?
Die 3D-Drucktechnologie unterstützt die Luft- und Raumfahrtindustrie auf sieben wichtige Arten:
Rationalisierung und Vereinfachung des Design-Workflows
Herstellung leichterer, stabilerer Teile
Konsolidierung mehrerer Teile in ein einziges Teil
Minimiert die Verschwendung von extrem teuren Rohmaterialien
Verkürzt die Zeit bis zur Marktreife
Verbessert die Kosten- und Ressourceneffizienz
Optimiert Lagerhaltung und Logistik
Die Luft- und Raumfahrtindustrie gehörte in den späten 1980er Jahren zu den ersten Anwendern des 3D-Drucks und ist auch heute noch führend in der Entwicklung und Anwendung dieses Verfahrens.
Flugzeughersteller und -zulieferer gehören zu den größten Nutzern des 3D-Drucks. Alle führenden Hersteller von Verkehrsflugzeugen (Airbus, Boeing, Bombardier und Embraer) und Triebwerkslieferanten (GE Aviation, Pratt & Whitney, Rolls-Royce und Safran) haben den 3D-Druck in ihre Prozesse integriert. Einige haben sogar eigene Geschäftsbereiche, die sich mit der Arbeit und der Weiterentwicklung von Hardware, Software, Materialien und Anwendungsfällen des 3D-Drucks beschäftigen.
Obwohl der 3D-Druck bereits 40 Jahre alt ist, hat er erst in jüngster Zeit den Sprung von der Nische zum Mainstream geschafft. Heute finden sich Beispiele für den 3D-Druck in der Luft- und Raumfahrt in jeder Phase der Produktion, von der Forschung und Entwicklung (F&E) über die Fertigung bis hin zu den Endteilen und der Wartung.
Das gilt für viele Branchen, insbesondere aber für die eng mit der Luft- und Raumfahrt verbundenen Bereiche wie Verteidigung, Raumfahrt und Automobilbau, in denen das Gewicht ein entscheidender Leistungsfaktor ist.
Der 3D-Druck in der Luft- und Raumfahrt ist ideal für die Bedürfnisse der Industrie geeignet, weil er:
relativ geringe Produktionsmengen,
komplexe Teilegeometrien
Nachfrage nach leichteren, effizienteren Teilen
Bedarf an Prozess- und Kosteneffizienz zur Einhaltung anspruchsvoller Liefertermine
3D-Druck macht Flugreisen nachhaltiger
Die E-Jet E2-Familie sind Mittelstreckenflugzeuge, die vom brasilianischen Hersteller Embraer entwickelt wurden. Der E2 wurde im April 2018 in Dienst gestellt und tritt die Nachfolge des ursprünglichen E-Jet an.
Thermoplast, eines der gängigsten 3D-Druckmaterialien für die Luft- und Raumfahrt, wurde zu Beginn des E2-Programms verwendet, um die zeitaufwändigen und manuellen Prozesse zu ersetzen, in denen Teile und Werkzeuge hergestellt wurden.
Heute benötigen dieselben Teile 50 % weniger Vorlaufzeit und erzeugen 65 % weniger Abfall. Das Ergebnis ist ein besseres, leichteres und nachhaltigeres Teil, das weniger kostet und schneller hergestellt werden kann.
Der 3D-Druck in der Luft- und Raumfahrt wird für die Herstellung von 37 Teilen für die Innenausstattung des E2 verwendet. Dazu gehören Klimagitter, Schutzvorrichtungen für Kabelbäume, Flansche für Ansaugtoiletten und Luftkanäle sowie Werkzeugteile und Vorrichtungen. Embraer nutzt den 3D-Druck auch, um Proof-of-Concept-Teile zu testen, von Becherhalter-Baugruppen bis hin zu Flügelvorderkanten.
