Industrial Robots, Machine Tools and 3D Printers
Driving Sustainable Innovation in Robotics, Machine Tools, and 3D Printing for Manufacturing Leadership.
What Trends Are Changing the Industrial Robots, Machine Tools and 3D Printers Landscape?
The landscape of Industrial Robots, Machine Tools, and 3D Printers is undergoing a profound transformation. AI-driven automation, collaborative robots (cobots) fostering safer human-machine synergy, and advancements in additive manufacturing for unparalleled customization are revolutionizing the industry. Coupled with a strong focus on sustainability—through energy-efficient processes, recyclable materials, and reduced waste—these innovations are enabling greater efficiency, precision, and adaptability while driving environmentally responsible manufacturing practices.
- Highly Customized Demand
- Connected and Autonomous Systems
- Competitive Demands
- From Selling Machines to Selling Services
- Regulations and Standards
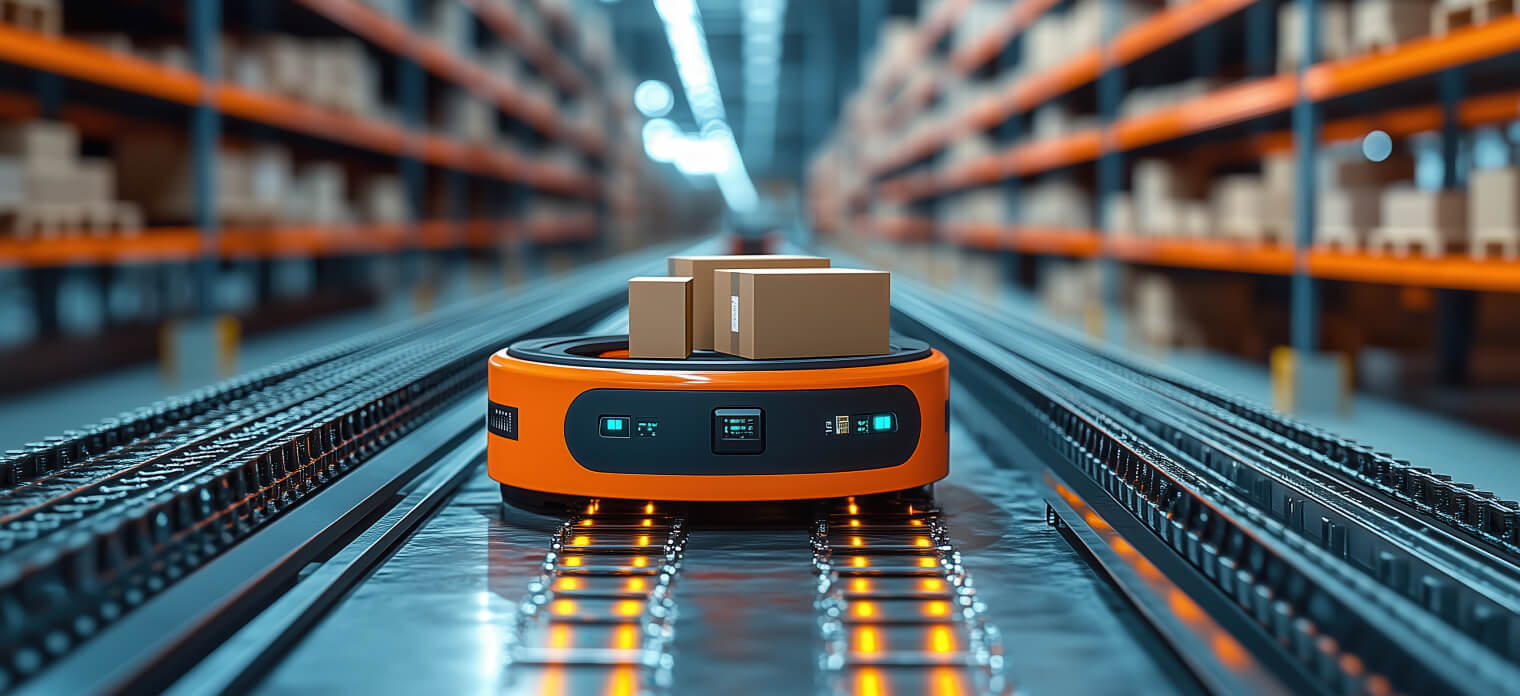
The megatrend of consumer individualization is fundamentally reshaping the landscape for original equipment manufacturers (OEMs) of industrial robots and machine tools. With customer expectations shifting toward products tailored to specific needs and constraints, the amount of unique and highly configured offerings is surging.
