PIVETEAUBOIS
To meet high demand for CLT from the construction industry, PIVETEAUBOIS chose the productization solution From Experience to Construction on the 3DEXPERIENCE platform on the cloud to manage the process around its clients’ custom orders, from requests through to machining and delivery. Automating tasks enabled the company to gain 50% to 60% in productivity and to deliver products quicker.
Mass timber for green building
Wood has always been a staple in construction, yet concerted efforts to reduce the industry’s environmental impact has put the material firmly back in the spotlight. Architects and builders are increasingly turning to timber, specifically engineered wood called mass timber, as a substitute for carbon intensive concrete and steel. One form of mass timber demonstrating widespread architectural potential is cross-laminated timber (CLT) – a sustainable multi-layered wood panel used for making large-scale walls as strong as concrete.
PIVETEAUBOIS Group vice president Jean Piveteau has long recognized the capabilities of new product developments like CLT and adapted his timber business to keep up with the changes happening across the construction industry. This foresight is paying off as the trend to use prefabricated timber instead of concrete continues to take off.
Beyond investing in cutting-edge machinery, the French industrial timber product manufacturer has transformed its entire approach to handle its clients’ custom orders. As a CLT factory runs 100% to order, PIVETEAUBOIS needed new production methods and digital capabilities to cater to customers’ individual requests, scale up to meet demand and make the entire process as efficient as possible.
To bring its industrial vision to life, the company worked closely with BEAM CUBE. The technology partner is recognized for its know-how of Dassault Systèmes solutions in the architecture, engineering and construction (AEC) industry, using the 3DEXPERIENCE® platform on cloud.
“Custom manufacturing is entirely new for us,” said Maxime Besnard, head of the PROJETSBOIS (Wood Projects) department at PIVETEAUBOIS. “It involves having a customer’s plan signed off before production and requires a different approach because we have to integrate industrial design tools, manufacture according to a plan and use machining programs. That’s what led us to the 3DEXPERIENCE platform.”
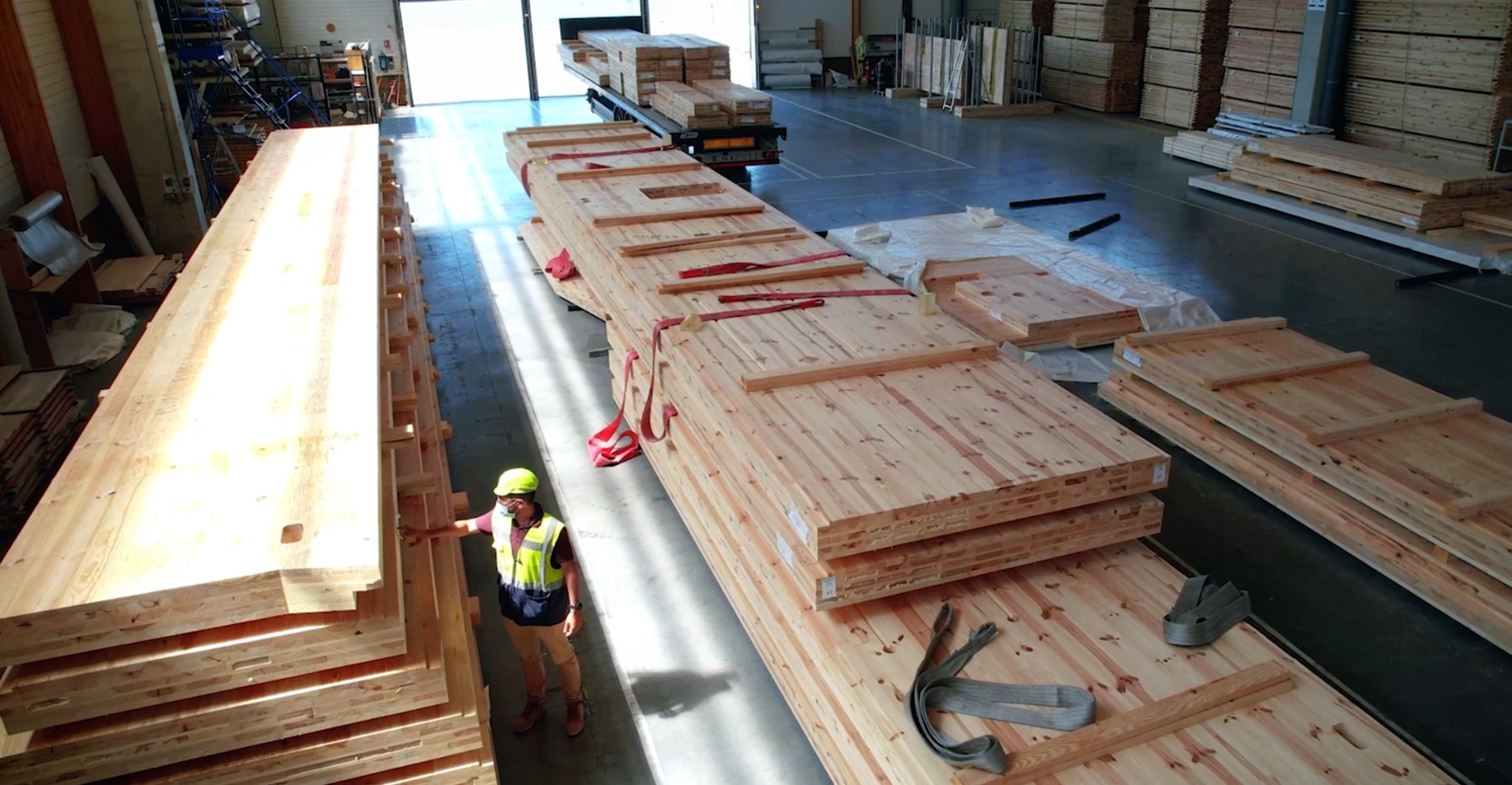
Industrial solutions for made-to-order manufacturing
In line with its social and environmental values, PIVETEAUBOIS ensures that it makes the most of 100% of the tree. Bark and offcuts are used to make energy and wood pellets; and the valuable board, which stores more carbon internally, is used to make all solid wood products, from basic planks to CLT and other construction products.