Das Unternehmen produziert derzeit etwa 1.800 Teile pro Jahr im 3D-Druck für das E2-Programm, und seine Ingenieure arbeiten an der Entwicklung von 3D-gedruckten Metallteilen. Ihre Studien haben mehrere Metallkomponenten identifiziert, bei denen der 3D-Druck in der Luft- und Raumfahrt ähnliche und möglicherweise sogar höhere Zeit-, Gewichts-, Kosten- und Umwelteinsparungen ermöglichen kann als bei thermoplastischen Materialien.
Die potenziellen Anwendungsmöglichkeiten für den 3D-Druck in der Luft- und Raumfahrt sind nach Angaben eines Unternehmenssprechers enorm". Embraer prüft die Effektivität des 3D-Drucks für eine Vielzahl von Bauteilen, darunter die Flugzeugzelle, Hydraulik-, Elektro- und Klimasysteme, das Fahrwerk, die Innenausstattung, Funktionsprototypen und Werkzeuge, um nur einige zu nennen.
Wie wird der 3D-Druck in der Luft- und Raumfahrt eingesetzt?
Die vier häufigsten Anwendungen des 3D-Drucks in der Luft- und Raumfahrt sind:
PROTOTYPING
Das Prototyping ist ein entscheidender Schritt im Produktentwicklungsprozess. So gut digitale Entwurfswerkzeuge auch sein mögen, es gibt immer noch keinen Ersatz für das Anfassen und Betrachten eines physischen Objekts.
Anhand eines Modells in einem frühen Stadium kann das Ingenieurteam sehen, wie ein Produkt aussieht und sich anfühlt. Es bietet die Möglichkeit zu sehen, wie sich die verschiedenen Komponenten zueinander verhalten, und zu beurteilen, ob ein Produkt ordnungsgemäß funktioniert und den Konstruktionsspezifikationen entspricht.
Früher wurden Prototypen von Hand oder mit Hilfe von Gussformen hergestellt, die oft von einem externen Unternehmen entworfen und gefertigt werden mussten. Das war teuer und konnte Wochen oder sogar Monate dauern.
Der 3D-Druck verkürzt den Produktentwicklungszyklus, da Luft- und Raumfahrtingenieure Prototypen in einem Bruchteil der Zeit entwerfen und drucken können, die mit herkömmlichen Fertigungsmethoden erforderlich wäre.
Durch die Verkürzung der Zeitspanne zwischen den einzelnen Entwurfsverfeinerungen können mehr Tests in der gleichen oder einer kürzeren Zeitspanne durchgeführt werden, was dazu beiträgt, potenzielle Probleme früher zu erkennen. Auf diese Weise können Luft- und Raumfahrtunternehmen ihre Markteinführung beschleunigen und der Konkurrenz einen Schritt voraus sein.
WERKZEUGBAU, VORRICHTUNGEN UND HALTERUNGEN
Ein Produktionsbereich, in dem sich der 3D-Druck in der Luft- und Raumfahrt als besonders vorteilhaft erweist, ist die Erstellung von kostengünstigen Schnellwerkzeugen, Vorrichtungen und Halterungen. Flugzeuge bestehen aus Millionen von Einzelteilen und Unterbaugruppen, von denen viele komplex sind und präzise in die Flugzeugzelle (die mechanische Grundstruktur eines Flugzeugs) eingepasst werden müssen.
Dazu sind für jedes Flugzeug Hunderte von spezifischen Fertigungsvorrichtungen, Halterungen, Führungen und Schablonen erforderlich. Das 3D-Drucken dieser Teile vor Ort oder in unmittelbarer Nähe kann zu erheblichen Zeit- und Kosteneinsparungen von 60 % bis 90 % im Vergleich zu herkömmlichen Produktionsverfahren führen.
