HD Hyundai Xitesolution
To foster greater synergy between its two subsidiaries, Korean construction machinery company HD Hyundai XiteSolution needed to create a common global product development management system to integrate their design, product lifecycle and bill of materials management capabilities.
Paving the way for autonomous construction
Today, a typical construction site might see workers doing manual work, operating machinery or surveying a build. The future of the construction industry will most likely look very different: robotics equipment remotely controlled from homes or offices, autonomous construction machinery or vehicles carrying out tasks based on the results of simulation and entire operations driven by virtual twin technology. This is the vision of Korea-based manufacturer of industrial equipment components HD Hyundai XiteSolution (HDX), the holding company of HD Hyundai Infracore (HDI) and HD Hyundai Construction Equipment (HCE).
To achieve its vision and represent the very best of Korea’s construction industry, HDX needed to foster greater synergy between its two subsidiaries HDI and HCE, which design and manufacture construction equipment, engines, attachments, utility apparatus and more.
“We are striving for integrated procurement and platform design so that we can design anywhere and build anywhere,” said Keewan Park, HDX’s vice president and ICT division lead. “This means integrating the two companies’ entire product development processes and data management systems.”
HDX’s aim is to create a common global product development management (GPDM) system that can assimilate the design, product lifecycle management (PLM) and bill of materials (BOM) management capabilities of the two companies.
The solution provider that will help HDX achieve its aims? Dassault Systèmes.
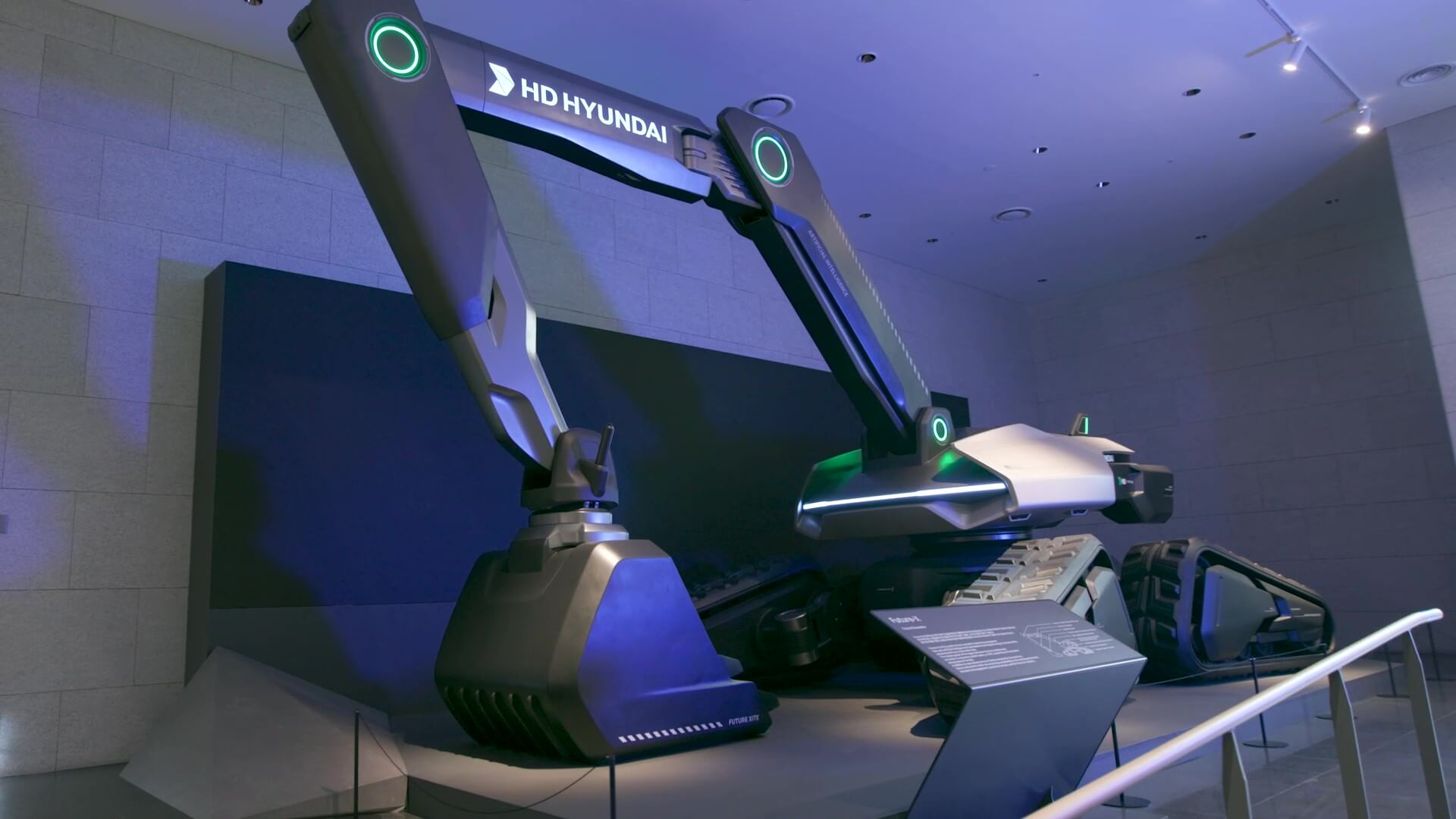
A platform for synergy
HDI was already using Dassault Systèmes software as its GPDM system – and Heeyoung Kim, HDX’s general manager, was impressed with what it was achieving. “We were particularly excited by Dassault Systèmes’ next-generation design, product lifecycle management (PLM) and bill of materials (BOM) management capabilities,” Kim said. “Its solutions are widely used in construction and manufacturing, so we knew it could deliver what we needed. At the same time, choosing a solution HDI had already implemented would mean less integration and compatibility issues. It would minimize the changes, risks and costs that may occur by adopting a completely new system.”
