Anodizado
Aprenda más sobre el anodizado, un proceso de acabado, cómo funcionan y cuáles son los usos en la industria.
Introducción al anodizado
Los fabricantes utilizan el anodizado para aumentar el grosor de las capas naturales de óxido en la superficie de las piezas metálicas. Aunque se aplica con más frecuencia a los sustratos de aleación de aluminio, también puede aplicarse al titanio, el zinc, el magnesio, el niobio, el circonio, el hafnio y el tántalo. El proceso de anodización emplea la pasivación electrolítica para conseguir las propiedades deseadas, como la resistencia a la corrosión y al desgaste, una mejor adherencia para la pintura y el pegamento, o efectos estéticos. Para los efectos estéticos, los revestimientos gruesos y porosos permiten absorber un colorante, mientras que los revestimientos finos y transparentes pueden añadir efectos de interferencia a la luz reflejada.
El proceso se llama anodizado porque el sustrato de aluminio forma el electrodo del ánodo de un circuito eléctrico. El anodizado también se adopta para evitar el gripado o el desgaste de los componentes roscados y para fabricar películas dieléctricas para los condensadores electrolíticos. La textura microscópica de una pieza y la estructura cristalina del metal cerca de la superficie cambian con el anodizado. Los revestimientos gruesos suelen requerir un proceso de sellado para evitar la corrosión debido a su naturaleza porosa. Las películas anódicas son beneficiosas porque presentan mayor resistencia y propiedades adhesivas que la mayoría de los tipos de revestimiento metálico; sin embargo, también son más frágiles, lo que las hace más susceptibles de agrietarse debido a la tensión térmica.
Las principales ventajas del anodizado son que la capa es mucho más fina que la de pintura o polvo, que es extremadamente duradera, dura, resistente a la abrasión y de larga duración, que no se descascarilla ni se astilla, que la superficie es mucho más dura que la de la pintura, que el color es resistente a la decoloración, que es una excelente protección contra la corrosión, que es respetuoso con el medio ambiente, que es un buen aislante eléctrico y que es asequible.
Históricamente, el anodizado apareció por primera vez en un contexto industrial en 1923 para proteger de la corrosión las piezas de duraluminio utilizadas en hidroaviones. Al principio, se adoptó el uso de ácido crómico y se denominó proceso Bengough-Stuart. Con el tiempo, esto llevó a la adopción del ácido sulfúrico, que pronto se convirtió y sigue siendo el electrolito de anodización más común en la actualidad. En 1923, el anodizado con ácido oxálico se patentó en Japón y, posteriormente, se adoptó ampliamente en Alemania, sobre todo en aplicaciones arquitectónicas. En los años sesenta y setenta, la extrusión de aluminio anodizado era un material arquitectónico muy popular, pero fue sustituido por plásticos más baratos y por el recubrimiento en polvo. Más recientemente, el ácido fosfórico se ha aplicado al campo del anodizado, utilizado por ahora exclusivamente como pretratamiento de adhesivos y pinturas orgánicas.
La especificación de anodizado más utilizada en Estados Unidos es una especificación militar estadounidense. Define tres tipos de anodización del aluminio: anodización con ácido crómico (Tipo I) y anodización con ácido sulfúrico (Tipos II y III). El ácido crómico es el proceso de anodización más antiguo, mientras que el ácido sulfúrico es la solución más utilizada en el recubrimiento anodizado. También es posible anodizar con un ácido orgánico, ácido fosfórico, baños de borato y tartrato, y oxidación electrolítica por plasma.
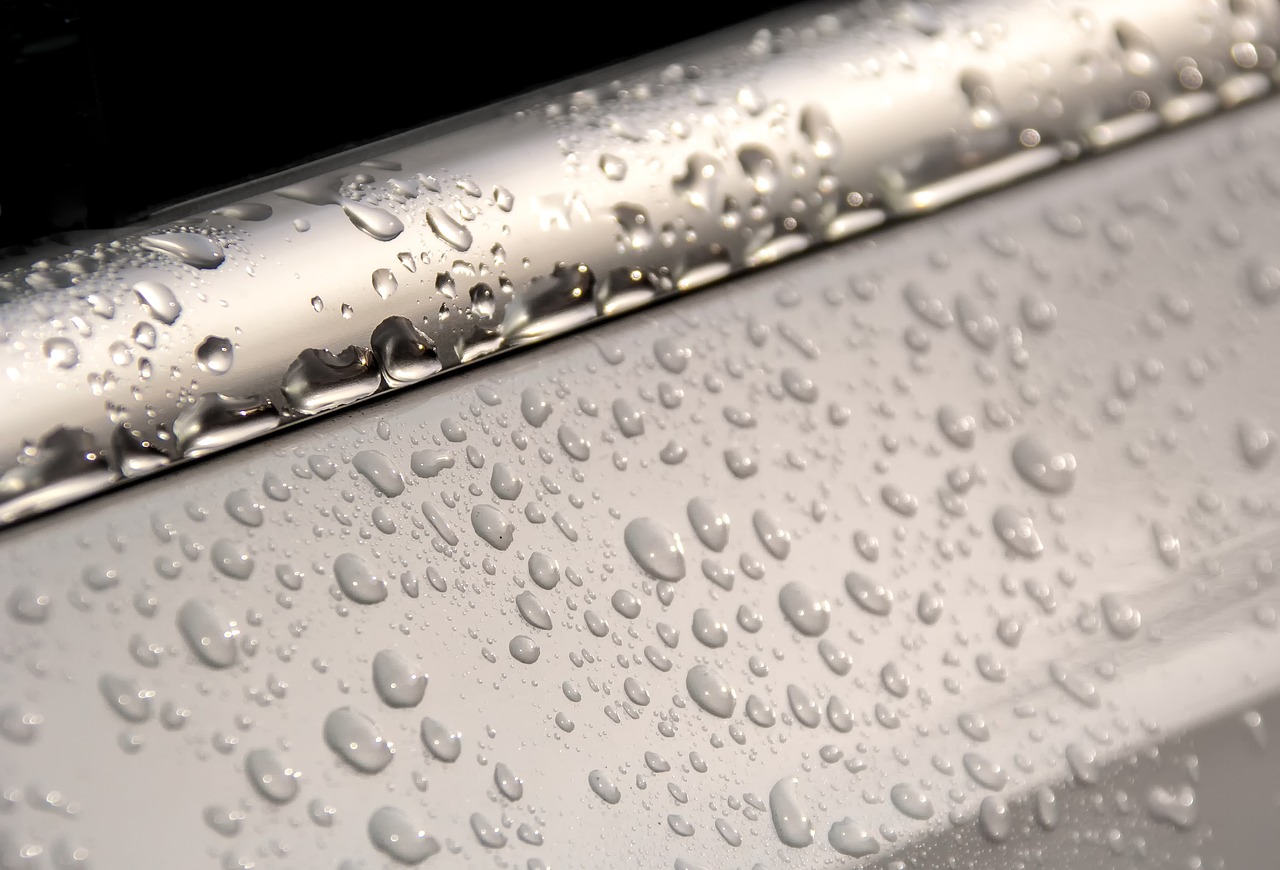
Reciba múltiples presupuestos para sus piezas en cuestión de segundos
Obtenga varios presupuestos para sus piezas en segundos