Edwards
Czech Edwards is developing vacuum pumps for the global life sciences industry. The company adopted the Digital Equipment Continuity industry solution on the 3DEXPERIENCE platform to manage all aspects of the product development lifecycle and ensure seamless data flows.
Science innovation in a vacuum
Without vacuum – spaces devoid of matter – many industries and products today would not exist. Everything from pharmaceutical drugs to the Lithium-ion batteries in electric vehicles need to be made in sterile environments or pressures below atmospheric levels, and this is only possible using vacuum pumps.
Leading the global vacuum market is Edwards. The company is part of Atlas Copco and its division in the Czech Republic develops vacuum pumps and systems for industrial customers across the life sciences sector. From a cutting-edge facility in Lutín, Edwards manufactures vacuum pumps that are suitable for different gases and stand up to all the challenges that come with handling corrosive, flammable, explosive and toxic chemicals.
Because Edwards operates at the cutting edge of the industry, it must connect directly with its customers’ research and development (R&D) teams to create custom pumps that make their processes safer, faster, sustainable and more economical while meeting exacting technical parameters and requirements. Every year, the pump manufacturer files for up to around eight patents as part of its own product development.
“Our science customers choose us for our premium quality products and excellent levels of communication and support,” said Petr Smerek, engineering manager, responsible for R&D at Edwards. “We get heavily involved in their R&D to create pumps and vacuum systems that work for very specific applications.”
These open innovation working relationships require Edwards to share data in a fast and very secure way, which means it always needs the latest technological capabilities to keep up. As demand grows for more customized pumps, Edwards made the decision to move its product development processes to the 3DEXPERIENCE platform.
“We have multiple large projects in the works focused on customization,” Smerek said. “We needed to find a way to connect our product lifecycle management (PLM) and bring our data together in one place. This is exactly what the 3DEXPERIENCE platform delivers, alongside a portfolio of connected applications and functionality we can take advantage of.”
We are driven by innovation and, thanks to the 3DEXPERIENCE platform, we can continue to support our people to push the boundaries of science.
Connected pump designs, data and departments
Before Edwards moved to the 3DEXPERIENCE platform, it lacked a centralized environment to store all its data and allow its R&D, design, process and quality teams to work together in a more streamlined way.
“Everything was disconnected,” Smerek said. “We had multiple applications, which didn’t all speak to each other. Data was siloed and it caused inefficiencies.”
Edwards already used CATIA V5 for product design and was ready to step up to the 3DEXPERIENCE platform to consolidate data management and take advantage of its associated applications, ENOVIA and DELMIA.
“The main positives are that it’s a database and all information is protected and in one place,” said Jiri Korycan, design lead at Edwards. “Data, people and resources are fully linked. I don’t need to go looking for details in spreadsheets any longer. I can log in to the 3DEXPERIENCE platform to do my work and see all related tasks and results. It’s a network for everyone across our organization.”
