Tree Composites
Tree Composites uses the Design for Sea industry solution experience to design, test and bring to life its wrapped composite joints for offshore structures.
Composite joints strengthen offshore structures
Offshore energy structures like wind turbines are exposed to some of the harshest conditions on Earth. Anchored to the seabed, their foundations are made from huge steel tubes that are welded together. Wind, waves and corrosion take a heavy toll on these welded joints, making them susceptible to fatigue damage. Over time, even the slightest crack could jeopardize the entire structure. A groundbreaking innovation from Tree Composites promises to solve this issue. Compared to traditional steel welds, the company has proven through testing that its wrapped composite joint concept has a significantly longer fatigue life, marking a revolution in offshore wind energy construction and durability.
The wrapped composite joint is designed to enhance the sustainability and cost-effectiveness of offshore wind projects. It was invented by Marko Pavlovic, assistant professor in Steel and Composite Structures at Delft University of Technology (TU Delft) in the Netherlands, who was inspired by the way that a 300-year-old tree grew around a supporting steel tubular structure. Pavlovic realized that by wrapping composite material around steel tubes, it would be possible to reinforce the huge foundational structures for offshore wind turbines and reduce the amount of steel used in the process – leading to stronger, lighter structures and more efficient manufacturing processes.
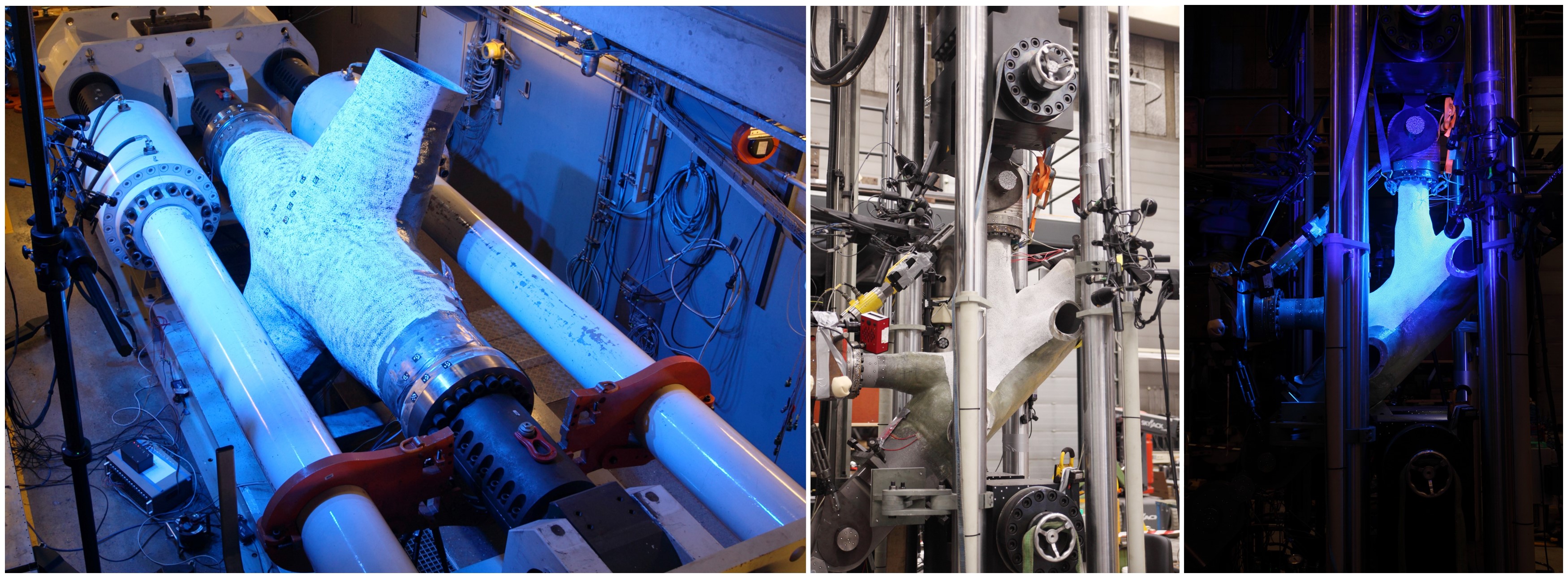
Challenge
Developed at TU Delft, the first prototype wrapped composite joint was built in 2017 and has since gone through hundreds of tests to characterize its behavior and prove it outperforms steel welds. Tree Composites was then founded to bring the technology to market and introduce it in full-scale applications.
