Virtual twin experiences in Manufacturing Industries
Producing better, more sustainable product with digital twin technology
What is a manufacturing digital twin technology?
A digital twin establishes a digital representation of a real-world component or process in manufacturing industries.
This data-driven computer model takes inputs from the real-world which allows a product to be monitored or to control a process optimally. Later, it also feeds back data from a deployed product, creating a constant cycle of improvement.
This helps manufacturing industries improve products used in everyday life, as well as the equipment that produces those goods. This not only accelerates innovation initiatives, but it does so sustainablity: manufacturers can simulate and evaluate impacts prior to production of a physical product, reducing their carbon footprint.
With such a positive contribution to sustainable innovation, business leaders are increasingly recognizing the power of digital twin technologies to advance digital transformation and innovation. The global digital twin market size was valued at USD 7.48 billion in 2021 and, according to Grand View Research, is projected to grow at a compound annual growth rate (CAGR) of 39.1% from 2022 to 2030.
How does a virtual twin benefit manufacturing more than a digital twin?
While digital twins bring tremendous value to the manufacturing sector, there is an even-more evolved technology: the virtual twin.
A digital twin is a mathematical representation of a real-world object or system. A virtual is not limited to a mathematical model of an object or a system but instead considers an entire system of systems, including the environment in which the physical object exists. This makes it possible to simulate in the virtual worlds the consequences of each modification or optimization of an individual product on the whole and within the entire model.
Dassault Systèmes unique virtual twins combine the science-based representation of a product, factory or company through modeling and simulation with the power of prediction brought about by incorporating real-world data. This convergence of the virtual and real worlds and the continuous cycle of information between the two creates a closed-loop capability that enables optimization in virtually any scenario.
How is a virtual twin used in manufacturing?
With consumers demanding more personalized products and experiences, manufacturers are under constant pressure to adapt while also keeping operations within budget. A virtual twin helps accelerate innovation by digitally testing new products, facilities and production methods, limited only by imagination. A virtual twin can also ensure regulatory needs are met, ensuring products and operations are safe and secure.
Seven ways virtual twins can benefit manufacturing:
• Unlimited simulation
• Continuous improvement (organization, process...)
• Improved human factors
• Added agility
• Global collaboration
• IIoT integration
• Production data manufacturer
• Knowledge retention
The virtual twin can add benefit across all phases in the manufacturing organizations and process; from planning facilities, process and manufacturing through to actual production. This starts purely in the virtual world, then once production is live, data is fed back to create a system of continuous improvement across all elements of manufacturing operations.
How does a virtual twin benefit manufacturers?
Test new products
Digitally evaluate potential changes and optimize innovative ideas
Re-assess manufacturing strategies
Analyze production processes and capacity to migrate delays
Synchronize planning and execution
Drive continuous improvement
Virtual vehicle innovation showroom
Learn how virtual twins can accelerate the development of sustainable vehicles
Designing impactful innovation
Discover the power of the Cloud by playing with E-way Rescue Roadster prototype in 3D!
Manufacturing virtual twins contribute to achieving the UN Sustainable Development Goals
The United Nations Sustainable Development Goals are worldwide guidelines to achieve a better and more sustainable future for all.
Virtual Twin Experiences for Manufacturing Industries, powered by Dassault Systèmes, help spur economic growth and tackle climate change as addressed in Goal 9 and Goal 12.
These goals drive long-term regulations to instill positive change, reduce resource consumption and reach net-zero carbon emissions.
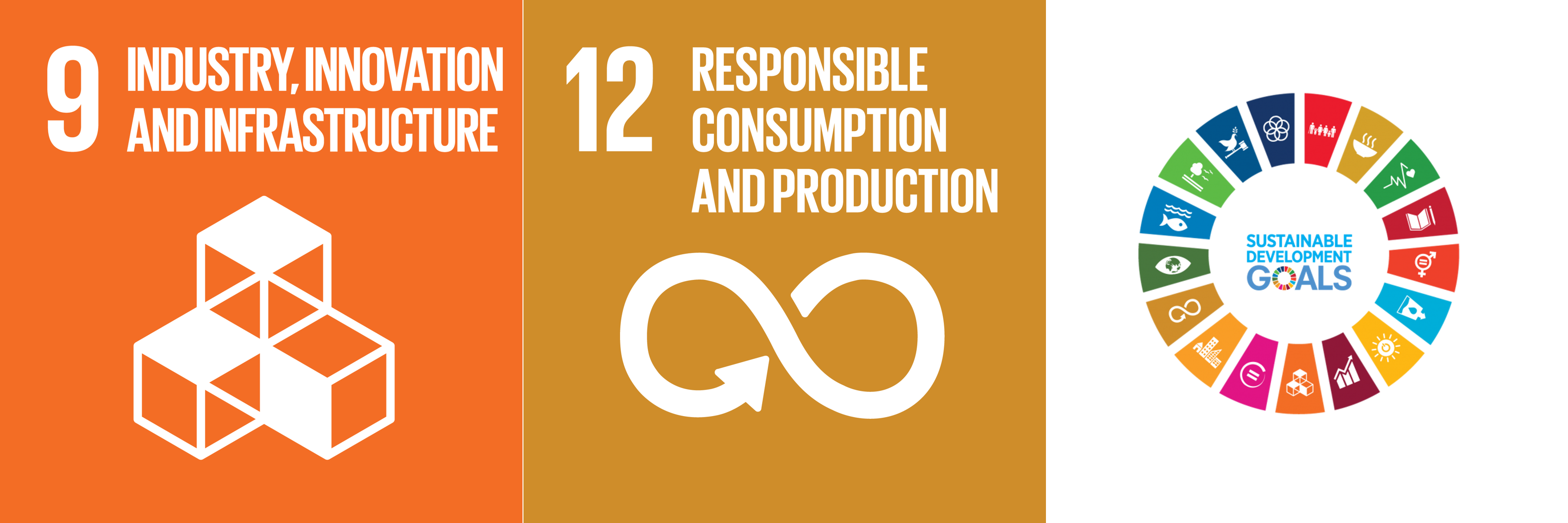