Aciturri
Facing increasing demands, Aciturri implemented the Ready for Rate solution to improve project planning, halving aerostructures delivery times while securing customer trust.
Design-to-build aerostructures for the future of aviation
When Ginés Clemente opened a small machining workshop in the Spanish city of Miranda de Ebro back in 1977, little did he know that it would evolve to become a company that has played a significant role in shaping some of the world’s most advanced aircraft.
As a strong Tier1 supplier to original equipment manufacturers (OEMs), Aciturri develops design-to-build airframe components for commercial and defense jets, including the Airbus A350, the Boeing 787, Boom Supersonic Overture and the Embraer KC390. Now expanding its activities into new fields such as electric mobility, the company is modeling and producing various parts of electric vertical take-off and landing (eVTOL) aircraft such as the wings for Brazilian company Eve Air Mobility.
With 40 production plants spread across Spain, France, Morocco and Brazil – each with its own area of expertise, whether that’s composites, metallics, assemblies or something else – Aciturri chooses the location for a project based on its particular specialism. Then, it needs to consider the physical requirements to handle such large components.
“We first look at the various geometries, manufacturing processes, process qualifications, machines specifications and other constraints to decide on where to produce,” said Eduardo Cid, industrialization manager at Aciturri. “And since parts can be 20 meters in length, it’s very important to ensure that we have enough room within our facilities for the equipment but also the people moving around it. That entails a detailed analysis of the layout.”
Today Aciturri has got the process of analyzing the layout down to a fine art. And it’s all thanks to its advanced digital simulation solutions, which enable it to pitch for and plan its projects quickly, with incredible precision.
Precise project planning for exacting projects
Considering the level of planning required to deliver a new component for an aircraft the size and complexity of a Boeing 787, the company quickly realized it would need an appropriate solution to complete such a project.
Looking for a 3D simulation solution that could help it better plan how to meet complex demands and win new contracts, Aciturri adopted Dassault Systèmes’ platform on the cloud as the best solution suited to its needs. By opting for a cloud-based solution, implementation was quick and access to Dassault Systèmes user communities enabled the engineers to receive comprehensive support from experts in the field.
“We are long-time CATIA V5 users; so, we have a huge existing database of 3D models of parts, tools, machines, industrial media, and more,” Cid said. “We wanted to manage all of our data and processes in a single environment, ensuring that everyone is working on the latest designs and enabling more effective change management. That’s why we decided to move to the 3DEXPERIENCE® platform.”
Dassault Systèmes’ developers provided great support on a daily basis. “Whenever we have difficulties, I can raise a question in the user community and we received the answer in a few hours,” Cid said. “It is exceptional.”
We create a discrete event simulation by means of factory flow simulation. This allows us to give a prediction like: "Our capacity is a minimum of 96 and a maximum of 102, with a confidence level of 95%."
Meanwhile, the implementation of DELMIA has facilitated a fundamental transformation in project planning. Aciturri is now able to build an accurate virtual twin of its plants, helping it to optimize and validate processes digitally before deploying them in the real world.
“We can create a 3D representation of a production facility, not only adding the parts, the machines and the manpower to account for space, but connecting all of these resources to estimate timings so that we can accurately work out how many components we can deliver in a given time,” Cid said.
While there is a level of automation within the aerospace industry, many processes are manual. Humans are not machines, so processes do not operate like clockwork. Aciturri has to consider this variability to get a realistic estimate of timings.
“We create a discrete event simulation by means of factory flow simulation,” Cid said. “And we run that simulation many times because it’s a stochastic approach as we have introduced variability. Finally, we calculate the means and standard deviations. This allows us to give a prediction like: ‘Our capacity is a minimum of 96 and a maximum of 102, with a confidence level of 95%.”
