Decoding the ABCs of Sustainable Manufacturing
Find out everything you need to know about achieving sustainable manufacturing with Dassault Systèmes expert Prashanth Mysore.
Designing Impactful Innovation podcast - episode 18
In this episode, discover the fundamentals of sustainable manufacturing with Prashanth Mysore, global strategic business development director at Dassault Systèmes.
What are manufacturers doing to move towards sustainable production? What kind of technologies can small and medium-sized businesses use to achieve their sustainability goals? What does this mean for companies, factories and workers? And what does the future of sustainable manufacturing look like?
Tune in to find out.
Meet our speaker
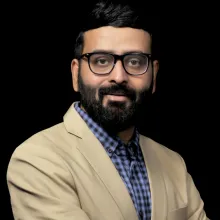
Manufacturers must adopt greater resilience and future readiness by optimizing resource usage, minimizing waste, and embracing renewable energy sources.
You can follow the "Designing Impactful Innovation" podcast on Apple podcasts, Spotify, Deezer, YouTube or by RSS.
Stay tuned!
Read the transcript
Clara: Hello and welcome to Designing Impactful Innovation. I'm Clara, your host, and today we're talking about sustainable manufacturing with Prashanth Mysore, global strategic business development director at Dassault Systèmes.
Hello Prashanth and welcome to the podcast.
Prashanth: Thank you, Clara. Good day all. Thank you for joining us on this podcast. My name is Prashanth Mysore. I'm a senior director for global strategic business development at Dassault Systèmes, and I’ve been with Dassault for a little over 24 years. I'm celebrating my 25th year in this company, a fascinating journey, being a mechanical engineer.
It’s the best place to work and I’ve been helping our customers on their digital transformation and product lifecycle management journey in multiple industry verticals. I've also supported most of our customers on the latest and greatest of technologies with Industry 4.0 or Industrial Internet of Things, which is IIoT. Defining and helping them on the journey of Factory of the Future and supply chain of the future.
And I was fortunate to be on a three-transformation journey at Dassault Systèmes, and I joined in the year 1999 when product lifecycle management was implemented. And I've had the experience of actually being on the 3DEXPERIENCE platform to bring in experience economy into the business processes. And we are on a journey of Virtual Twin Experience to optimize product, nature and life. And then we are on a sustainability journey for the next 20, 30 years. Fortunately, I've been in this company… 25th year, which is a silver jubilee year for me.
Clara: Impressive!
Prashanth, you have a lot of experience working with and advising companies that want to transform their manufacturing processes in many different industries.
Prashanth: Manufacturers globally are obviously facing multiple challenges. They're experiencing growing pressure to reduce carbon emission. That's one of the important aspects, which is the important aspects of sustainability. We need to help them reduce carbon emissions in their production processes.
The manufacturing industry is definitely characterized by disruptions, volatility, supply chain problems. Obviously, inflation really bothers them, the raw materials and increased financial costs, making it paramount for manufacturers to find innovative solutions to face the challenges ahead.
A lot of people are embarking on a journey of Industry 5.0 or smart manufacturing, but the crux of all going forward is all about sustainability. It's all about sustainable manufacturing: reduce, reuse, recycle. That's the mantra for most of the manufacturing and supply chain companies. And the path forward is clear. Manufacturers must adopt greater resilience and future readiness by optimizing resource usage, minimizing waste, and embracing renewable energy sources like wind and solar. That's going to be mandatory from now on.
But the difficulty lies in how do you simultaneously embark on profitability as well by having environmental sustainability and governance goals. Yeah, we'll have a lot of interesting stories to share about how we work with our customers to help them on their Factory of the Future journey to bring in sustainable manufacturing.
Prashanth: So, sustainability is not a passing by topic, right? Sustainability is imperative. Sustainability has to be in the culture of any organization that's going forward in the next 20, 30 years. All products, all production processes, every business process will have sustainability as the most infrastructure to really achieve carbon neutral or carbon footprint management, right?