PRODUKTIONSTEILE
Es gibt zwei Hauptkategorien von 3D-gedruckten Produktionsteilen, die in der Luft- und Raumfahrt verwendet werden:
Flugzeuginnenteile - wie Luftkanäle, Wandpaneele, Verkleidungsteile, Endkappen, Sitzlehnen, Griffe, Beleuchtungskörper und Kabinenzubehör. Diese werden in der Regel aus einem thermoplastischen oder polymeren Material wie ABS, Nylon oder Harz hergestellt. 3D-gedruckte Innenteile machen derzeit den Großteil der fliegenden Teile aus, da sie als nicht oder nur geringfügig kritisch für den Flug eingestuft werden. Daher ist es relativ einfach, für sie eine Zulassung von den zivilen Luftfahrtbehörden zu erhalten. Innenraumteile sind jedoch oft für die Passagiere sichtbar und müssen unter Umständen bedient werden. Daher müssen sie nicht nur funktional, sondern auch ästhetisch ansprechend sein.
Mechanische Flugzeugteile - wie Kraftstoffdüsen, Halterungen, Querlenker, Tragflächen, Luken und Gehäuse. Aufgrund der mechanischen und temperaturbedingten Belastungen, denen diese Teile ausgesetzt sind, insbesondere im Zusammenhang mit Triebwerken, werden sie in der Regel aus einem Metall wie Titan oder Aluminium hergestellt.
Nur eine Handvoll Teile hat bisher den Status "flugsicher" erhalten, da das Zulassungsverfahren für flugkritische Komponenten strenger ist. Diese Zahl nimmt dank der kontinuierlichen Erforschung neuer Materialien und Verfahren sowie der zunehmenden Gewöhnung von Behörden und Herstellern an die 3D-Drucktechnologie stetig zu.
ERSATZTEILE FÜR WARTUNG UND REPARATUREN
Die Wartung, Reparatur und Überholung (MRO) ist ein wichtiger Bestandteil der Luft- und Raumfahrtindustrie. Der Begriff umfasst alle Wartungs- und Inspektionstätigkeiten, die durchgeführt werden, um den sicheren Betrieb eines Flugzeugs zu gewährleisten.
Ein Flugzeug wird erst dann zum Umsatzbringer, wenn es fliegt. Für MRO-Anbieter ist es daher von größter Bedeutung, die Zeit am Boden" zu minimieren. Dazu muss das richtige Teil mit minimaler Zeitverzögerung am richtigen Ort sein.
Die Luft- und Raumfahrt hat eine der bekanntesten und längsten Lieferketten aller Branchen. Die Verfügbarkeit von Teilen zum richtigen Zeitpunkt führt dazu, dass Unternehmen große Mengen an Komponenten in Lagern vorrätig halten müssen, was mit erheblichen Kosten verbunden ist.
Die Geschwindigkeit, Flexibilität und Effizienz des 3D-Drucks in der Luft- und Raumfahrt ermöglicht es den Herstellern, Ersatzteile auf Abruf zu produzieren. Das ist drastisch schneller und kostengünstiger als die Bestellung über die üblichen Lieferkanäle und bietet den zusätzlichen Vorteil, dass die Teile für den jeweiligen Zweck maßgeschneidert sind. Dies trägt nicht nur zur Optimierung der Lagerbestände bei, sondern macht auch die Unterhaltung von Lagereinrichtungen überflüssig. Außerdem können Ingenieure schwer zu beschaffende oder veraltete Komponenten für den 3D-Druck umgestalten. Dies kann zu Zeit-, Kosten- und Arbeitseinsparungen sowie zu leichteren Teilen mit besserer Leistung führen.
3D-Druck trägt zur Verlängerung der Lebensdauer von Flugzeugen bei
Die Verfügbarkeit von Ersatzteilen kann den Unterschied zwischen dem Betrieb eines Flugzeugs und der Verhinderung eines Flugs ausmachen. Da ein durchschnittliches Flugzeug aus Millionen von Bauteilen besteht, kann es sich als schwierig erweisen, eine sichere Versorgung mit Ersatzteilen über die 30-jährige Betriebsdauer eines Flugzeugs zu gewährleisten.
