Designing Beyond Limits: CATIA for Industrial Design
Learn about how our guest experts use CATIA on the 3DEXPERIENCE platform to bring their ideas to life, how CATIA is evolving and what the future holds for industrial design.
Designing Impactful Innovation podcast - episode 13
Two returning guests join us to share their insights into how they use CATIA for industrial design. Join Felix Rockel, CATIA Design Industry process expert senior specialist and Alain Dugousset, CATIA Core Engineering Roles Portfolio senior manager, for a fascinating discussion about the evolution of design on CATIA, how they enhance their design workflows and what they think the future of design will look like.
Meet our speakers
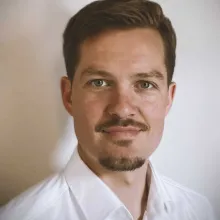
Future design has to be sustainable and it will influence the way that we design our products heavily. And also of course, the new technologies that we will have, with artificial intelligence, will have a huge influence on the design process itself.
More about Felix’s design projects on the 3DEXPERIENCE community
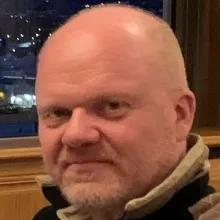
Twenty-five years ago the main challenges were to be able to design mechanical parts. If we look at what we have today, it's completely different. Now, we are able to create the complete virtual twin of a plane or a car.
More about Alain’s design projects on the 3DEXPERIENCE community
You can follow the "Designing Impactful Innovation" podcast on Apple podcasts, Spotify, Deezer, YouTube or by RSS.
Stay tuned!
Read the transcript
Clara: Hello, Alain and Felix. Welcome back to the podcast. For our listeners who might not have heard our first episode, could you please introduce yourselves?
Alain: Hello. So my name is Alain Dugousset. I’ve been working on CATIA for more than 25 years now at Dassault Systèmes and most of the time on aviation topics. And I am also very interested in innovation.
Felix: Yes my name is Felix Rockel. I haven’t worked with CATIA for such a long time as Alain – I think I’m now close to 10 years of experience with CATIA. And yeah, that's also the time that I’ve been with Dassault Systèmes in the CATIA design IPS team. I'm 35 years old and I live in Hamburg, Germany.
Clara: All right, thank you. We talked about industrial design in our previous episode and the projects you've worked on such as Tintin’s spaceship or innovative e-cars to showcase CATIA capabilities.
Felix: So I love the history that you have in CATIA, the history on each model that you create. The phrase that we use, the terminology is “associative”. CATIA is very strong in its associativity. That means that if you create a model, you can change all the parameters that you assign to generate this model at any stage.
And your whole scene tree or your whole workflow that you did after this parameter will update according to your changes. And I think this fact, or the strength of CATIA, makes it very, very useful and very strong in concept modeling because you can try out so many different variants when you first assign a parameter or create a model. You don't have to really make sure that everything is perfect yet. You can then at any time tweak and really produce the shapes that you like.
And then as well, I always use a hybrid modeling approach of subdivision surface modeling and parametric CATIA NURBS modeling. And I find that this is quite unique, this mix of using both those technologies so linked together. That's quite unique in CATIA and this makes my modeling process really fast but at the same time very intuitive, that's why I use CATIA for concept modeling.
Alain: Yes, I agree with Felix, there are a lot of good reasons to prefer CATIA in fact. The associative and parametric approach you described is a good one, Felix, clearly. But you have, I think, other very interesting things in CATIA. The first one I think is that, we have with CATIA, the best geometric core modeler available on the market.
To be honest, when you start to design something with CATIA, you know you will be able to create exact shapes, exact surfaces, and the exact geometry you want to create with high-level precision. It's one key topic and to do this, we have a lot of amazing ways of working, amazing features depending on the way you want to work.
If you want to work with a very strict structure, you can do this. If you want to have other ways – not so strict to work – you can use them. At the end you will create the same geometry, but using a different methodology. That's one point for, I will say, all the modeling, the part design, surface design.