When it came to modernizing its working methods and embracing digital solutions, then PIVETEAUBOIS wanted a technology platform that would help to further optimize its resources.
“The goal is to add a little more value to each cubic meter of raw wood that comes into the factory every day,” Piveteau said. “Dassault Systèmes’ role is to bring performance between the wooden beam or CLT panel that we have produced and the machining that we will have to do on it. It will enable us to return wood to its rightful place in the construction world.”
Specifically, PIVETEAUBOIS needed a cutting-edge solution that would allow it to take the building models it receives from each customer and break them down into a plan of parts. This plan would be used to create each individual timber panel and optimize manufacturing. From that same information, the solution would also produce a loading plan, which determines how the manufactured timber panels are arranged onto the truck, so they come off in precisely the right order at the construction site.
“We’re talking about components that weigh between 500 kilograms and 2.5 metric tons that cannot be manipulated easily,” Besnard said. “We must stick to the unloading order of the truck requested by the customer, so the automated loading plan is crucial.”
Part of the 3DEXPERIENCE platform, CATIA delivers the design capabilities PIVETEAUBOIS needs to manage all these aspects as it can automatically create several different assemblies from the same unit parts within a single 3D model.
“The data-centric side of the platform left no doubt about our decision to go for 3DEXPERIENCE,” Besnard said. “It allows us to work from a single information source, accessible to everyone, and linked to our project management system. Nobody wonders if it’s the right data or the latest version. There’s one single source of truth for everyone. That’s what really makes the difference.”
With the 3DEXPERIENCE platform, we have gained 50% to 60% in productivity and delivered finished products on site faster.
Synchronized plans save time
PIVETEAUBOIS has been able to harness the 3DEXPERIENCE platform’s capabilities thanks to the support of BEAM CUBE. Now, PIVETEAUBOIS can manufacture standardized and customized products at scale while maintaining full control of every step of its operation – all within a single environment.
“CATIA translates the customer’s plan into surface area, quantity, loading plan, parts plan and order confirmation,” Besnard said. “With the 3DEXPERIENCE platform, we gained 50% to 60% in productivity across these stages, and delivered finished products on site quicker.”
For the technicians and engineers tasked with coming up with the loading plans – a critical part of delivering the finished timber panels on site correctly – the platform has been key for keeping up with growing demand.
