Eloxierung
Erfahren Sie mehr über die Eloxierung, ein Endbearbeitungsverfahren, wie es funktioniert und welche Verwendungsmöglichkeiten es in der Industrie gibt.
Einführung in die Eloxierung
Eine Eloxierung wird durchgeführt, um die Dicke der natürlichen Oxidschichten auf der Oberfläche von Metallteilen zu erhöhen. Sie wird am häufigsten auf Aluminiumlegierungssubstrate angewendet, kann aber auch auf Titan, Zink, Magnesium, Niobium, Zirkonium, Hafnium und Tantal aufgetragen werden. Beim Eloxierungsprozess wird elektrolytische Passivierung eingesetzt, um die gewünschten Eigenschaften wie Korrosions- und Verschleißfestigkeit, bessere Haftung für Farbe und Klebstoff oder ästhetische Effekte zu erreichen. Für ästhetische Effekte ermöglichen dicke poröse Beschichtungen die Aufnahme eines Farbstoffs, während dünne transparente Beschichtungen Störungseffekte hinzufügen können, um Licht zu reflektieren.
Bei der Eloxierung bildet das Aluminiumsubstrat die Anodenelektrode eines elektrischen Schaltkreises. Die Eloxierung wird ebenfalls eingesetzt, um das Festfressen oder Abnutzen von Gewindekomponenten zu verhindern und dielektrische Folien für Elektrolytkondensatoren herzustellen. Die mikroskopische Struktur eines Werkstücks sowie die Kristallstruktur des Metalls in der Nähe der Oberfläche erfahren bei der Eloxierung Veränderungen. Dickflüssige Beschichtungen erfordern in der Regel einen Dichtungsprozess, um Korrosion aufgrund ihrer porösen Eigenschaften zu verhindern. Eloxalschichten sind vorteilhaft, da sie eine höhere Festigkeit und bessere Klebeeigenschaften aufweisen als die meisten Arten von Metallbeschichtungen. Sie sind jedoch auch spröder, wodurch sie aufgrund von thermischer Belastung anfälliger für Risse werden.
Zu den Hauptvorteilen der Eloxierung gehören: deutlich dünnere Beschichtung als Farbe oder Pulver, extrem haltbar, hart, abriebfest und langlebig, kein Ablösen oder Absplittern, viel härtere Oberfläche als Farbe, Farbbeständigkeit, ausgezeichneter Schutz gegen Korrosion, umweltfreundlich, guter elektrischer Isolator und erschwinglich.
Geschichte der Eloxierung
In der Vergangenheit trat die Eloxierung erstmals 1923 in einem industriellen Kontext auf, um die in Wasserflugzeugen verwendeten Duralumin-Teile vor Korrosion zu schützen. Ursprünglich wurde eine Chromsäure verwendet. Dieses Verfahren wurde Bengugh-Stuart-Prozess genannt. Letztendlich führt dies zur Einführung von Schwefelsäure, die schon bald zum häufigsten Eloxierungselektrolyt wurde und es bis heute bleibt. 1923 wurde die Oxalsäure-Eloxierung in Japan patentiert und anschließend in Deutschland weit verbreitet, insbesondere für Architekturanwendungen. In den 1960er und 1970er Jahren war die eloxierte Aluminium-Extrusion ein beliebtes architektonisches Material, wurde aber durch billigere Kunststoffe und Pulverbeschichtungen ersetzt. Zuletzt wurde Phosphorsäure auf das Eloxierungsfeld angewendet, das bisher ausschließlich als Vorbehandlung für Klebstoffe und organische Farben verwendet wurde.
Die am häufigsten verwendete Eloxierungsspezifikation in den USA ist eine Spezifikation des US-Militärs. Darin werden drei Arten von Aluminiumeloxierung definiert: Chromsäureeloxierung (Typ I) und Schwefelsäureeloxierung (Typ II und III). Chromsäure ist der älteste Eloxierungsbeschichtungsprozess, während Schwefelsäure die am häufigsten verwendete Lösung in eloxierten Beschichtungen ist. Es ist auch möglich, mit organischer Säure, Phosphorsäure, Borat- und Tartrat-Bädern sowie Plasma-Elektrolytoxidation zu eloxieren.
