Rotomoldeo
Descubra en qué consiste el proceso de moldeo por rotomoldeo y su uso en la industria.
Introducción al rotomoldeo
El rotomoldeo, también llamado moldeo rotacional, consiste en introducir una carga, o peso de inyección, de material en un molde hueco calentado, seguido de la rotación lenta del molde, lo que hace que el material ablandado se disperse y se adhiera a las paredes del molde. El molde sigue girando en todo momento durante la fase de calentamiento para conseguir y mantener un grosor uniforme en toda la pieza. Esta rotación también evita el hundimiento, o la deformación, durante la fase de enfriamiento.
La clara ventaja del rotomoldeo es que se trata de un proceso más sencillo que cualquier otro a la hora de producir piezas grandes y huecas, como depósitos de aceite o sillas. Además, los moldes utilizados en el rotomoldeo son mucho menos costosos que otros tipos de moldes. El rotomoldeo genera mucho menos material de desecho; el material sobrante puede servir a menudo para otro uso, por lo que resulta económico y ecológico.
Otra ventaja radica en los propios moldes, ya que necesitan menos herramientas. En consecuencia, las empresas pueden poner en producción mucho más rápido que otros procesos de moldeo. Esto es especialmente valioso para las piezas complejas. El moldeo rotacional es también el proceso elegido para las tiradas cortas y las entregas urgentes. El operario puede cambiar los moldes rápidamente o utilizar diferentes colores sin necesidad de purgar el molde. Con otros procesos, puede ser necesario purgar el molde para cambiar los colores.
Los principales inconvenientes son las zonas de difícil acceso del molde y la larga duración del enfriamiento, que conlleva un importante tiempo de inactividad del molde.
La historia del rotomoldeo
La primera aplicación de la rotación biaxial y el calor se documentó en 1855, principalmente para producir proyectiles de artillería metálicos y otros recipientes huecos. El objetivo inicial del uso de la rotación era crear consistencia en el grosor de las paredes y en la densidad. Con el tiempo, el uso del moldeo rotacional fue para ahuecar objetos de cera; poco después, las fábricas de chocolate fabricaron huevos de chocolate gracias al rotomoldeo. Posteriormente, hubo aplicaciones con el uso de yeso de París en la década de 1920. En los años 50, se empezó con los plásticos y tardó en ser adoptado por la industria debido a su escaso índice de productividad y a la limitación que suponían los pocos plásticos adecuados. Los primeros productos rotomoldeados fueron cabezas de muñecas. Ayudó a desarrollar otros juguetes de plástico, conos de carretera, boyas marinas y reposabrazos de coches. La popularidad resultante aceleró el desarrollo de maquinaria de mayor tamaño y, finalmente, condujo a la creación de una asociación comercial mundial llamada The Association of Rotational Molders (ARM).
En la década de 1980 se introdujeron nuevos plásticos como el policarbonato, el poliéster y el nailon en el moldeo rotacional, lo que dio lugar a nuevas aplicaciones para el proceso, como los depósitos de combustible y los moldes industriales. Más recientemente, el desarrollo de los polvos de plástico y las mejoras en el control del proceso han llevado a un aumento considerable de su aplicación.
Las distintas máquinas de rotomoldeo tienen un amplio espectro de tamaños de equipos. Por lo general, una máquina de moldeo rotacional contiene moldes, un horno, una cámara de refrigeración y husillos de moldeo. El recubrimiento uniforme del plástico dentro de cada molde se consigue con los husillos montados en un eje giratorio. De la calidad de los moldes, normalmente de aluminio, depende directamente la calidad y el acabado del producto final.
¿Qué tipo de máquinas de rotomoldeo?
Las diferentes máquinas de rotomoldeo son las siguientes
- Máquina Rock and Roll
- Máquina de almeja
- Máquina rotomoldeadora vertical o basculante
- Inyección de material
- Máquina rotativa vertical o basculante
- Máquina lanzadera
- Máquina de brazo oscilante
- Máquina de carrusel
La máquina de brazo giratorio está especializada en la producción de piezas largas y estrechas principalmente. La máquina clamshell es una máquina de moldeo rotacional de un solo brazo que calienta y enfría en las mismas cámaras y ocupa menos espacio que las máquinas shuttle y de brazo oscilante. Las máquinas rotativas verticales tienen un tamaño entre pequeño y mediano (en comparación con otras máquinas de rotomoldeo) y son eficientes desde el punto de vista energético, gracias a sus cámaras compactas de calentamiento y enfriamiento.