To thrive in this environment, manufacturers must provide an extensively diversified product portfolio that can address volatile market demands. This creates significant challenges for after sales services: as companies’ installed bases become more dispersed, their capacity to provide standardized products and spare parts diminishes.
Industrial robot and machine tool OEMs who want to maintain their competitive edge must develop fully flexible, modular, and intelligent production equipment.
This equipment must not only adapt to a variety of applications but also easily integrate into diverse operational environments, ensuring long-term value for customers while maintaining efficiency in serviceability and support.
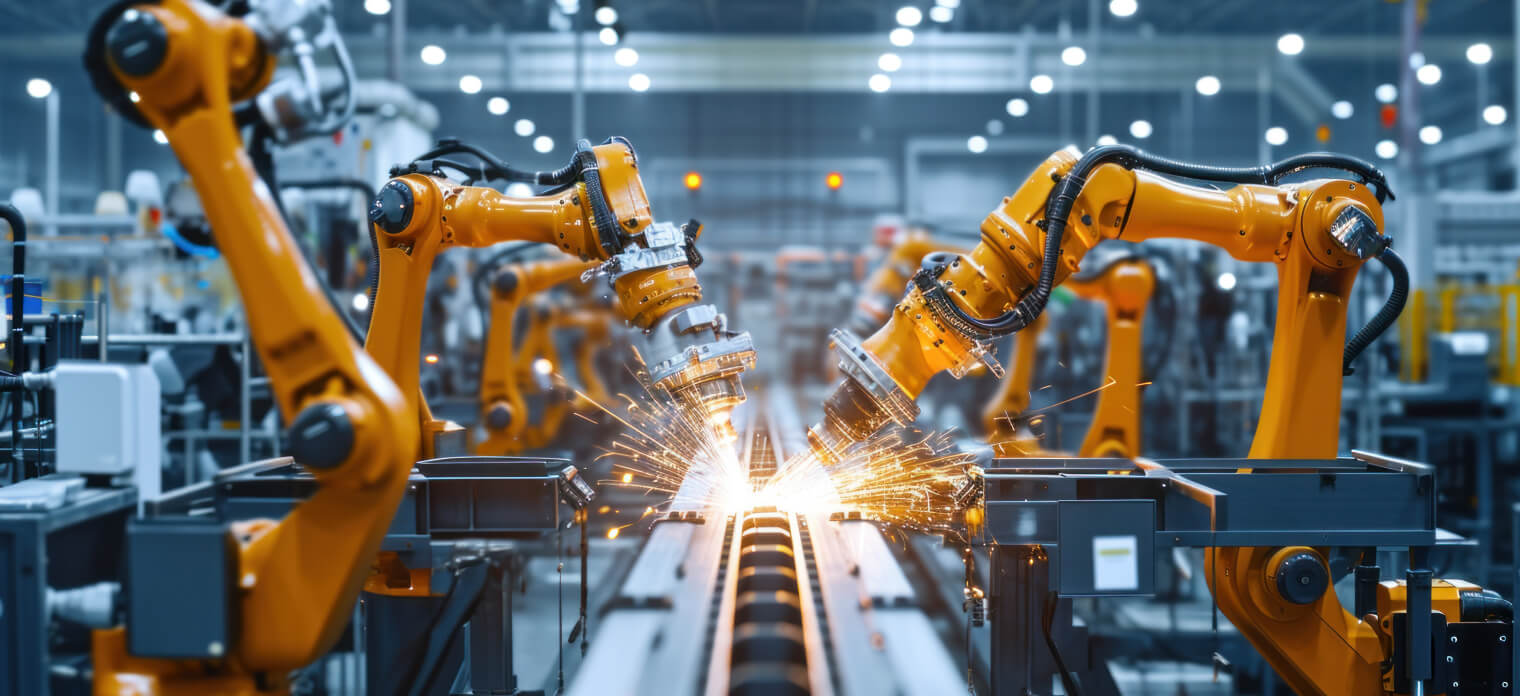
In today’s fiercely competitive market, differentiation requires continuous innovation. To meet rapidly evolving demands, industrial robot and machine tool OEMs are shifting from producing purely mechanical and electrical solutions to intelligent, software-defined systems. In parallel, their customers are increasingly expecting connected, autonomous, and highly adaptable equipment.