And another topic, when you switch to product design – I would call it assembly design on my side –you have very interesting capabilities for designing in context. If you need to design a part with other parts as a context, it’s very easy with CATIA. And if you need to create links between parts, the relational design between parts is very powerful in CATIA.
So as Felix explained, you can start designing something and say “Okay, I need to change a spline, a surface, a parameter,” and then everything will update according to the new specification. And for me it's clearly a great differentiator for CATIA compared to other CAD tools, in fact.
Alain: On my side, most of the time I start choosing applications such as Natural Sketch to be able to import a picture if I need, or sketches drawn with pencil. Then I switch to a modeling application, mainly Generative Shape Design and Part Design, in order to be able to create both surfaces and solids, depending on the need.
And everything is – on my side – done in the context of assembly because most of the time when I create a product, it's not only one part. So I am working on one part with everything around it on the screen to be able to design what I want and then modify another part to come back to the one I am working on and see the impact and so on.
So for me, it's clearly very powerful to have this kind of capability. Most of the time, to be a bit more technical, I use what we are calling the “skeleton methodology” to have one part with the main specifications, main points, axis, surfaces of my design and then go into the detailed design of solid parts using this first part.
And when I can – most of the time I try to do this – I switch to 3DEXCITE to use Planets Studio and Creative Experience. Planets Studio is our “home”, directly available for the designer, and Creative Experience allows me to put my design in a real life environment. As you may have seen on some of my designs, I love to put what I am designing on the sea, in the air, with the sun moving, the clouds and so on to see what will be the final result of the design in lifelike environments.
Felix: I would say my design workflow with CATIA is pretty close and similar to what Alain has described. He uses some applications that I use, that I don't use, but I think that's also the beauty with CATIA, that you can pick and develop your own customized workflow that best fits your style of modeling and working.
So I also use reference pictures that I bring in with Natural Sketch or now we have a new application for that, Creative Design Experience. And then, I don't know, Alain, do you use Imagine & Shape: Subdivision Surface Modeling at all?
Alain: Yes, sometimes, but I am not an expert on this one. I need your help to learn this one maybe.
Felix: Yeah, why not? No problem. I’m pretty sure you can also teach me a lot of stuff, so we can exchange. This would be good. But yeah, so I use this mostly for my main surfaces, subdivision surface modeling with Imagine & Shape.
And then I do the detailing with parameters. Mainly from or in Generative Shape Design. I also do a lot of visualizations of course for renderings and stuff. I assign materials, I use Live Rendering for that sometimes. Then I use our capabilities in VR – virtual reality – so we can connect VR glasses directly to the 3DEXPERIENCE platform to review our models in virtual reality.
So I have VR glasses that I can use with my laptop. I have a quite powerful laptop that is capable of doing that. And I love that: the possibility to review in virtual reality my model that I started to design in the morning, and then in the evening already, I can walk around my, I don't know, car or house or whatever, I designed and then make decisions and instantly I'm back in CATIA and can reshape. And thanks to the history that we have in CATIA that we talked about earlier, I can instantly change certain parameters and my model will update accordingly.
And then we have an application as well for creating design presentations – Product Perception Experience – to explain a bit how the product will work, how the user will interact with the product. So, I usually create a design presentation with this in the end, with this application, in order to basically share my product with others and communicate its features.
Clara: All right. Well, thank you for sharing your workflows with us.
Felix: My first project, I think, with CATIA was designing a bridge. I collaborated with an architect office in Finland, I think. I don't really recall the name because it was like 10 years ago, but that was my first project with CATIA designing a bridge.
Alain: Yes, on my side it's a little bit different. My first project, if I really think about my first one, was in CATIA V5 to design a mechanical bracket. It's maybe not so funny, but it was even before CATIA V5 was on the market.
If I look at, let's say, more “funny” projects, my first one was to redesign on V5 a Star Wars X-Wing fighter – just for fun – and to test CATIA V5 at this time.