Satair, ein in Dänemark ansässiges Unternehmen für Flugzeugkomponenten und -dienstleistungen und eine Tochtergesellschaft von Airbus, hat dieses Problem mit Hilfe des 3D-Drucks von Metall gelöst. Im Jahr 2020 lieferte das Unternehmen einem seiner Fluglinienkunden in den USA das angeblich erste zertifizierte 3D-gedruckte fliegende Ersatzteil aus Metall.
Das betreffende Teil wurde vom ursprünglichen Zulieferer nicht mehr produziert, aber die Neukonstruktion des Teils, das mit herkömmlichen Fertigungsmethoden wie der maschinellen Bearbeitung hergestellt werden sollte, erwies sich als zu kostspielig und zu langwierig.
Mithilfe eines neuen Zertifizierungsverfahrens konnte Satair das ehemalige Gussteil innerhalb von fünf Wochen neu zertifizieren und an Titan, ein qualifiziertes luftfahrttaugliches additives Fertigungsmaterial, anpassen.
Vier Teile (ein kompletter Satz für ein Flugzeug) werden gleichzeitig gedruckt, was 26 Stunden dauert, wodurch die Kosten und die Druckzeit pro Teil reduziert werden. Nach dem Druck wird das Teil einer Nachbearbeitung unterzogen, um flugtauglich zu werden, so dass es ein Eins-zu-Eins-Ersatz für die ursprüngliche Komponente ist und die gleichen Sicherheitsanforderungen erfüllt.
Insgesamt hat der 3D-Druck in der Luft- und Raumfahrt zu höherer Flexibilität, kürzeren Vorlaufzeiten und einer wirtschaftlicheren Produktionsweise geführt. Außerdem wird prognostiziert, dass die Zertifizierungszeit von fünf Wochen sinken wird, wenn sich die Technologie weiter durchsetzt.
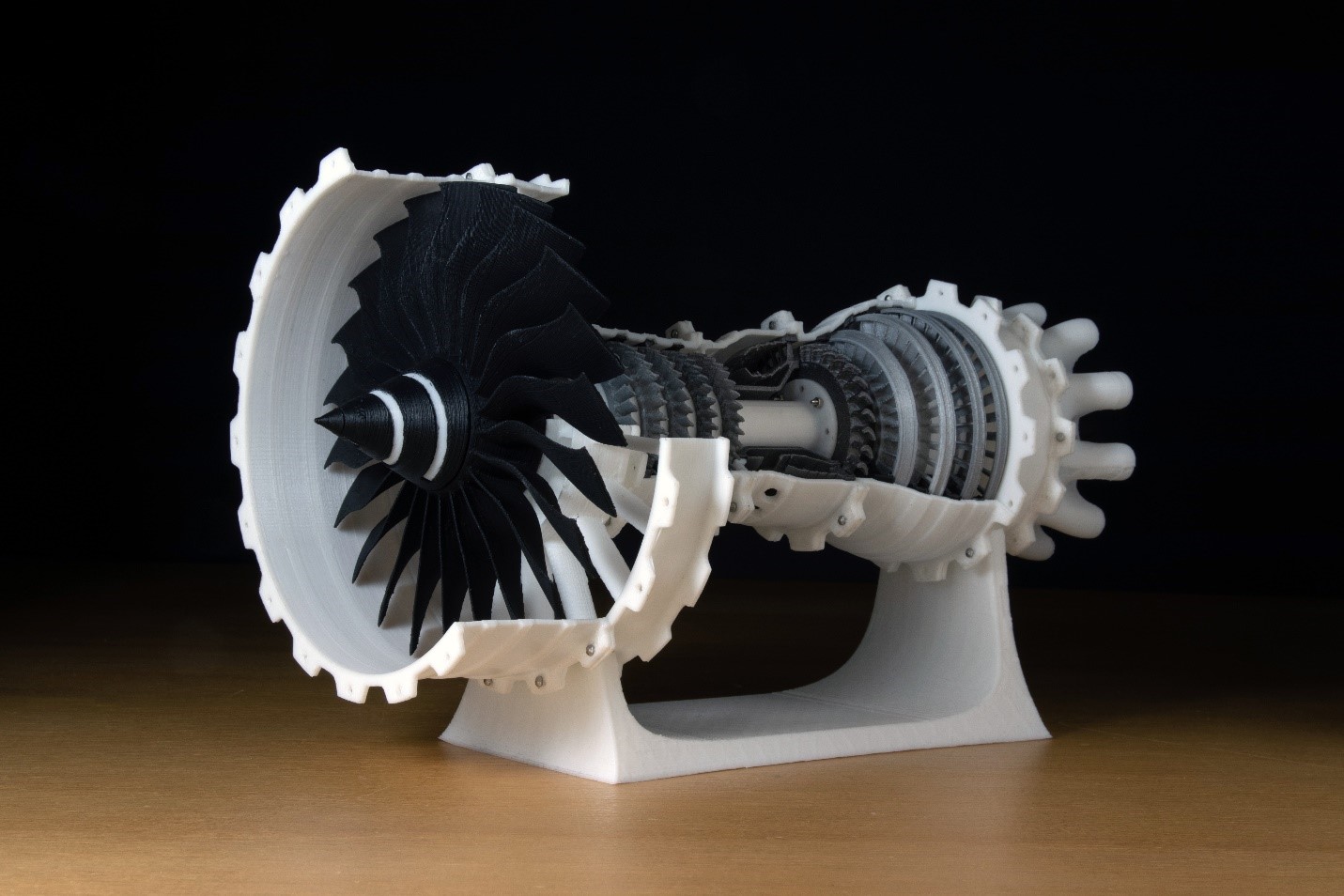
Wo liegen die Wachstumschancen für den 3D-Druck in der Luft- und Raumfahrt?