As a startup, the company needed a powerful and scalable yet affordable design and simulation platform to refine the wrapped composite joint. It needed the capabilities to accurately test, model and calculate the joint’s properties for real-world, full-scale applications, doing as much as possible in the virtual world first ahead of physical prototype production.
The biggest challenge for wrapped composite joint innovation is gaining acceptance in the offshore industry. Dassault Systèmes’ virtual testing and analysis solutions are crucial for proving the wrapped composite joint’s viability and accelerating its adoption.
Solution
Tree Composites joined Dassault Systèmes’ 3DEXPERIENCE® for Startups program, taking advantage of CATIA and SIMULIA within a hybrid cloud setup of the 3DEXPERIENCE platform. All simulations and virtual testing are carried out on premise. Meanwhile all design work and product development data is hosted and managed in the platform on the cloud.
The company uses the platform-based modeling and simulation (MODSIM) approach for all composite design, testing and analysis. Within the centralized environment, engineers can model the joint and then carry out realistic simulation using finite element analysis (FEA), which considers everything from structural performance and durability to dynamic stress and failure rates.
Tree Composites’ technology partner, 4RealSim, delivers all simulation support, providing the strong technical knowhow to best leverage Abaqus, SIMULIA’s finite element analysis solution for resolving complex engineering challenges. Working closely with Dassault Systèmes, the startup is now looking at how it can harness DELMIA to scale and optimize the composites manufacturing process.
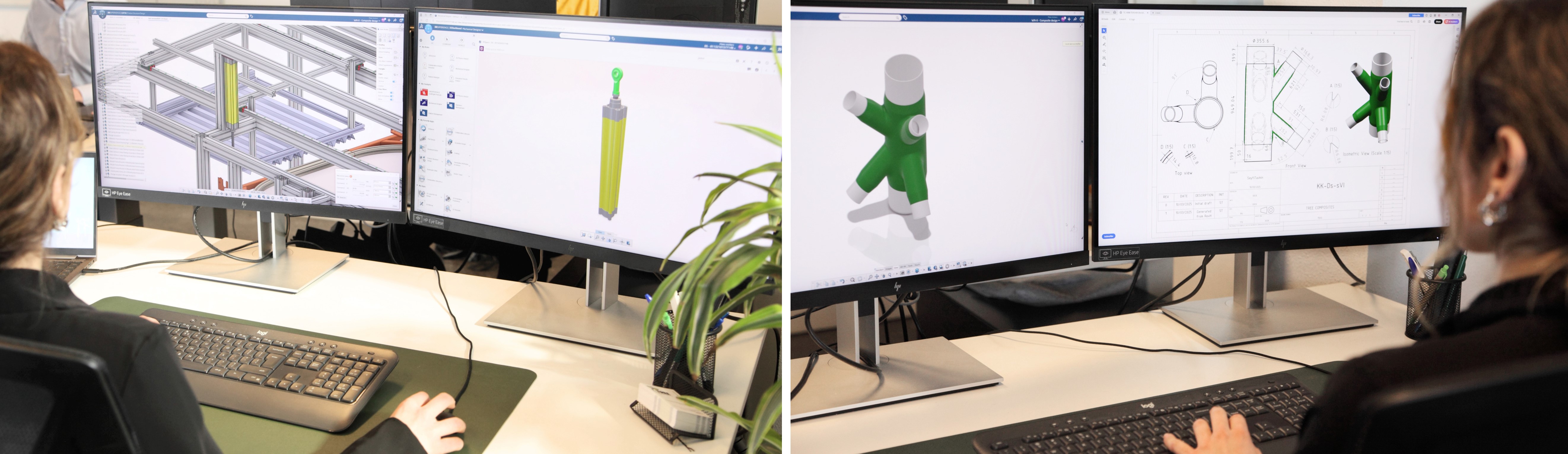
Benefits
Using the 3DEXPERIENCE platform on the cloud, Tree Composites successfully engineered, tested and produced the first full-scale wrapped composite joint for the WrapNode-I project, measuring 2.6 meters tall and 10 meters wide. It’s now moving ahead with the WrapNode-II project. This will involve constructing and assembling composite joints within an actual onshore jacket support structure for extensive testing, ahead of commercial implementation.