And on the 3DEXPERIENCE platform with CATIA I do not remember if it was the Infinity Gauntlet used by Thanos or the arc reactor of Iron Man. I think it's the last one. I think it was the arc reactor of Iron Man that I just redesigned for fun, using all the applications I mentioned just before.
Felix: Which was the first version on the platform of CATIA that you used?
Alain: Here again, same thing, one which was not on the market.
Felix: Oh yeah.
Alain: But for the Iron Man arc reactor, I think it was two or three years ago.
Felix: Oh, okay.
Alain: Maybe four.
Alain: Yes. Depending on the job you have at Dassault Systèmes and the time you may have.
Felix: Yeah, for sure.
Alain: Before this, I was designing more for aerospace and defense. It was more for customer demonstrations or this kind of thing.
Felix: Yeah, for me, when I started with CATIA, it was already on the 3DEXPERIENCE platform. That was R2015x back then on the platform. And I first learned CATIA actually on the platform and then went back to also use it in V5 afterwards.
Of course, in the beginning, I always preferred to be on the platform because that's where I learned CATIA. But then for some customer engagements, I had to learn it in V5 as well. So yeah, I learned it the “wrong way” from the platform back to V5.
Clara: So lots of different projects and ways of working! So I know you went forward and Felix went a bit backward – in a way.
Alain: You know, 25 years ago the main challenges were to be able to design mechanical parts. That's why my first project was more mechanical bracket than something funny. So it seems to be obvious today, but at that time, you know, creating the exact geometry of a mechanical part was not so simple, so easy to do.
Then if you managed to create your parts, the next challenge at this time was to be able to put them together, to create the product, to create what we are calling at this time the digital mockup of your product. It's another interesting challenge we face today. You know, again, it seems to be obvious but it was not simple at this time.
And if you managed to do this kind of thing, you were very happy to be able to launch a process to try to have a nice picture of your product. But it was only static pictures that you could have to have all the details, the rendering of your car or your plane depending on what you were working on. And it was a little bit long to have this kind of picture, to have the result. You may wait between a few minutes and several hours, depending on the complexity of the product.
If we look at what we have today, it's completely different. We are able to create, now, the complete twin of a plane or a car. And when I say the virtual twin of this kind of product, it's not only the mechanical parts or the digital mockup, it's also all the physical behaviors of the product, even if it does not exist. We are able to describe all the physical behaviors with exact mathematical equations, so it's really amazing compared to 25 years ago.
And then if you have all those parts, together with all the behaviors of your product, you're able to put it in a real time environment, to replay all those behaviors and to check that everything will be okay. For your product, and of course to check that for the final customer, the product will be the good one for him, even if you have not started the production. That's what is really amazing. You're able to test everything in a lifelike environment, real-time environment, before pushing the manufacturing button.
Felix: I find that really interesting Alain, I'm a bit jealous, I have to say. It's really cool that you were able to see, or be part of this whole process from the first steps of the cut development of products until today. That must have been nice, right? To really see every year the evolvement of the software and being part of this process. I just came in at a certain stage where it was already quite developed.
Alain: Yes. When I joined Dassault Systèmes, we were less than 1,000 people. So you can imagine today compared to the number of people we have at Dassault Systèmes. I know I was lucky on this topic!
Felix: Yeah! I'm curious, maybe in 15 years from now, I will talk in a similar fashion and will explain about the time before AI did all this automatically and some young colleague will not believe it, but yeah, let's see how it develops!
Clara: You've witnessed the shift from CATIA V5 on premise to CATIA on the 3DEXPERIENCE platform on the cloud for Alain, and Felix you've gone the other way around meaning you've gone from the cloud to on-premise.
Felix: Yes. So as you, as you said, right, so I was not really working with CATIA when it was still in V5, but now working with the 3DEXPERIENCE platform and supporting customers that work with the 3DEXPERIENCE platform on the cloud I see strong benefits using the platform for design processes.
And for me, the most obvious and important one is the collaboration that you have with CATIA on the 3DEXPERIENCE platform, where each profile that you have in the design studio, they all come together on the same platform and they can work and collaborate, working basically in parallel on the same part.