“Before, the Pricing department used to spend 70% of its time making parts and loading plans,” Besnard explained. “If we want to grow volumes while maintaining our workforce, we need automation and a high-performance solution to manage these tasks. That’s what the 3DEXPERIENCE platform on cloud gives us.”
This approach also enables PIVETEAUBOIS to be more responsive to its customers’ needs and accommodate their requests as each unique building project evolves.
“Typically, the time between receipt of a customer order and delivery is six weeks,” Besnard said. “With this cloud solution, the speed and dynamism of the information will help us shorten this timeframe and, above all, allow us to be more flexible as we will be able to integrate customers’ change requests until late in the process.”
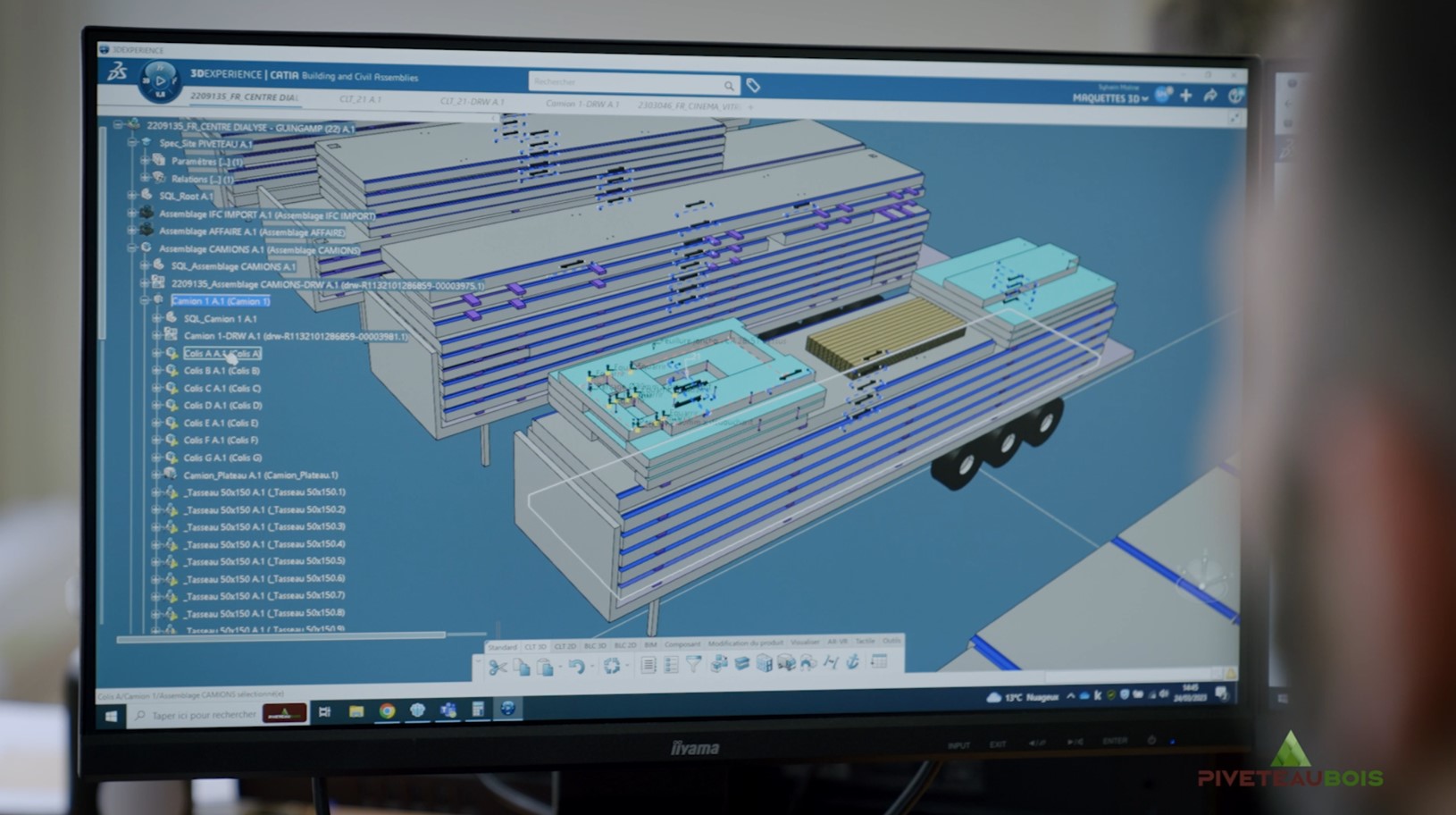
Digitalizing document and project management
With so many projects and parts to manage, PIVETEAUBOIS has significantly benefited from the 3DEXPERIENCE platform’s robust data and project management capabilities seamlessly integrated through ENOVIA. It enables the company to handle multiple custom orders at the same time, and maintain full version control of all the building and part models and related documents as they are exchanged and updated. This avoids data duplication and errors.