Having access to comprehensive MODSIM capabilities within a single environment has proven crucial for demonstrating the viability of the wrapped composite joints and moving to large- and full-scale component testing. Being able to simulate the product in all manner of scenarios and refine it in the virtual world is helping to shorten development time, reduce costly physical prototype manufacturing, and lower raw material usage including associated waste.
The 3DEXPERIENCE for Startups program offers Tree Composites a low risk, high reward opportunity to take advantage of enterprise-level, industry leading software solutions. Tree Composites continues to test and optimize its innovation and benefits from the hands-on support from 4RealSim and Dassault Systèmes, confident in the knowledge that its technology roadmap will match its evolution as a business and deliver everything it needs to launch the wrapped composite joint to market.
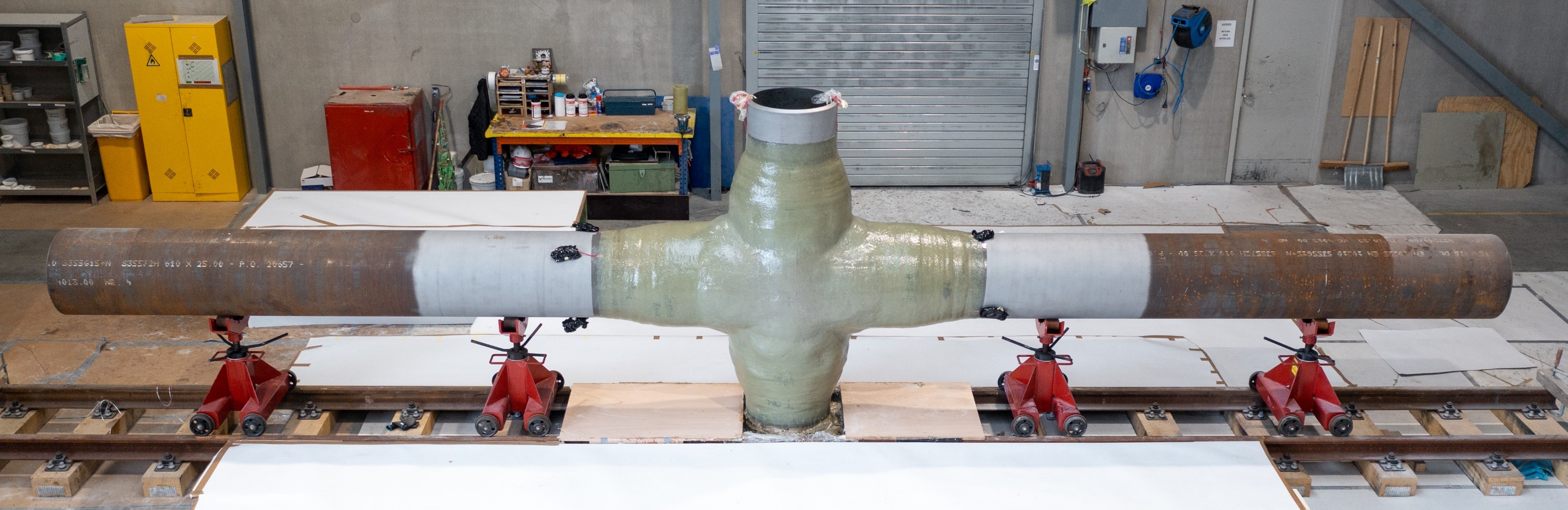
Discover more about the Designed for Sea industry solution experience.