Aunque existe una máquina de lanzadera de un solo brazo, la mayoría de las máquinas de lanzadera tienen dos brazos que alternan los moldes entre la cámara de calentamiento y la estación de enfriamiento. Los brazos son independientes entre sí y hacen girar los moldes biaxialmente. La máquina de brazo oscilante es beneficiosa para las empresas con ciclos de enfriamiento prolongados o tiempos de desmoldeo largos. Puede tener hasta cuatro brazos con movimiento biaxial. Cada brazo es independiente del otro, ya que no es necesario accionar todos los brazos simultáneamente. La máquina de carrusel es una de las máquinas biaxiales más comunes en la industria. Puede tener hasta cuatro brazos y seis estaciones y está disponible en una amplia gama de tamaños.
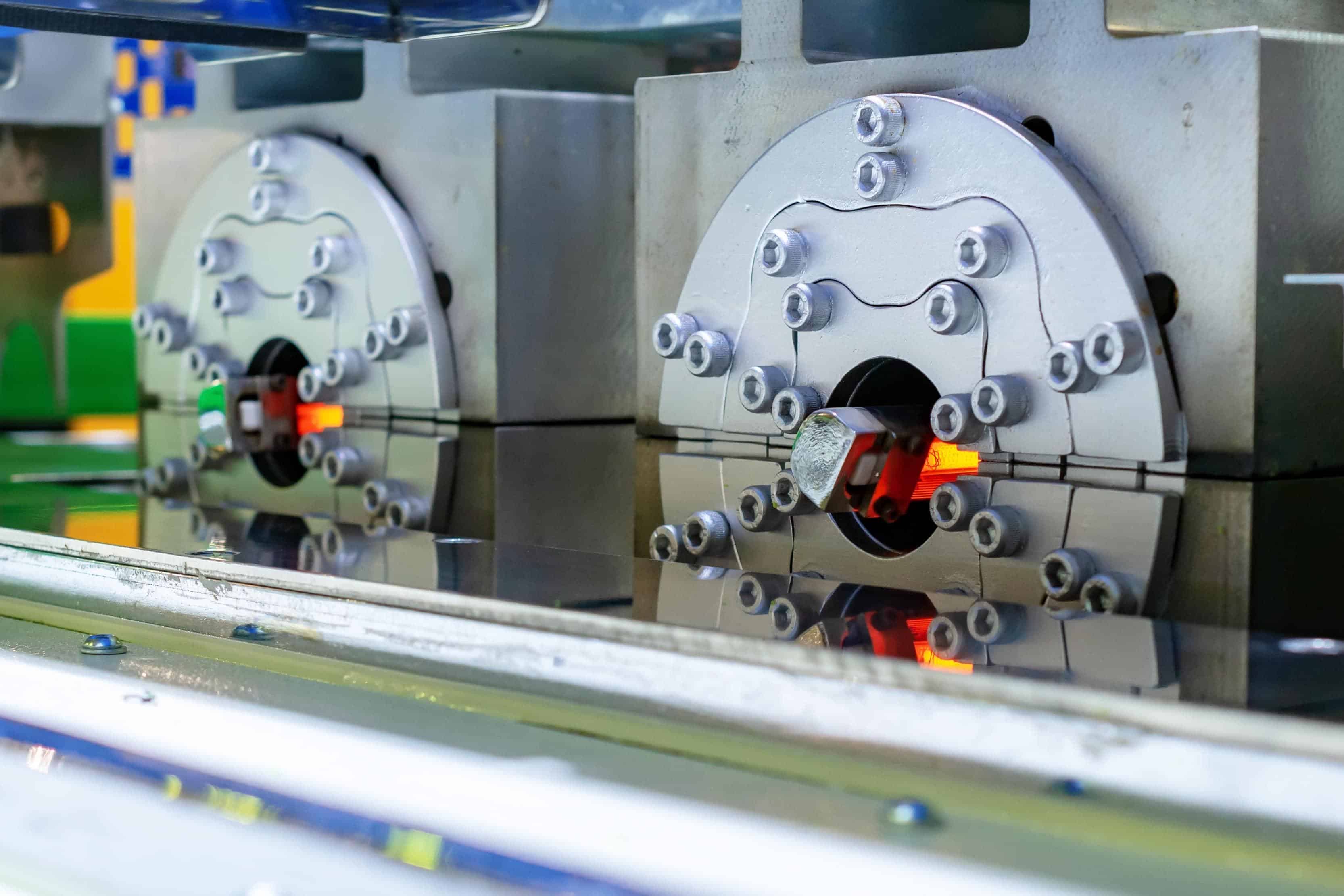
Reciba múltiples presupuestos para sus piezas en cuestión de segundos
Obtenga varios presupuestos para sus piezas en segundos