“Before, we manually updated spreadsheets and a lot of information became obsolete as soon as there was a modification from the client,” Besnard said. “Now, questions no longer need to be asked; there’s total confidence in the information because it’s available and updated in real time.”
Today, PIVETEAUBOIS uses the 3DEXPERIENCE platform to manage every project from the moment it receives a customer request until the final prefabricated timber parts are delivered on the construction site.
“Project management is now entirely handled on the platform,” Besnard said. “It allows us to formally structure the sequence of tasks, create the right user groups, connect them at the right time, set up the factory and ensure we meet every deadline. It has introduced a continuous flow of information between every stakeholder.”
Because all CLT related know-how is stored on the cloud through the 3DEXPERIENCE platform, PIVETEAUBOIS can get up to speed on new projects fast, and experienced team members can effectively share ideas and expertise. Collaboration happens within the platform, ensuring information traceability and consistent communication between sales, engineering and production.
“We mainly use the 3DSwym Community to communicate and use the Ideas posts to initiate each project,” Besnard said. “Everything is in place from start to finish. So, it’s both a dynamic and structured collaboration. Today, with the communities, posts and collaborative management of the platform, people are only asked to be involved when they really need to be.”
Eventually, PIVETEAUBOIS hopes to use the platform to connect directly with its customers, so they can review building models and make changes without having to send data back and forth.
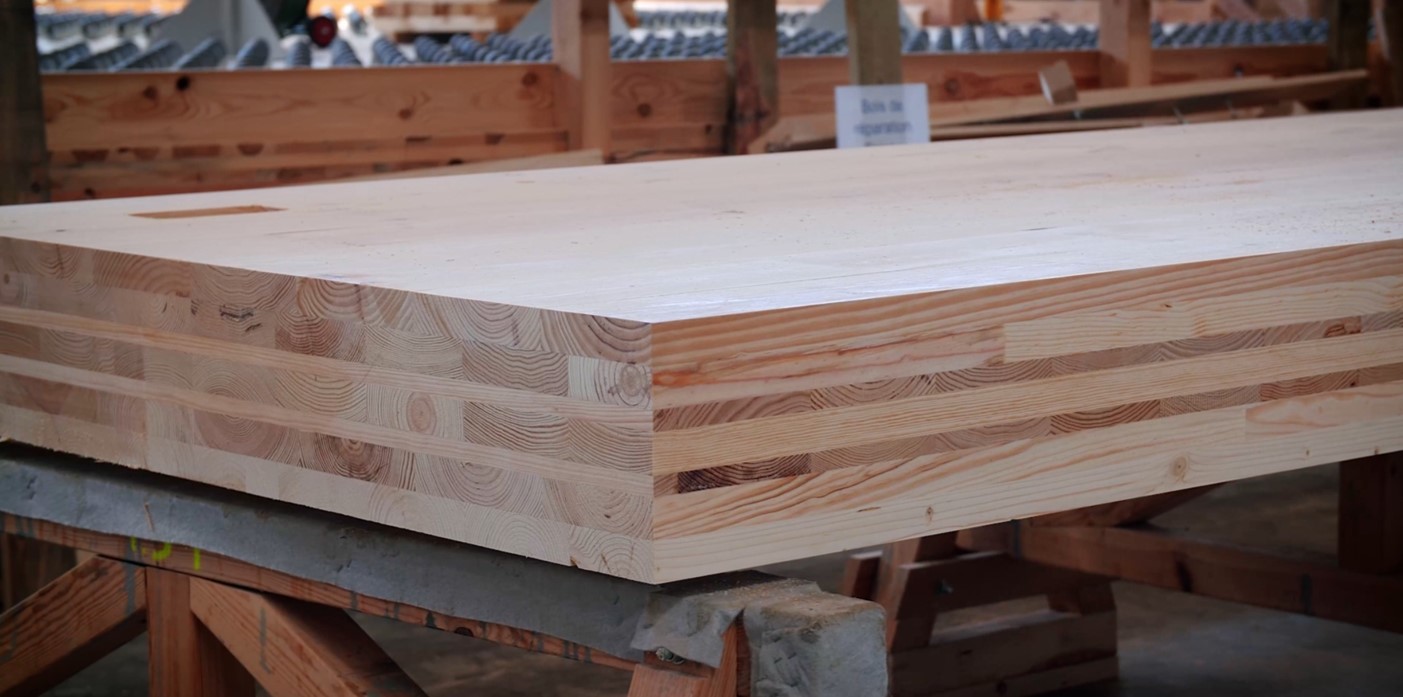
Building sustainability into future constructions
Since its creation, PIVETEAUBOIS has always focused on optimizing the natural resources it uses and saving energy across its production processes.