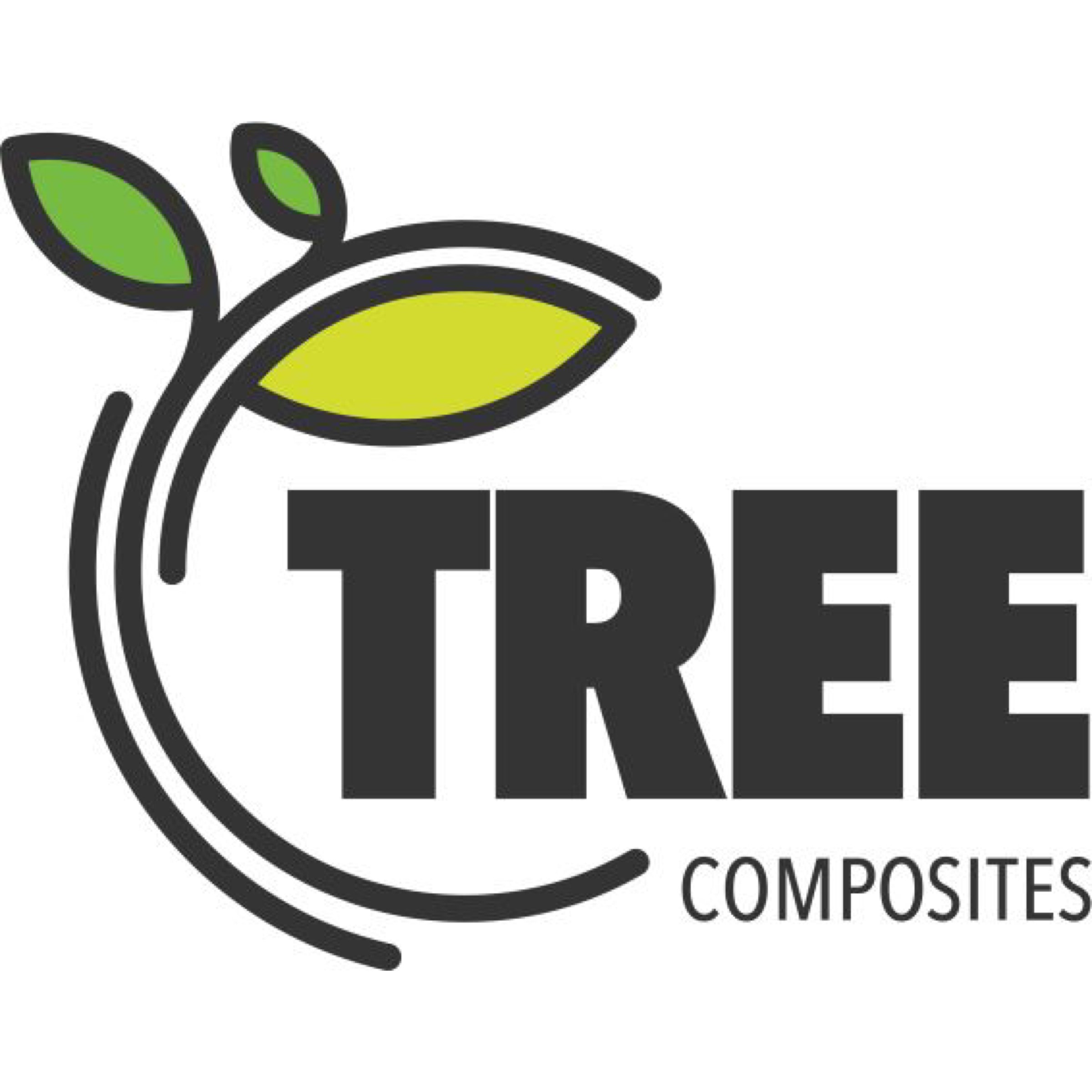
Focus on Tree Composites
Based in the Netherlands, Tree Composites is the company behind wrapped composite joints, a novel technology based on composites as an alternative to the complex welded joints in multi-membered tubular structures. Tree Composites provide solutions to realize dynamically loaded structures with less material and at the same time increase the production rate at the construction yard.
For more information: https://www.treecomposites.com
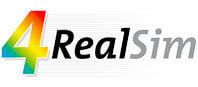
Focus on 4RealSim
With over 100 years of combined experience, 4RealSim specializes in delivering Dassault Systèmes SIMULIA solutions. Its expertise spans finite element analysis, fatigue, optimization and aeroacoustics, serving key industries such as aerospace and defense, transportation and mobility, and marine and offshore. In addition to software solutions, 4RealSim provides high-quality finite element engineering services to assess, validate, and optimize the performance of products, assemblies, and processes.
For more information: https://www.4realsim.com