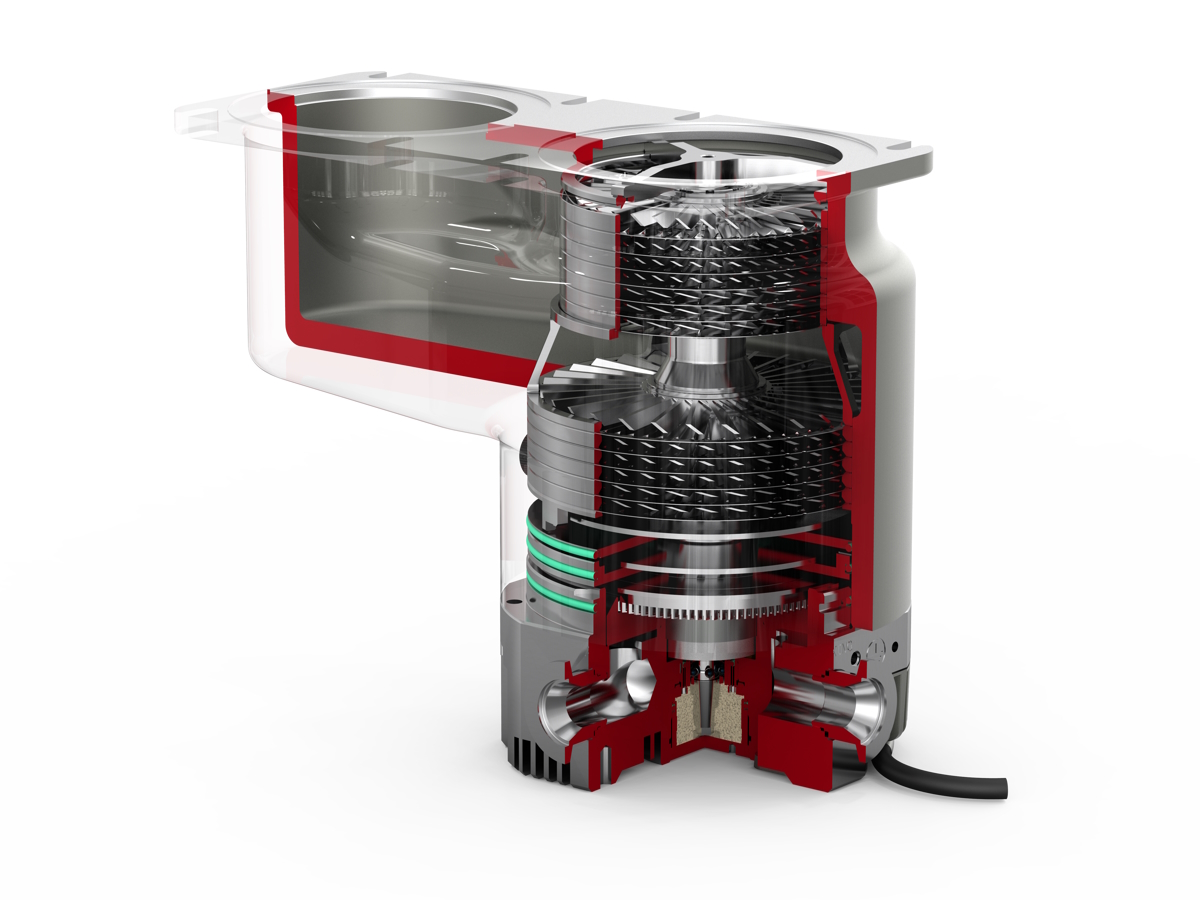
Matching Edwards' needs to the platform
Edwards worked closely with its technology partner Technodat to adapt its processes and become familiar with the rich functionality the 3DEXPERIENCE platform has to offer.
“We now have more than five years of experience with the platform and more than 60 users within our own organization, plus over 400 users across all divisions in Atlas Copco,” Korycan said. “Our processes work well as we’ve taken the time to understand the 3DEXPERIENCE platform. There is a real synergy between the platform and Edwards’ needs.”
Throughout, Technodat has supported Edwards as it rolls out the platform across different departments, including the new technology validation team, responsible for scientific development; the R&D team, which oversees demonstrator and serial production; and the machining department for managing computer aided manufacturing (CAM) data. At every phase, both companies work together to map the platform’s capabilities to Edwards’ needs and put in place the necessary training and support.
“Technodat offered great presales service in terms of testing licenses on our data and 3D models,” Korycan said. “They helped to simulate our internal processes to determine the best solutions, and they always go above and beyond to support us.”