To implement the software in the most effective way possible, HDX adopted Dassault Systèmes’ Value Engagement framework, which consists of four key steps: Value Assessment; Value Definition; Value Commitment; and Value Delivery.
To assess the transformation value, HDX worked with Dassault Systèmes to determine its key business requirements. After reviewing various integration options, Dassault Systèmes presented a plan for developing the GPDM system, which helped HDX understand the technologies’ capabilities and potential.
Dassault Systèmes then helped HDX define its roadmap for implementing and rolling out its new design, PLM and BOM capabilities, before making the transition to digital manufacturing. “This enabled us to identify the value of the GPDM system and allowed us to visualize our digital transformation,” said Sanghan Lee, a senior manager and integration R&D innovation team lead in HDX’s ICT division.
The value commitment stage helped HDX prepare for the changes it needed to make to fully embrace a new integrated way of working. “PLM integration doesn’t just mean integrating design systems; it means changing work processes internally and externally across the value chain,” Sanghan Lee said. “How, which systems, and what to integrate as well as re-organized processes were key topics of many discussions and consultations. The value commitment stage gave us confidence to manage these changes effectively.”
With a clear plan in place, the final stage is execution. Since HDX chose Dassault Systèmes’ out-of-the-box capabilities, the implementation process was fast and efficient, taking just six months.
A collaborative platform for faster product development
HDX has now established its GPDM system on Dassault Systèmes technologies, providing a unified environment for team members across engineering, design, purchasing and manufacturing departments from both HDI and HCE to collaborate on the latest product data.
“Previously, the two companies had separate software solutions for design, analysis and production, as well as their own systems for managing data, so it wasn’t easy to access reliable data,” said II Cho, a senior manager in HDX’s integration R&D innovation team. “Now, with a GPDM system based on Dassault Systèmes platform, that complexity has disappeared. We can now work effectively as one team.”
By working in a shared environment, teams are more productive. CATIA, for example, enables multiple engineers to access and work on the same 3D model at the same time. It’s also faster: “Even the most data-heavy models can be opened 40% quicker compared to previous design solutions,” Sanghan Lee said.
Without having to install design software, non-designers can leverage the 3DPlay widget to work with 3D data and make necessary checks. “Authorized employees from any department can be involved in the design review process – helping to identify issues earlier in the product development lifecycle, improving quality assurance and reducing the likelihood of errors,” Park said.
All this is achieved while ensuring the highest levels of security: Access to the data stored in collaborative spaces is restricted by role-based access lists.