“Our family’s passion for wood has always dictated our mission: to build a sustainable world for future generations by offering everyone the best of each tree,” Piveteau said. “We are involved in the material’s development by promoting our local forests and responding to environmental challenges with low-carbon products and production methods.”
As it looks to the future, the company plans to explore how it might use the 3DEXPERIENCE platform to carry out lifecycle assessment calculations of a product and building, and measure its overall carbon footprint.
“Our job is to make the best use of the material that comes into our factory and to think about the sustainable products of tomorrow, such as wood wool and insulation,” Piveteau added. “We want to be able to demonstrate the carbon reduction efforts we’re making and carry out the material evaluations for upcoming European regulations.”
Just as the AEC industry strives to become more productive and sustainable, so too is PIVETEAUBOIS driving positive change across the timber sector – using digital technology to scale up made-to-order manufacturing and develop the timber products required to decarbonize the built environment.
Discover more about the From Experience to Construction industry solution experience.
00:00 – 00:15
Jean Piveteau, Vice President, PIVETEAUBOIS Group:
What defines PIVETEAUBOIS is innovation – with two strong passions, in wood and technologies.
00:16 – 00:35
Maxime Besnard, Manager PROJETSBOIS (Wood Projects), PIVETEAUBOIS:
Dassault Systèmes solutions are integrated into our process from the customer request through the delivery of the prefabricated elements on the construction site. The benefit is that we’re able to industrialize custom products.
00:36 – 00:45
Jean Piveteau:
We create timber solutions for landscaping, construction and energy. The objective is to make wood effective in construction.
01:01 – 02:13
Maxime Besnard:
We integrated Dassault Systèmes solutions into the company with the arrival of the Wood Projects service and products such as CLT [Cross-Laminated Timber] and glulam. These products require custom manufacturing, as we have to transform the customer’s mockup and plans into finished products. The 3DEXPERIENCE platform facilitates the data flow related to the client’s request, and allows the customer's plan to be translated into surface area, quantity, loading plan, parts plan, and order confirmation. The major evolution we gain with Dassault Systèmes solutions is the automation of all these steps. Before, with our previous tools, technicians and engineers in the pricing department used to spend 70% of their time making plans, either parts plans or loading plans. And if a client asked for a change, we had to restart from scratch. Dassault Systèmes solutions helped us gain 50% to 60% in productivity on these steps. Using the solution on cloud is essential for information accessibility. Also, the data speed will give us more flexibility as we will be able to integrate customer’s change requests until very late in the process. The data-centric side of Dassault Systèmes solutions is key. It allows us to have a single source of the truth, accessible to everyone. That's what really makes the difference.
02:14– 02:35
Jean Piveteau:
The important role of Dassault Systèmes is to help us improve performance between the wooden beam or the CLT panel that we produce and the machining that we’ll have to do, and to reposition wood in its rightful place in the world of construction.