Verbesserungen bei der Größe von Industriedruckern, bei der Druckgeschwindigkeit und bei der Design- und Materialflexibilität tragen dazu bei, dass der 3D-Druck zu einem praktikableren Fertigungsverfahren wird - insbesondere für kleine bis mittlere Produktionsserien hochwertiger, geometrisch komplexer Teile.
Infolgedessen entstehen ständig neue Anwendungen für den 3D-Druck in der Luft- und Raumfahrt. Einige der Bereiche, für die in den nächsten fünf bis zehn Jahren ein beträchtliches Wachstum erwartet wird, sind:
GRÜNE LUFTFAHRT
Die Luft- und Raumfahrt steht wie jede Branche unter dem Druck, nachhaltiger zu werden. Ein klarer Vorteil des 3D-Drucks ist der Leichtbau - ein Begriff, der die Verwendung leichterer Teile zur Verringerung des Gesamtgewichts eines Fahrzeugs und damit zur Reduzierung des Kraftstoffverbrauchs beschreibt. Eine Gewichtsreduzierung von 20 % bei einem Verkehrsflugzeug führt beispielsweise zu einer Verbesserung der Treibstoffeffizienz um etwa 10 %.
Auf diese Weise trägt der 3D-Druck in der Luft- und Raumfahrt dazu bei, leichtere und schnellere Flugzeuge herzustellen, die mit der gleichen Menge Treibstoff weiter fliegen können. Die Technologie macht auch die Kohlenstoffemissionen überflüssig, die durch den Transport von Teilen rund um die Welt entstehen. Stattdessen können Unternehmen sofort CAD-Dateien senden, die von Druckern überall auf der Welt verwendet werden können.
3D-Drucker haben auch einen wesentlich geringeren Materialverlust während des Herstellungsprozesses als z. B. bei der maschinellen Bearbeitung, bei der bis zu 98 % eines Metallblocks abgetragen werden können.
In engem Zusammenhang mit der nachhaltigeren Entwicklung der Luft- und Raumfahrtindustrie steht die Einführung von batteriebetriebenen Flugzeugen. Diese Entwicklung hat sowohl bei Start-ups als auch bei etablierten Marktführern wie Airbus und Rolls-Royce große Aufmerksamkeit erregt.