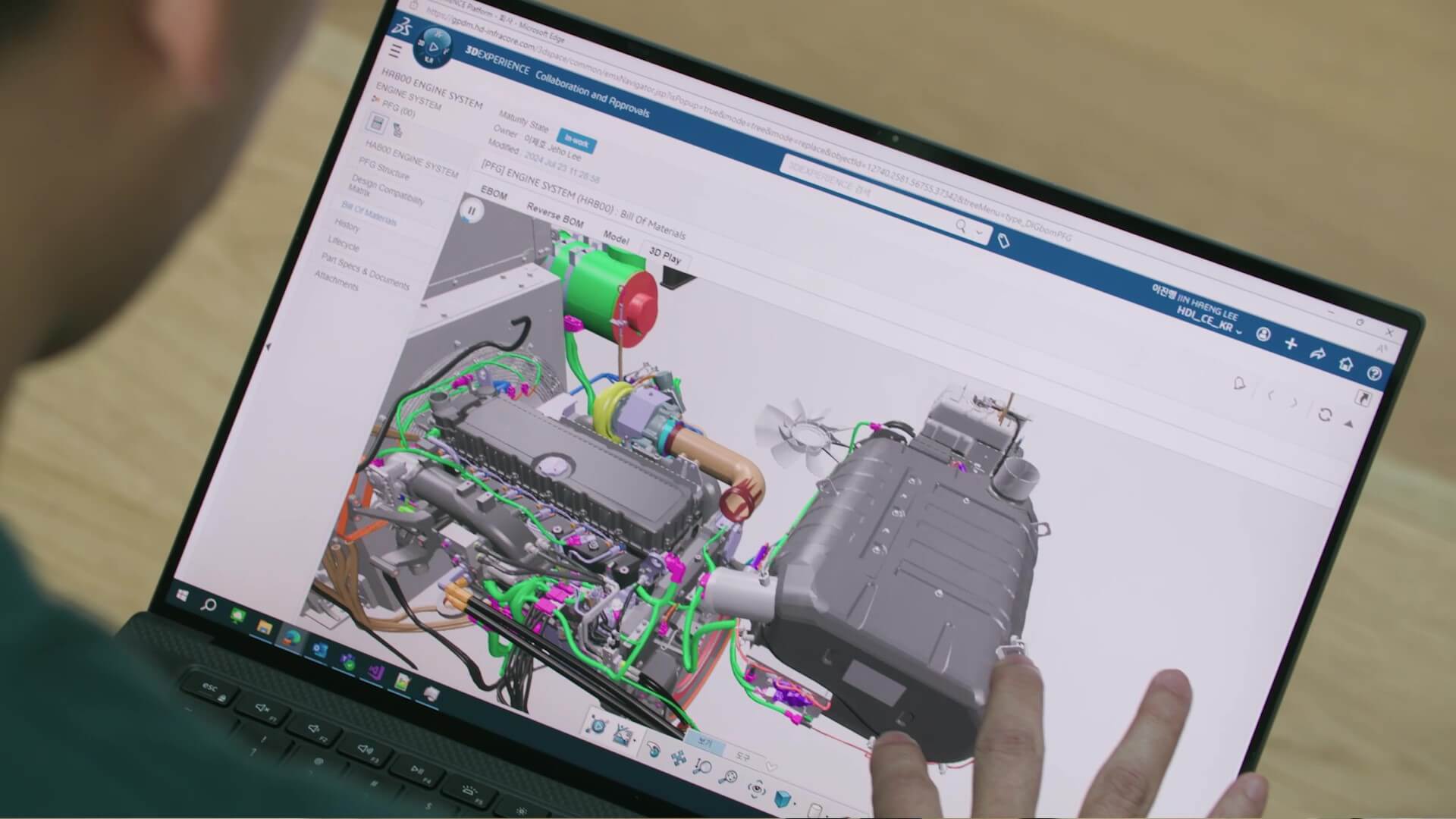
Unifying data for a single BOM
ENOVIA’s product data management capabilities on the platform have enabled HDX to establish a common parts library which any employee can reference. “We’ve standardized our product specifications and established a reference information system for company-wide use,” said Seonkyeong Lee, a senior engineer and engineering process operation team lead at HCE. “The combined efficiencies of our new centralized approach have reduced product development lead time which decreases costs. This is driving innovation and strengthening our products’ competitiveness.”
Now with a single, unified BOM, sync tasks and the associated system latency are eliminated, reducing designer wait times. Duplicated data is removed, which minimizes the likelihood of repeated work. Designers can also now directly configure the BOM on the web, resulting in a much smoother change management process. “Previously, it was necessary to save design modifications, synchronize and check the BOM. Now, by utilizing a single BOM system that integrates CATIA data, we have maximized design productivity,” Park said. “The extra time gained can be used for the main design work.”
Leveraging BOM data in DELMIA also facilitates digital pre-assembly. Material allocation can be configured, for example, and any problems can be flagged prior to physical manufacturing. “Concurrent digital pre-assembly and design means we can verify the production and assembly processes in advance and make changes to designs at the earliest possible stage of the product lifecycle,” Cho said. “This ability to digitally transform our business from design to production with a single source of truth is advancing our digital manufacturing approach.”
The use of DELMIA Apriso for manufacturing operations management (MOM) extends these benefits to HDX’s two production sites – the Ulsan campus, where hydrogen excavators and wheel loaders are manufactured, and the Gunsan plant where hydrogen forklifts are produced. Consistent data is verified in advance through the 3DEXPERIENCE platform and delivered to the manufacturing facilities. At the same time, DELMIA Apriso’s integrated production monitoring and analytics function provides staff with a real-time view of activities on the shop floor, enabling them to analyze and optimize manufacturing processes. “This minimizes downtime, prevents production errors and associated costs, and ensures quality,” Sanghan Lee said.