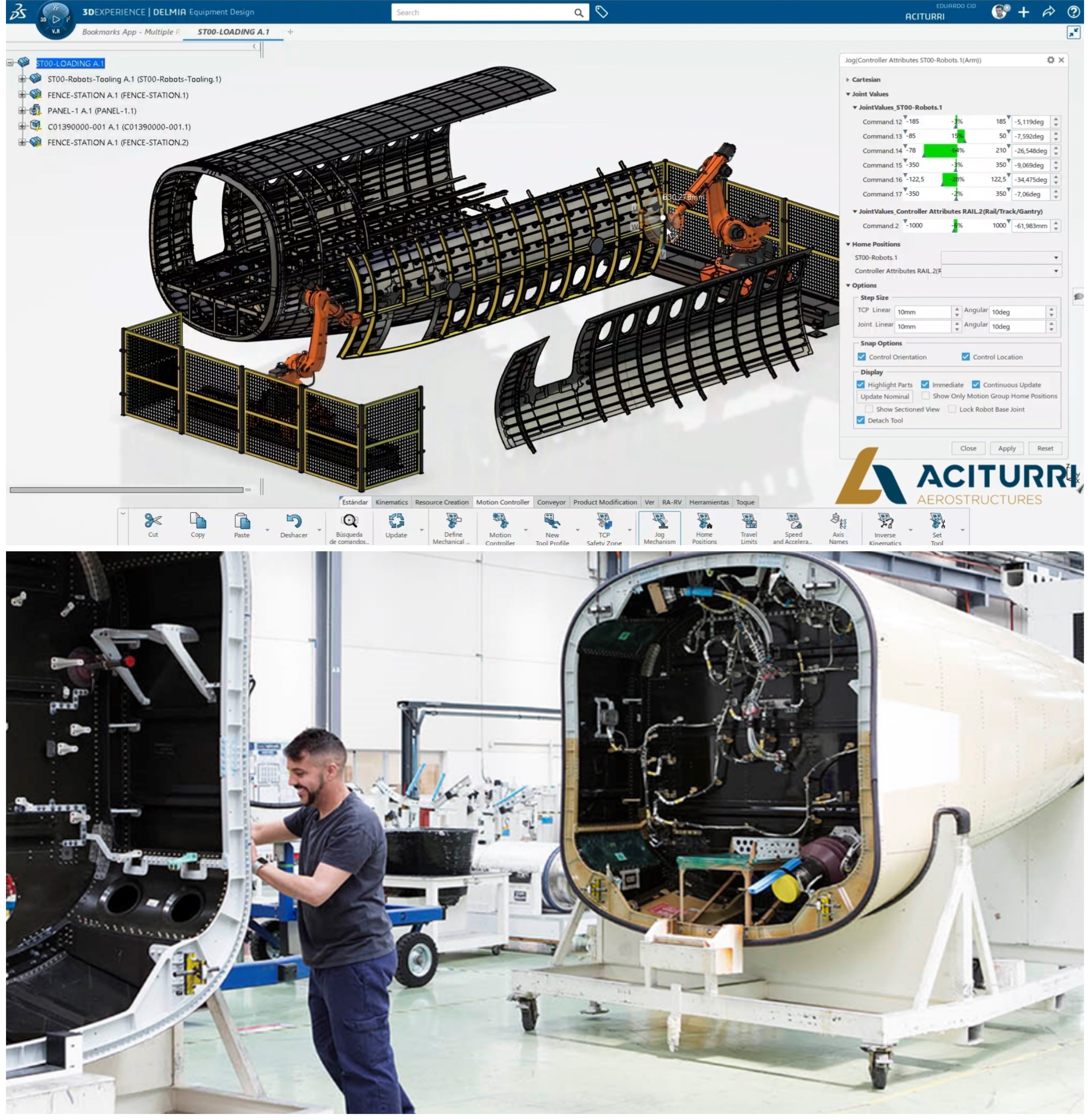
Halving delivery times while securing customers' trust
By creating more efficient and accurate processes, Aciturri has been able to halve the time it takes to complete a project.
“In the past, it was a standard assumption in the aerospace industry that industrializing a new work package – from design through to prototyping through to final delivery – would take two years,” Cid said. “That’s because there was so much guesswork around whether we had enough space or capacity, or whether our Excel formulas were accurate. Thanks to DELMIA, we can make better, faster and more accurate decisions. As a result, we have been able to reduce the typical time it takes to deliver a project to one year.”
Using DELMIA, Aciturri can now create animated models that it can present to customers, detailing production processes, full simulations of workflows and even the expected capacity of manufacturing plants. This has enabled the company to secure customer trust.
“Our customers can see that we have deeply analyzed their issues, simulated processes, run various scenarios and arrived at an optimal solution,” Cid said.
The value of this approach was made clear at a meeting Cid had with one of its customers.
“I was invited at the end of a meeting that has overrun, and everyone was tired,” he said. “My hour-long slot was cut down to two minutes. I decided to only show the animation of what we could deliver. That convinced the customer to go with us. That’s when I realized the true value of DELMIA – I knew we had taken the right way forward.”