Leichte 3D-gedruckte Teile können dazu beitragen, das zusätzliche Gewicht der Batterien zu kompensieren und das Gesamtgewicht des Flugzeugs zu reduzieren, was wiederum zu einer Erhöhung der potenziellen Reichweite beiträgt.
KLEINFLUGZEUG
Alle Vorteile, die der 3D-Druck in der Luft- und Raumfahrt für Passagierflugzeuge bietet, gelten auch für kleinere Flugzeuge wie Satelliten, Weltraumraketen, unbemannte Luftfahrzeuge (UAVs) und Drohnen.
Die Hersteller von Kleinflugzeugen setzen zunehmend auf den 3D-Druck statt auf herkömmliche Fertigungsmethoden, um die boomende Nachfrage zu befriedigen.
Der Einsatz von Drohnen beispielsweise ist in den letzten Jahren sprunghaft angestiegen. Es wird erwartet, dass der Markt bis 2025 ein Volumen von mehr als 60 Mrd. US-Dollar erreichen wird, während es 2018 noch weniger als 5 Mrd. US-Dollar waren.
Dank des 3D-Drucks werden Drohnen immer leichter, schneller und flexibler und können ein breiteres Spektrum von Anwendungen ausführen. Außerdem können Drohnenkonstruktionen schnell, einfach und kostengünstig an spezifische Kundenerwartungen und -anforderungen angepasst werden.
3D-GEDRUCKTE TRAGFLÄCHEN
Tragflächen sind ein grundlegender Bestandteil eines Flugzeugs, stellen jedoch eine Reihe von Herausforderungen bei der Herstellung dar. Sie gehören zu den technisch komplexesten Flugzeugstrukturen und sind aufgrund ihrer Größe schwer in einer Fabrik zu manövrieren und zu bearbeiten.
In mehreren Ländern laufen Versuche, um herauszufinden, ob mit Hilfe des 3D-Drucks in der Luft- und Raumfahrt leichtere Tragflächenkomponenten hergestellt werden können, die für den Bau einer aerodynamischeren Tragflächenstruktur zu geringeren Produktionskosten verwendet werden können. Solche Innovationen würden dazu beitragen, die Treibstoffeffizienz und die Kosteneinsparungen weiter zu steigern.
Ein Team von NASA- und MIT-Ingenieuren hat eine "radikal" neue Art von Flugzeugflügeln gebaut und getestet, die aus Hunderten von identischen Dreiecken mit streichholzähnlichen Streben bestehen. Diese winzigen Baugruppen werden miteinander verschraubt und bilden ein offenes, leichtes Gittergerüst, das anschließend mit einer dünnen Polymerschicht überzogen wird.
Der daraus resultierende Flügel ist viel leichter und energieeffizienter als herkömmliche Konstruktionen aus Metall oder Verbundwerkstoffen, so die Forscher. Die Innovation könnte die Effizienz der Flugzeugproduktion, des Flugs und der Wartung erheblich steigern und auch andere Anwendungen finden, wie z. B. die flügelähnlichen Blätter von Windkraftanlagen.
Lufttaxis für das tägliche Leben
Bevölkerungswachstum, Verstädterung und unterfinanzierte Infrastrukturen führen dazu, dass die Verkehrssysteme in vielen Städten an ihre Grenzen stoßen und die Bewohner mit überlasteten Straßen, längeren Pendelzeiten und geringerer Lebensqualität konfrontiert sind. Diese Situation hat der Entwicklung alternativer Verkehrsmittel wie Lufttaxis neuen Auftrieb gegeben.
Joby Aviation ist ein in Kalifornien ansässiger Pionier in der Entwicklung von eVTOL-Flugzeugen (Electric Vertical Take-off and Landing Vehicles), also Lufttaxis. Das vollelektrische Flugzeug legt mit einer einzigen Ladung 150 Meilen zurück und ermöglicht es einem Piloten und vier Passagieren, den Stau unter ihnen emissionsfrei zu überwinden.