Technologies such as self-learning robots, collaborative robots (cobots), and autonomous mobile robots (AMRs) are revolutionizing material handling and transportation and streamlining routine tasks. These advancements not only improve operational efficiency but also accelerate time to market – key factors for manufacturers striving to remain competitive.
The concept of software-defined machines has become central to this transformation, creating a paradigm shift: software updates, in addition to mechanical and electrical upgrades, are now enhancing product functionality and performance. Industrial robots and machine tools are no longer merely hardware-based assets but intelligent systems that seamlessly integrate mechanical, electrical, fluidic, and control components.
These intelligent systems deliver unprecedented versatility, allowing manufacturers to swiftly adapt to changing requirements while ensuring optimal productivity and efficiency. Embracing this transition to connected and autonomous systems is not just an opportunity for OEMs – it is an essential step to meet modern market demands and stay ahead in the era of intelligent manufacturing.
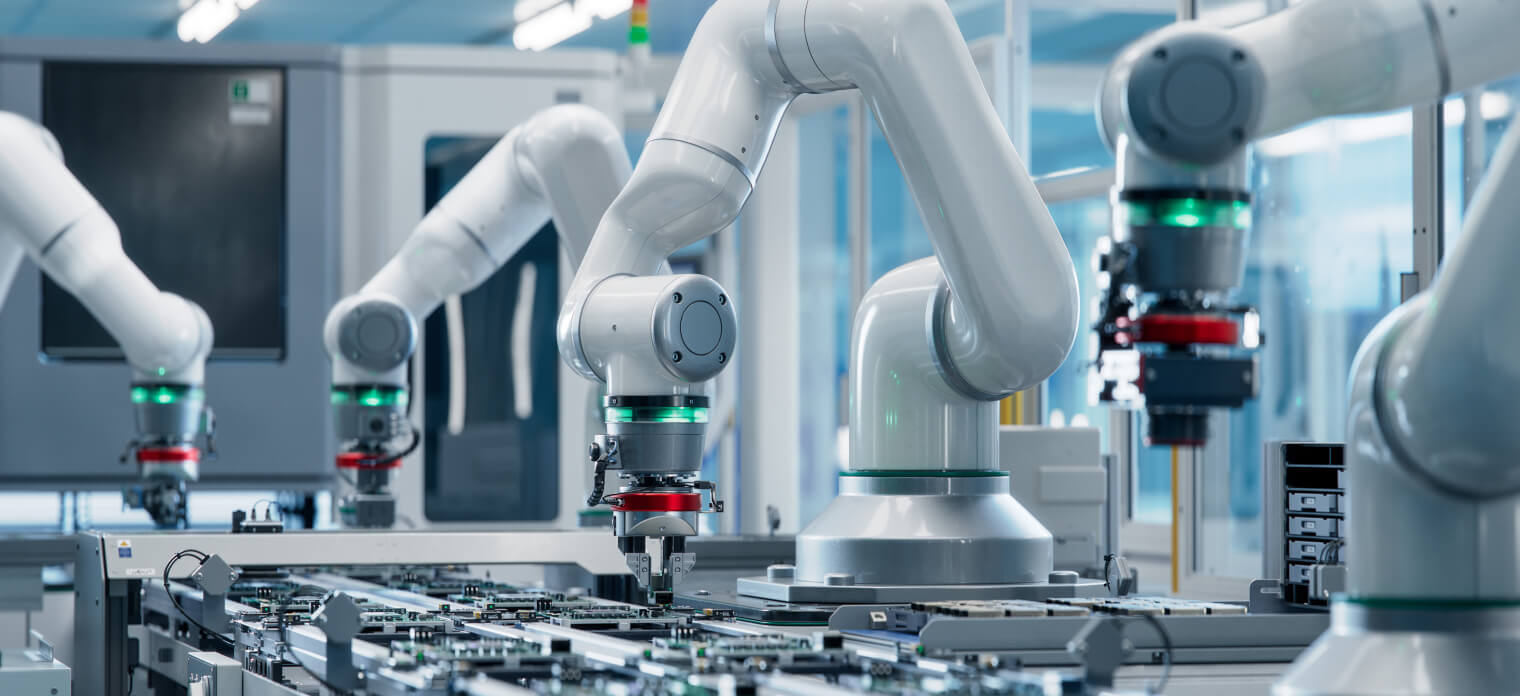
Intensifying competition among OEMs in various industries is pressuring industrial robot and machine tool manufacturers to deliver faster, more cost-efficient, and highly innovative production equipment. Automotive manufacturers, for example, need to be first to market and are expecting quicker turnarounds, while demanding production equipment that integrates cutting-edge technologies to support their drive for efficiency, flexibility, and sustainability. New entrants and disruptive innovators are also seizing this opportunity to challenge traditional robot manufacturers, accelerate innovation, and gain a foothold in this rapidly evolving market.