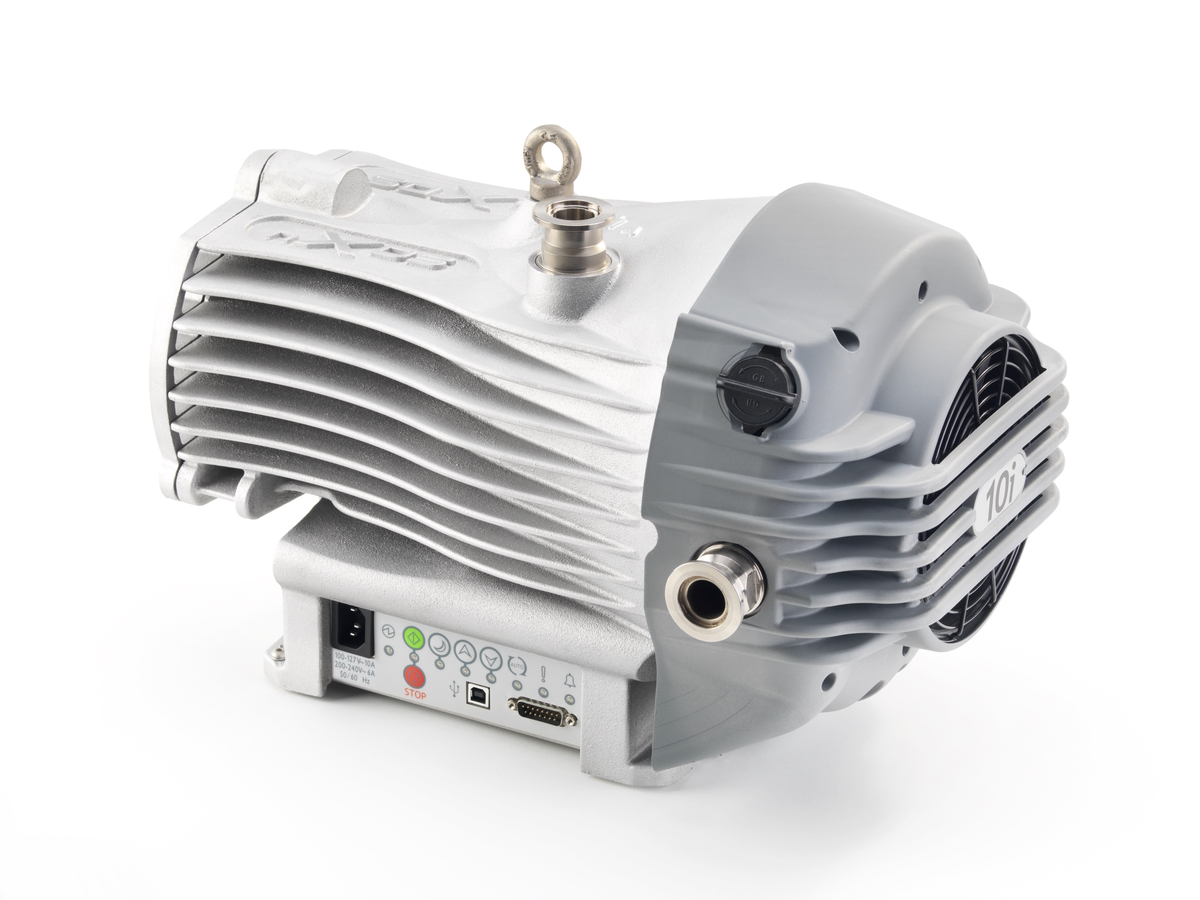
Secure collaborative innovation spaces
Backed by a consistent flow of connected and interrelated information from one department to the next, Edwards is speeding up development and making informed decisions about new product designs ahead of manufacturing them.
“We are able to extensively model and test new pumps virtually, create many more design iterations and validate the assembly process before we create any prototype,” Korycan said. “Before we spend real money on the shop floor, we can garner a lot of opinions from different areas of the business.”
The 3DEXPERIENCE platform lets the right people with the correct access permissions see the information they need at the right time.
“Today, we have the capabilities to set up users with different control rights, whether they’re an engineer or in other functions such as sales or services,” Smerek said. “Some users don’t need to create and edit designs, but they do need to be able to view 3D data and share feedback.”
The result is secure, collaborative spaces in the 3DEXPERIENCE platform. New users must be approved before accessing specific data and there is no need to export and convert data from one system to another; all software, even third-party applications, is fully integrated in the 3DEXPERIENCE platform.
“The platform has been set up to support collaboration while protecting our intellectual property,” Korycan said.
I receive far less negative feedback from internal customers regarding missed due dates or similar issues as I am able to review the system, plan ahead and give them capacity for their priority. It is absolutely amazing as I can also make more precise predictions when planning similar future projects.