Reducing waste production is an important step in achieving most sustainable manufacturing practices. Obviously, manufacturers, we have heard about lean manufacturing like 30, 40 years ago, the Japanese have invented that. And still lean manufacturing is really prevalent.
Just to give you some numbers, approximately 300 million tons of plastic waste is produced year on year by manufacturers. Obviously, they're looking at implementing waste reduction programs, circular processes, circular economy, designing of products for sustainability, and then implementing lean manufacturing principles, as I mentioned, like 30 to 40 years ago, how the Japanese have actually started that.
But now adoption of technology is really helping most of our customer partners on their journey towards sustainability. How are we starting this? We're starting at defining the product itself: better material, lean design, lean utilization of materials, and addressing even how the materials can come back to the recycling process with much better circularity processes.
You know, these are the things which we can actually define using technology. This is where system simulation, system modeling, and all of them are really helping them in terms of lifecycle assessment of manufacturing processes.
We started with product lifecycle management way back in ‘99, when sustainability was well defined along with lean manufacturing, when we introduced the Virtual Twin Experience, which is all about validating your sustainable manufacturing processes before you actually implement them in your shop floor. It can be robotics and automation processes. It can be additive manufacturing. It can be lean flow of materials within the shop floor so that you can optimize production processes.
Yeah, there are multiple ways and means to be on sustainable manufacturing practices, but I'll lay out more in detail in a subsequent part of this podcast.
Prashanth: It's all about acronyms, right? We have heard about the three R's: Reduce, Reuse, and Recycle. There are also three P's: People, Planet, and Profit. And added to that, there are three C's, which is Communicate, Collaborate, and Contextualize, right? These are all acronyms.
Leaving acronyms apart, what does it take for a company of any scale? It could be small and medium-enterprise companies to large transformation companies or OEMs.
All of them can have a methodical process, a stepwise deployment or option of business practices, of best practices to be on a sustainable manufacturing journey. So we have defined these five steps, and we have also helped multiple manufacturers and supply chain companies on their journey to be on a resilient supply chain or a Factory of the Future journey.
So first and foremost is what we actually offer as the Virtual Twin Experience. It's a real time virtual representation of a product, manufacturing or supply chain that can be used to model, visualize, predict, and provide feedback. That's an important first step: being on a Virtual Twin Experience journey.
And the second important aspect is all about optimization, business process optimization, which is, just definitely backed by technologies like mathematical approach for optimization, for decision-making to get the best outcome under conditions of constraints, KPI-based optimization, constraint-based optimization, which could be schedules, which could be resources, manpower, supply chain, logistics, and all of them. And we have also helped in a smart and autonomous integration into these automation processes. That's the second step. How do you optimize your business process?
The third important aspect is all about actual adoption of technology. We've heard about data, right? We’ve talked about artificial intelligence, machine learning. Obviously, manufacturers have more and more data than before, which makes artificial intelligence and machine learning ripe for disruption – this is the term which I want to use. And AI and ML is a game changer for manufacturing supply chain and it has the potential to offer CAPEX-free productivity improvements. This is where the data and AI come into picture.
And the fourth important aspect is about continuous improvement and real-time operations. And continuous improvement has always been there. We have had Kaizen as one of the lean manufacturing principles as continuous improvement. But how do you do the continuous improvement through real-time operations? It’s what entrepreneurs and enterprise business processes are enabling: greater visibility and easy access to information for all stakeholders, right? The visibility and the flexibility there.
And the last but not the least is about: you need to have picture-perfect collaboration. A systematic approach is required to effectively and inclusively consider multiple perspectives and decisions and work efficiently with all the stakeholders, which can be achieved through a platform kind of a concept. Platform technology, platform business processes, efficiently helps in collaboration so that the lean principles can be adopted and the solution enables teams to be on a better journey to optimize cost, optimize time and optimize resources.
So these are the five steps which we've been working on with multiple transformation companies.
Clara: So we've seen the ABCs of sustainability, right? The three Cs, the three Ps, the three Rs, and the implementation steps. And those are more about the bigger picture.