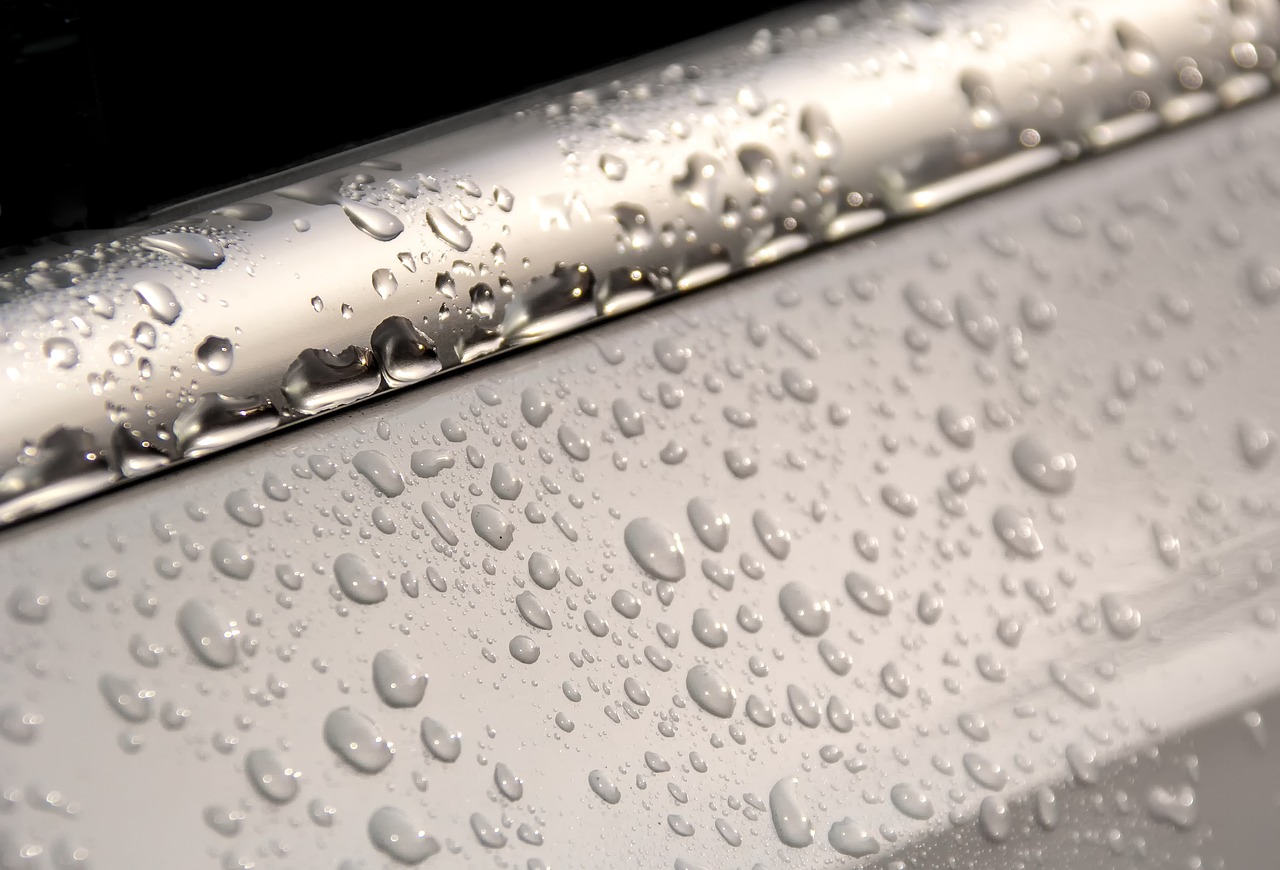
Erhalten Sie sekundenschnell Angebote für Ihre Bauteile