The combined efficiencies of our new centralized approach have reduced product development lead time which decreases costs. This is driving innovation and strengthening our products’ competitiveness.
Autonomous construction equipment in a smarter future
In the future, HDX expects to use additional Dassault Systèmes technologies to integrate electrical design processes into its GPDM system. It also wants to use the solutions to advance its ‘Xite Transformation’ concept, which involves developing autonomous industrial vehicles and robotics, increasing product effectiveness and refining its processes to become more competitive and sustainable.
“We want to leverage artificial intelligence and machine learning to drive design automation and optimization and to reduce costs,” Kim said. “CATIA’s 3D data is also a key enabler in the drive toward smart factories, where integrated modeling and simulation (MODSIM) drives the entire process. Having combined design and manufacturing management and data-driven decision-making can deliver new efficiencies and improve quality.”
In addition, HDX is exploring how it might use SIMULIA for simulation process and data management (SPDM), and DELMIA to fully embrace the power of virtual twins – digital models that replicate real-world operations. “The augmented reality space is already enabling businesses to leverage 3D data for design review and validation, education and training, and service and sales, and will continue to evolve,” Kim said.
These capabilities might even form the basis of ‘Twin Xite’ – HDX’s vision for digital twins in the future of the construction industry that will replicate construction environments and inform fully autonomous sites leveraging smart and connected equipment including robotics and autonomous construction machinery.
Ultimately, the combination of Dassault Systèmes technologies will enable HDX to maximize resources and reduce inefficiencies, with the end goal of revolutionizing construction sites as we know them today. “We’re expecting Dassault Systèmes to continue contributing to our product innovation and competitiveness through its diverse technology and scalability offerings,” Kim said. “We look forward to continuing our mutual growth and realizing further tangible business results in the near future.”
FAQs
Autonomous construction involves the use of robots and autonomous heavy equipment that can work without a human operator.
With less humans required on site, autonomous construction vehicles or robotics minimize the chance of on-site accidents and improve efficiency through around-the-clock operation.
Construction automation is the use of technology to perform various tasks in the construction industry with minimal human intervention.
Autonomous equipment can be robots or heavy equipment such as dozers, excavators or load carriers.
Discover more about the Integrated Heavy Machinery and Ready to Make industry solutions.
00:05 - 00:17
HD Hyundai XiteSolution specializes in construction equipment,
with technological innovations such as artificial intelligence, virtual reality and automation.
00:25 - 00:43
To fully leverage the advanced construction equipment of HD Hyundai Construction Equipment and HD Hyundai Infracore,
we wanted to integrate operations across development, sales, purchasing, production, and international business to create synergy.
00:44 - 01:24
The 3DEXPERIENCE platform was already working well for HD Hyundai Infracore, so it was the logical choice as our global product development management system.
With the adoption of the 3DEXPERIENCE platform, our workflow has improved drastically.
Every change is reflected instantly.
Now multiple users can access and work on the same model in CATIA at the same time.
This ensures we’re always working with accurate data.
It is so essential because we’re now seeing reduced time and costs in product development in terms of purchasing and production.
01:25 - 01:39
Our integrated global product development management system now operates one Bill of Materials system that handles computer-aided design, engineering and manufacturing.
This is much easier to manage instead of one system for each discipline.
01:41 - 02:15
The greatest value comes from establishing a unified work process through the platform, for better collaboration between design and production.
When changes occur during product development, data is first verified in the platform before we send it to the production site.
This reduces production errors and rework, improving production quality and also enhancing productivity.
Additionally, we expect to improve business efficiency through performing various tasks in a virtual environment, such as pre-assembly verification using 3D data and material allocation.
02:17 - 02:36
Now that we have successfully integrated our processes, we’re well-equipped to innovate and stay ahead of the competition.
The 3DEXPERIENCE platform now serves as the crucial backbone of our operations and I’m sure it will help us create new business models and further grow into a global business holding company.

Focus on HD Hyundai XiteSolution
HD Hyundai XiteSolution is HD Hyundai’s intermediate holding company in the construction machinery sector, with HD Hyundai Construction Equipment and HD Hyundai Infracore operating as subsidiaries. HD Hyundai XiteSolution is building its own business area by selling MCVs, transmissions, cylinders and other hydraulic parts. The company provides optimized solutions so that HD Hyundai Construction Equipment and HD Hyundai Infracore can create synergy in development, sales, purchasing and international business. By growing with partners and stakeholders, the three companies hope to create a blueprint for the future of the autonomous construction machinery industry in Korea.
For more information: https://www.hd-xitesolution.com