To meet these demands, industrial equipment manufacturers need to transform how they approach product development and adopt agile strategies, from product concept to delivery. Accelerating innovation is no longer optional – it is critical. Digital technologies such as virtual twins and AI-driven simulation are empowering manufacturers to enhance design, prototyping, and production, as well as shorten development cycles and optimize product performance before production even begins.
Companies also need to deliver tailored, high-value solutions that not only address immediate needs, but also anticipate future challenges to stand out in today’s crowded market. This involves integrating advanced automation, modularity, and connectivity into equipment designs, which allows their customers to quickly adapt to changing production requirements.
The challenges are significant, but so are the opportunities. By embracing these market dynamics, industrial equipment manufacturers can position themselves as innovation leaders and outpace competitors while delivering exceptional value to their customers.
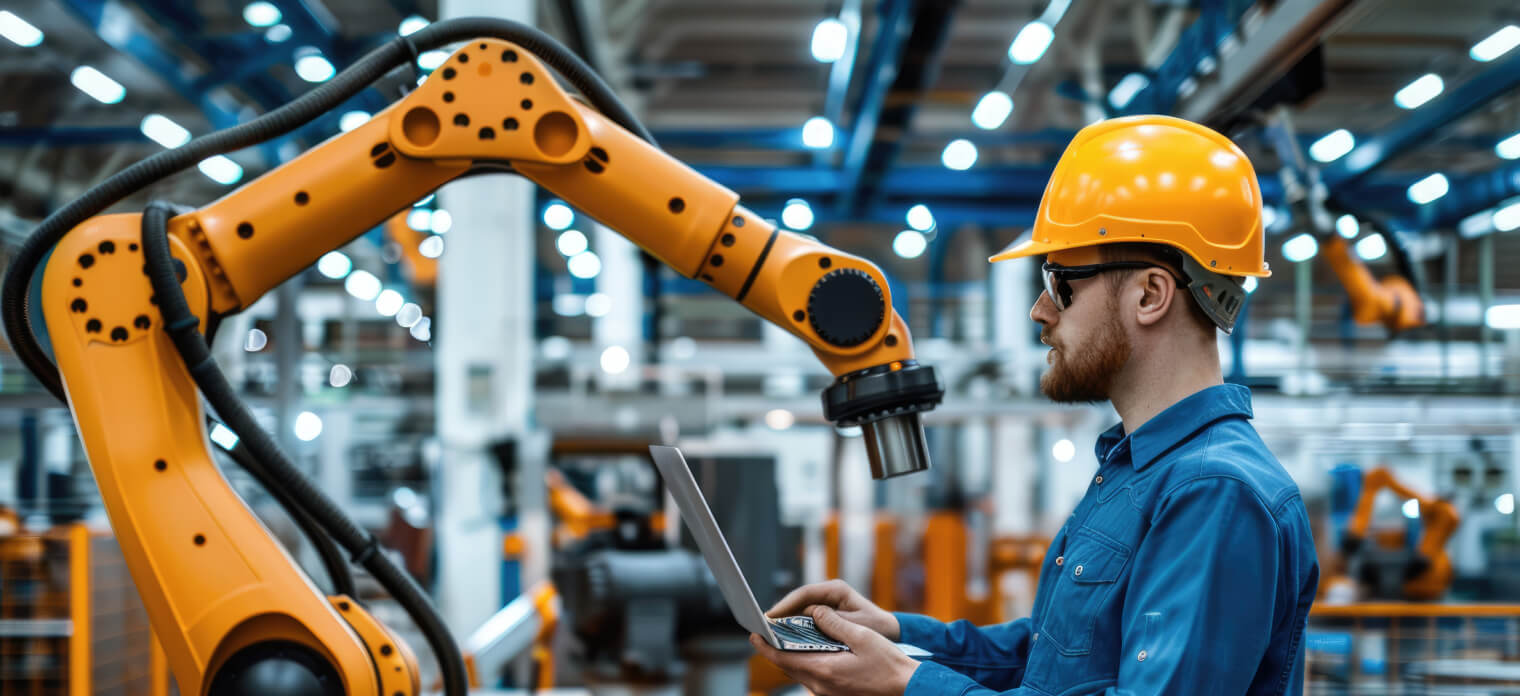
End users of machines such as laser cutting systems are increasingly seeking outcomes rather than ownership. They are now purchasing the results a machine delivers – such as the number of quality parts produced or the precision of a robot’s welds – rather than the equipment itself. This shift is driving the adoption of equipment as a service (EaaS), where industrial equipment suppliers focus on delivering machine capabilities and uptime as services instead of selling standalone products.
This transition is made possible by the rise of connected machines, enabled by Internet of Things (IoT) technologies. By tracking real-time performance and efficiency, OEMs can implement usage-based payment models where customers pay only for uptime or output. This approach aligns with customer expectations while fostering closer, longer-term relationships between equipment suppliers and their customers.
