Materialextrusion – FDM
Entdecken Sie, wie die Materialextrusion, ein 3D-Druckverfahren, auch bekannt als FDM, funktioniert.
Einführung in die Materialextrusion - FDM
Bei der 3D-Printing-Technologie der Materialextrusion wird ein kontinuierlicher Glühfaden aus einem thermoplastischen Material als Basismaterial verwendet. Das Filament wird von einer Spule durch einen sich bewegenden, beheizten Drucker-Extruderkopf gespeist, der oft kurz Extruder genannt wird. Das geschmolzene Material wird aus der Extruderdüse gepresst und zuerst auf einer 3D-Printing-Plattform abgelegt, die für zusätzliche Adhäsion erhitzt werden kann. Nach Abschluss der ersten Schicht werden Extruder und Plattform in einem Schritt getrennt und die zweite Schicht kann dann direkt auf das wachsende Werkstück platziert werden. Der Extruderkopf wird computergesteuert bewegt. Mindestens drei Achsen sind erforderlich, damit sich der Extruder in kartesischen Architekturen bewegen kann, aber auch Polar- und Deltasysteme werden immer beliebter. Eine Schicht wird auf einer vorherigen Schicht abgelegt, bis die Verarbeitung des Objekts abgeschlossen ist.
Die Materialextrusion wird als Fused Filament Fabrication (FFF) bezeichnet und ist einer der beliebtesten Prozesse für das 3D Printing in Hobbyqualität. Der proprietäre Begriff Fused Deposition Modeling (FDM) wurde Ende der 1980er Jahre von S. Scott Crump geprägt und 1990 vom Stratasys-Unternehmen vermarktet. Mit dem Ablauf des Patents dieser Technologie gibt es jetzt eine große Open-Source-Entwicklungsgemeinschaft namens RepRap sowie kommerzielle und DIY-Varianten, die diese Art von 3D-Printing-Technologie nutzen. Dies hat zu einer messbaren Preissenkung geführt. Die Materialextrusionsmethode weist jedoch Größengenauigkeitsbeschränkungen auf und ist sehr anisotrop.
Materialextrusion and Materialien
Eine Vielzahl von Materialien kann extrudiert werden, die beliebtesten sind Thermoplaste, wie z. B. Acrylnitril-Butadien-Styrol (ABS), Polylactidsäure (PLA), schlagfestes Polystyrol (HIPS), thermoplastisches Polyurethan (TPU), aliphatische Polyamide (PA, auch als Nylon bezeichnet) und seit kurzem auch Hochleistungskunststoffe wie Polyetheretherketon (PEEK) oder Polyetherimid (PEI). Darüber hinaus können pastöse Materialien wie Keramik, Beton und Schokolade mit dieser 3D-Printing-Technik extrudiert werden.
Als es möglich wurde, einen 3D-Drucker mit mehreren Extrudern auszustatten, um den Herstellungsprozess zu beschleunigen oder mehrere Materialien zu verwenden, entstanden Möglichkeiten zur Verarbeitung von Verbundwerkstoffen. Die Composite Filament Fabrication (CFF) ist eine von ihnen. Dieser Begriff wurde vom Unternehmen Markforged erschaffen und bei dem Verfahren werden zwei Druckdüsen verwendet. Eine Düse arbeitet nach dem typischen Materialextrusionsprozess; sie legt einen Kunststofffaden ab, der die Außenhülle und die Innenmatrix des Teils bildet. Die zweite Düse formt auf jeder Schicht einen durchgehenden Strang aus Verbundfasern (aus Carbon, Fiberglas oder Kevlar). Diese durchgängigen Stränge aus Verbundfasern in gedruckten 3D-Teilen verleihen dem fertigen Objekt eine Stärke, die mit Teilen aus Metall vergleichbar ist. Neben der Verwendung von Verbundwerkstoffen für starke Teile kann die Strategie zum Ablegen von Schichten die Festigkeit von Teilen beeinflussen. Markforged unterscheidet zwei Strategien: isotrope Faserfüllung oder konzentrische Faserfüllung.