Linking project planning to 3D Data
As well as benefiting from the 3DEXPERIENCE platform’s strong collaboration features, Edwards took the opportunity to modernize its project management capabilities, which it handled previously in spreadsheets. Today, the company uses ENOVIA on the platform to organize all new R&D activities, compare project plans, generate task sequences and make accurate calculations about required resources.
“Within seconds, the system calculates a project plan, and I can see on screen which tasks to focus on and how to plan resources,” Korycan said. “I receive far less negative feedback from internal customers regarding missed due dates or similar issues as I am able to review the system, plan ahead and give them capacity for their priority. It is absolutely amazing as I can also make more precise predictions when planning similar future projects.”
With all information available in a single dashboard, project managers work more efficiently and can ensure projects stay on track, using the data in front of them to move resources to where they’re needed. Any updates to pump designs are made in CATIA and shared with those who need to see them via the 3DEXPERIENCE platform. This has proven effective for tracking and approving product updates, and maintaining traceability at every stage of the development lifecycle.
“I have objective evidence of who, where, when and what has been approved in the system,” Korycan said. “There’s no need for me to go through hundreds of emails and meeting notes.”
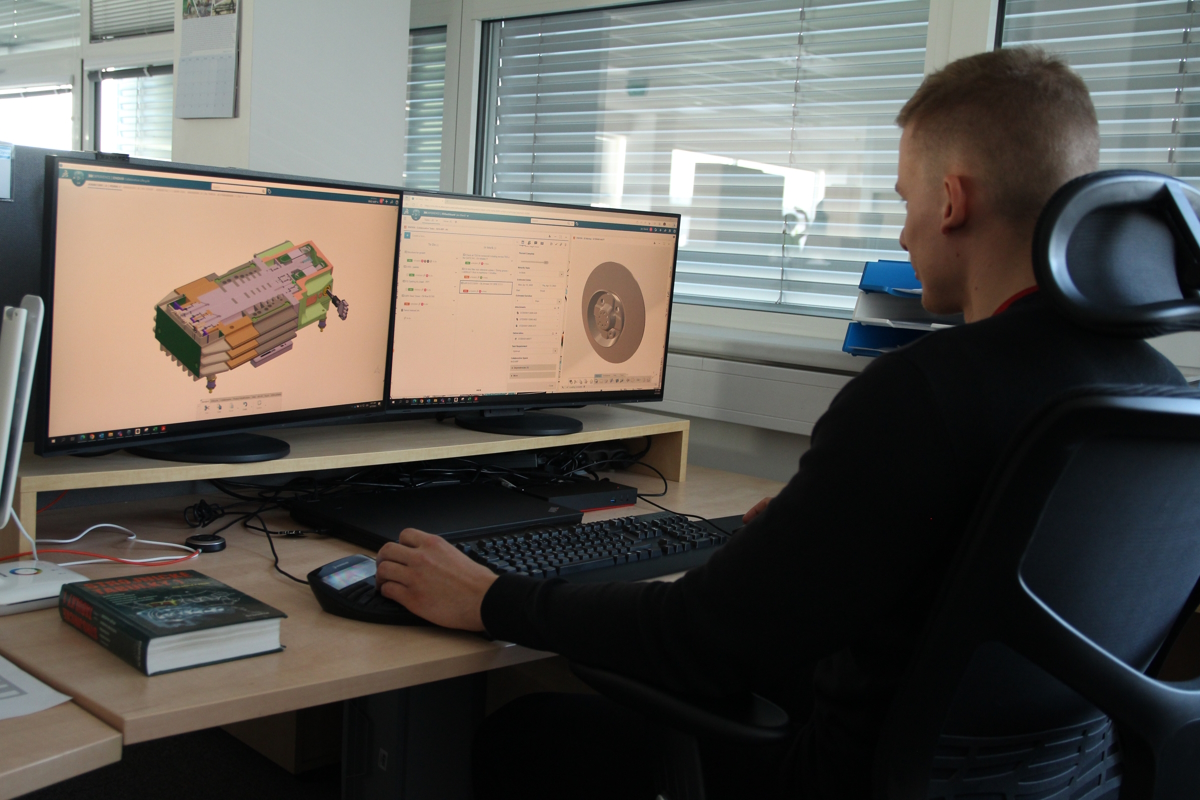
Optimizing manufacturing early on
High precision manufacturing requires advanced tolerancing analyses as well as assembly feasibility studies. With the 3DEXPERIENCE platform, Edwards is able to carry out these tasks as early in the product development phase as possible. This speeds up time to market and optimizes pump part designs in terms of material consumption and the CAM processes required to make them.