Prashanth: This is where we work as a framework with most of the manufacturers. It's not like one size fits all. You have newer factories and newer facilities which are coming up. We consider them as greenfield facilities. And bigger challenges with existing facilities, which are brownfield facilities, like existing infrastructure, existing machines, existing factory layout.
And we do have the best practices for both. So, if you want to be on a sustainable manufacturing process on an existing facility, what are we trying to achieve? We do have this principle of “let's model the existing facility”. Let's model the existing factory so that you model your as-is process off your existing manufacturing throughput, existing manufacturing productivity, right?
Then we will define the KPIs to be on a sustainable manufacturing journey. What are those KPIs? Carbon footprint management, reduction of raw material, optimization of utilization of manpower. And we also talk about these five M's. Again, an acronym, sorry for that. Manpower, Machineries, Materials, Methods, and Measurement.
This is an important step, right? This is where the tools and technologies would really come into picture to optimize these processes. We did as-is processes using modeling of our existing facility. The to-be process is all about optimizing your manufacturing processes, as I said, 5M.
How do we do this? We use this technology, Virtual Twin Experience. The Virtual Twin Experience is to bring in and validate changes into your existing manufacturing facility so that you're actually monitoring and even optimizing your key principles or KPIs of reduction of raw material, energy consumption, optimal utilization of material and manpower, and all of them through the best principles of lean manufacturing and optimization technology.
Prashanth: Workforce is an important aspect, right? As I said in my three Ps – people, planet, and profit – it's all about people, right? Sustainable manufacturing is a fascinating journey, even for workers, mainly because of adoption of technologies and improvements in their health and safety conditions, right?
Sustainable manufacturing will bring in a great place to work, a fun place to work in the manufacturing environment, because it's all about lean, it's going to be green, and there is a purpose in actually achieving the sustainability here.
And how are we doing this? Adoption of technology. The technologies like augmented reality, the virtual reality, a data-driven environment, ChatGPTs, assisted reality, all of them will help workforce – it could be workforce of the future or existing workforce – to be on this journey of sustainability by adoption of these technologies, right?
That's where I would bring in the technology as a key principle in transforming sustainable actions or sustainability deployments at the factory, where workers would get benefited in terms of improving health and safety, improving working conditions and enjoyable workplace.
Clara: Got it. So, the technology is the key, right?
Prashanth: It is. It is all about PPT. No, it's not about a PowerPoint presentation. PPT is about people, process, and technology. Again, an acronym.
Clara: Yeah, we're really going to do the entire alphabet in this podcast.
Prashanth: It looks so.
Clara: So, staying on the topic of the workforce, I recently read that there were up to 600,000 unfulfilled manufacturing jobs in the US just last year. With older skilled workers retiring, the gap is getting bigger between older and younger generations.
Prashanth: You know, the manufacturing labor deficit is always a growing challenge for global manufacturers, right? It is up to the responsive and responsible leaders in manufacturing to make enabling workers their top priority. And by doing so, they can accelerate growth and value for their organization. This is mandatory, right?
They can bring in value to their organization, individuals and communities. If workforce enablement is not catching up with the latest and greatest of technologies, the industry could lose up to $11 to 12 trillion in cumulative GDP growth in the next 10 years. So it's imperative. It's mandatory.
The future of work will be a race between education, skill and technology. We have to harmonize education, skill, and technology for the new workforce. It's mandatory, right? And coming back to your question about what do we do? Why are we doing this workforce enablement now?
Why workforce of the future and why now? Because changing consumer experiences, mass customization, there's glocalization – it means global companies are trying to localize as much as possible – there’s remote management of factories through automation, there are continuous evolvement of 3D printing, NC manufacturing and robotics and automation are continuously going.
And there are a lot of smart objects, sensors and augmented reality devices. All of them are really changing the way the manufacturers actually work – and regulatory compliance, mandatory sustainability compliance, which is imperative. We need to actually bring in foolproofing of this in the manufacturing, right?