Das Flugzeug könnte nicht nur in bewohnten Gebieten eingesetzt werden, sondern auch dazu beitragen, die Anbindung unterversorgter ländlicher Gemeinden zu verbessern.
Im Mai 2022 erhielt Joby die erste von drei Genehmigungen - ein Part 135 Air Carrier Certificate -, die die Federal Aviation Administration für den Betrieb seines eVTOL-Flugzeugs als Lufttaxidienst in den Vereinigten Staaten benötigt.
Das Unternehmen arbeitet derzeit an den beiden verbleibenden Zulassungen - einer Musterzulassung und einer Produktionszulassung - und erwartet, seinen Uber-ähnlichen Lufttaxidienst 2024 zu starten.
Einem Sprecher zufolge ist der 3D-Druck für die Luft- und Raumfahrt - insbesondere für Metallteile - "entscheidend" für die Fertigungsprozesse des Unternehmens, das seine Produktion hochfahren will. Der Schlüssel dazu ist die Art und Weise, wie Job kundenspezifische Endpunktsoftware mit CAD-Lösungen kombiniert, um einen robusten Arbeitsablauf mit nur einer einzigen, unveränderlichen Datendatei für die Zertifizierung von additiv gefertigten Metallkomponenten zu schaffen.
Was sind die Grenzen des 3D-Drucks in der Luft- und Raumfahrt?
MANGELNDE VERTRAUTHEIT
Obwohl der 3D-Druck in der Luft- und Raumfahrt immer weiter verbreitet ist, ist er noch nicht allgegenwärtig - zumindest außerhalb des Prototypenbaus. Diese Zeit könnte kommen, und zwar möglicherweise früher als erwartet, aber im Moment ist die Technologie vielen Unternehmen noch unbekannt.
Die Komplexität und die strengen Standards, die mit der Herstellung von Teilen für die Luft- und Raumfahrt verbunden sind, bedeuten, dass das Ersetzen der bewährten konventionellen Bearbeitung durch etwas Neues ein Risiko darstellt, mit dem sich einige Vorstandsetagen nicht anfreunden können.
GROSSE VOLUMEN
In vielen Fällen kann der 3D-Druck in der Luft- und Raumfahrt ein einzelnes Teil oder eine kleine Serie von Teilen schneller und effizienter herstellen als herkömmliche Fertigungsmethoden. Allerdings kann jede Maschine nur eine bestimmte Anzahl von Objekten gleichzeitig drucken, je nach Maschinengröße und Objekt, und ist daher möglicherweise nicht die geeignetste oder kostengünstigste Methode für große Produktionsserien.
TEILGRÖSSE
3D-Drucker haben inhärente Größenbeschränkungen, die es ihnen unmöglich machen, große Teile zu produzieren. In einigen Fällen können mehrere kleinere Teile zusammengefügt werden, was jedoch nicht immer eine ideale Lösung darstellt.
Die Hersteller von 3D-Druckern arbeiten daran, die Größenbeschränkungen bestehender Geräte zu überwinden, indem sie beispielsweise in einer offenen Umgebung ohne die Barriere drucken, die in typischen Druckkammern vorhanden ist.
UNEINHEITLICHE QUALITÄT
3D-Drucker können noch nicht jedes Mal perfekte Ergebnisse drucken. Die Fehlerquote hängt von der Maschine, dem verwendeten Material und dem zu druckenden Objekt ab. Auch das Entfernen von Oberflächenunregelmäßigkeiten oder -strukturen kann zusätzliche manuelle Bearbeitungsschritte erfordern, um das gewünschte Ergebnis zu erzielen.
Die Fehlerquoten und die Nachbearbeitung werden sich wahrscheinlich verringern, wenn die 3D-Drucker besser werden und die Menschen sich mit der Technologie besser vertraut machen.
Erhalten Sie sekundenschnell Angebote für Ihre Bauteile