Selbst Verbundstoffe können mit der Materialextrusionstechnik auf Maschinen mit nur einem Extruder in 3D gedruckt werden. Die einzige Bedingung ist, dass das Grundmaterial (ein Thermoplast) in ausreichender Menge vorhanden ist, um eine Fusion zwischen den Schichten zu gewährleisten. Daher machte eine Mischung aus zwei Materialien in einem einzigen Filament den 3D-Druck von Holz (in PLA eingebettete Holzpartikel), Metall (in Thermoplast eingebettete Metallpartikel) und sogar Kohlenstoff (in Thermoplast eingebettete Kohlenstofffasern) möglich.
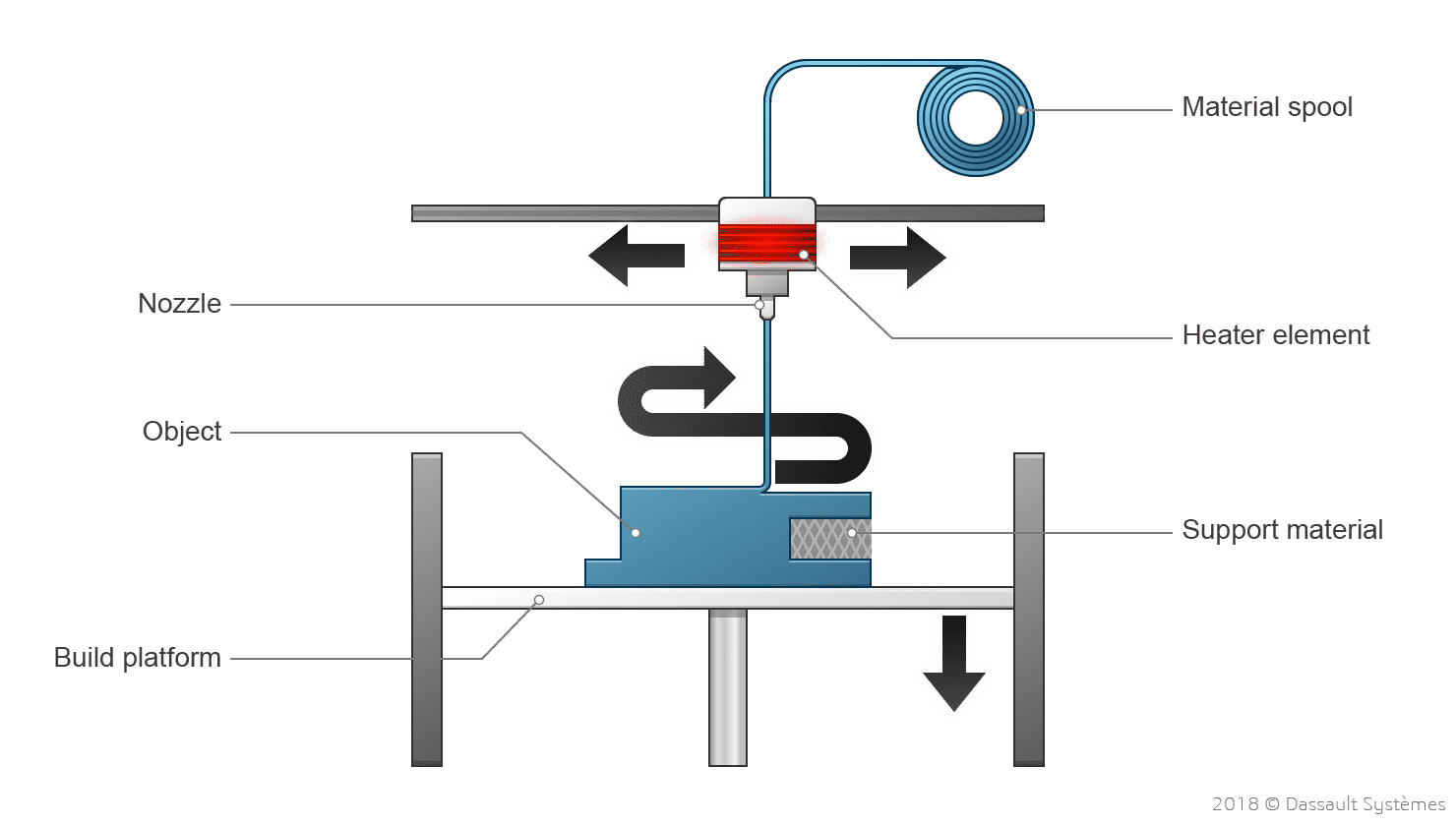
Entdecken Sie, wie Materialextrusion mit Bombyx funktioniert
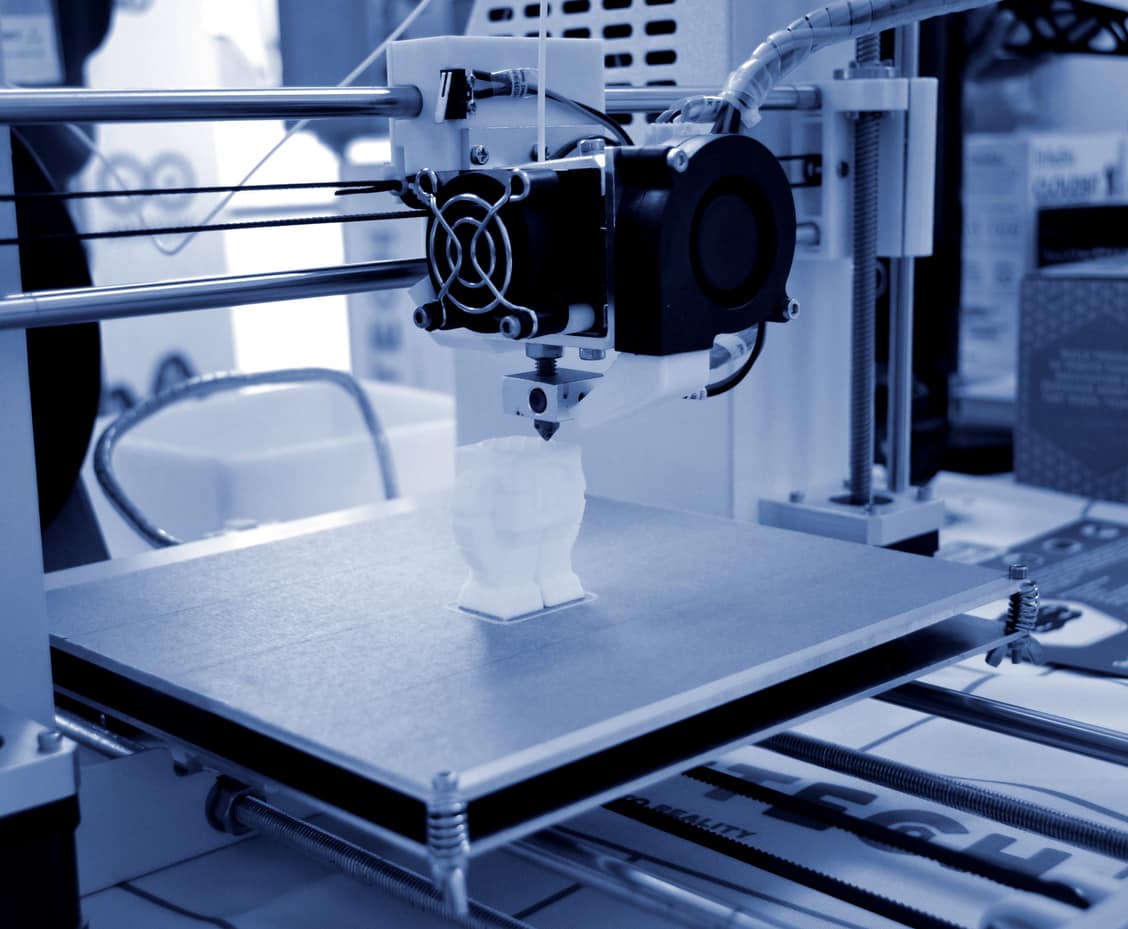
Erhalten Sie sekundenschnell Angebote für Ihre Bauteile