Adopting a robust after sales strategy is becoming critical for industrial equipment suppliers, including those producing machine tools, robots, 3D printers, and mobile robots. After sales services not only ensure sustained customer satisfaction, but also represent a highly profitable revenue stream. While margins on new machine sales hover around 10%, aftersales services can achieve margins as high as 50%.
Aftersales services empower customers to extend the lifecycle of their machines instead of investing in new equipment. This approach also provides industrial equipment manufacturers with continuous revenue streams, without compromising customer demands for cost-effectiveness.
Digital services and industrial IoT further enhance aftersales opportunities by enabling industrial equipment OEMs to deliver predictive maintenance, remote monitoring, and performance optimization solutions. Beyond customer satisfaction, the data generated through digital services allows manufacturers to refine and innovate their product offerings, ensuring that future machines are even more efficient, reliable, and aligned with market needs.
The shift from selling machines to providing services not only strengthens the financial resilience of OEMs but also fosters long-term relationships with customers, positioning equipment suppliers to thrive in an evolving, service-driven marketplace.
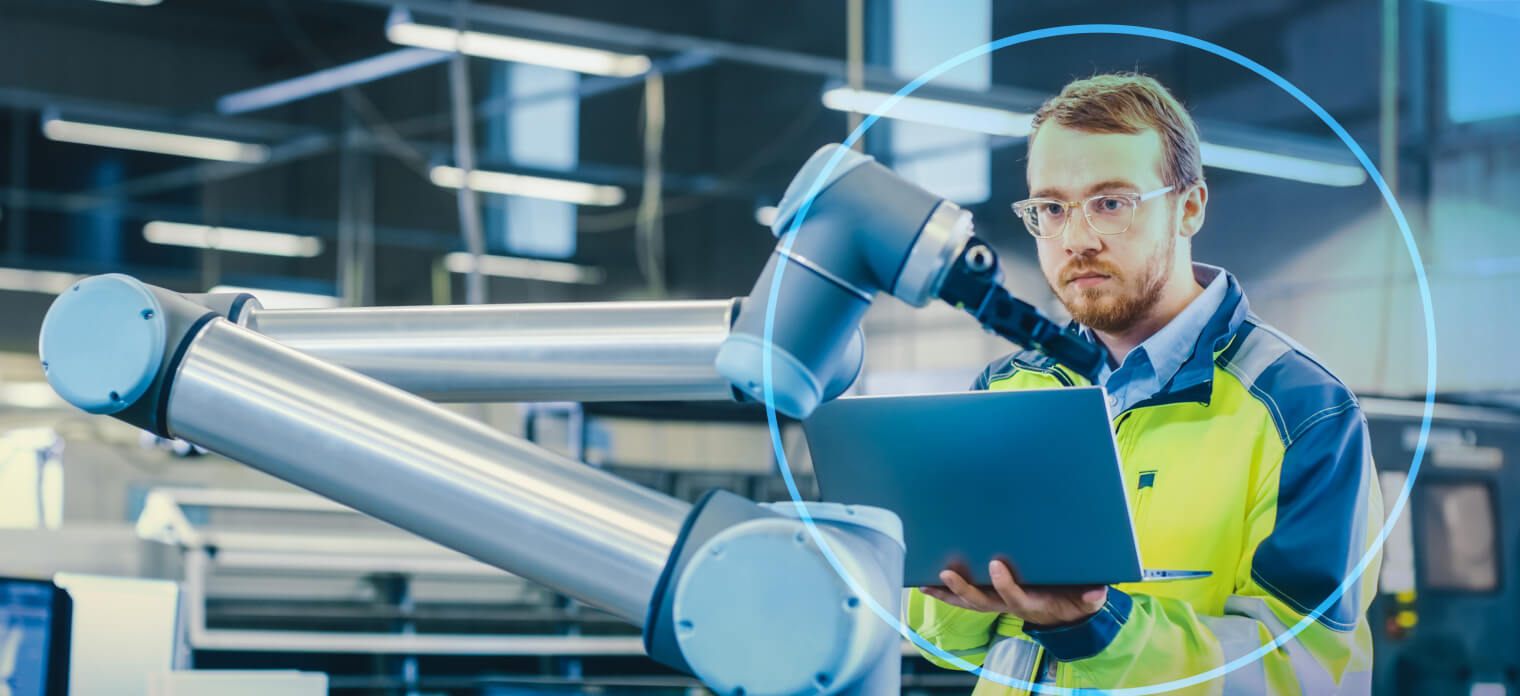
The rapid evolution of standards and regulations presents a significant challenge for global players, especially in industries like machine tools and robotics. Manufacturers must navigate a complex landscape of international and local requirements, which often vary widely between countries and regions.
Staying compliant is not optional – it's a business-critical necessity. As new regulations emerge and outdated ones are voided, OEMs must continuously ensure that their products meet current requirements. Failure to comply can lead to significant consequences, including costly fines, the inability to sell products, and substantial financial losses resulting from the need to redesign and revalidate non-compliant equipment.