Because all the data is saved on a server on the cloud, they can collaborate and work together on the same part at the same time. Where with CATIA V5 back then where everybody had his or her own local installation on their own laptops, the collaboration was much more difficult and data had to be exchanged and stuff. So all this is made much more streamlined with the 3DEXPERIENCE platform, the collaboration.
Alain: Yes, you're right. If I can just add something: for me, using the platform on the cloud today, it means freedom because you are able to work, to retrieve your data, to work from everywhere, on several machines if you need…
It's really amazing to have this kind of capability and it's, as Felix explained, yes, you do not have to take care of your files. Everything is on the cloud so you can access it from everywhere. For me, it's a good starting point for the cloud. It's really a key added value on this capability.
And moreover, as I am dreaming with the cloud to have new services which may need, you know, some processing on the cloud. You cannot do this on your pc, but to have the capability to have new services, to check the sustainability of your design. Maybe not in real time, but almost in real time.
You know, you are working, you say “Okay, with all the information I have put in my design, please Dassault Systèmes tell me if it's sustainable or not.” And you're still working on your design and then you have the answer saying yes or no. And you’ll know what to change in your design, depending on the feedback you will have, from this kind of capability coming from the cloud.
For me, it's a dream, but I think it's not so far from what we can do and it's maybe really interesting to have this kind of capability and others coming from the cloud, with the cloud.
Felix: Yeah, this would be super cool, a super nice feature to have.
Also if I may add something, where I was talking about collaboration on the cloud. So I think our team that we have at Dassault Systèmes is a very good example of that because, for example, I'm sitting in Hamburg. Then we have a colleague sitting in Stuttgart in Germany. Then we have three colleagues actually in Paris, one colleague in Manchester. And there are so many projects that we do together. So a concept car, or recently we did a plane cabin together.
And through the cloud, we can all work on this exact same data without any data passing around. My colleague maybe doesn't know anymore, which is the latest version that he should actually work on. No, we actually work on the same data together in real time. And this works so well even though we are located all around Europe. So that's really cool and a big benefit of working with the 3DEXPERIENCE platform on the cloud.
Alain: I would say for me, the key point is clearly as Felix explained for, let's say for short term, to collaborate more together and increase the collaboration between the designer to work more closely with other people. Not only designers with designers, but designers with mechanical engineers, with the simulation specialist to check the structure capability of the design, manufacturing experts and so on. And sustainability experts of course to be sure that the dream design can become reality and of course, checking all the information needed for the cost and the impact on the planet during all the lifetime of the product.
For me it's clearly a good thing we are working on and it's clearly very important for the future, for industrial design. Then maybe we can have some AI coming to enhance all the things and allow all the users to optimize their design more quickly and take care of the Earth.
Felix: Yeah, I can totally agree with Alain. I think those topics that he mentioned, with sustainability, are definitely the main challenge for the future.
Design, future design has to be sustainable and it will influence the way that we design our products heavily. And also of course, the new technologies that we will have with artificial intelligence will have a huge influence on the design process itself.
But I think that with our 3DEXPERIENCE platform and with CATIA on the 3DEXPERIENCE platform, we are really in the right spot because we enable, with our platform, collaboration within the design studio. Between the different profiles that you have in the design studio, but also with the other departments of a company – so between the designer, the engineer and the experts for sustainability, and the manufacturing department – we can bring with our platform all those different profiles together. And you need this collaboration between those different stakeholders in order to produce sustainable products and make best use of all the new technologies that we have.
Clara: All right. So thank you so much for coming back to the podcast, Alain and Felix. This was a really interesting discussion!
Felix: Yeah. Thank you. It was as fun as last time. Thanks.
Alain: Thanks a lot!
Clara: Thank you for listening to Designing Impactful Innovation. To find out more, go to 3ds.com/cloud. Don’t forget to subscribe for more insights and stories from our guest experts!
Learn more
Ready to learn more?
See how the 3DEXPERIENCE platform on the cloud can transform your business. Fill out the form to get in touch with our experts.