Eaton
Eaton manufactures connectors for harsh environments.
DELMIA is scalable because it allows us to communicate well with our systems.
Sharing expert insights
With about 3,400 dedicated employees strategically stationed in ten factories around the world, Eaton is a trusted manufacturer of connectors for challenging environments.
Francois-Xavier Marchais, Vice-President of Operations, Aerospace Group at Eaton, shares his expert insights about his company's initiatives in manufacturing connectors for harsh environments, their journey into digitalizing production and their plans for future expansion.
Their clientele primarily comes from the civil aviation industry, a sector where quality is revered above all else. The demands are not easy – the products have to be impeccable, have airtight traceability and yet be reasonably priced. Eaton, however, does not falter. They deliver consistently, aided by factories that vary in size and capability, from small pockets of around 50 people to large establishments housing around 1,000.
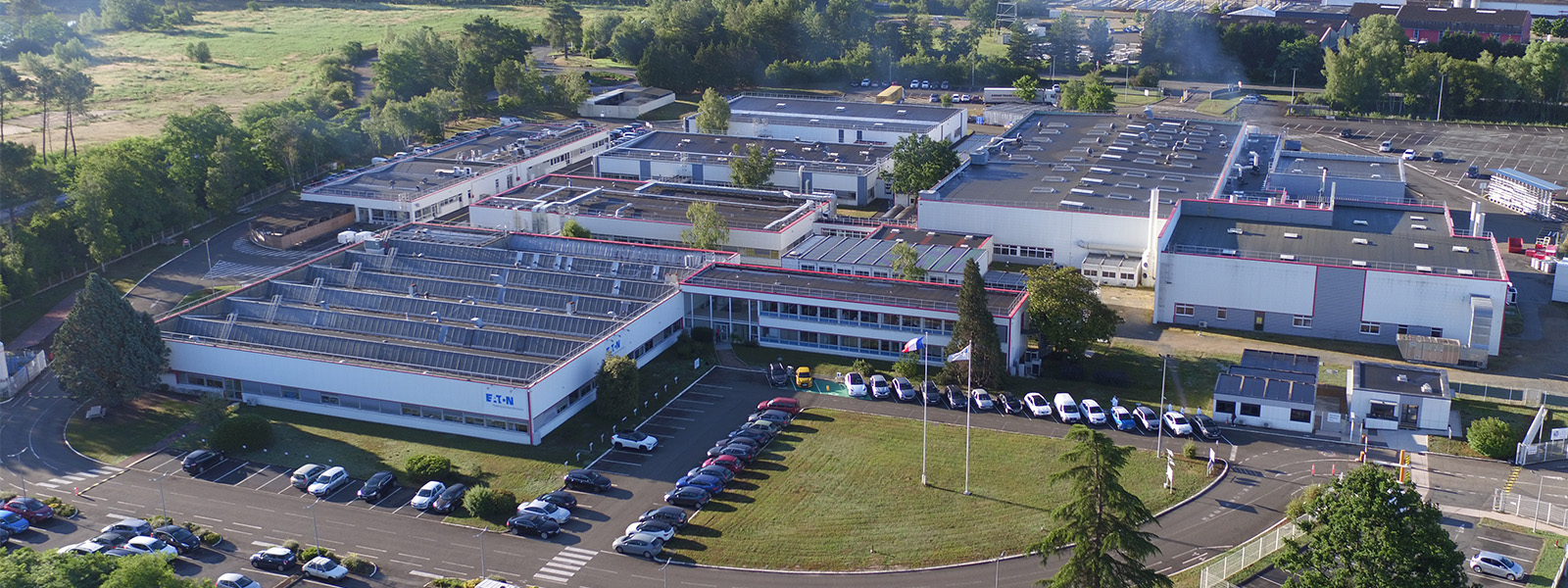
Paving the way for a single solution
Franck Jollivet, Eaton's Production Director explains that the essence of their production lies in four main processes: machining, electroplating, molding, and assembly. Their ambition? To digitalize their production workshop to elevate their competitiveness, to manage their efficiency and quality more precisely, to dematerialize their production documents for the same cost as paper and to improve their product traceability process.
This desire for improved efficiency is reflected in incorporating a scalable Manufacturing Operations Management (MOM) solution, DELMIA Apriso. As Marchais points out, DELMIA Apriso eases communication within the enterprise, providing coherence and fluidity from the ERP or PLM system to ENOVIA.
The benefits are a clearer view in production workshops and swift real-time decision-making ability. More importantly, it harmonizes the processes, paving the way for a single solution for all their indicators.
This focus on maintenance levels, quality and safety has resulted in a marked improvement in productivity. The data collected has aided Eaton in channeling efforts into targeted and practical actions, ultimately improving the ease and quality of work on the shop floor. As Marchais talks about their plan of rolling out this system across all their worldwide sites, it stands as a testament to their relentless pursuit of improvement and unwavering commitment to quality and efficiency.
Challenge
Challenge lies in maintaining product traceability, quality, and affordable cost, all while managing a diverse global production network involving machining, electroplating, molding, and assembly.
Solution
By adopting DELMIA, a solution that communicates efficiently with ERP or PLM systems and ENOVIA, production processes are dematerialized leading to improved product traceability and meticulous management of efficiency and quality.
Benefits
This digital transformation strategy has brought forth numerous benefits such as improved visibility in production workshops, real-time decision-making capabilities, and a uniform solution throughout the production chain. Moreover, this evolution has significantly improved productivity, safety, and maintenance levels, making it an integral part of Eaton's global expansion strategy.
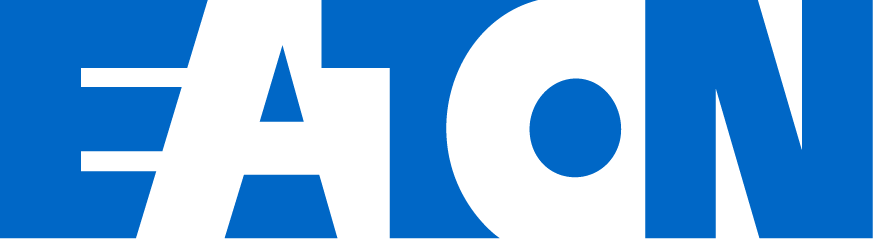
Focus on Eaton
Eaton is an intelligent power management company dedicated to improving the quality of life and protecting the environment for people everywhere. We are guided by our commitment to do business right, to operate sustainably and to help our customers manage power ─ today and well into the future. By capitalizing on the global growth trends of electrification and digitalization, we’re accelerating the planet’s transition to renewable energy and helping to solve the world’s most urgent power management challenges.
For more information: https://www.eaton.com