Digital tools such as IoT-enabled tracking systems are enabling global manufacturers to monitor and adapt to this dynamic regulatory environment. Through real-time updates and insights into regulatory shifts, companies can reduce the risk of non-compliance and its associated costs.
By prioritizing compliance as a core component of their operations, OEMs not only mitigate risks but also build trust with customers and regulatory bodies, ensuring that their products remain competitive and market-ready in a fast-changing global environment.
In the Spotlight
Our Customers
Explore Our Solutions
FAQ
An industrial robot is a programmable machine used in manufacturing to automate tasks like material handling, welding, assembly, painting, machining, inspection, and palletizing. These robots improve efficiency, ensure quality, reduce costs, and enhance workplace safety. They are widely used in industries such as automotive, electronics, pharmaceuticals, and food production, playing a key role in modern smart factories.
Integrating industrial robots into existing production lines involves challenges such as ensuring compatibility with legacy systems, including equipment, software, and communication protocols. High upfront costs for purchasing robots, installation, and upgrades can be a barrier, requiring a clear ROI justification. Space constraints may necessitate redesigning production layouts to accommodate robots and ensure safety. Additionally, workflows often need reengineering to incorporate automation effectively. Workforce training is critical to operate and maintain robots, while overcoming resistance to change and concerns about job displacement is essential for successful implementation.
A digital twin in robotics is a virtual representation of a physical robot, including its components, systems, and performance. It allows real-time monitoring, simulation, and optimization of the robot's operations, enabling better design, predictive maintenance, and improved efficiency in manufacturing or other applications.