What do robots dream of?
A robot is an exceptional dance partner, executing his sequences to perfection, completely in time, performing lifts with absolute security.
A collaboration between ABB and Kulturhuset Stadsteatern.
ABB has operations in more than 100 countries and 136,000 employees. It is a world leader in electricity networks, industrial automation and robotics. One of its managing directors, Michael Larsson, sees how quickly the manufacturing sector is changing, and believes that technology’s role is to improve the way in which humans and robots collaborate. “We want to be certain that our technologies are safe,” he says, “and that humans and robots can share the same workspace.” He stresses that the traditional factory needs to change, and that work is needed to develop the sustainable factories of the future.
The first robots carried out repetitive, programmable and unchanging tasks, with humans controlling them from afar. He explains that in the manufacturing industry, it is now possible to imagine a collaborative robot working alongside humans in every part of the plant, with changes in demand leading to dynamic adjustment of the production process and the creation of new products. He emphasizes how sustainable processes will be integral to all stages of production in future factories.
Dances with robots
Imagine two dancers: a human and a robot… Not a humanoid like those that appear in science-fiction films or made by Japanese manufacturers, but an industrial robot that is 2m (6.5 feet) tall and weighing 900kg (1,984 pounds)!
For Swedish dancer and choreographer Fredrik Rydman, a robot is an exceptional dance partner, executing his sequences to perfection, completely in time, performing lifts with absolute security. The show makes us think differently about the way artificial intelligence and robots are becoming part of our lives. The dance shatters preconceptions about our relationship with machines, and the emotion that the audience feels is derived from the implied questions raised by the piece.
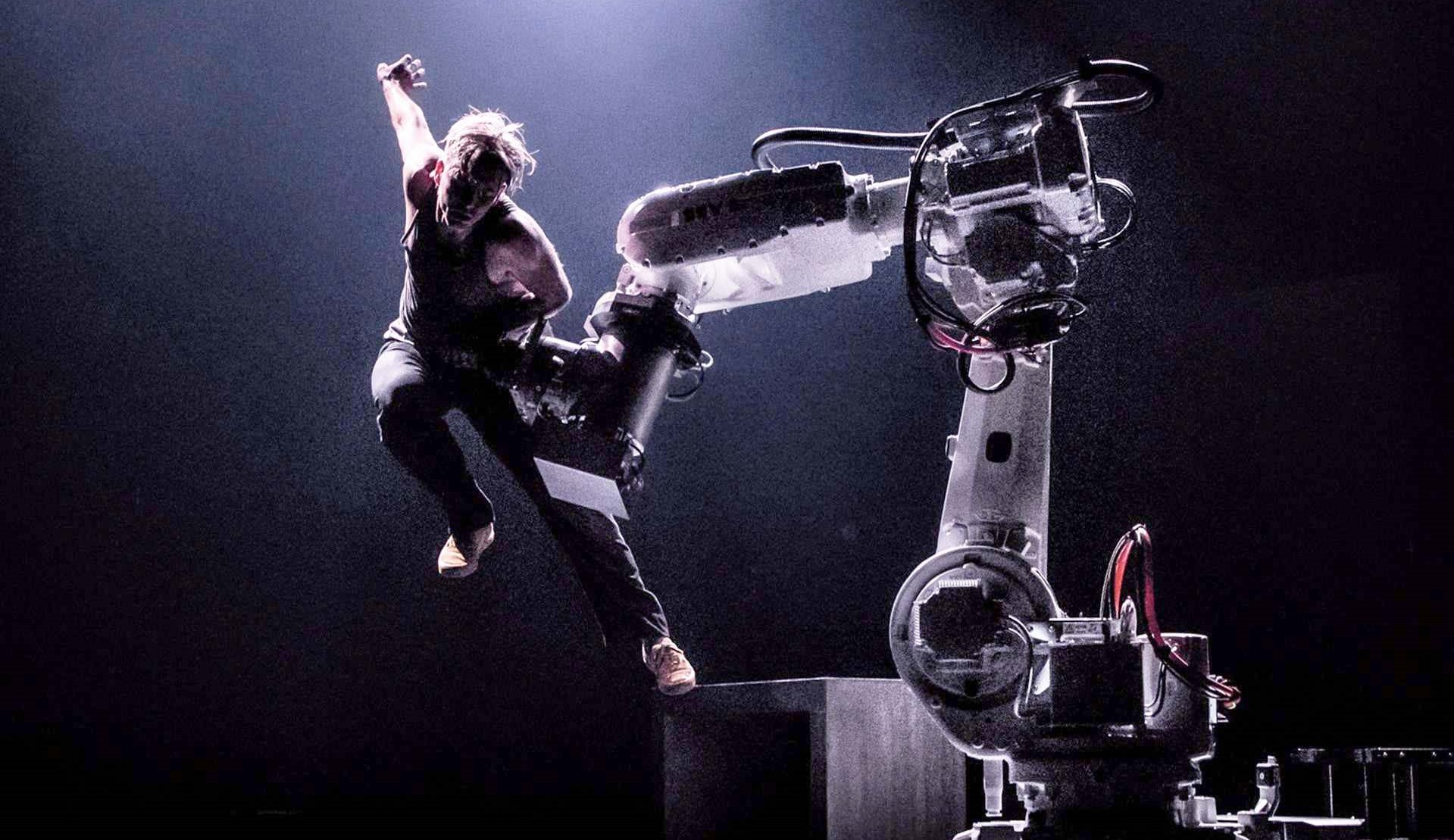
Highly versatile
“What we want to do,” Larsson explains, “is to integrate collaboration, simplification and digitalization to enhance flexibility and productivity. Collaboration means making the most of what needs to be done by humans and what can be done by robots. For us, creating a collaborative work envelope provides an opportunity to develop efficient technologies that allow them to work together.”
Traditional manufacturing concepts with monolithic assembly lines and conveyor belts are disappearing. ABB now uses automatically guided vehicles and mobile robots to produce items in a more flexible environment. This reduces the amount of floorspace required and allows a factory to better respond to demand. “The approach also allows our customers to be highly versatile,” adds Larsson. “They can start on a small scale and increase volume as required. Because we use standardized production cells, we can add more cells to take production to the next level.” This means that the factory doesn’t need to be oversized at the start of a product’s lifecycle, since production can be expanded when needed, depending on production requirements and market developments.