And sustainability everywhere, which we spoke about, this is where industry is evolving. And this is where the leaders who are at the forefront of their business are enabling their workers to be on an evolution journey of this industry, be it industry 3.0 to 4.0 to 5.0 now where sustainability is mandatory.
Clara: We talked about what manufacturers need to do to produce more sustainably, and I'd like to talk a little bit more about the technology you mentioned.
Prashanth: The tools and technologies are not silos. Manufacturers currently, if you go to a large manufacturer, they're already using multiple technologies: technology for design, like CAD systems, product lifecycle management, project management tools, supply chain management tools, simulation tools, and all. There are a huge or humongous amount of technologies which are already there with the manufacturers.
And on the other side of the spectrum, you also have operation technologies. You have sensors and smart objects, PLCs and SCADA. They're all there, right?
What is missing is contextualization between the existing technologies of IT landscape, which is ERPs and PLMs and 3D CADs to project management tools, with sensors and smart objects. And this is where we at Dassault Systèmes are working on the 3DEXPERIENCE platform to contextualize IT and OT, which is Information Technology and Operation Technology. I want to put it in a funny way. Between IT and OT, you need an ET. ET is Experience Technology on the 3DEXPERIENCE platform.
Clara: Got it. So contextualization is imperative to achieve sustainable manufacturing.
Prashanth: This is a simple answer: it's available to everyone. It's so democratized. With the advent of cloud and affordable IT infrastructure, anyone can be on this technology.
It's not only technology, right? We need to have best practices. We need to have standard best practices to help various types of customers or our partners.
It could be small and medium enterprises to large transformation customers that are like OEMs, original equipment manufacturers that own or operate trillion-dollar economies as well. We would help them with standard best practices, industry solution experience, industry process experience.
And we are on a journey of helping them with the value path. Value path is all about adopting the best practices to achieve their KPIs. In this case, sustainability or sustainable manufacturing. We have well defined value paths so that they can readily deploy, readily adopt some of the best practices into the sustainable manufacturing process.
Prashanth: The future is bright, the future is sustainable, our future is fun. This is an optimistic statement from an engineer like me, right? The future of manufacturing is all about resilience. The future of manufacturing is all about bringing in technology adoption, the future of manufacturing is to bring in agility and flexibility and creating the workforce of the future.
And how are we doing this? There are four different types of disruptive digital technologies that will really help the future of supply chain or the future of manufacturing.
One is commodity of IOT sensors, which has the ability to capture and process data, connect and exchange data with other systems. And we obviously have deployment of cobots in place of robots to improve the productivity of the workers.
And we spoke about the second point. We spoke about cloud computing and access to advanced algorithms, enabling organizations to derive better insights with the data, analyze, and then predict the future of manufacturing, the future of their individual enterprise, right?
And as I said, the technologies like robotics, business process management, RPA (robotic process automation), ChatGPTs, voice assistants, and chat bots, all of them are enabling automation of physical and non-physical processes, leading to a faster and more efficient processing going forward.
And as I said, I'm raising disparate IT and OT data sources into a single system mainly to define sustainable manufacturing with much better digital operational insights and business KPIs at an enterprise level, which will continue to help manufacturers on their sustainability journey.
Clara: This was a really insightful conversation, Prashanth. Thank you so much for joining us today.
Prashanth: Thanks, Clara. That was a useful conversation. And I would encourage all of our listeners to feel free to reach out to us in your journey on Factory of the Future, supply chain of the future, workforce of the future, awareness of the future, anything future requirements, please feel free to reach out to us. We will offer you an outcome-based engagement with standard business processes and best practices and value paths.
Clara: Thank you for listening to Designing Impactful Innovation. To find out more, go to 3ds.com/cloud. Don't forget to subscribe for more insights and stories from our guest experts.
Learn more
Ready to learn more?
See how the 3DEXPERIENCE platform on the cloud can transform your business. Fill out the form to get in touch with our experts.