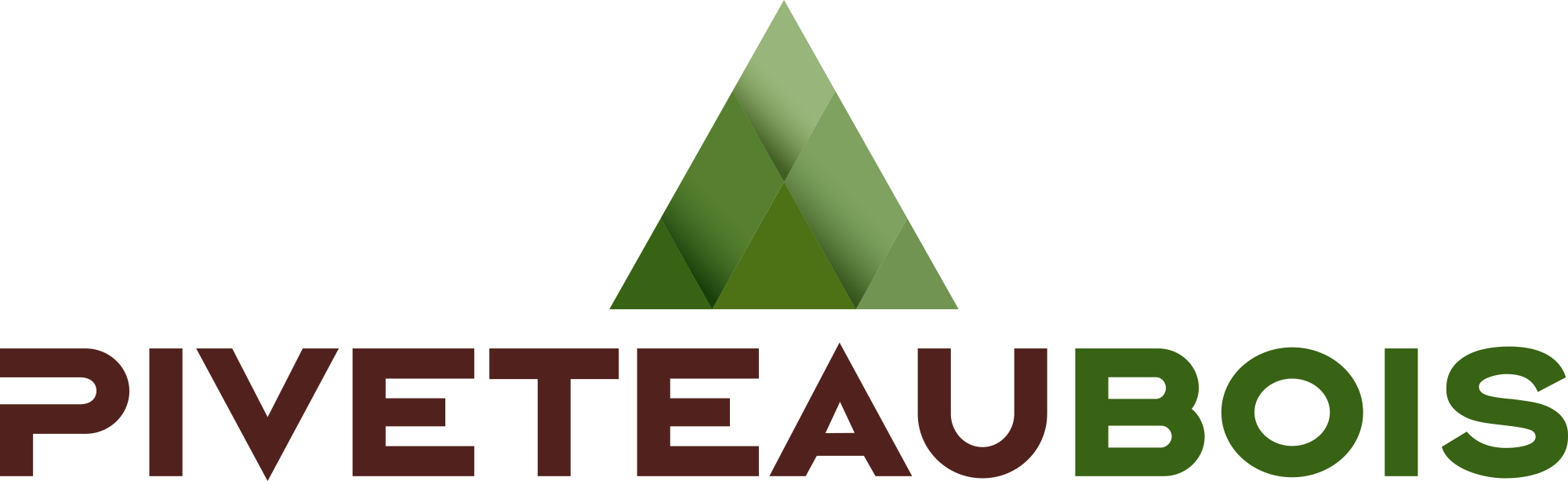
Focus on PIVETEAUBOIS Group
France-based manufacturer of wood solutions for construction, landscaping and wood energy since 1948, PIVETEAUBOIS Group is a leader in its sector. Committed to a rigorous policy of sustainable development, the three production sites of the company source their supplies from local, PEFC eco-certified forests located less than 300 kilometers away. The Group’s know-how and continuous investment in new technologies allows it to get the best out of each tree, both in terms of optimizing the material as well as guaranteeing the premium quality of its products.
For more information: www.piveteaubois.com
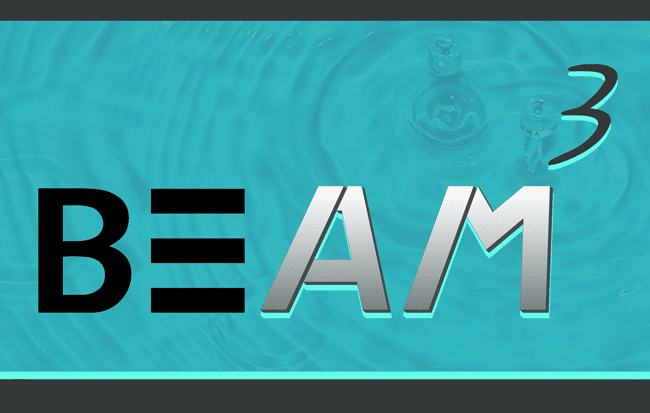
Focus on BEAM CUBE
BEAM CUBE brings digital project management and design (BIM) solutions to the construction industry based on the 3DEXPERIENCE platform. The company provides support and training to companies in the architecture, building and land management sector, helping them to take advantage of the next generation of BIM tools, which are key to the global progress of the building and territory world. Backed by the 3DEXPERIENCE platform, BEAM CUBE provides its customers with the most efficient approaches that will define the future of buildings and cities.