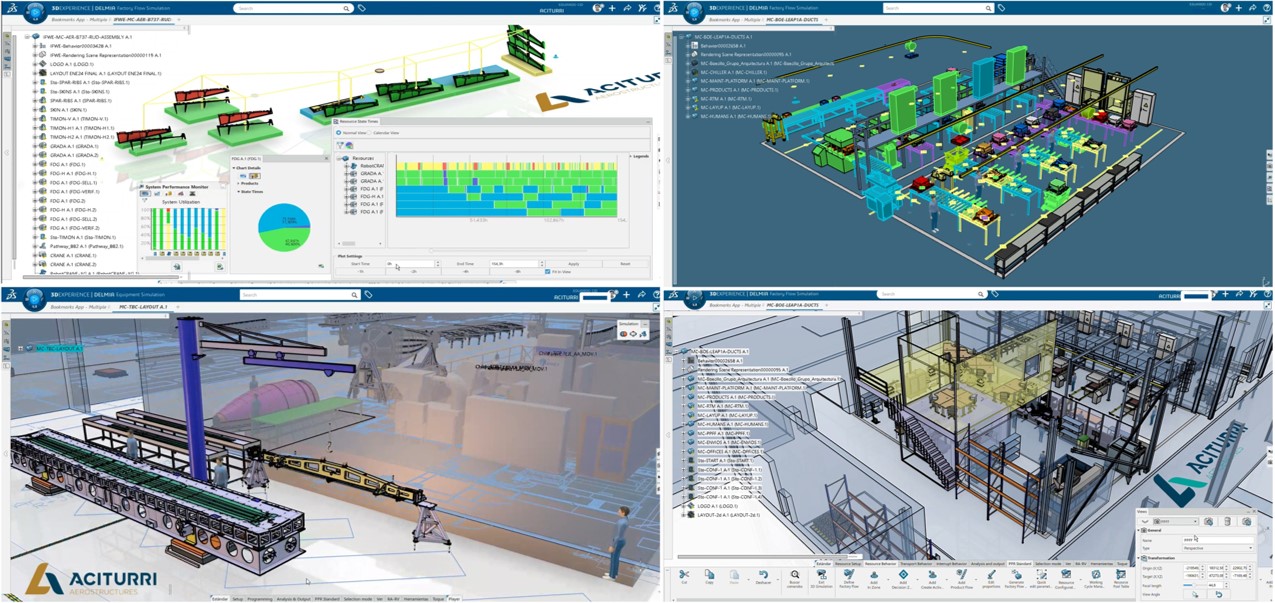
Paving the way for next steps
As competition continues to intensify and customers become even more demanding, Aciturri is keen to streamline processes further. The company currently manages multiple systems and tools, which has made data normalization and integration difficult. However, the company will soon be standardizing all of its data on the 3DEXPERIENCE platform.
“We are deploying the 3DEXPERIENCE platform as our main product lifecycle management (PLM) solution,” Cid said. “Using ENOVIA, we can centralize product and data management, which will not only save time spent importing information into DELMIA but also allow for greater visibility and transparency of data throughout the organization.”
With a workforce of 2,800 employees that it expects to double by the end of the decade, this will pave the way for the next stage in Aciturri’s transformation and help it support the industry’s continued growth.
Discover more about the Ready for Rate industry solution experience.
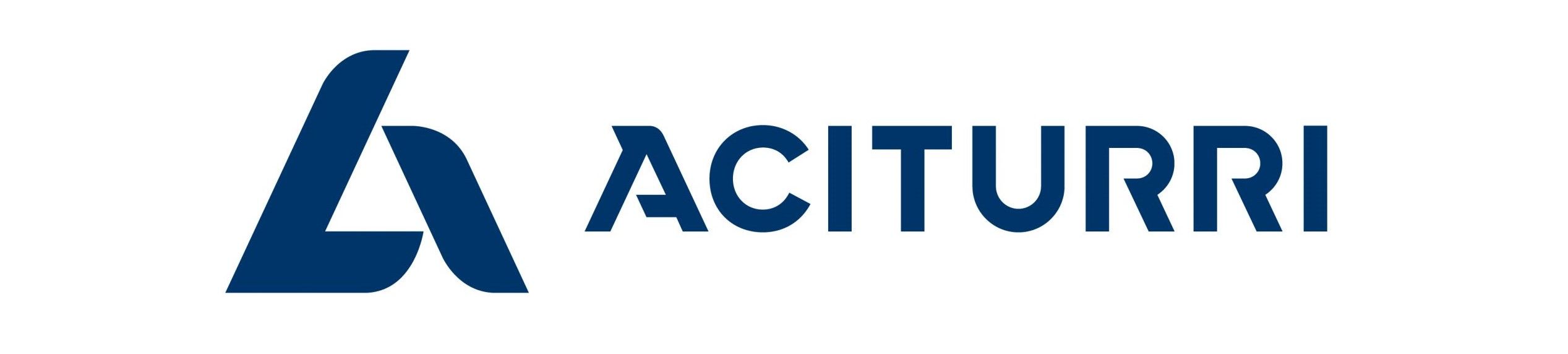
Focus on Aciturri
Headquartered in Spain, Aciturri is a tier 1 supplier of complex aerostructures. The company has a wealth of experience, particularly when it comes to developing lightweight composite and metallic components. The company is a founding member of Clean Aviation — the benchmark public-private initiative in the EU for the development of new aeronautical technologies.
For more information: https://www.aciturri.com
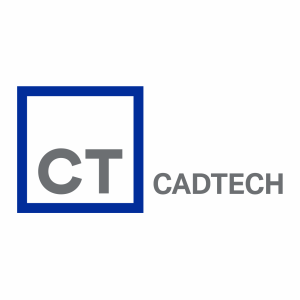
Focus on CadTech
Cadtech provides consultancy services specializing in PLM solutions. As an official value-added reseller of Dassault Systèmes technology, the solutions provider helps businesses effectively manage their product lifecycles, processes, projects and assets, including data simulation and management across Spain and Portugal.
For more information: https://www.cadtech.es