“We normally design a few variants of the part and use the 3DEXPERIENCE platform to define the ideal geometries for the CAM processes, such as the milling tool size and speed, and determine the balance between function and cost,” Korycan said.
The machining team uses DELMIA to efficiently set up the NC machining for individual parts in a more automated way.
“By using DELMIA to program our machines, we can quickly implement changes to the application programming interface, where there can be lots of edits,” said Martin Filipovic, Machining Manufacturing Engineering Leader at Edwards. “If we were writing each program by hand, it could take up to a week. With DELMIA, we can do it in a few hours.”
Eventually, Edwards wants to use the 3DEXPERIENCE platform to simulate its assembly lines. This will help it to find the ideal set up before the assembly line is built.
“Our goal is to automate all machining processes, backed by DELMIA,” Filipovic said. “We also see the potential of using DELMIA for managing robotics. By simulating all production processes in the virtual world first, we’ll be able to detect and avoid possible issues, such as collisions, later on.”
By simulating all production processes in the virtual world first, we’ll be able to detect and avoid possible issues, such as collisions, later on.
Sustainable vacuum pumps from design to operation
In times of rapidly rising energy costs, Edwards and its customers face growing pressure to remain profitable. That’s why the company focuses on developing vacuum pump solutions that are reliable, sustainable, cost efficient and save energy in production.
“The 3DEXPERIENCE platform helps us to optimize product design and machining of parts,” said Smerek. “By supporting innovation, it plays a key role in our goal to develop and produce vacuum products that deliver a further 5% in terms of power efficiency to our customers’ production processes. This will have a significant impact on their own energy reduction efforts.”
Backed by the power of the 3DEXPERIENCE platform, Edwards is confident in its ability to deliver customized vacuum pumps that give its customers a competitive advantage while ensuring it continues to innovate sustainably and responsibly.
“Through our combination of industry expertise, engineering strength and a rich product portfolio, we are in a unique position to develop the best solutions for our customers’ needs,” Smerek said. “We are driven by innovation and, thanks to the 3DEXPERIENCE platform, we can continue to support our people to push the boundaries of science.”
Discover more about the Digital Equipment Continuity industry solution experience.
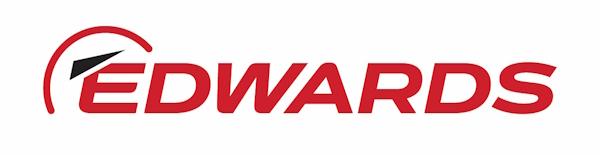
Focus on Edwards
Edwards is a global leader of vacuum and abatement. Part of Atlas Copco Group, the company enables environments where innovation thrives. Its products are integral to manufacturing processes for semiconductors, flat panel displays, LEDs and solar cells; are used within an increasingly diverse range of industrial processes including power, glass and other coating applications, steel and other metallurgy, pharmaceutical and chemical; and for both scientific instruments and a wide range of R&D applications.
For more information: www.edwardsvacuum.com
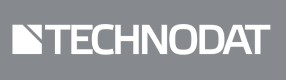
Focus on Technodat
Technodat provides value-added business consulting services, PLM project implementation and integration, training and support to its customers in the Czech Republic and Slovakia. The company is a leading integrator and distributor of the 3DEXPERIENCE platform, and a preferred PLM and 3D solutions partner to customers of all sizes and in all industries, helping them develop and manufacture better products and innovative services faster.
For more information: www.technodat.cz